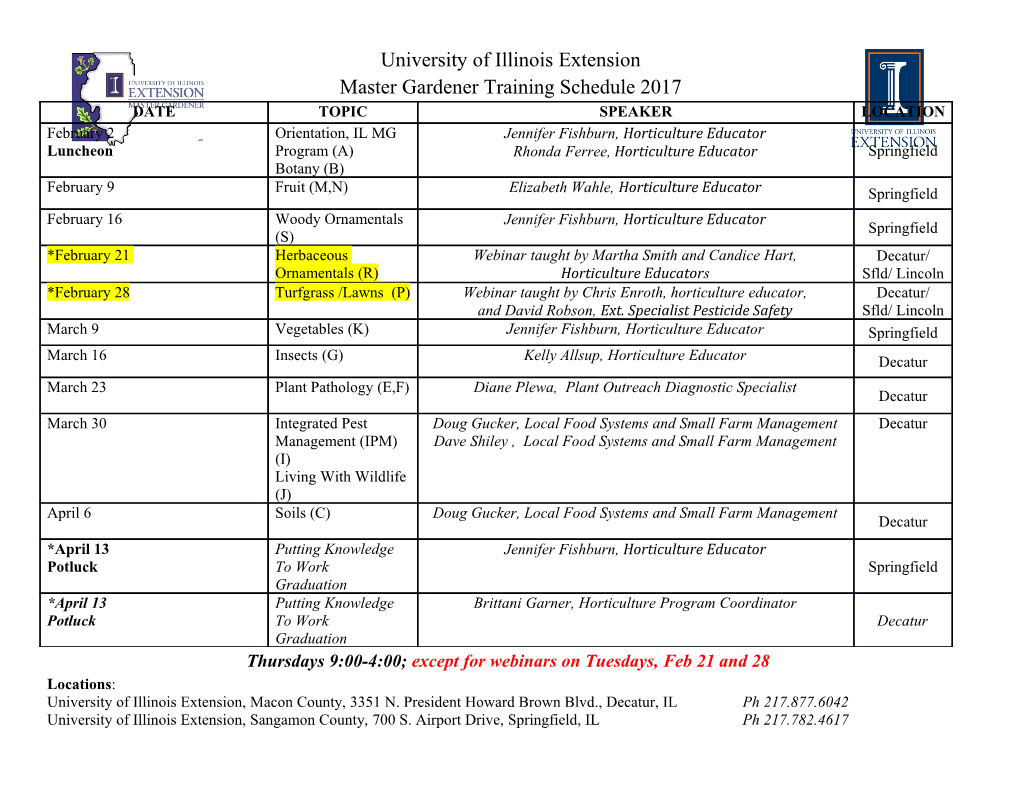
Chapter 3 Concrete Repair & Restoration 197 Efficacy of MCI in Existing Concrete Structures (repair and rest) Corrosion inhibitors can also provide protection to existing concrete structures through topical coating or repair mortar application. Products in this category generally come in the forms of A) pure inhibitor solution to be applied on concrete surface – the inhibitors will then be transported to embedded steel rebar via capillary infiltration and vapor phase diffusion; B) Hydrophobic sealer with MCI component – this approach protects by reducing egression of corrosive species while simultaneously forming barrier layer on rebar surface though the action of MCI molecules; and C) MCI containing repair mortar that supplies the rebar with the migrating corrosion inhibitors. MCI-2020, MCI-2020M, MCI-2020VO is a family of water-based impregnating migrating corrosion inhibitors. In testing protocol according to G109 that lasted 1500 days and over 200 cycles of 3.5%NaCl ponding/drying, Figure 10, it was found that the inhibitor MCI-2020 had increased polarization resistance (Rp) (60-80 kohms-cm2 with increasing trends) in the MCI coated concrete than un-coated concrete, for both low density and high density concretes. The untreated not only had lower Rp values, but also decreasing trends, Figure 11. Examination of the embedded steel rebar after corrosion tests showed no corrosion attack for the MCI treated concrete samples, while un-treated concrete showed corrosion, Figure 12. X-ray photoelectron spectroscopy (XPS) and depth profiling confirmed that the inhibitor had reached the rebar surface in less than 150 days. Depth profiling showed an amine-rich compound on the rebar surface that corresponded with the increase in Rp and improved corrosion protection for the MCI treated steel rebar even in the presence of chloride ions, Table 1. Based on measured corrosion rate the life expectancy of a concrete reinforced structure can be improved by more than 40 years. Figure 10 – Modified ASTM G109 Test Set-Up (continuous submersion) a) b) a) Samples prepared per ASTM G109 b) Samples modified for continuous immersion 198 Figure 11 – Comparison in Polarization Resistance (Rp) in Low & High Density Concretes – Treated (MCI 2020 & MCI 2020 M) vs. Untreated 199 Figure 12 – Rebar at the end of 1500 Days of Testing a) b) a) Un-treated concrete, rebar showed localized corrosion attacks. b) MCI-treated concrete, rebar did not show any corrosion attacks. Table 2: XPS analysis and spectrum of the rebar surface, untreated and MCI 2020M treated concrete after 1500 days in 3.5% NaCl Atomic Conc (%) Mass Conc (%) Atomic Conc (%) Mass Conc (%) Peak Untreated Untreated MCI MCI Fe 2p 0.87 3.32 0.08 0.3 O 1s 30.19 33.06 31.4 35.91 C 1s 62.48 51.37 59.43 48.12 Ca 2p 0.15 0.42 1.08 3.01 Si 2p 4.72 9.08 1.26 4.14 Cl 2p 0.84 2.04 1.11 2.81 N 1s 0.74 0.71 5.64 5.71 Figure 13 - UV spectroscopy analysis of a concrete section 3” below a MCI-2020 treated surface 5 weeks after the treatment demonstrated the inhibitor presence at that depth 200 Adhesion testing of several traffic coatings applied over surfaces treated with MCI-2020 showed that MCI treatment had no adverse effect on the adhesion of the traffic coatings that followed . A more severe test, the Cracked Beam Test modified from ASTM G109, on MCI-2020 showed that the inhibitor delayed onset of corrosion. The control started to corrode at average of 3.75 cycles while the MCI-2020 treated specimens at average of 9.25 cycles, an improvement of 150%, Table 2. After corrosion initiation, the treated specimens showed reduced amount of damage. For MCI-2020 treated concrete, the average corrosion was 28% of the control and the average corrosion current was 53% of the control, respectively, after 20 monthly cycles, Table 3. Table 3: Time-To-Corrosion of Cracked Beams Concrete Monthly Cycles before Initiation of Corrosion Mix Beam Ave 1 2 3 4 Control 0 0 5 10 3.75 MCI2020 11 8 12 6* 9.25 * Beam had bottom bar corrosion 201 Table 4: ElectroChemical Measurements in Cracked Beams Concrete Number of Monthly Test Cycles Mix Ave corr current, Resistance, Half-cell potential, Intergral current, μA ohms negative Volts μA-days 1 10 20 1 10 20 1 10 20 1 10 20 Control -37 - - 67 131 135 0.155 0.349 0.379 131 15837 75839 145 228 MCI2020 5 -18 -91 70 130 158 0.103 0.192 0.346 -16 583 21329 Another MCI product in protecting existing structures is MCI-2018, a sealer with MCI component. Due to the MCI molecules, this sealer not only repels intrusion of corrosive species from the surface, but introduces migrating inhibitors to the concrete and the embedded rebar. The Cracked Beam Test shows that the resistance in the treated beam is 55% higher than untreated at 7th cycle, Figure 14. Figure 14: Resistance in Cracked Beams (MCI-2018 treated and untreated) 202 Specification of MCI Surface Treatments by Product MCI surface treatments are designed for use on existing structures. They are designed to be applied to clean, dry surfaces – free of dirt, grease, oils, laitance, presence of other sealers or coatings, etc. The most concentrated application of MCI in a surface treatment is in a water-based solution (MCI 2020, MCI 2020 V/O, MCI 2020 M, MCI 2020 MSC, MCI 2020 M V/O). These products contain corrosion inhibitor only and are best for use direct to concrete or mortar. They can be followed by a top coat if desired. The MCI technology has also been combined with water repellants to create two-in-one surface treatments – with 100% organosilane (MCI 2018, MCI 2018 V/O), 40% silane (MCI 2019, MCI 2019 W), silane/siloxane blends (MCI 2022, MCI 2022 V/O) and silicates (MCI 2021). UV Tracers or fugitive dyes can be added to MCI surface treatments to confirm application upon request. Repair and Specialty MCI admixtures have been combined into repair mortars and grouts (MCI 2023, MCI 2039 SC, MCI 2701, and MCI 2702). They have also been incorporated into specialty products such as a gel for injection to embedded reinforcing steel (MCI 2020 Gel), protection for post tensioned cables (MCI 309, MCI PTC Emitters), concrete cleaners (MCI 2060, MCI 2061), concrete removers (MCI Super Remover) and concrete curing compounds (MCI CorteCure). 203 Presented at the International Conference for Concrete Under Sever Conditions (ConSec), 2001, Vancouver, Canada SURFACE APPLIED MIGRATING INHIBITORS FOR PROTECTION OF CONCRETE STRUCTURES Prof. Dubravka Bjegovic University of Zagreb, Zagreb, Croatia Prof. Behzad Bavarian California State University, Northridge, USA Masaru Nagayama General Building Research Corporation of Japan, Osaka, Japan Abstract This paper discusses the protection of reinforced concrete using surface applied Migrating Corrosion Inhibitors (MCI). Concrete surface could be treated with migration corrosion inhibitor during maintenance life as the prevention measure to assure the extension of the structure service life. Migrating Corrosion Inhibitor could be also added in repair systems as an admixture. The experimental results are given for both applications from different independent laboratories in different countries around the globe. 1.Introduction Corrosion of reinforcement has been recognized as one of the most prevalent durability factors, which affects the largest group of reinforced concrete structures as bridges, parking garages etc. Corrosion could be brought under such control by application of the protective measure. One of the possibilities is the topical application of the migrating corrosion inhibitor. Migrating corrosion inhibitors (MCI’s) are a mixed (anodic /cathodic) amino-carboxylate based inhibitor (1). The inhibition of cathodic 204 process is achieved by incorporation of one or more oxidizing anions in an organic (amine) molecule of MCI. Inhibitor molecules are hydrolyzed when adsorbed on the metal surface. The nitrogen of the amine group is capable of entering into a coordinate bond with metals thus enhancing the adsorbtion process. Adsorption of cations increases the overpotential of metal ionization and slow down the corrosion. The mixed monomolecular film serves as a buffer to hold the pH at the interface in the optimum range for corrosion resistance. The inhibitor adsorption isn’t a momentary process and requires much time for completion resulting in a chemisorbed layer on the metal surface. The migrating corrosion inhibitors can be added to concrete as admixtures during concrete mixing, or topically applied to the concrete surface, or placed into cracks in concrete for injection application or inserted in the form of emitting capsules for easy and renewable corrosion protection of existing structures (2). In spite of many published studies a lot of conflicting opinions exist concerning the effectiveness of these products for corrosion protection. In this paper the effectiveness of the migrating corrosion inhibitor applied on the concrete surface is tested and the results of the investigation from different independent laboratories in different countries around the globe are presented. 2. Experimental Procedures 2.1. Laboratory 1 (University of Zagreb, Croatia) The concrete with w/c factor 0.7 was used for the preparation of the test slabs as concrete substrate (2). The reinforced concrete specimens were made in accordance with ASTM G 109. The specimens were demolded after 24 hours and kept in a wet chamber for 28 days (RH = 95%, T = 20+2oC). After 28 days the upper surface of the specimens was wire brushed and the topical application by brush was made according to supplier’s specification of 450 g/m2. After the topical application of the migrating corrosion inhibitor the specimens were cured for two weeks at 20°C and 65% RH. 205 0,000,501,001,502,002,503,003,504,004,505,00147101316192225283134374043 Fig 1.
Details
-
File Typepdf
-
Upload Time-
-
Content LanguagesEnglish
-
Upload UserAnonymous/Not logged-in
-
File Pages258 Page
-
File Size-