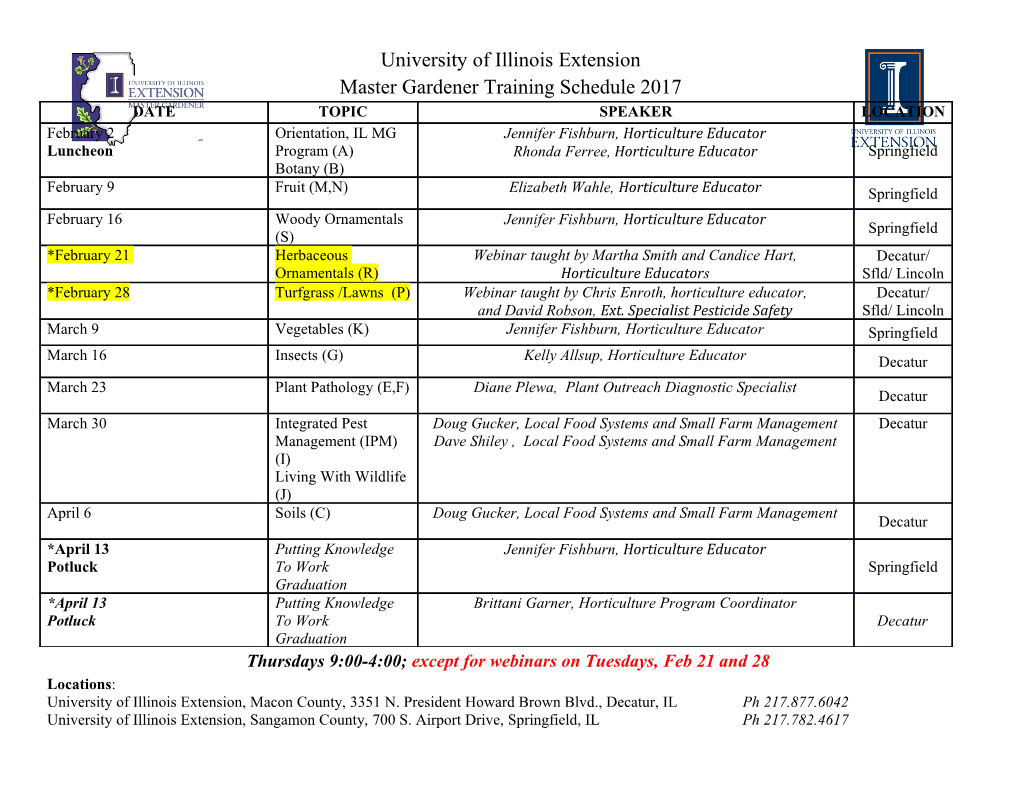
<p></p><ul style="display: flex;"><li style="flex:1">A</li><li style="flex:1">R</li><li style="flex:1">T</li><li style="flex:1">I</li><li style="flex:1">C</li><li style="flex:1">L</li><li style="flex:1">E</li></ul><p></p><p><a href="/goto?url=https://doi.org/10.1038/s41467-019-12938-4" target="_blank">https://doi.org/10.1038/s41467-019-12938-4 </a></p><p><strong>OPEN </strong></p><p></p><ul style="display: flex;"><li style="flex:1">T</li><li style="flex:1">u</li></ul><p>r</p><ul style="display: flex;"><li style="flex:1">n</li><li style="flex:1">i</li><li style="flex:1">n</li></ul><p>egg</p><ul style="display: flex;"><li style="flex:1">w</li><li style="flex:1">e</li></ul><p>otr</p><ul style="display: flex;"><li style="flex:1">t</li><li style="flex:1">a</li><li style="flex:1">b</li><li style="flex:1">i</li><li style="flex:1">l</li><li style="flex:1">i</li></ul><p>ituym</p><ul style="display: flex;"><li style="flex:1">o</li><li style="flex:1">f</li></ul><p>m</p><ul style="display: flex;"><li style="flex:1">m</li><li style="flex:1">o</li></ul><p>all</p><ul style="display: flex;"><li style="flex:1">t</li><li style="flex:1">e</li></ul><p>a</p><ul style="display: flex;"><li style="flex:1">n</li><li style="flex:1">l</li></ul><p>oid</p><ul style="display: flex;"><li style="flex:1">t</li><li style="flex:1">h</li></ul><p>e</p><ul style="display: flex;"><li style="flex:1">i</li><li style="flex:1">u</li><li style="flex:1">m</li><li style="flex:1">v</li><li style="flex:1">i</li><li style="flex:1">a</li><li style="flex:1">a</li><li style="flex:1">c</li><li style="flex:1">h</li><li style="flex:1">e</li><li style="flex:1">m</li><li style="flex:1">i</li><li style="flex:1">c</li><li style="flex:1">a</li><li style="flex:1">l</li></ul><p></p><ul style="display: flex;"><li style="flex:1">s</li><li style="flex:1">t</li><li style="flex:1">a</li><li style="flex:1">t</li><li style="flex:1">y</li><li style="flex:1">f</li><li style="flex:1">l</li><li style="flex:1">i</li><li style="flex:1">t</li><li style="flex:1">h</li><li style="flex:1">e</li><li style="flex:1">t</li><li style="flex:1">n</li><li style="flex:1">s</li></ul><p></p><p></p><ul style="display: flex;"><li style="flex:1">1</li><li style="flex:1">1</li><li style="flex:1">1</li><li style="flex:1">,</li><li style="flex:1">2</li><li style="flex:1">1</li><li style="flex:1">,</li><li style="flex:1">2</li><li style="flex:1">1</li><li style="flex:1">,</li><li style="flex:1">2</li><li style="flex:1">1</li><li style="flex:1">1</li><li style="flex:1">,</li><li style="flex:1">2</li></ul><p></p><p></p><ul style="display: flex;"><li style="flex:1">S</li><li style="flex:1">h</li><li style="flex:1">u</li><li style="flex:1">-</li><li style="flex:1">H</li><li style="flex:1">u</li><li style="flex:1">a</li><li style="flex:1">W</li><li style="flex:1">a</li><li style="flex:1">n</li><li style="flex:1">g</li><li style="flex:1">,</li><li style="flex:1">J</li><li style="flex:1">u</li><li style="flex:1">n</li><li style="flex:1">p</li><li style="flex:1">e</li><li style="flex:1">i</li><li style="flex:1">Y</li><li style="flex:1">u</li><li style="flex:1">e</li><li style="flex:1">,</li><li style="flex:1">W</li><li style="flex:1">e</li><li style="flex:1">i</li><li style="flex:1">D</li><li style="flex:1">o</li><li style="flex:1">n</li><li style="flex:1">g</li><li style="flex:1">,</li><li style="flex:1">T</li><li style="flex:1">o</li><li style="flex:1">n</li><li style="flex:1">g</li><li style="flex:1">-</li><li style="flex:1">T</li><li style="flex:1">o</li><li style="flex:1">n</li><li style="flex:1">g</li><li style="flex:1">Z</li><li style="flex:1">u</li><li style="flex:1">o</li><li style="flex:1">,</li><li style="flex:1">J</li><li style="flex:1">i</li><li style="flex:1">n</li><li style="flex:1">-</li><li style="flex:1">Y</li><li style="flex:1">i</li><li style="flex:1">L</li><li style="flex:1">i</li><li style="flex:1">,</li><li style="flex:1">X</li><li style="flex:1">i</li><li style="flex:1">a</li><li style="flex:1">o</li><li style="flex:1">l</li><li style="flex:1">o</li><li style="flex:1">n</li><li style="flex:1">g</li><li style="flex:1">L</li><li style="flex:1">i</li><li style="flex:1">u</li><li style="flex:1">,</li><li style="flex:1">X</li><li style="flex:1">u</li><li style="flex:1">-</li><li style="flex:1">D</li><li style="flex:1">o</li><li style="flex:1">n</li><li style="flex:1">g</li><li style="flex:1">Z</li><li style="flex:1">h</li><li style="flex:1">a</li><li style="flex:1">n</li><li style="flex:1">g</li><li style="flex:1">,</li></ul><p></p><p></p><ul style="display: flex;"><li style="flex:1">1</li><li style="flex:1">,</li><li style="flex:1">2</li><li style="flex:1">1</li><li style="flex:1">,</li><li style="flex:1">2</li><li style="flex:1">1</li><li style="flex:1">,</li><li style="flex:1">2</li><li style="flex:1">1</li><li style="flex:1">,</li><li style="flex:1">2</li></ul><p></p><p></p><ul style="display: flex;"><li style="flex:1">L</li><li style="flex:1">i</li><li style="flex:1">n</li><li style="flex:1">L</li><li style="flex:1">i</li><li style="flex:1">u</li><li style="flex:1">,</li><li style="flex:1">J</li><li style="flex:1">i</li><li style="flex:1">-</li><li style="flex:1">L</li><li style="flex:1">e</li><li style="flex:1">i</li><li style="flex:1">S</li><li style="flex:1">h</li><li style="flex:1">i</li><li style="flex:1">,</li><li style="flex:1">Y</li><li style="flex:1">a</li><li style="flex:1">-</li><li style="flex:1">X</li><li style="flex:1">i</li><li style="flex:1">a</li><li style="flex:1">Y</li><li style="flex:1">i</li><li style="flex:1">n</li><li style="flex:1">&</li><li style="flex:1">Y</li><li style="flex:1">u</li><li style="flex:1">-</li><li style="flex:1">G</li><li style="flex:1">u</li><li style="flex:1">o</li><li style="flex:1">G</li><li style="flex:1">u</li><li style="flex:1">o</li><li style="flex:1">*</li></ul><p></p><p></p><ul style="display: flex;"><li style="flex:1">M</li><li style="flex:1">e</li><li style="flex:1">t</li><li style="flex:1">a</li><li style="flex:1">l</li><li style="flex:1">l</li><li style="flex:1">i</li><li style="flex:1">c</li><li style="flex:1">l</li><li style="flex:1">i</li><li style="flex:1">t</li><li style="flex:1">h</li><li style="flex:1">i</li><li style="flex:1">u</li><li style="flex:1">m</li><li style="flex:1">a</li><li style="flex:1">f</li><li style="flex:1">f</li><li style="flex:1">o</li><li style="flex:1">r</li><li style="flex:1">d</li><li style="flex:1">s</li><li style="flex:1">t</li><li style="flex:1">h</li><li style="flex:1">e</li></ul><p>n</p><ul style="display: flex;"><li style="flex:1">h</li><li style="flex:1">i</li><li style="flex:1">g</li><li style="flex:1">h</li><li style="flex:1">e</li><li style="flex:1">s</li><li style="flex:1">t</li><li style="flex:1">t</li><li style="flex:1">h</li><li style="flex:1">e</li><li style="flex:1">o</li><li style="flex:1">r</li><li style="flex:1">e</li><li style="flex:1">t</li><li style="flex:1">i</li><li style="flex:1">c</li><li style="flex:1">a</li><li style="flex:1">l</li><li style="flex:1">c</li><li style="flex:1">a</li><li style="flex:1">p</li><li style="flex:1">a</li><li style="flex:1">c</li><li style="flex:1">i</li><li style="flex:1">t</li><li style="flex:1">y</li><li style="flex:1">a</li><li style="flex:1">n</li><li style="flex:1">d</li><li style="flex:1">l</li><li style="flex:1">o</li><li style="flex:1">w</li><li style="flex:1">e</li><li style="flex:1">s</li><li style="flex:1">t</li><li style="flex:1">e</li><li style="flex:1">l</li><li style="flex:1">e</li><li style="flex:1">c</li><li style="flex:1">t</li><li style="flex:1">r</li><li style="flex:1">o</li><li style="flex:1">c</li><li style="flex:1">h</li><li style="flex:1">e</li><li style="flex:1">m</li><li style="flex:1">i</li><li style="flex:1">c</li><li style="flex:1">a</li><li style="flex:1">l</li><li style="flex:1">p</li><li style="flex:1">o</li><li style="flex:1">t</li><li style="flex:1">e</li><li style="flex:1">n</li><li style="flex:1">t</li><li style="flex:1">i</li><li style="flex:1">a</li><li style="flex:1">l</li></ul><p></p><ul style="display: flex;"><li style="flex:1">a</li><li style="flex:1">n</li><li style="flex:1">d</li><li style="flex:1">i</li><li style="flex:1">s</li><li style="flex:1">v</li><li style="flex:1">i</li><li style="flex:1">e</li><li style="flex:1">w</li><li style="flex:1">e</li><li style="flex:1">d</li><li style="flex:1">a</li><li style="flex:1">s</li><li style="flex:1">a</li></ul><p>,</p><ul style="display: flex;"><li style="flex:1">l</li><li style="flex:1">e</li><li style="flex:1">a</li><li style="flex:1">d</li><li style="flex:1">i</li><li style="flex:1">g</li><li style="flex:1">c</li><li style="flex:1">o</li><li style="flex:1">n</li><li style="flex:1">t</li><li style="flex:1">e</li><li style="flex:1">n</li><li style="flex:1">d</li><li style="flex:1">e</li><li style="flex:1">r</li><li style="flex:1">a</li><li style="flex:1">s</li><li style="flex:1">a</li><li style="flex:1">n</li><li style="flex:1">a</li><li style="flex:1">n</li><li style="flex:1">o</li><li style="flex:1">d</li><li style="flex:1">e</li><li style="flex:1">f</li><li style="flex:1">o</li><li style="flex:1">r</li><li style="flex:1">h</li><li style="flex:1">i</li><li style="flex:1">g</li><li style="flex:1">h</li><li style="flex:1">-</li><li style="flex:1">e</li><li style="flex:1">n</li><li style="flex:1">e</li><li style="flex:1">r</li><li style="flex:1">g</li><li style="flex:1">y</li><li style="flex:1">-</li><li style="flex:1">d</li><li style="flex:1">e</li><li style="flex:1">n</li><li style="flex:1">s</li><li style="flex:1">i</li><li style="flex:1">t</li><li style="flex:1">y</li><li style="flex:1">r</li><li style="flex:1">e</li><li style="flex:1">c</li><li style="flex:1">h</li><li style="flex:1">a</li><li style="flex:1">r</li><li style="flex:1">g</li><li style="flex:1">e</li></ul><p>c</p><ul style="display: flex;"><li style="flex:1">a</li><li style="flex:1">b</li><li style="flex:1">l</li><li style="flex:1">e</li></ul><p></p><ul style="display: flex;"><li style="flex:1">b</li><li style="flex:1">a</li><li style="flex:1">t</li><li style="flex:1">t</li><li style="flex:1">e</li><li style="flex:1">r</li><li style="flex:1">i</li><li style="flex:1">e</li><li style="flex:1">s</li><li style="flex:1">.</li><li style="flex:1">H</li></ul><p>e</p><ul style="display: flex;"><li style="flex:1">o</li><li style="flex:1">w</li><li style="flex:1">e</li><li style="flex:1">v</li><li style="flex:1">e</li><li style="flex:1">r</li><li style="flex:1">t</li><li style="flex:1">h</li><li style="flex:1">e</li><li style="flex:1">p</li><li style="flex:1">o</li><li style="flex:1">o</li><li style="flex:1">r</li><li style="flex:1">w</li><li style="flex:1">e</li><li style="flex:1">t</li><li style="flex:1">t</li><li style="flex:1">a</li><li style="flex:1">b</li><li style="flex:1">i</li><li style="flex:1">l</li><li style="flex:1">i</li><li style="flex:1">t</li><li style="flex:1">y</li><li style="flex:1">o</li><li style="flex:1">f</li><li style="flex:1">m</li><li style="flex:1">o</li><li style="flex:1">l</li><li style="flex:1">t</li><li style="flex:1">e</li><li style="flex:1">n</li><li style="flex:1">l</li><li style="flex:1">i</li><li style="flex:1">t</li><li style="flex:1">h</li><li style="flex:1">i</li><li style="flex:1">u</li><li style="flex:1">m</li><li style="flex:1">d</li><li style="flex:1">o</li><li style="flex:1">e</li><li style="flex:1">s</li><li style="flex:1">n</li><li style="flex:1">o</li><li style="flex:1">t</li><li style="flex:1">a</li><li style="flex:1">l</li><li style="flex:1">l</li><li style="flex:1">o</li><li style="flex:1">w</li><li style="flex:1">i</li><li style="flex:1">t</li><li style="flex:1">t</li><li style="flex:1">o</li><li style="flex:1">s</li></ul><p>a</p><ul style="display: flex;"><li style="flex:1">p</li><li style="flex:1">r</li><li style="flex:1">e</li><li style="flex:1">a</li><li style="flex:1">d</li><li style="flex:1">a</li><li style="flex:1">r</li><li style="flex:1">o</li><li style="flex:1">s</li><li style="flex:1">s</li></ul><p></p><ul style="display: flex;"><li style="flex:1">t</li><li style="flex:1">h</li><li style="flex:1">e</li><li style="flex:1">s</li></ul><p>eu</p><ul style="display: flex;"><li style="flex:1">u</li><li style="flex:1">r</li><li style="flex:1">f</li><li style="flex:1">a</li><li style="flex:1">c</li><li style="flex:1">o</li><li style="flex:1">f</li><li style="flex:1">l</li><li style="flex:1">i</li><li style="flex:1">t</li><li style="flex:1">h</li><li style="flex:1">i</li><li style="flex:1">o</li><li style="flex:1">p</li><li style="flex:1">h</li><li style="flex:1">o</li><li style="flex:1">b</li><li style="flex:1">i</li><li style="flex:1">c</li><li style="flex:1">s</li></ul><p>a</p><ul style="display: flex;"><li style="flex:1">u</li><li style="flex:1">b</li><li style="flex:1">s</li><li style="flex:1">t</li><li style="flex:1">r</li><li style="flex:1">a</li><li style="flex:1">t</li><li style="flex:1">e</li><li style="flex:1">s</li><li style="flex:1">,</li><li style="flex:1">h</li><li style="flex:1">i</li><li style="flex:1">n</li><li style="flex:1">d</li></ul><p>e</p><ul style="display: flex;"><li style="flex:1">e</li><li style="flex:1">r</li><li style="flex:1">i</li><li style="flex:1">n</li><li style="flex:1">g</li><li style="flex:1">t</li><li style="flex:1">h</li><li style="flex:1">e</li><li style="flex:1">p</li><li style="flex:1">r</li><li style="flex:1">o</li><li style="flex:1">d</li><li style="flex:1">u</li><li style="flex:1">c</li><li style="flex:1">t</li><li style="flex:1">i</li><li style="flex:1">o</li><li style="flex:1">n</li><li style="flex:1">a</li><li style="flex:1">n</li><li style="flex:1">d</li><li style="flex:1">a</li><li style="flex:1">p</li><li style="flex:1">p</li><li style="flex:1">l</li><li style="flex:1">i</li><li style="flex:1">c</li><li style="flex:1">a</li><li style="flex:1">t</li><li style="flex:1">i</li><li style="flex:1">o</li><li style="flex:1">n</li><li style="flex:1">o</li><li style="flex:1">f</li><li style="flex:1">t</li><li style="flex:1">h</li><li style="flex:1">i</li><li style="flex:1">s</li><li style="flex:1">a</li><li style="flex:1">n</li><li style="flex:1">o</li><li style="flex:1">d</li><li style="flex:1">e</li><li style="flex:1">.</li></ul><p></p><ul style="display: flex;"><li style="flex:1">H</li><li style="flex:1">e</li><li style="flex:1">r</li><li style="flex:1">w</li><li style="flex:1">e</li><li style="flex:1">r</li><li style="flex:1">e</li><li style="flex:1">p</li><li style="flex:1">o</li><li style="flex:1">r</li><li style="flex:1">t</li><li style="flex:1">a</li><li style="flex:1">g</li><li style="flex:1">e</li><li style="flex:1">n</li><li style="flex:1">e</li><li style="flex:1">r</li><li style="flex:1">a</li><li style="flex:1">l</li><li style="flex:1">c</li><li style="flex:1">h</li><li style="flex:1">e</li><li style="flex:1">m</li><li style="flex:1">i</li><li style="flex:1">c</li><li style="flex:1">a</li><li style="flex:1">l</li><li style="flex:1">s</li><li style="flex:1">t</li><li style="flex:1">r</li><li style="flex:1">a</li><li style="flex:1">t</li><li style="flex:1">g</li><li style="flex:1">y</li><li style="flex:1">t</li><li style="flex:1">o</li><li style="flex:1">o</li><li style="flex:1">v</li><li style="flex:1">e</li><li style="flex:1">r</li><li style="flex:1">c</li><li style="flex:1">o</li><li style="flex:1">m</li><li style="flex:1">e</li><li style="flex:1">t</li><li style="flex:1">h</li><li style="flex:1">i</li><li style="flex:1">s</li><li style="flex:1">d</li><li style="flex:1">i</li><li style="flex:1">l</li><li style="flex:1">e</li><li style="flex:1">m</li><li style="flex:1">m</li><li style="flex:1">a</li><li style="flex:1">b</li><li style="flex:1">y</li><li style="flex:1">r</li><li style="flex:1">e</li><li style="flex:1">c</li><li style="flex:1">t</li><li style="flex:1">i</li><li style="flex:1">n</li><li style="flex:1">g</li><li style="flex:1">m</li><li style="flex:1">o</li><li style="flex:1">l</li><li style="flex:1">t</li><li style="flex:1">e</li><li style="flex:1">n</li></ul><p></p><ul style="display: flex;"><li style="flex:1">l</li><li style="flex:1">i</li><li style="flex:1">t</li><li style="flex:1">h</li><li style="flex:1">i</li><li style="flex:1">m</li><li style="flex:1">w</li><li style="flex:1">i</li><li style="flex:1">t</li><li style="flex:1">h</li><li style="flex:1">f</li><li style="flex:1">u</li><li style="flex:1">n</li><li style="flex:1">c</li><li style="flex:1">t</li><li style="flex:1">i</li><li style="flex:1">o</li><li style="flex:1">n</li><li style="flex:1">a</li><li style="flex:1">l</li><li style="flex:1">o</li><li style="flex:1">r</li><li style="flex:1">g</li><li style="flex:1">n</li><li style="flex:1">i</li><li style="flex:1">c</li><li style="flex:1">c</li><li style="flex:1">o</li><li style="flex:1">a</li><li style="flex:1">t</li><li style="flex:1">i</li><li style="flex:1">n</li><li style="flex:1">g</li><li style="flex:1">s</li><li style="flex:1">o</li><li style="flex:1">r</li><li style="flex:1">e</li><li style="flex:1">l</li><li style="flex:1">e</li><li style="flex:1">m</li><li style="flex:1">e</li><li style="flex:1">n</li><li style="flex:1">t</li><li style="flex:1">a</li><li style="flex:1">l</li><li style="flex:1">a</li><li style="flex:1">d</li><li style="flex:1">d</li><li style="flex:1">i</li><li style="flex:1">t</li><li style="flex:1">i</li><li style="flex:1">v</li><li style="flex:1">e</li><li style="flex:1">s</li><li style="flex:1">.</li><li style="flex:1">T</li><li style="flex:1">h</li><li style="flex:1">e</li><li style="flex:1">G</li><li style="flex:1">i</li><li style="flex:1">b</li><li style="flex:1">b</li><li style="flex:1">s</li><li style="flex:1">f</li><li style="flex:1">o</li><li style="flex:1">r</li><li style="flex:1">m</li><li style="flex:1">a</li><li style="flex:1">t</li><li style="flex:1">i</li><li style="flex:1">o</li><li style="flex:1">n</li><li style="flex:1">e</li><li style="flex:1">n</li><li style="flex:1">e</li><li style="flex:1">r</li><li style="flex:1">g</li><li style="flex:1">y</li></ul><p></p><ul style="display: flex;"><li style="flex:1">g</li><li style="flex:1">a</li><li style="flex:1">n</li><li style="flex:1">d</li></ul><p>h</p><ul style="display: flex;"><li style="flex:1">n</li><li style="flex:1">e</li><li style="flex:1">w</li><li style="flex:1">l</li><li style="flex:1">y</li><li style="flex:1">f</li><li style="flex:1">o</li><li style="flex:1">r</li><li style="flex:1">m</li><li style="flex:1">e</li><li style="flex:1">d</li><li style="flex:1">c</li><li style="flex:1">h</li><li style="flex:1">e</li><li style="flex:1">m</li><li style="flex:1">i</li><li style="flex:1">c</li><li style="flex:1">a</li><li style="flex:1">l</li><li style="flex:1">b</li><li style="flex:1">o</li></ul><p>h</p><ul style="display: flex;"><li style="flex:1">n</li><li style="flex:1">d</li><li style="flex:1">s</li></ul><p>v</p><ul style="display: flex;"><li style="flex:1">a</li><li style="flex:1">r</li><li style="flex:1">e</li><li style="flex:1">f</li><li style="flex:1">o</li><li style="flex:1">u</li><li style="flex:1">n</li><li style="flex:1">d</li><li style="flex:1">t</li><li style="flex:1">o</li><li style="flex:1">b</li></ul><p>a</p><ul style="display: flex;"><li style="flex:1">e</li><li style="flex:1">t</li><li style="flex:1">h</li><li style="flex:1">e</li><li style="flex:1">g</li><li style="flex:1">o</li><li style="flex:1">v</li><li style="flex:1">e</li><li style="flex:1">r</li><li style="flex:1">n</li><li style="flex:1">i</li><li style="flex:1">n</li><li style="flex:1">g</li><li style="flex:1">f</li><li style="flex:1">a</li><li style="flex:1">c</li><li style="flex:1">t</li><li style="flex:1">o</li><li style="flex:1">r</li><li style="flex:1">f</li><li style="flex:1">o</li><li style="flex:1">r</li><li style="flex:1">t</li><li style="flex:1">h</li><li style="flex:1">e</li><li style="flex:1">w</li><li style="flex:1">e</li><li style="flex:1">t</li><li style="flex:1">t</li><li style="flex:1">i</li><li style="flex:1">n</li></ul><p></p><ul style="display: flex;"><li style="flex:1">b</li><li style="flex:1">e</li></ul><p>aak</p><ul style="display: flex;"><li style="flex:1">v</li><li style="flex:1">i</li><li style="flex:1">o</li><li style="flex:1">r</li><li style="flex:1">.</li><li style="flex:1">A</li><li style="flex:1">s</li><li style="flex:1">a</li><li style="flex:1">r</li><li style="flex:1">e</li><li style="flex:1">s</li><li style="flex:1">u</li><li style="flex:1">l</li><li style="flex:1">t</li><li style="flex:1">o</li><li style="flex:1">f</li><li style="flex:1">t</li><li style="flex:1">h</li><li style="flex:1">e</li><li style="flex:1">i</li><li style="flex:1">m</li><li style="flex:1">p</li><li style="flex:1">r</li><li style="flex:1">o</li><li style="flex:1">e</li><li style="flex:1">d</li><li style="flex:1">w</li><li style="flex:1">e</li><li style="flex:1">t</li><li style="flex:1">t</li><li style="flex:1">a</li><li style="flex:1">b</li><li style="flex:1">i</li><li style="flex:1">l</li><li style="flex:1">i</li><li style="flex:1">t</li><li style="flex:1">y</li><li style="flex:1">,</li><li style="flex:1">s</li><li style="flex:1">e</li><li style="flex:1">r</li><li style="flex:1">i</li><li style="flex:1">e</li><li style="flex:1">s</li><li style="flex:1">o</li><li style="flex:1">f</li><li style="flex:1">u</li><li style="flex:1">l</li><li style="flex:1">t</li><li style="flex:1">r</li><li style="flex:1">a</li><li style="flex:1">t</li><li style="flex:1">h</li><li style="flex:1">i</li><li style="flex:1">n</li><li style="flex:1">l</li><li style="flex:1">i</li><li style="flex:1">t</li><li style="flex:1">h</li><li style="flex:1">i</li><li style="flex:1">u</li><li style="flex:1">m</li><li style="flex:1">o</li><li style="flex:1">f</li><li style="flex:1">1</li><li style="flex:1">0</li></ul><p></p><p>–</p><p></p><ul style="display: flex;"><li style="flex:1">2</li><li style="flex:1">0</li></ul><p></p><p>μ</p><p>m</p><ul style="display: flex;"><li style="flex:1">t</li><li style="flex:1">h</li><li style="flex:1">i</li><li style="flex:1">c</li><li style="flex:1">i</li><li style="flex:1">s</li><li style="flex:1">o</li><li style="flex:1">b</li><li style="flex:1">t</li><li style="flex:1">a</li><li style="flex:1">i</li><li style="flex:1">n</li><li style="flex:1">e</li><li style="flex:1">d</li><li style="flex:1">t</li><li style="flex:1">o</li><li style="flex:1">g</li><li style="flex:1">e</li><li style="flex:1">t</li><li style="flex:1">h</li><li style="flex:1">e</li><li style="flex:1">r</li><li style="flex:1">w</li><li style="flex:1">i</li><li style="flex:1">t</li><li style="flex:1">i</li><li style="flex:1">m</li><li style="flex:1">p</li><li style="flex:1">r</li><li style="flex:1">e</li><li style="flex:1">s</li><li style="flex:1">s</li><li style="flex:1">i</li><li style="flex:1">v</li><li style="flex:1">e</li><li style="flex:1">e</li><li style="flex:1">l</li><li style="flex:1">e</li><li style="flex:1">c</li><li style="flex:1">t</li><li style="flex:1">r</li><li style="flex:1">o</li><li style="flex:1">c</li><li style="flex:1">h</li><li style="flex:1">e</li><li style="flex:1">m</li><li style="flex:1">i</li><li style="flex:1">c</li><li style="flex:1">a</li><li style="flex:1">l</li><li style="flex:1">p</li><li style="flex:1">e</li><li style="flex:1">r</li><li style="flex:1">f</li><li style="flex:1">o</li><li style="flex:1">r</li><li style="flex:1">m</li><li style="flex:1">a</li><li style="flex:1">n</li><li style="flex:1">c</li><li style="flex:1">e</li><li style="flex:1">i</li><li style="flex:1">n</li><li style="flex:1">l</li><li style="flex:1">i</li><li style="flex:1">t</li><li style="flex:1">h</li><li style="flex:1">i</li><li style="flex:1">u</li><li style="flex:1">m</li><li style="flex:1">m</li><li style="flex:1">e</li><li style="flex:1">t</li><li style="flex:1">a</li><li style="flex:1">l</li></ul><p></p><ul style="display: flex;"><li style="flex:1">b</li><li style="flex:1">t</li><li style="flex:1">t</li><li style="flex:1">e</li><li style="flex:1">r</li><li style="flex:1">i</li><li style="flex:1">e</li><li style="flex:1">s</li><li style="flex:1">.</li><li style="flex:1">T</li><li style="flex:1">h</li><li style="flex:1">e</li><li style="flex:1">s</li><li style="flex:1">e</li></ul><p></p>
Details
-
File Typepdf
-
Upload Time-
-
Content LanguagesEnglish
-
Upload UserAnonymous/Not logged-in
-
File Pages8 Page
-
File Size-