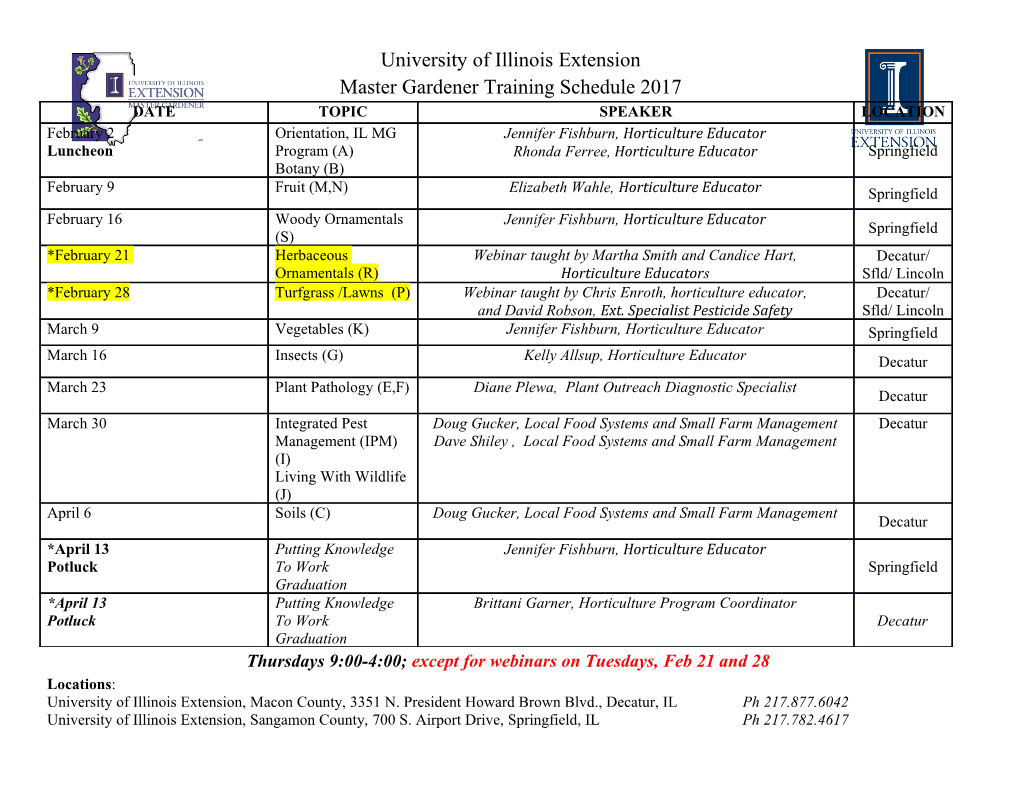
3,536,479 United States Patent Office attented Oct. 27, 1970 2 a hydrogen pressure of at least about 15 pounds per 3,536,479 square inch gauge (p.S.i.g.). METHOD FOR THE PRODUCTION OF HIGH PURTY (OSMUM The concentrated osmium-containing solution can ad Alexander Ellis, Clarkson, Ontario, and Alan Manson, vantageously be prepared from a dilute osmium-contain Oakville, Ontario, Canada, assignors to The Interna 5 ing solution as described hereinafter. However, most gen tional Nicke Company, Inc., New York, N.Y., a cor erally the concentrated solution will be prepared by poration of Delaware scrubbing gases containing osmium tetroxide with a Solu No Drawing. Filled Dec. 13, 1967, Ser. No. 690,083 tion containing, by weight, about 5% to 40% sodium hy Claims priority, application Canada, Feb. 21, 1967, droxide to produce a sodium perosmate solution which 983,421 10 contains about 5 grams per liter (gp.l.) to about 100 nt. C. C22b 7/00, 11/04 g.p.l. of osmium, e.g., about 60 g.p.l. of osmium. Gen U.S. C. 75-108 29 Claims erally at this stage only minor amounts of ruthenium, i.e., less than about 0.5 g.p.l. of ruthenium, accompany the osmium and can be precipitated with only minor ABSTRACT OF THE DISCLOSURE 5 amounts of osmium occluded therein from the concen Metallic osmium is recovered from a slurry of an trated osmium-containing solution by adding a Water osmium-containing material to which sufficient hydro soluble, mild organic reducing agent such as methyl al chloric acid has been added to assure a final pH value cohol and ethyl alcohol. The mild organic reducing agent in the slurry of about 1 to 9 by heating the slurry to a also reduces the sodium perosmate in solution to the temperature of at least about 150 F. under a hydrogen 20 sodium osmate state which is highly advantageous since pressure of at least about 15 p.S.i.g. sodium perosmate solutions display substantial vapor pressures even at room temperature whereas sodium os mate solutions at room temperature display only negli The present invention relates to the recovery of gible vapor pressures. In order to precipitate ruthenium osmium, and more particularly to recovery and purifi 25 and to reduce sodium perosmate to sodium osmate, the cation of osmium by hydrometallurgical techniques. mild organic reducing agent is added to the concentrated It was long suspected that the nickel-containing com osmium-containing solution at least in amounts effective plex sulfide ore deposits of the Sudbury district of On to reduce sodium perosmate to sodium osmate and to tario, Canada, contained osmium but the presence of precipitate ruthenium, e.g., about 1% to about 10% by osmium in recoverable amounts was only confirmed re 30 volume of the alkaline solution and advantageously about cently when it was determined that most of the osmium 4% to about 6%. Advantageously, the volatilized osmium was lost during treatment of the slimes resulting from tetroxide is collected in an alkaline scrubbing solution the electrorefining of nickel. U.S. patent application Ser. containing the water soluble, mild organic reducing agent No. 506,899 filed on Nov. 8, 1965, now Pat. No. to increase the scrubbing efficiency and to precipitate 3,413,114, discloses that osmium-bearing materials such ruthenium. as secondary nickel anode slimes can be treated to con Metallic osmium sponge is precipitated from solution centrate the precious metal content without undue losses by adding sufficient hydrochloric acid to the solution to of osmium being encountered by treating the anode slimes provide after precipitation a final pH value of about 1 with sulfuric acid at temperatures below about 500 F. to 9. The hydrochloric acid addition is required to neu to sulfate the base metals such as copper and nickel 40 tralize excess alkali and the control of the final pH is and removing the sulfated base metals by leaching. The important since at pH values below about 1 precipitation residue containing osmium is then treated to oxidize and is incomplete and the osmium sponge is likely to be con volatilize osmium as osmium tetroxide which is collected taminated as a result of corrosion of the apparatus and in an alkaline solution such as sodium hydroxide to form at pH values above about 9 precipitation is also incom a dilute osmium-containing solution. The dilute osmium 45 plete. Advantageously, the hydrochloric acid addition is containing solution is then treated to form a more con controlled so that after precipitation the final pH value centrated solution of sodium osmate from which osmium is between about 4 and 7. Substantial precipitation of is then recovered. Treatement of the dilute alkaline solu osmium occurs upon addition of the hyrochloric acid to tion to ultimately recover osmium required a number of the concentrated solution resulting in a slurry. Although carefully controlled operations and often involved inter 50 the hydrochloric acid can be added directly to the con mediate products which presented materials-handling centrated sodium osmate solution, such direct additions problems. are not always accurate and there is a distinct possibility It has now been discovered that purified metallic os of osmium losses due to volatilization of osmium tetrox mium sponge can be recovered from concentrated osmi ide. Therefore, it is highly advantageous to treat the um-containing solutions in an economic manner and that 55 concentrated sodium osmate solution to produce an os dilute solutions of osmium can be treated to form con mium-containing material to which accurate hydrochloric centrated osmium-containing solutions from which metal acid additions can be made without encountering losses lic osmium sponge of high purity can be precipitated. of osmium through volatilization. Such an osmium-con It is an object of the present invention to precipitate taining material can be produced by the intermediate step metallic osmium sponge from concentrated osmium 60 of adding an excess of a potassium hydroxide solution, containing solutions. advantageously as a saturated solution of potassium hy It is a further object of the present invention to produce droxide, to the concentrated sodium osmate solution to concentrated and purified osmium-containing solutions precipitate violet crystals of potassium osmate, from which metallic osmium sponge can be precipitated. Broadly stated, the present invention contemplates a KOsO4.2H2O process for precipitating osmium from an aqueous solu After separation, washing with alcohol and water and tion by forming a concentrated osmium-containing slurry then with pure alcohol and drying, the violet crystals of which contains sufficient hydrochloric acid to give a final potassium osmate can be slurried with cold water and pH value between about 1 and 9 after precipitation and 70 easily determined stoichiometric amounts of hydrochloric then precipitating metallic osmium sponge by heating the acid are added to provide a slurry which can readily be slurry to a temperature of at least about 150 F. under treated with hydrogen at elevated temperatures and pres 3,536,479 3 4. sures to precipitate metallic osmium sponge. Regardless When the evolution of gases such as sulfur dioxide sub of whether hydrochloric acid additions are made directly sides or ceases, an oxidizing reagent such as Sodium chlo to the concentrated Sodium osmate solution or to a slurry rate, sodium bromate or nitric acid in amounts equivalent of precipitated potassium osmate crystals, metallic os to sodium chlorate additions from about 1% to about mium sponge is precipitated from the resulting osmium 10%, by weight of the pulp, is added to the pulp. Heat containing solution by heating the solution to a temper ing is then continued to volatilize osmium tetroxide which ature of at least about 150 F., e.g., about 200 F. to is collected in a solution of about 5% to about 40% 350 F. and at a hydrogen partial pressure of at least Sodium hydroxide, by weight, to form a purified con about 15 p.s.i.g., e.g., advantageously about 300 p.s.i.g. centrated sodium perosmate solution. to 700 p.s.i.g. O In carrying the invention into practice, it is preferred Metallic osmium sponge precipitated from solution by to gradually heat an osmium-containing material which hydrogen reduction contains substantial quantities of ad can also contain Sulfur, Selenium and ruthenium to a sorbed hydrogen and trace amounts of other impurities temperature of from about 1200' F. to about 2000 F. and can be purified by washing the osmium sponge with at a rate of about 50 F. to 100 F. per hour in a free an aqueous solution of hydrochloric acid at a temperature oxygen-containing atmosphere to volatilize osmium as below about 100 F., e.g. at room temperature. Impur osmium tetroxide. Gradual heating is necessary to avoid ities such as iron, nickel and chromium react with the fusion of the osmium-containing material before osmium aqueous solution of hydrochloric acid to form soluble is volatilized therefrom. The osmium tetroxide along with chlorides which are removed from the osmium sponge sulfur, Selenium and dust is collected in an aqueous so while adsorbed hydrogen is concomitantly released. The dium hydroxide solution to form a dilute osmium-con aqueous solution of hydrochloric acid advantageously has taining solution. The aqueous sodium hydroxide solution a normality of about 0.5 to 5. advantageously contains between about 5% and 40% Another advantageous embodiment of the present in Sodium hydroxide by weight. An osmium-containing pre vention is to heat osmium sponge purified in accordance cipitate is recovered from the Solution without separation with the present invention to a temperature of at least of the solids from the collecting solution since the solids about 1500 F.
Details
-
File Typepdf
-
Upload Time-
-
Content LanguagesEnglish
-
Upload UserAnonymous/Not logged-in
-
File Pages5 Page
-
File Size-