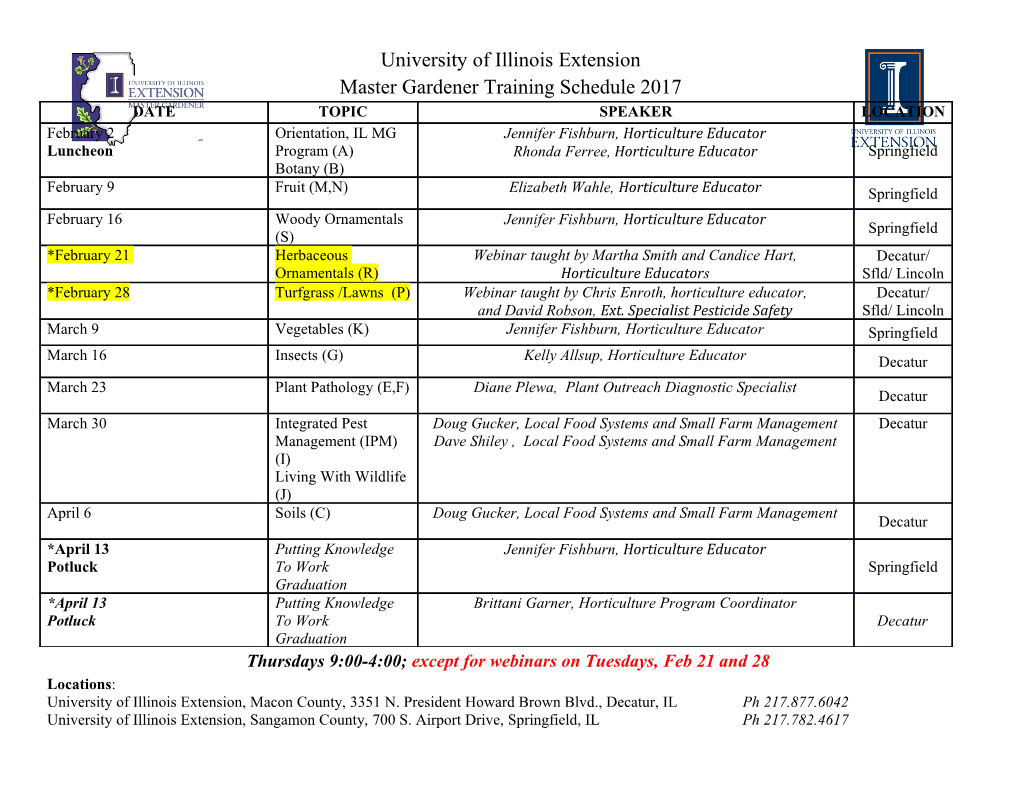
I11111 111111ll111 Ill11 Ill11US006406611B3 IIIII 11111 Ill11 IIIII IIIII IIIII 11ll11111111ll1111 (12) United States Patent (io) Patent No.: US 6,406,611 B1 Engelhaupt et al. (45) Date of Patent: Jun. 18,2002 (54) NICKEL COBALT PHOSPHOROUS LOW 6,099,624 A * 812000 Martyak .................... 10611.27 STRESS ELECTROPLATING FOREIGN PATENT DOCUMENTS (75) Inventors: Dare11 E. Engelhaupt, Madison; Brian EP 0 502 475 A2 911992 D. Ramsey, Huntsville, both of AL OTHER PUBLICATIONS (US) Electroformed Bulk Nickel-Phosphorous Metallic Glass, A (73) Assignees: University of Alabama in Huntsville, Mayer et al., Plating and Surface Finishing, pp. 76-78, No. Huntsville, AL (US); The United States 1985. of America as represented by the Evaluation of Electroplated Nickel Phosphorous With High Marshall Space Flight Center, Phosphorous Content, Hans van Oosterhout; AMP Journal Washington, DC (US) of Technology, vol. 2, Nov. 1992, pp. 63-69. ( * ) Notice: Subject to any disclaimer, the term of this Structure & Properties of Electroless Ni-P-B,C Composite Coatings, J-P Ge et al., Plating & Surface Finishing, Oct. patent is extended or adjusted under 35 1998, pp. 69, 70, and 73. U.S.C. 154(b) by 0 days. High-Temperature Highstrength Nickel Base Alloys, NiDI (Nickel Development Institute), 1995 Supplement No. 393, (21) Appl. No.: 09/456,862 No Month Available. (22) Filed: Dec. 8, 1999 Electrodeposition of Ni-Cr-P Alloys In the Presence of Additives, R., Bindish et al., Plating and Surface Finishing, (51) Int. C1.7 .................................................. C25D 3/56 pp. 68-73, Apr. 1992. (52) U.S. C1. ....................... 205/259; 2051255; 2051236; Electrodeposition of Alloys Containing Phosphorus and 2051258; 10611.27 Nickel or Cobalt, pp. 457483, No Date Available. (58) Field of Search ......................... 10611.27; 2051236, 2051255, 258, 271-280, 259 * cited by examiner Primary Examinerqobert Dawson (56) References Cited Assistant Examineraichael J Feely U.S. PATENT DOCUMENTS (74) Attorney, Agent, or Firmaston & Bird LLP 2,644,787 A 711953 Bonn et al. (57) ABSTRACT 3,637,471 A * 111972 Faulkner ...................... 204143 4,101,389 A 711978 Uedaira An electrolytic plating process is provided for electrodepos- 4,529,668 A 711985 Croopnick et al. iting a nickel or nickel cobalt alloy which contains at least 4,619,872 A 1011986 Goor et al. about 2% to 25% by atomic volume of phosphorous. The 4,647,365 A 311987 Irlesberger et al. process solutions contains nickel and optionally cobalt 4,648,944 A 311987 George et al. sulfate, hypophosphorous acid or a salt thereof, boric acid or 4,673,468 A 611987 Myers et al. a salt thereof, a monodentate organic acid or a salt thereof, 4,767,509 A 811988 Gamblin et al. 4,770,751 A 911988 Kawagishi et al. and a multidentate organic acid or a salt thereof. The pH of 4,786,376 A 1111988 Vaaler the plating bath is from about 3.0 to about 4.5. An electro- 4,808,967 A 211989 Rice et al. plating process is also provided which includes electroplat- 4,888,574 A 1211989 Rice et al. ing from the bath a nickel or nickel cobalt phosphorous 4,892,628 A * 111990 Guilinger ................... 204144.7 alloy. This process can achieve a deposit with high 4,935,310 A 611990 Nakatsugawa microyield of at least about 84 kgimm' (120 ksi) and a 4,986,130 A 111991 Engelhaupt et al. density lower than pure nickel of about 8.0 gmicc. This 5,032,464 A 711991 Lichtenberger process can be used to plate a deposit of essentially zero 5,302,464 A 411994 Nomura stress at plating temperatures from ambient to 70" C. 5,389,226 A 211995 Scruggs et al. 5,779,873 A * 711998 Law et al. .................. 2051271 5,901,432 A 511999 Armstrong et al. 36 Claims, 3 Drawing Sheets US. Patent Jun. 18,2002 Sheet 1 of 3 US 6,406,611 B1 0 N x 2 L a, .--I.- .-I E 3 0 I E 6 z m 0 US. Patent Jun. 18,2002 Sheet 2 of 3 US 6,406,611 B1 \cn E d t \cn E h! T- .cn E -? c-4 US. Patent Jun. 18,2002 Sheet 3 of 3 US 6,406,611 B1 m0 hl 0 0 hl n 0 0 2 2 z -od Q) Y v) v) .-0 M z 2 L tj 0 -rlt;l rc Frc tn 0 tn 0 2 .r 3i 0 In 0 0 0 0 0 0 0 0 0 0 0 0 0 0 m 0 m m uz hl hl r s US 6,406,611 B3 1 2 NICKEL COBALT PHOSPHOROUS LOW Despite the efforts in the art, the electrodeposition of STRESS ELECTROPLATING nickel phosphorous alloys have generally found limited industrial applications due to the various drawbacks in the GOVERNMENT LICENSE RIGHTS heretofore known electroplating processes. For example, The United States Government has a paid-up license in S plating is generally done at very high current densities, and this invention and the right in limited circumstances to the plating efficiency is very low. The processes normally require the patent owner to license others on reasonable require plating at a pH of less than 2.0, making the bath terms as provided for by the terms of Contract Number solution very corrosive to base metals. As a result, expensive NCC8-65 awarded by NASA-Marshall Space Flight Center. precious metal anodes such as platinum and rhodium anodes 10 have to be used. The processes typically require plating at FIELD OF THE INVENTION high temperatures of above 75" C. to increase the cathode This invention generally relates to electroplating of metal current efficiency and to control the internal stress in the alloys, and in particular to processes for electrodeposition of deposited alloy. With the high temperature, low plating nickel and nickel cobalt phosphorous alloys. efficiency, corrosive solution and constant chemical addi- BACKGROUND OF THE INVENTION 1s tions required, there has been little incentive to use the prior art electrolytic processes. Accordingly, there remains need The deposition of nickel phosphorous alloys has generally for developing improved processes for electroplating nickel been known in the art. The deposited nickel phosphorous phosphorous or nickel cobalt phosphorous alloys. alloys can be useful as corrosion and wear resistance coat- SUMMARY OF THE INVENTION ings on many different substrates. In addition, they can also 20 be used in decorative coatings and in the fabrication of This invention provides electroplating bath formulations certain optical components. and processes for electrodepositing from the baths nickel Nickel phosphorous alloys can be deposited by electroless phosphorous alloys or nickel cobalt phosphorous alloys that or electrolytic processes. However, the electroless processes contain at least about 2% and up to 25% by atomic volume known in the art are generally limited to the deposition of 2s of phosphorous. The preferred electroplating bath for elec- rather thin nickel phosphorous coatings. This in part is due troplating nickel phosphorous alloys has a composition to the low plating rate, continuous chemical feed, frequent including nickel sulfate, hypophosphorous acid or a salt need to remove solution from the tank for maintenance, and thereof, boric acid or a salt thereof, a monodentate organic high cost associated with these processes. The internal stress acid or a salt thereof, and a multidentate organic acid or a in the electroless deposited alloys cannot be precisely con- 30 salt thereof. A surfactant such as Triton X-100 or sodium trolled in real-time during the plating process and the laurel (dodecal) sulfate is optionally included. For electro- mechanical properties of the alloys are less than optimum plating nickel cobalt phosphorous alloys, the bath contains, for many operations. For example, electroless processes in addition, a cobalt source such as cobalt sulfate. The generally are not suitable for preparing thick deposits or electroplating baths normally have a pH of from about 3.0 freestanding forms. In addition, the electroless processes 3s to 4.5. typically require a hazardously high plating temperature at The alloys of the present invention can be electrodepos- or above 85" C. and are associated with the evaporation of ited from the bath onto a substrate at a current density of less the plating bath solution forming potentially hazardous than about 35 mA/cm2 and a temperature of from about 25" vapors. C. to about 70" C., preferably less than about 50" C. Anodes There has been significant effort in the art in developing 40 such as platinum or other precious metal anodes can be used and improving electrolytic nickel phosphorous plating pro- in the electroplating. Preferably, one or more soluble anodes cesses. For example, U.S. Pat. Nos. 4,673,468 and 4,767,509 containing nickel and/or cobalt metal or alloys thereof can disclose that "sulfate" baths for nickel phosphorous electro- be used in electroplating using the electroplating bath of this plating have relatively poor cathode efficiency and, poor invention. bath conductivity and that unwanted precipitates are easy to 4s In accordance with the electroplating process of this form in the bath. The patents disclose that improved alloy invention, the internal stress in the electrodeposited alloys quality can be obtained by increasing the anode current can be conveniently controlled in real time to zero stress or density to at least 200 amperes per square foot. The patents near zero stress. When electroplating from a specific bath propose an all-chloride bath prepared from NiC1, and composition of this invention at a given temperature and a H,PO,, H,PO,, NiCO,, Ni(H,PO,), and/or HC1. The plat- so predefined pH, the internal stress in an electrodeposited ing is conducted at a cathode current density of at least 200 alloy varies with the current density in the electroplating amperes per square foot, at a temperature of 78" C.
Details
-
File Typepdf
-
Upload Time-
-
Content LanguagesEnglish
-
Upload UserAnonymous/Not logged-in
-
File Pages13 Page
-
File Size-