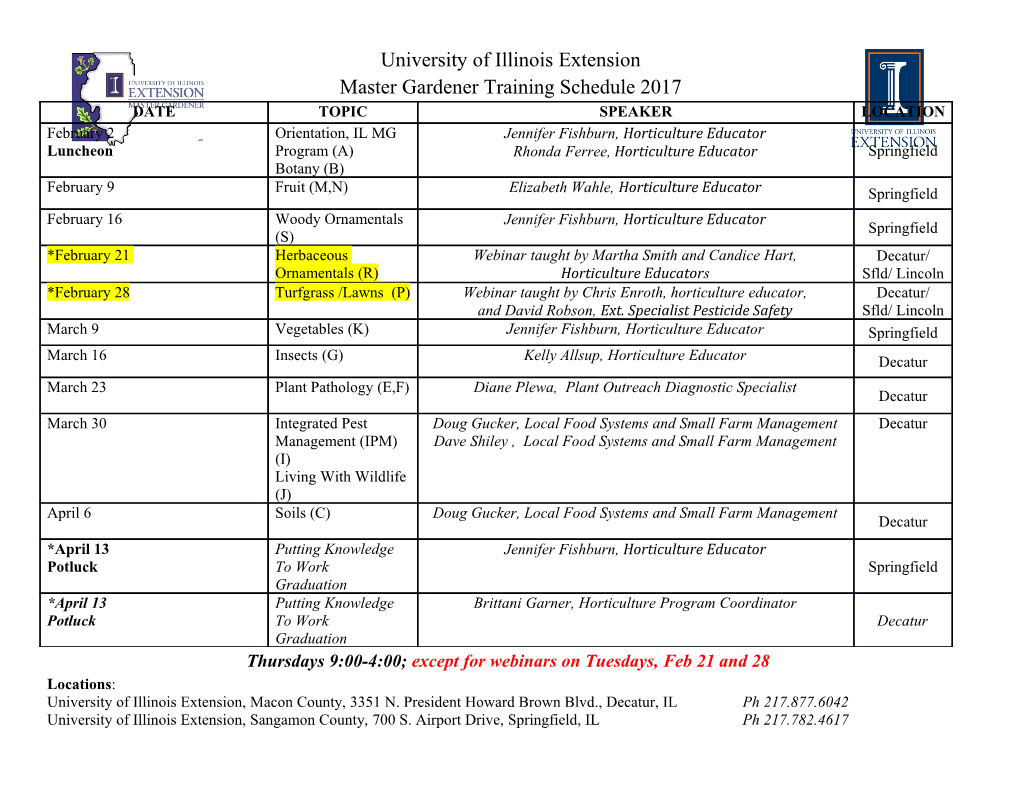
sensors Article Considerations for Determining the Coefficient of Inertia Masses for a Tracked Vehicle 1 1 1 2, Octavian Alexa , Iulian Coropet, chi , Alexandru Vasile , Ionica Oncioiu * 1 and Lucian S, tefănit, ă Grigore 1 Military Technical Academy “FERDINAND I”, 39-49 George Cos, buc Av., 050141 Bucharest, Romania; [email protected] (O.A.); [email protected] (I.C.); [email protected] (A.V.); [email protected] (L.S, .G.) 2 Faculty of Finance-Banking, Accountancy and Business Administration, Titu Maiorescu University, 040051 Bucharest, Romania * Correspondence: [email protected]; Tel.: +40-372-710-962 Received: 8 August 2020; Accepted: 28 September 2020; Published: 29 September 2020 Abstract: The purpose of the article is to present a point of view on determining the mass moment of inertia coefficient of a tracked vehicle. This coefficient is very useful to be able to estimate the performance of a tracked vehicle, including slips in the converter. Determining vehicle acceleration plays an important role in assessing vehicle mobility. Additionally, during the transition from the Hydroconverter to the hydro-clutch regime, these estimations become quite difficult due to the complexity of the propulsion aggregate (engine and hydrodynamic transmission) and rolling equipment. The algorithm for determining performance is focused on estimating acceleration performance. To validate the proposed model, tests were performed to determine the equivalent reduced moments of inertia at the drive wheel (gravitational method) and the main components (three-wire pendulum method). The dynamic performances determined during the starting process are necessary for the validation of the general model for simulating the longitudinal dynamics of the vehicle. Finally, the differential and algebraic equations of the virtual model approximate more accurately the actual process of the operation of the vehicle. The virtual model, through the data obtained from the simulation process, allows for the determination, indirectly, of the variation of the mass moment of inertia coefficient and its expression of approximation. Keywords: tracked vehicle; mobility; stability; acceleration; torque converter; engine; coefficient of inertia masses; hydro-clutches 1. Introduction The acceleration resistance generated by the inertial forces during the starting process of the vehicle depends not only on its weight but also on the rotating masses, from the traction engine elements to the vehicle tracks [1]. According to the relation of the moments of inertia δ [-] [2], the resistance generated by the inertia of the rotating elements depends not only on the mass but also on their radius. In the literature [3–5], the effect generated by the moving masses of translation and rotation is materialized in the form of the mass moment of inertia coefficient δ [6]. The mobility and stability of a vehicle on wheels or tracks are influenced by the moment of inertia [7] but also by the place (on the ground) where gravity acts [8,9]. In [10] is presented a database of the National Highway Traffic Safety Administration (NHTSA), which presents a methodology for calculating not only moments of inertia and center of gravity but also the physical characteristics of the vehicle. Sensors 2020, 20, 5587; doi:10.3390/s20195587 www.mdpi.com/journal/sensors Sensors 2020,, 2020,, 5587x FOR PEER REVIEW 2 of 3135 tracks [10–12]. The Matlab programming environment—SIMULINK and SIMSCAPE modules—was usedThe to developmentdevelop the ofgeneral the virtual simulation simulation model model. The aimed simulation at modeling model, the main which parts refers of a trackedto the vehicle,determinationSensors such 2020,as 20of, the xthe FOR 8power PEER V engine, REVIEW flow, theis built hydromechanical modularly, and transmission, the data on the the characteristics final transmission, of the2 of physical and 35 the trackscomponents, [10–12 ].used The for Matlab the construction programming of the environment—SIMULINK hydromechanical transmission, and SIMSCAPE are found modules—was in [13,14]. The usedmodular-typetracks to develop [10–12]. simulation the The general Matlab model simulation programming was generated model. envi Theronment—SIMULINK due simulation to the fact model, that itand whichwill SIMSCAPE be refers able to modules—was be the modified determination later, ofdepending theused power to on flow,develop the ischaracteristics builtthe general modularly, ofsimulation the and respecti the model datave on.components, The the simulation characteristics which model, come of thewhich from physical refers othercomponents, toequipment the determination of the power flow, is built modularly, and the data on the characteristics of the physical usedmanufacturers. for the construction of the hydromechanical transmission, are found in [13,14]. The modular-type components, used for the construction of the hydromechanical transmission, are found in [13,14]. The simulation model was generated due to the fact that it will be able to be modified later, depending on modular-typeThe virtual simulationsimulation model model was ha generateds as input due elements to the fact the that experi it will bemental able to data be modified provided later, by the themanufacturer, characteristicsdepending theon the ofmain thecharacteristics mass respective and dimensional of components, the respecti characteristicsve which components, come fromof which the other vehicle, come equipment from gearshift other manufacturers. times,equipment obtained experimentallymanufacturers.The virtual after simulation experimental model determination has as input of elementsthe pressure the variation experimental in the data hydraulic provided control by thesystem manufacturer, atThe changing virtual the simulationgears main [3], mass andmodel the and ha positions dimensional as input of elementsthe characteristicsaccelerator the experi pedal.mental of the The data vehicle, output provided gearshiftelements by the times,of the obtainedvirtualmanufacturer, model, experimentally generated the main after aftermass experimental andrunning dimensional the determinationprogra characteristicsm (simulation of of thethe pressurevehicle,process), gearshift variation show times, the in variation theobtained hydraulic over controltime experimentallyof systemthe main at changingdynamic after experimental characteristics gears [3], determination and theof the position tracked of the of pressure thevehicle accelerator variationand of the pedal. in themass hydraulic The moment output control of elements inertia ofcoefficient, thesystem virtual andat model,changing are shown generated gears in [3], Figure and after the1. running position the of programthe accelerator (simulation pedal. The process), output elements show the of variation the overvirtual time of model, the main generated dynamic after characteristics running the progra of them tracked (simulation vehicle process), and of show the mass the variation moment over of inertia time of the main dynamic characteristics of the tracked vehicle and of the mass moment of inertia coefficient, and are shown in Figure1. coefficient, and are shown in Figure 1. Figure 1. General virtual simulating model of the tracked vehicle [1]. FigureFigure 1. 1.General General virtual virtual simulatingsimulating model model of of the the tracked tracked vehicle vehicle [1]. [1]. The evaluation of the parameters necessary to determine the moments of inertia by the The evaluation of the parameters necessary to determine the moments of inertia by the gravitationalThe evaluation method of Figure the parameters 2 is based necessary on detaching to determine the tracks the momentsfrom the ofdrive inertia wheel by theand gravitational attaching a methodgravitational Figure2 methodis based Figure on detaching 2 is based theon detaching tracks from the tracks the drive from wheel the drive and wheel attaching and attaching a cylindrical a cylindricalcylindrical device. device. Its Itsrole role is isto to wind wind a a cable cable around it,it, which which has has a weighta weight hanging hanging from from the other the other device. Its role is to wind a cable around it, which has a weight hanging from the other end. end. end. Figure 2. Schematic for the installation for measuring the moments of inertia of the transmission of a tracked vehicle, using the gravitational method. Figure 2. Schematic for the installation for measuring the moments of inertia of the transmission of a tracked vehicle, usingusing thethe gravitationalgravitational method.method. Sensors 2020, 20, 5587 3 of 31 The weight is hung by means of a pulley of a crane-type support. The working principle is as follows: the driver connects a stage of the hydromechanical transmission with an external pressure source, releases the brakes and the weight begins to fall. Knowing the weight value, the radius of the cylindrical device, the distance traveled by the weight and the fall time, analytical calculations can be performed to determine the moment of inertia [15]. Performing the same operations for both drive wheels will make it possible to determine the overall moment of inertia. The experimental determination of the mass moment of inertia coefficient [16] aims to highlight its implications for the dynamic performance of the vehicle, in particular for the variation of speed, acceleration and space traveled during the starting process. Another parameter necessary to be verified is the dependence of the mass moment of inertia coefficient on the transmission
Details
-
File Typepdf
-
Upload Time-
-
Content LanguagesEnglish
-
Upload UserAnonymous/Not logged-in
-
File Pages31 Page
-
File Size-