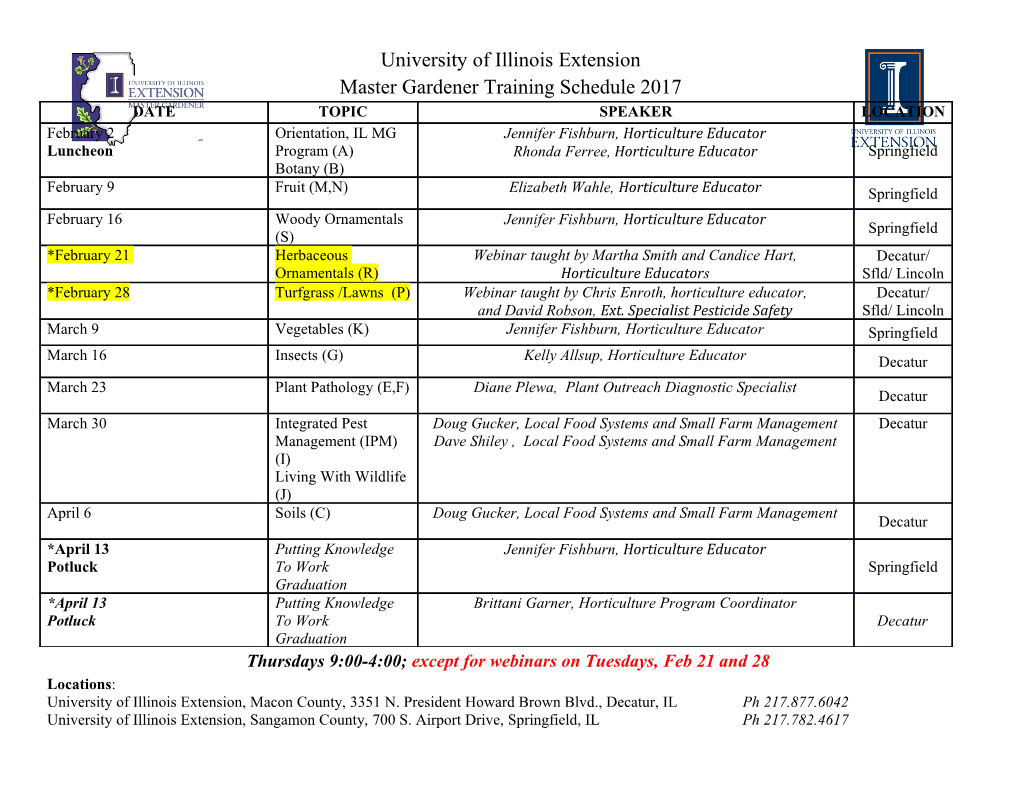
MODELING AND OPTIMIZATION OF A CATALYTIC NAPHTHA REFORMER by UNMESH MOHAN TASKAR, B.S.Ch.E. A DISSERTATION IN CHEMICAL ENGINEERING Submitted to the Graduate Faculty of Texas Tech University in Partial Fulfillment of the Requirements for the Degree of DOCTOR OF PHILOSOPHY Approved May, 1996 ,.„.3'6 ACKNOWLEDGMENTS When one is so closely involved with an organization and one project for a period of over four years, it becomes a monumental task to try to acknowledge all the people who have influenced you in various different ways. However, it also becomes imperative, due to the valuable contributions that they make towards your life and work, to attempt to perform this task right at the beginning. The following text is just a result of that attempt. First of all, I wish to express my sincere thanks to E>r. James B. Riggs for providing me with the opportunity to work on this project, and also for his guidance and constant support during the course of this work. There were quite a few valuable skills, academic as well as non-academic life to leam from him. He will always be remembered for the free spirit that he represents so vividly. I also wish to extend my sincere thanks to Dr. Russ Rhinehart for his valuable insights during my stay at Texas Tech. In my eyes, he is a rare combination of a good researcher and a good engineer, something that makes him a person who can be counted on to solve problems in a practical manner, but based also on a sound theoretical background. His ability to methodically approach any problem and "think" the way out of it is something that I would like to successfully imitate some day. I would also like to thank my other committee members, Uzi Mann and Surya Liman, for their assistance in the project. Special thanks go to Ed Sugrue from Phillips Petroleum for his v^llingness to take the time to answer all my questions and providing us with other valuable help. I would also like to thank Dave Hoffinann from the Dynamic 11 Matrix Control for giving me the opportunity that only a few months ago would not have seemed possible. There is no way that this section on acknowledgments could even come close to completion without mentioning my fellow graduate students. Let me start by mentioning my late night officemates Bob, Scott, Ash, and Ravi without whom those long hours in the night would have become unbearably long. With so many people that provided me their support and influenced my life in different ways; Suhas, Siva, Mahesh, Vikram, Hoshang, Kermeen Tausha, Paul, Rick, Joe, Sonemaly, Prabhu and Geetha, Crams, Rohit, Yogesh, Dr. Chung, Dutta, Steve, Himal, Sandeep, Vikas, Kedar... , the list is almost endless. I really wish to express my most sincere thanks to all of you guys. In the end, I would like to say that all of this could be possible only because of constant love and encouragement by my mother and father and other family and friends back home. I owe a large part of whatever I have achieved so far, including this work, to them. m TABLE OF CONTENTS ACKNOWLEDGMENTS ii ABSTRACT vi LIST OF TABLES viii LIST OF FIGURES x CHAPTER 1. INTRODUCTION 1 1.1 Catalytic Naphtha Reforming 1 1.2 Optimization of a Catalytic Naphtha Reformer 2 1.3 Phenomenological Simulation Model 3 1.4 Organization of Dissertation 4 2. LITERATURE SURVEY 6 3. CATALYTIC NAPHTHA REFORMER: PROCESS DESCRIPTION AND CHEMICAL REACTIONS 13 3.1 Process Description 13 3.2 Chemistry of Catalytic Naphtha Reforming 17 3.3 Catalyst Deactivation 23 3.4 Reforming Catalysts 24 4. MODEL DEVELOPMENT 27 4.1 Kinetic Modeling 28 4.2 Kinetics of Deactivation 39 IV 4.3 Modeling of Fixed-Bed Reactors 4 J 4.4 Modeling of Product Separator 50 4.5 Incorporating Recycle Phenomena in the Model 52 4.6 Recycle Gas Compressor Power Calculation 54 4.7 Modeling of Reactor Eftluent-to-Feed Exchanger 55 4.8 Description ofthe Overall Model 56 5. MODEL BENCH MARKING 60 5.1 Feed Characterization 66 5.2 Data Verification 75 5.3 Parameter Estimation 79 6. MODEL VERIFICATION 95 6.1 Profiles along the Length of the Catalyst Bed 96 6.2 Profiles over the Life ofthe Catalyst 102 6.3 Sensitivity Studies 104 7. OPTIMIZATION 120 7.1 Formulation of the Optimization Problem 120 7.2 Optimization Results 134 8. DISCUSSION, CONCLUSION AND RECOMMENDATIONS 157 BIBLIOGRAPHY 163 ABSTRACT Catalytic naphtha reforming is one ofthe key processes in petroleum refining, converting gasoline boiling range low-octane hydrocarbons to high-octane compounds which can be blended into gasoline. Other valuable byproducts include hydrogen and cracked light gases. Modeling of a t)^ical semi-regenerative catalytic reformer has been carried out involving most its key constituent units. Kinetic modeling ofthe reactions occurring in the fixed bed reactors connected in series formed the most significant part ofthe overall simulation effort. A reaction scheme involving 36 pseudocomponents connected together by a network of 35 reactions for components in the C5-C10 range has been modeled. The Hougen-Watson Langmuir-Hinshelwood type reaction rate expressions are used to represent rate of each reaction. Deactivation ofthe catalyst was modeled by including the corresponding equations for coking kinetics. The kinetic model was parameterized by bench marking the kinetic model against plant data. A feed characterization procedure was developed to infer the composition of chemical species in the feed and reformate from the given ASTM distillation data. A non­ linear regression procedure was carried out to calculate the rate parameters that provided the best match between the model and the plant data. The key to most optimum reformer operation lies in choosing the four catalyst bed inlet temperatures, and recycle ratio. Sometimes, in practice, four beds are operated at same inlet temperatures and varying influence of each bed behavior on the outlet VI properties is not taken into account. This leads to a sub-optimal operation. It is also important to consider the objective fiinction over the entire catalyst run-length, which has been predetermined for optimization analysis. The optimization analysis was conducted in two stages. In the first stage, the decision variables are optimized but held constant throughout the life ofthe catalyst. This time-invariant mode of operation shewed a significant improvement in objective function over the base case. In the second stage of the analysis, the problem was expanded to optimize the path ofthe decision variables over the run-length. This time-optimal problem also showed a substantial improvement in profits over the time-invariant case. Finally, sensitivity of objective fiinction to uncertainties in model parameters was examined. vii LIST OF TABLES 4.1 Reaction rate equations obtained by analyzing experimental conversions for C? hydrocarbons 38 4.2 The coking reaction scheme and rate equations, for C? hydrocarbons 44 5.1 Feed and reformate analysis and flows in the given data 63 5.2 Composition and flows of separator gas, stabilizer gas and stabilizer liquid in the given data 64 5.3 Reactor bed temperatures, pressure, and catalyst bed weights 65 5.4 ASTM data and corresponding TBP data for catalytic naphtha reformer feed 68 5.5 Correlation constants for Equation 5.3 71 5.6 Calculated properties for the TBP fractions of Table 5.4 72 5.7 Computed mole fractions of components in each TBP fraction of Table 5.4 73 5.8 Calculated overall mole fraction of components in feed 74 5.9 Comparison between calculated and predicted PNA analysis ofthe feed 76 5.10 Material balance test for the data set selected to bench mark the catalytic naphtha reformer 78 5.11 Hydrogen balance test for the data set selected to bench mark the catalytic naphtha reformer 80 5.12 Molar flow rates of hydrocarbon species at the outlet of last reactor bed computed from given industrial data 84 5.13 Parameter values computed by least squares regression on data in Table 5.12 92 5.14 Rate parameters for coking reactions 93 viii 7.1 Product values and operating costs ^23 7.2 Distribution ofthe overall objective fiinction in terms of its constituents 1-"^ 7.3 Optimum operating conditions for the time-invariant mode of operation 1^6 7.4 Optimum operating conditions for the time-invariant mode of operation, for varying feed types 1^9 7.5 Model parametric sensitivity analysis 1^^ IX LIST OF FIGURES 3.1 Process flow scheme ofthe catalytic naphtha reformer 14 4.1 Reaction network for the kinetic model 34 4.2 Program flow-chart for the catalytic naphtha reformer 58 6.1 Temperature profile through reactor system 97 6.2 Profile of main component types through reactor system 99 6.3 Volumetric reformate yield and research octane number along the reactor system 101 6.4 Accumulation of average coke content in each bed over the life ofthe catalyst 103 6.5 Variation of volumetric reformate yield and octane number over the life of the catalyst 105 6.6 Sensitivity of products to first bed inlet temperature 107 6.7 Sensitivity of products to second bed inlet temperature 108 6.8 Sensitivity of products to third bed inlet temperature 109 6.9 Sensitivity of products to fourth bed inlet temperature 110 6.10 Sensitivity of products to recycle ratio 112 6.11 Sensitivity of products to first bed inlet temperature over the catalyst life 114 6.12 Sensitivity of products to second bed inlet temperature over the catalyst Ufe 115 6.13 Sensitivity of products to third bed inlet temperature over the catalyst life 116 6.14 Sensitivity of products to fourth bed inlet temperature over the catalyst life 117 X 6.15 Sensitivity of products to recycle ratio
Details
-
File Typepdf
-
Upload Time-
-
Content LanguagesEnglish
-
Upload UserAnonymous/Not logged-in
-
File Pages179 Page
-
File Size-