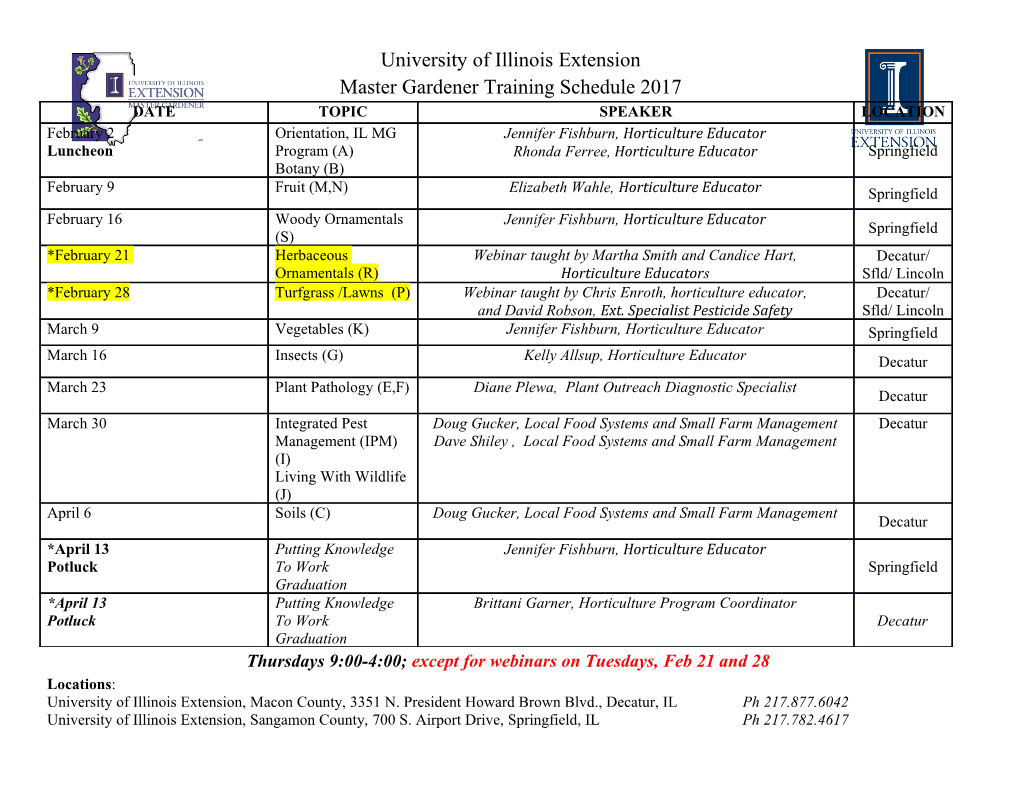
Analyst Insight Who’s the Winner- Prismatic Battery vs. Pouch Battery? Contents ■ Production State of Electric Vehicle Battery by Company (Prismatic Battery, Pouch Battery) ■ Assembling Features of Prismatic Battery/Pouch Battery ■ Comparison between Prismatic Battery & Pouch Battery by section (process/price/Delivery/stability/reliability) ■ Implications • Outline : The confrontation between prismatic battery and pouch battery in the medium-large sized lithium battery market is interesting. Arguments on the performance superiority between prismatic battery, represented by Samsung and Panasonic and pouch battery, represented by LG and AESC are intense. First of all, LG Chem, which is ranked first on the number of contracts on electric vehicle as well as a representative of pouch battery, is raging. It has signed contracts with GM, Ford, Renault, Hyundai, Volkswagen as well as Daimler. Samsung SDI is also expanding its market share on prismatic battery centered on BMW and Volkswagen. Analyst Insight ■ Electric Vehicle Battery Production by Company LG Chem, which is the forerunner of vehicle battery market, has been conventionally manufacturing pouch battery. Ever since LG Chem started to produce battery used in electric vehicles, the company did business with over 20 automobile enterprises and has the most number of customers ranging from Hyundai and Kia Motors, General Motors (GM), Ford, Renault, Volvo, Shanghai Automotive Industry Corporation, Changan Automobile, China FAW Group Corporation, and Koros. Through commercialization of GM Volt in September 2010, the safety and reliability of pouch battery has been acknowledged and it is receiving attention from many vehicle manufacturers. Other than this, Korean enterprise SK Innovation and AESC of Japan are also producing pouch-type battery. Samsung SDI and Panasonic (old name: Sanyo) are the representatives of prismatic battery. Samsung SDI has won a contract with BMW, Volkswagen, Chrysler, Audi, Mahindra, Delphi, Porsche and Fiat, and is supplying prismatic battery. Following the contract that Samsung SDI had made with BMW in August 2008 on exclusive supply of battery, the company signed other contracts with BMW in July 2014 on electric vehicles i3,i8 and further on developing model of HEV to provide batteries. The main clients of xEV battery of Panasonic are Toyota Motors of Japan, Ford, Volkswagen and Audi. The enterprise is also supplying lithium-ion battery to Plug-in Prius vehicle of Toyota through PEVE, which is a joint venture with Toyota. Panasonic is also supplying small cylindrical battery to Tesla. ATL, distinctively, chooses to produce pouch battery for small-sized battery, and prismatic battery for medium to large sized battery. Type Battery Manufacturer Vehicle Makers Square-Type Samsung SDI, Panasonic, BMW, Volkswagen, PEVE, BYD, ATL etc. Toyota etc. Pouch-Type LG Chem, AESC, SK GM, Ford, Renault, Volvo, Innovation etc. Nissan, Hyundai Kia etc. Cylindrical type Panasonic TESLA Analyst Insight ■ Assembly Features of Prismatic/Pouch Battery - Prismatic battery The outer case of prismatic battery is made out of aluminum, and the main components include can, gasket, cap plate, insulator, terminal plate, cap assy that binds pin into one module, and PP Case. Laser beam welding Tab welding Can-Cap welding Insert Ball Electrolyte welding (Source : SNE Report “<2015> LIB Key 4 Components Technology Trends and Manufacturing Process”) J/R Insert : The process of inserting jelly roll after being winded. Checks for the depth of jelly roll insert and for any damages. Tab welding : Negative tab is welded through resistance welding while positive tab is welded through ultrasonic. Can-Cap welding : The process of welding and sealing the junction between can and cap assembly through laser. Inserting Electrolyte : Inserting optimal level of electrolyte and wetting it into the electrode in a form of jelly roll in a short period of time. Ball welding : Pressing in the in-gate of electrolyte with a ball, and welding it with laser. Finishing off with UV hardener after welding. Analyst Insight ■ Assembly Feature of Prismatic/Pouch Battery - Pouch battery Most pouch battery has a similar design specification with prismatic battery, but uses a pouch case and it is possible to design it as ultra-thin and with high energy density. Also, it is very flexible with size, so it possesses the advantage of freely designing the capacity as well as its size. <Folding> <Vacuum Impregnation> <J/R Insert> <1st Sealing> <Insert> <2nd Sealing> (Source : SNE Report “<2015> LIB Key 4 Components Technology Trends and Manufacturing Process”) Forming : The process of creating a room in the pouch for jelly roll (J/R). Secures specified room in the pouch through press machine, and makes it easy to insert jelly roll. J/R Insert : Insert jelly roll (J/R) to accurate position in the formed pouch through winding or laminating Folding & 1st Sealing : After enfolding jelly roll located at one side of the pouch without any damage, first sealing is done to fix jelly roll in place and seal 3 sides of the pouch, getting it ready to insert electrolyte. Insert Electrolyte : Inserts optimal amount of electrolyte into the pouch with three-sides sealed, repeats giving it vacuum and pressure. Vacuum Impregnation & 2nd Sealing : Process to equally disperse the inserted electrolyte. It is impregnated through vacuumed chamber, and vacuum and pressure process is used simultaneously if needed. Last side of the pouch is sealed through 2nd sealing once electrolyte is inserted completely. Analyst Insight ■ Comparison between Prismatic Battery & Pouch Battery by section (process/price/Delivery/stability/reliability) - Process (Prismatic Battery favorable) As prismatic battery uses winding method of electrode jelly roll, it is easier to control the process, and it is also favorable in regards to the production speed. Pouch battery uses stacking & folding method of electrode jelly roll (in the case of LG Chem), so there is a possibility of damage at the end of jelly roll and the production speed is slower than that of prismatic battery. However, LG Chem has made improvements through production technology. - Price (similar) The price of pouch used in pouch battery is higher than that of CAN used in prismatic battery, but more components of cap assy’ is used in prismatic battery than pouch battery, giving prismatic battery a disadvantage. - Delivery (Pouch battery favorable) The production of mold to make CAN in prismatic battery is long, while pouch battery is favorable in terms of delivery responsiveness. - Stability (similar) In the case of batteries used in vehicles, both types are vulnerable to shock. Therefore, design and technology that will prevent impact for both module and pack is important, and several safety devices are needed. Also, technology that will allow no short to occur inside both prismatic and pouch battery is important. - Reliability (Prismatic battery favorable) Pouch battery is more favorable in terms of prevention of radiation as it can make the cell thinner, but once the battery is made in units of pack, prismatic battery is more safe to vibration or shocks. Analyst Insight ■ Implications It is difficult to determine between prismatic battery and pouch battery on which battery is more favorable. Both prismatic battery and pouch battery have its own advantages and disadvantages, and manufacturers are trying to overcome through their own technology. Vehicle manufacturers also ponder between using prismatic battery and pouch battery. There are moves to change from prismatic battery to pouch battery, and vice versa. In such situation, Europe prefers prismatic battery while United States prefer pouch type. However, it is difficult to predict how the situation might change and the attention is on which battery type will become more favorable. SNE Research host a seminar in COEX between 27th and 28th of April. It will allow the participants to apprehend battery technology of each type through speakers from Samsung SDI and LG Chem, companies representing each battery type. Joint venture of SDI, Bosch Absorbed to SDI Joint venture of NEC, Nissan A123 taken over by Chinese Wanshang Group Joint venture with Daimler Joint venture of Panasonic, Toyota Joint venture of Honda, GS Yuasa *organized centered on supply performance *Chinese corporates excluded Joint venture of Mitsubishi, GS Yuasa (Source : SNE Report „Strategy Analysis on Leading LIB Manufacturers‟) Analyst Insight .
Details
-
File Typepdf
-
Upload Time-
-
Content LanguagesEnglish
-
Upload UserAnonymous/Not logged-in
-
File Pages8 Page
-
File Size-