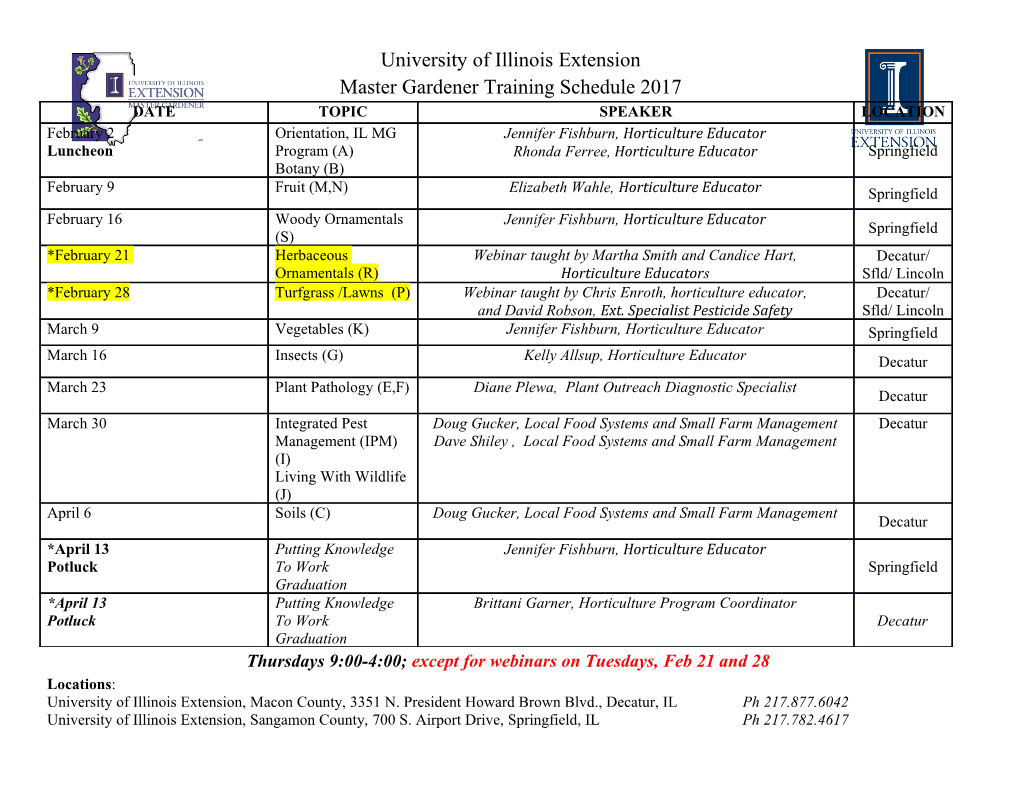
Assessment of Rail Flaw Inspection Data Brandon D. Jeffrey M. L. Peterson Department of Civil Engineering Colorado State University Fort Collins, Colorado August 1999 ACKNOWLEDGMENTS It is an honor to thank the following individuals for their support, help, and guidance. A first thanks is given to Alex Trindade, Ph.D. candidate at Colorado State University in statistics, for his expertise in statistical analysis. Also, in the statistics department at Colorado State University, a Master’s candidate Jill Smith, proved to be a tremendous help. Special thanks is given to Dr. Michael Peterson, professor of mechanical engineering at Colorado State University, for his guidance throughout this project. Finally, for the real world experience, Greg Garcia of the Transportation Technology Center Inc., for his time and efforts in providing a unique educational experience that will carry forward to a career. DISCLAIMER The contents of this report reflect the views of the authors, who are responsible for the facts and the accuracy of the information presented. This document is disseminated under the sponsorship of the Department of Transportation, University Transportation Centers Program, in the interest of information exchange. The U.S. Government assumes no liability for the contents or us thereof. ABSTRACT This project is an analysis of the rail flaw data for the Transportation Technology Center Inc. (TTCI). Six major railroads provided TTCI with defective rail, that had been removed from service. The rail, which contained a variety of defects, was placed into a gauntlet track at the Transportation Technology Center (TTC). The gauntlet track is known as the Railflaw Detection Test Facility (RDTF) and is a railroad industry tool, in cooperation with the Federal Railroad Administration (FRA), to evaluate rail flaw detection technology. TTCI inspected the rail, catalogued the defects, and installed the rail in the RDTF. There are 49 defects for each inspection vehicle evaluation. To date, there have been six evaluations performed at the RDTF. This paper is the assessment of those six evaluations. TABLE OF CONTENTS 1. Introduction 1 2. Current and Past Technologies 2 History 2 Ultrasonic Technology 4 Research Overview 8 3. Gauntlet Test Course 10 Gauntlet Description 10 Rail Defect Documentation 12 Types of Rail Defects 14 Railflaw Evaluations on the RDTF 17 Gauntlet Defect Study 19 4. Analysis of Results 20 Results 20 Detection Ratios 21 CHI-SQUARE Test Statistic 21 Logistic Regression Test 22 Probability of Detection Plots 24 5. Conclusions 27 References 29 LIST OF TABLES Table 2.1: Rail Derailments 1992-1995 3 Table 2.2: Ultrasonic Wave Angles 6 Table 3.1: Gauntlet Course Defect List 12 Table 3.2: Railflaw Evaluation Results 18 Table 3.3: Frequently Missed Defects during Benchmarking Evaluations at TTC 19 Table 4.1: Detection Ratios for RDTF Evaluations 21 Table 4.2: Hosmer and Lemeshow Good of Fit Table for Overall Evaluations 23 Table 4.3: Odds Ratios and 95 Percent Confidence Interval for Overall Evaluations 23 LIST OF FIGURES Figure 2.1: Road / Rail Ultrasonic Car 4 Figure 2.2: Railbound Induction / Ultrasonic Car 5 Figure 2.3: Ultrasonic Probe Wheel Transducer Arrangements 7 Figure 2.4: Typical Rail Defects 9 Figure 3.1: Railflaw Detection Test Facility (RDTF) 10 Figure 3.2: Industry Donated Rail 13 Figure 3.3: Ultrasonic Testing of Rail Samples 13 Figure 3.4: Radiography of Donated Rail Samples 14 Figure 3.5: Detail Fracture (DF) 15 Figure 3.6: Transverse Defect (TD) 16 Figure 3.7: Vertical Split Head (VSH) 16 Figure 3.8: Horizontal Split Head (HSP) 17 Figure 3.9: Detail Fracture under Shelling 17 LIST OF GRAPHS Graph 3.1: Service Failures From 1986-1988 15 Graph 2: Evaluation 1 24 Graph 3: Evaluation 2 24 Graph 4: Evaluation 3 25 Graph 5: Evaluation 4 25 Graph 6: Evaluation 5 25 Graph 7: Evaluation 6 26 Graph 8: Overall Evaluation 26 Graph 5.1: Inspection Reliability and Probability of Detection Comparison 27 1. INTRODUCTION The detection of defects in steel rail is perhaps the first widespread application of non-destructive testing. Failure to detect defects is significant for the development of non-destructive testing and, more importantly, the safety of the railroads. However, in the decades that have passed since the initial development of the rail defect detecting technology, the basic inspection processes have not changed. Significant developments have been made in signal processing and automated rail flaw evaluation. This project is a small part of an assessment of the rail inspection industry and the many factors that contribute to the ability to detect defects in steel rail. The Transportation Technology Center Inc. (TTCI), a wholly owned subsidiary of the Association of American Railroads (AAR), and the Federal Railroad Administration (FRA) have cooperated to explore current technologies for rail inspection with an emphasis on reducing risk, while maintaining cost control on the maintenance of the railroads. TTCI is partially funded by the six major railroads whose rail lines represent a significant portion of the track mileage and the total tonnage, which is transported by rail. The primary technical efforts will focus on detection of typical defects that occur in rails. As an experimental base, examples of true defects actually have been removed from revenue service lines and placed in track section in a test loop. The test loop is located on the 52-square-mile test center at the Transportation Technology Center (TTC), east of Pueblo, Colo. The defects are hosted in conventional curved and tangent track segments. In addition, fabricated defects were placed in the track sections for determining the limitations to the testing technologies. Support for this research paper has been provided in part by the U.S. Department of Transportation (USDOT) via the Mountain Plains Consortium, which is sponsored through the University Transportation Centers Program. The efforts of Colorado State University (CSU) have concentrated on providing an assessment of evaluations of the rail inspection vehicles. Through the spring of 1998, TTCI has tested six rail inspection vehicles to provide detection results for the 49 catalogued defects on the gauntlet course. The results presented in this paper consist only of results from the first six trials , the 1 statistics are expected to change as additional cars are tested. This paper provides an overview of the ultrasonic inspection technology, the gauntlet course, plus its defects, and the statistical results from six evaluations of the rail inspection vehicles. 2. CURRENT AND PAST TECHNOLOGIES History Non-destructive testing had its beginning in rail application in 1923 when Dr. Elmer Sperry noticed an increase in the number of disastrous train derailments. Sperry developed the first rail inspection car (Car SRS #101) to detect transverse fissures in railroad rails. By November 1928, Sperry had an inspection car testing rail on the Wabash Railway in Montpelier, Ohio, and Clarke Junction, Ind., for its first commercial use. Car SRS 102 detected a large transverse fissure in the head of a rail. Much to the annoyance of the railroad, the rail was taken out of service and the following day was tested by Sperry’s chief research engineer. The rail was tested and broken where the transverse fissure was found. After the convincing test of the SRS 102, Sperry expanded his services and increased his fleet to 10 cars by the end of 1930 (Clarke, 1997). The first inspection car employed an induction method. A heavy current was induced through the rail to be tested. Search coils were moved through the resulting magnetic field to find perturbations in this field caused by defects. By 1959, Sperry developed the first ultrasonic test car for the New York City Transit Authority (NYCTA). Today, Sperry has a fleet of more than 40 test cars, both, magnetic induction cars and ultrasonic detection cars that employ both methods. By the 1950’s track conditions significantly improved when continuous welds of each rail replaced joint bars. This resulted in a shift of defect types found in the rails, away from joint defects. Over the next 10 to 20 years the average age of the rail naturally increased as did the average load of the rail cars. Then, in the 1980’s, with increased use of inspection cars throughout North America the general trend in detection was lower defect rates (Davis, 1997). 2 Today, interest in repair and maintenance, and the characteristics of the railroad industry have changed. There is great pressure on operations to gain efficiencies for greater financial returns with increased traffic. This pressure has resulted in heavier axle loads and higher train speeds. Due to higher train speeds, shorter work windows exist for the conducting of ultrasonic inspection. Fifteen to 20 years ago, a typical rail life was 800 million gross tons. Today, 1.5 billion gross tons is not unusual for a 136-lb. rail (136-lb. is the force at which the rail undergoes yield deformation and is the standard rail rating). Federal regulations require immediate remediation of detected defects, regardless of the type size or the amount of traffic the rail has seen. It has been the industry standard to replace rail when six to eight defects are detected per mile per year. In the past, it was four defects per mile per year (Franke, 1997). A fleet of 30 detector cars can cover about 110,000 miles per year. On the average, every mile of track is inspected by a rail detector car at least three times a year. Table 2.1 is a list of
Details
-
File Typepdf
-
Upload Time-
-
Content LanguagesEnglish
-
Upload UserAnonymous/Not logged-in
-
File Pages36 Page
-
File Size-