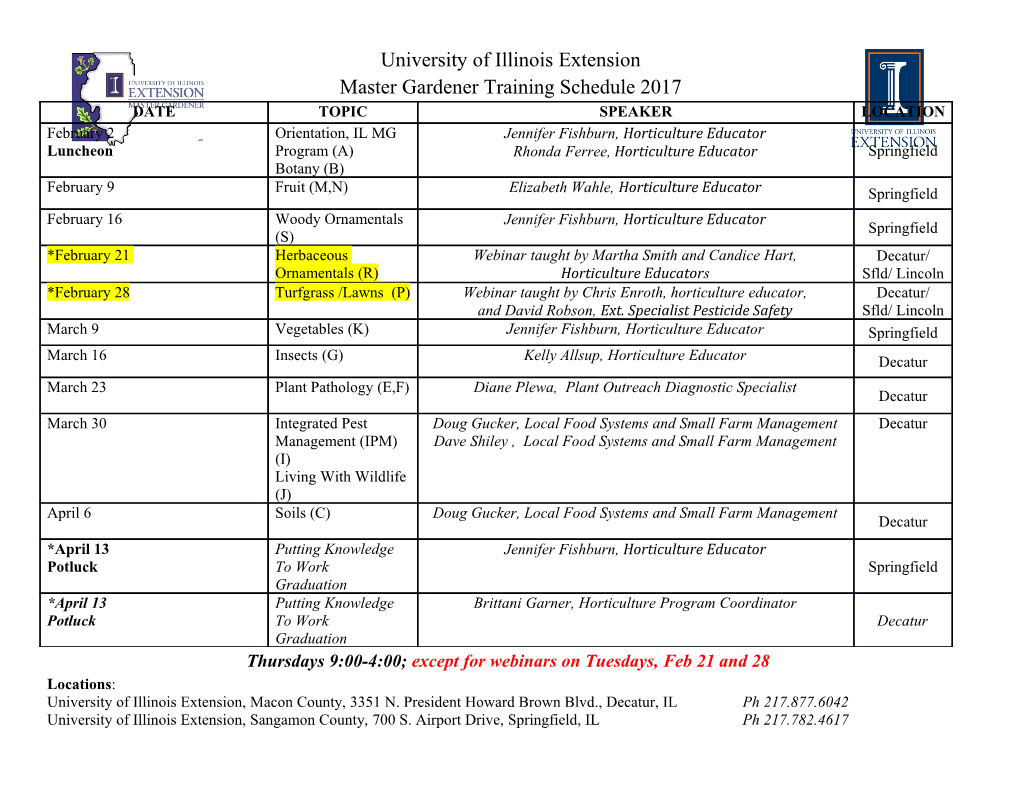
Chemical pulping The most common chemical pulping process used in the USA is the “Kraft” process (also called Sulfate process). Kraft belongs to the “alkaline pulping processes”. Alkaline pulping only means pulping pH has to be alkaline: can be Soda process (NaOH) or Kraft process (NaOH+ Na2S) or any other process with high pH. Today the Kraft process is used for around 90 % of all chemical pulp production in the US. The other main chemical process is sulfite pulping, using H2SO3 (original design used acid conditions, but today also used under neutral or alkaline conditions).Main purpose of chemical pulping it to remove enough lignin so that the fibers can be separated from each other. The Kraft Process The Kraft process was developed 1879 by Dahl. Dahl added the cheaper sodium sulfate (Na2SO4) as make-up chemical to a recovery system for the soda process (he tried to replace sodium carbonate). In this pulping process the aqueous liquor is collected and incinerated after the pulping process ( to recover chemicals and energy). During the incineration in the recovery system sulfate is reduced to sulfide. So the name “sulfate” process is actually misleading since sulfide is the active ingredient, not sulfate. In the Kraft process, a mixture of sodium sulfide (Na2S) and sodium hydroxide (NaOH) is used to pulp the wood. The sulfide accelerates the delignification: consequently, the chips are exposed to the hot alkali for a shorter time than in the soda process; this makes it possible to produce a stronger pulp. The name “Kraft” is the German and Swedish word for strength and was chosen because these pulps are very strong. The Kraft process is superior to the soda process (NaOH only) with respect to the rate of pulping, pulp quality, and production cost. It also has several advantages over the sulfite process (H2SO3) can use any wood species can tolerate more bark cooking times are shorter less problems with pitch extremely high pulp strength very effective, well established recovery system can produce valuable by-products, such as tall-oil and turpentine Kraft pulping: heating up time = 0.5-1h overall cooking time =1-4 hours max. temp =1800C Acid sulfite: heating up time = 3-4 h overall cooking time = 5-6 hours max. temp =1400C The Process: Wood chips are screened to assure uniform size distribution. Chips that are to thick might end up producing uncooked centers (rejects). Thin chips might be “overcooked” and result in yield loss. Chips are presteamed and packed into a 1 digester. The presteaming is done to help pack the chips tightly and to saturate them with water so the chemicals can diffuse into the chips easier. The chips have to be packed as tight as possible; since the chips have to be covered with cooking liquor to many voids would mean the liquor has to be diluted to much. Cooking liquor is added to the digester. This liquor is called “white liquor” and contains the cooking chemicals NaOH and Na2S. In most cases some black liquor ( liquor at the end of the cook) is also recirculated into the digester. Black liquor recirculation results in increased solid concentration of the black liquor, which is important since this means less water has to be evaporated in the recovery system before the black liquor can be incinerated (energy savings). Cooking temperatures are most often around 160-170 o C. At the end of the cook pressure is partially released and with the help of some remaining pressure pulp is blown out of the digester. Chips are softened to the point that they don’t need any mechanical disintegration. Terminology in Kraft pulping In North America, the widely accepted practice is to express all sodium compounds in the cooking liquors on the basis of the equivalent amount of sodium oxide (Na2O). In Scandinavian and other European literature it is more common to select NaOH equivalent as the basis.The selection of sodium oxide as the North American standard is purely arbitrary. Sodium oxide only exists under anhydrous conditions and therefore is not present in the actual Kraft pulping liquor. It may be present in small amounts in the recovery furnace but converts instantly: Na2O + H2O 2 NaOH 2 This conversion means, 62 parts of Na2O (molecular weight) are equivalent to 80 parts of NaOH (NaOH molecular weight is 40, you get two molecules for each Na2O). Conversion of Na2S is based on the hypothetical equation; Na2O + H2S Na2S + H2O 62 parts of Na2O are equivalent to 78 parts of Na2S. Chemical Molecular Equation for Conversion of Conversion of weight conversion to chemical to Na2O to Na2O Na2O chemical NaOH 40 62/80 0.775 1.290 Na2S 78 62/78 0.795 1.258 Na2S X 9 H2O 240 62/240 0.258 3.871 Na2CO3 106 62/106 0.585 1.710 Standard Kraft Pulping terms: 1. Total Alkali: All sodium salts : NaOH + Na2S + Na2CO3 + Na2SO3 + Na2SO4 + Na2S2O3 etc. expressed as Na2O 2. Total Titratable alkali (TTA): NaOH + Na2S + Na2CO3 3. Active Alkali: NaOH + Na2S, expressed as Na2O 4. Effective Alkali: NaOH + ½ Na2S, expressed as Na2O 5. Activity: the percentage ratio of active alkali to total alkali, both expressed as Na2O 6. Causticizing efficiency: in white liquor the percentage ratio of NaOH to the sum of NaOH + Na2CO3, (both chemicals expressed as Na2O), and corrected for the NaOH content of the original green liquor in order to represent only the NaOH produced. 7. Causticity:The percentage ratio of NaOH, expressed as Na2O, to active alkali 8. Sulfidity: in white liquor, the percentage ratio of Na2S to Active Alkali, both expressed as Na2O. In green liquor, the percentage ratio of Na2S to total alkali both expressed as Na2O. 9. Reduction: in green liquor, the percentage ratio of Na2S to the sum of Na2SO4 + Na2S (+ any other soda-sulfur compounds if present), all expressed as Na2O. 3 10. Unreduced salt cake: Na2SO4 in the green liquor expressed as Na2SO4 11. Make up chemical consumption: The pounds of Na2SO4 , or other sodium compounds all expressed as Na2 SO4, added as new chemicals per ton of air- dry pulp production. 12. Chemical recovery efficiency: the percentage ratio – total chemical fed to the digester minus total chemical in the new Na2 SO4 ( make-up chemical) divided by total chemical fed to the digester. 13. Chemical loss: Total loss: the percentage ratio – total chemical in the new Na2 SO4 divided by the total chemical fed to the digester. Loss in cooking and pulp washing: the percentage ratio – total chemical fed to the digester minus total chemical fed to the evaporator divided by total chemical fed to the digester. Loss in evaporator and furnaces: the percentage ratio – total chemical fed to the evaporator minus total chemical in the green liquor divided by total chemical fed to digester Loss in recausticizing and mud washing: the percentage ratio- total chemical in the green liquor minus the total chemical in the white liquor divided by the total chemical fed to the digesters. Kraft Liquors White liquor: This is the cooking liquor added to the chips at the beginning, it contains NaOH and Na2S. pH is around 13.5-14. White liquors in mill can have several impurities (inefficiencies in recovery and causticizing). Impurities can be: 1. Sodium sulfate, sodium carbonate, sodium thiosulfate 2. Sodium chloride, Potassium salts 3. Iron, Manganese, Calcium These “ineffective” chemicals are called “dead load”. 2nd group (chloride) can cause corrosion problems. “Dead load” chemicals have no direct effect on pulping. But they help determine ionic strength of the liquor, therefore they can result in decreased lignin solubility. Black Liquor Liquor exiting the digester with the cooked chips. In addition to the inorganic material that entered with the white liquor, black liquor contains both organic and inorganic material removed from the wood during the cook. Significant portions of the sulfur compounds have been oxidized to sulfate and thiosulfate, also hydroxide concentration was reduced (lower pH). Trace metals have increased. 4 Concentration of Calcium and Silicate ion concentration is very important; it can cause scaling problems later on in the recovery system. Major difference between white liquor and black liquor is presence of organic material. Organic material is present mainly as organic acids. Also, significant amounts of dissolved alcohols such as methanol are present. Some organic material may be recovered in the chemical recovery system as the mixture of resin and fatty acids known as tall oil. Most of the organics carry through to the recovery furnace, where they are burned, and generating heat. Green liquor The liquor that results when the inorganic smelt from the recovery furnace is dissolved in water is called green liquor. The name comes from small amounts of iron sulfide, giving the liquor a greenish color. Green liquor has very high carbonate levels and a low hydroxide concentration. This combination does not provide the high pH necessary for the Kraft process -- carbonate has to be converted to hydroxide in the causticizing process before it can be used. Chemical Reactions of Wood Constituents Properties of wood which are of interest in chemical pulping are: 1. Porous structure, permitting penetration of water and chemical reagents 2. Chemical heterogeneity, allowing selective chemical reaction of its constituents ( you are trying to remove preferentially lignin) 3. The fibrous form of wood cells, which allows them, when separated, to be reorganized into the random network of fibers and fiber debris. In chemical pulping the fiber separation occurs in the middle lamella, leaving the primary wall intact. In order to achieve this separation, the components (lignin) of the middle lamella must be chemically removed, at least to the point that fiber separation is possible.
Details
-
File Typepdf
-
Upload Time-
-
Content LanguagesEnglish
-
Upload UserAnonymous/Not logged-in
-
File Pages17 Page
-
File Size-