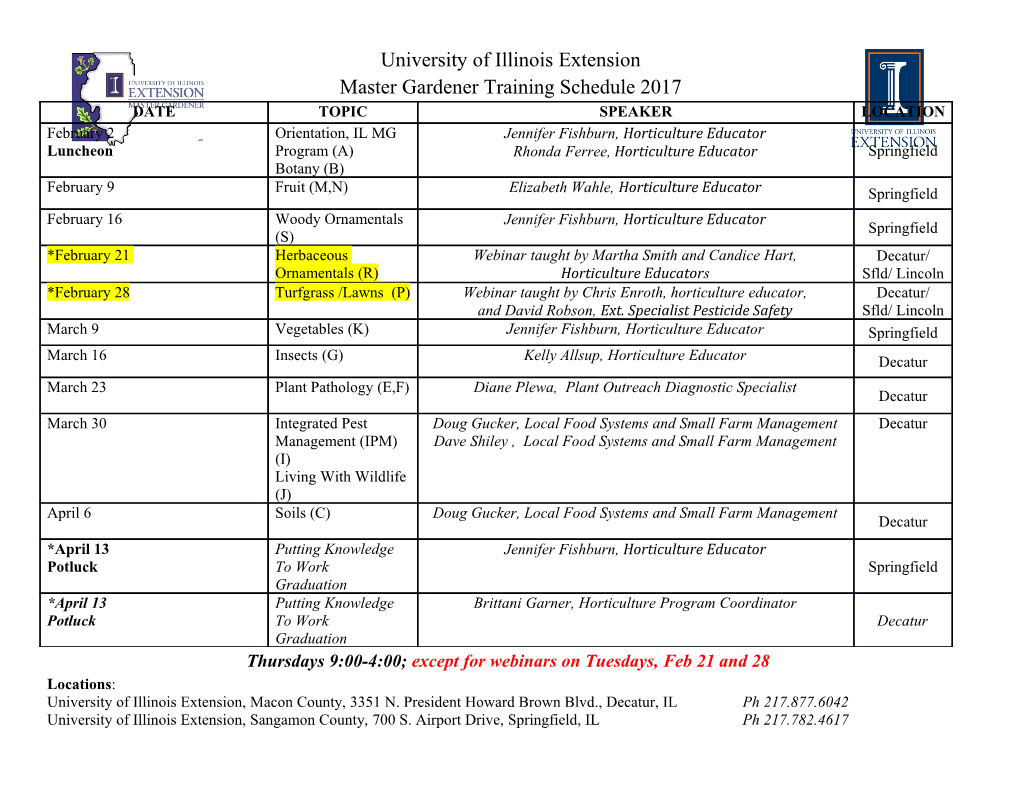
Journal of Thermal Engineering, Vol. 5, No. 6, Special Issue 10, pp. 141-148, December, 2019 Yildiz Technical University Press, Istanbul, Turkey A NEW APPROACH FOR EVALUATING THE RANKINE CYCLE THROUGH ENTROPY GENERATION A. Sinan Karakurt1,*, Umit Gunes1 ABSTRACT Increasing oil prices, the growing demand for energy, the adoption of new regulations for greenhouse gases and other harmful particulate emissions, as well as political instabilities and crises have necessitated the design of more efficient and environmentally-friendly plants. This paper presents a useful combination of mean cycle irreversibility (MCI) for thermodynamically optimizing the Rankine cycle using the MCI as the currently proposed criterion. The thermal irreversibilities and physical size of a system are evaluated together using the criterion that aims to minimize the ratio of the thermal irreversibilities or exergy destruction to a specified size that is characterized as the difference between the maximum and the minimum specific volumes of the cycle. The analyses consider the effects of different boiler-outlet or turbine-inlet pressures and temperatures, different condenser pressures, and different isentropic efficiencies on cycle performance. The results show that increasing the inlet temperature for a constant turbine-inlet pressure increases the MCI and increasing the turbine-inlet pressure at a constant inlet temperature decreases the MCI. With boiler pressure at 500 kPa, the boiler temperature increases from 500K to 600K, the MCI value increases nearly seven-fold, and thermal efficiency increases from 14% to nearly 16%. Also, the results show that the criterion gives more beneficial information to designers and engineers in terms of exergy destruction for designing more environmentally friendly and smaller thermal systems. Keywords: Rankine Cycle, Entropy Generation, Exergy Density INTRODUCTION The increases in global-energy demand, material and fuel prices, and restrictive emissions regulations has necessitated the design of more efficient, environmentally-friendly, and more compact thermal systems. In order to develop innovative systems, using all kinds of energy sources with smaller system more ecologically is important. In this context, using low-grade heat sources or recovering waste heat through different types of thermal applications, such as direct energy conversion or the Rankine cycle, which are well-known and widely- used technologies for energy production, is very important. Within this scope, low-pressure steam-turbine thermal systems have many application areas for energy production, from recovering the waste-heat energy of marine engines, diesel trucks, and industrial plants to renewable energy sources from solar, geothermal, or biogas or the fossil fuels used in small thermal plants. From the first steam engine to current technology, even throughout the history of thermodynamics, many technological achievements have been done in the names of increasing thermal efficiency and decreasing environmental destruction with smaller developed systems. In this regard entropy generation minimization (EGM), also known as “thermodynamic optimization” or “finite time thermodynamics,” has great importance in thermal system analyses. We should note that studies became crucial starting with Bejan’s [1,2]. EGM combines the fundamental principles of thermodynamics, heat transfer, and fluid mechanics. Also, Bejan illustrated how EGM can be applied to real devices. Plenty of studies are found to have focused on EGM, such as Martins’ [3] showing entropy generation in spark ignition engines and Haseli’s [4] analyzing the thermal performance of heat engines (i.e., Otto, diesel, and Brayton cycles). Tchanche et al. [5] presented applications for the the organic Rankine cycle (ORC) and analyzed their usage with solar energy, geothermal energy, biomass products, surface seawater, and waste heat from various thermal processes as a heat source. In addition to types of heat sources, Xiaojun et al. [6] developed mathematical models for investigating ORC’s feasibility for power systems working under conditions with 150– 350oC heat sources. They indicated ORC to have the highest thermal performance in cases with 150–210oC heat sources; steam-ORCs (S-ORCs) have higher thermal performance than steam Rankine cycles (SRCs) and ORC This paper was recommended for publication in revised form by Regional Editor Ali Celen 1 Department of Naval Architecture and Marine Engineering, Yildiz Technical University, Istanbul, Turkey *E-mail address: [email protected], [email protected] Orcid id: 0000-0002-6205-9089, 0000-0001-6942-6403 Manuscript Received 25 August 2019, Accepted 19 November 2019 Journal of Thermal Engineering, Research Article, Vol. 5, No. 6, Special Issue 10, pp. 141-148, December, 2019 systems in cases with 210–350oC heat sources. Andreasen et al. [7] also compared SRCs and ORCs for waste- heat recovery in marine engines. Their results show that, while ORCs have higher thermal performance at lower engine loads, SRCs have higher thermal performance at higher engine loads. Analyzing thermal efficiency and size has been very important because thermal performance is insufficient for a feasibility study; the system size also needs to be known. In this regard, Sahin et al. [8] defined a new expression for power density as the ratio of power to the maximum specific volume in the cycle. Therefore, they were able to include the effects of engine size in their thermal analysis. Ust et al. [9] indicated the ecological coefficient of performance (ECOP) to be the ratio of power output to the rate of loss of availability. They did the analysis using the ECOP objective function for generalized irreversible Carnot heat engines as well as the irreversible Brayton heat engine with variable-temperature thermal reservoirs using the ECOP objective function [10]. Yeginer et al. [11] presented their analysis of different thermodynamic cycles, such as Brayton, Rankine, and Otto. Chen et al. [12] gathered power, efficiency, entropy-generation rate, and ecological optimization studies and analyzed universal heat-engine cycles such as the Diesel, Otto, Brayton, Atkinson, dual, and Miller cycles. Karakurt and Sahin [13] have defined exergy density as the ratio of physical exergy to specific volume at a given point. Gunes et al. [14] also analyzed the effect of size on entropy generation for different types of waste-heat recovery boilers. The results show that, due to larger (dual pressure) boilers being more efficient, entropy generation is less per heat transfer compared to smaller (single pressure) boilers. Although ECOP [9] defines the energy production for unit exergy destruction or irreversibilities and sGen [1] defines the irreversibilities of the system, there is a lack of information about the relationship between exergy destruction and volume. The main objective of this study is to evaluate both exergy destruction and the dimensions of the thermal system together. The specific objective of this study is to analyze a low-grade Rankine power cycle using the proposed criterion of mean cycle irreversibility (MCI) and other performance criteria (ECOP, sGen and ηth) for different boiler temperatures, boiler pressures, condenser pressures, and isentropic efficiencies. The main objective of this study is to evaluate together both the exergy destruction and the dimensions of the thermal system. The specific objective of this study is to analyze a low-grade Rankine power cycle using the proposed criterion (MCI) and other performance criteria (ECOP, sGen and ηth) for different boiler temperatures, boiler pressures, condenser pressures, and isentropic efficiencies. THERMODYNAMIC MODEL The analyses have modeled the simple Rankine cycle’s four processes using Engineering Equation Solver (EES) [15]. The dead state/η conditions have been assumed as 298 K and 10 kPa for the Rankine cycle, the boiler temperature as 500 K, boiler pressure as 1000 kPa, and condenser pressure as 50 kPa; pressure losses are neglected in pipes and heat exchangers, working fluid is non-compressible, and the isentropic efficiency of the pump and turbine is 0.9. The values for the state properties (T, P, v, h, s, ex) of cycle points can be obtained from the property tables, and the exergy density (ρEx) [16] values can be calculated as the ratio of specific exergy to the specific volume at a point. The specific exergy values of state points can be calculated as in Equation 1 while neglecting the potential and kinetic exergies; and heat transfers (qH and qL) are calculated by assuming the specific enthalpy difference at the boiler and condenser units as from Equations 2 and 3. Thermal efficiency of the system can be calculated using Equation 4, (1) exm h m h0 T 0 (s m s 0 ) (2) qH h32 h (3) qL h41 h qqHL th (4) qH where m-values between 1 and 4 refer to cycle points and an m-value of 0 is the dead state conditions; h is the specific enthalpy in the kJ/kg unit, and s is the specific entropy in the kJ/(kg.K) unit, which are specifiable from the property tables of water. 142 Journal of Thermal Engineering, Research Article, Vol. 5, No. 6, Special Issue 10, pp. 141-148, December, 2019 Entropy generation is defined in Equation 5 as a comparative tool for combining real and finite times and finite size systems using the most basic concepts of heat transfer, fluid mechanics, and thermodynamics [1]. Total exergy destruction of the system can be calculated using Equation 6. qq s HL Gen (5) TTHL (6) ExDTot T0 s Gen where qH, (hot side of the heat transfer) is assumed to be equal to the heat addition to the cycle and also TH (hot- side source temperature) is equal to the maximum temperature of the cycle, T3. The variable qL (cold-side heat transfer) is assumed to be equal to the heat outlet from the cycle, and TL (cold-side source temperature) is equal to the minimum temperature of the cycle (T4) such that no temperature difference exists between the heat sources and heat machine. T0 refers to the ambient/dead-state temperature. The ecological coefficient of performance (ECOP) is defined in Equation 7 as the ratio of the net specific work to exergy destruction [17].
Details
-
File Typepdf
-
Upload Time-
-
Content LanguagesEnglish
-
Upload UserAnonymous/Not logged-in
-
File Pages8 Page
-
File Size-