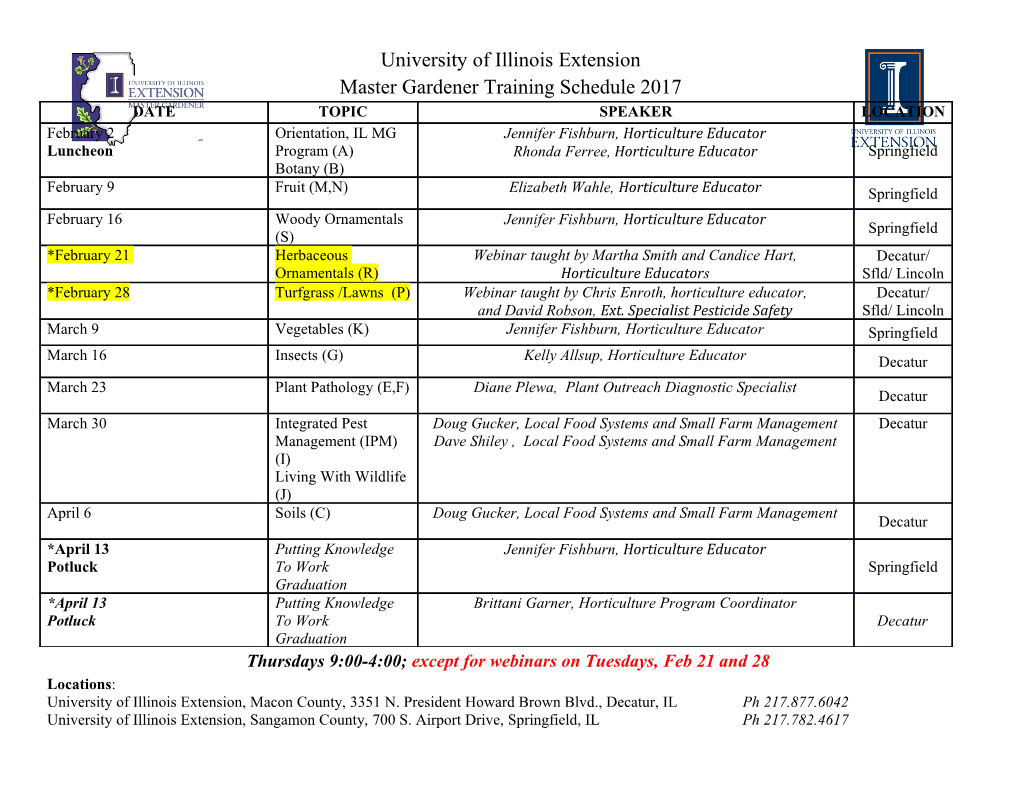
Bafna et al., International Journal of Advanced Engineering Research and Studies E-ISSN2249–8974 Proceedings of BITCON-2015 Innovations For National Development National Conference on : Information Technology Empowering Digital India Review Article 3D PRINTING: ENDLESS OPPORTUNITIES 1Harsh Bafna, 2Prof. Sarang Pitale Address for Correspondence 1Director, Ingenious Technosys, 36/B 2nd floor, New Civic Centre, Bhilai (C.G.) 2Asst. Professor, Bhilai Institute of Technology, Durg (C.G.) ABSTRACT 3D printing (or additive manufacturing, AM) is any of various processes used to make a three-dimensional object. In 3D printing, additive processes are used, in which successive layers of material are laid down under computer control. These objects can be of almost any shape or geometry, and are produced from a 3D model or other electronic data source. A 3D printer is a type of industrial robot. 3D printing in the term's original sense refers to processes that sequentially deposit material onto a powder bed with inkjet printer heads. More recently the meaning of the term has expanded to encompass a wider variety of techniques such as extrusion and sintering based processes. Technical standards generally use the term additive manufacturing for this broader sense. KEY WORDS: 3D, Printing. 1. INTRODUCTION In 1993, Massachusetts Institute of Technology 3D printing is a form of additive manufacturing (MIT) patented another technology, named "3 technology where a three dimensional object is Dimensional Printing techniques", which is similar to created by laying down successive layers of material. the inkjet technology used in 2D Printers. It is also known as rapid prototyping, is a mechanized In 1996, three major products, "Genisys" from method whereby 3D objects are quickly made on a Stratasys, "Actua 2100" from 3D Systems and reasonably sized machine connected to a computer "Z402" from Z Corporation, were introduced. containing blueprints for the object. The 3D printing In 2005, Z Corp. launched a breakthrough product, concept of custom manufacturing is exciting to nearly named Spectrum Z510, which was the first high everyone. This revolutionary method for creating 3D definition colour 3D Printer in the market. models with the use of inkjet technology saves time Another breakthrough in 3D Printing occurred in and cost by eliminating the need to design; print and 2006 with the initiation of an open source project, glue together separate model parts. Now, you can named Reprap, which was aimed at developing a create a complete model in a single process using 3D self-replicating 3D printer. printing. The basic principles include materials 3. WORKING OF A 3D PRINTER cartridges, flexibility of output, and translation of The model to be manufactured is built up a layer at a code into a visible pattern. time. A layer of powder is automatically deposited in the model tray. The print head then applies resin in the shape of the model. The layer dries solid almost immediately. The model tray then moves down the distance of a layer and another layer of power is deposited in position, in the model tray. The print head again applies resin in the shape of the model, binding it to the first layer. This sequence occurs one layer at a time until the model is complete. Figure 1: Typical 3D Printer 3D Printers are machines that produce physical 3D models from digital data by printing layer by layer. It can make physical models of objects either designed with a CAD program or scanned with a 3D Scanner. It is used in a variety of industries including jewellery, footwear, industrial design, architecture, engineering and construction, automotive, aerospace, dental and medical industries, education and consumer products. 2. HISTORY OF 3D PRINTER The technology for printing physical 3D objects from digital data was first developed by Charles Hull in 1984. He named the technique as Stereo lithography Figure 2: Side View of Printing Process and obtained a patent for the technique in 1986. The model to be manufactured is built up a layer at a While Stereo lithography systems had become time. A layer of powder is automatically deposited in popular by the end of 1980s, other similar the model tray. The print head then applies resin in technologies such as Fused Deposition Modelling the shape of the model. The layer dries solid almost (FDM) and Selective Laser Sintering (SLS) were immediately. The model tray then moves down the introduced. Int. J. Adv. Engg. Res. Studies/IV/II/Jan.-March,2015/137-140 Bafna et al., International Journal of Advanced Engineering Research and Studies E-ISSN2249–8974 distance of a layer and another layer of power is cross-section of the model. SHS is best for deposited in position, in the model tray. The print manufacturing inexpensive prototypes for concept head again applies resin in the shape of the model, evaluation, fit/form and functional testing. SHS is a binding it to the first layer. This sequence occurs one Plastics additive manufacturing technique similar to layer at a time until the model is complete. selective laser sintering (SLS), the main difference being that SHS employs a less intense thermal printhead instead of a laser, thereby making it a cheaper solution, and able to be scaled down to desktop sizes. 4.6 Selective Laser Melting (SLM) Selective laser melting is an additive manufacturing process that uses 3D CAD data as a digital Figure 3:A Typical 3D Printing Process Flow information source and energy in the form of a high- Chart power laser beam (usually an ytterbium fiber laser) to 4. CURRENT 3D PRINTING TECHNOLOGIES create three-dimensional metal parts by fusing fine 4.1 Stereo lithography metallic powders together. Stereo lithographic 3D printers (known as SLAs or The ASTM F42 standards committee groups stereo lithography apparatus) position a perforated selective laser melting into the category of "laser platform just below the surface of a vat of liquid sintering", although this is acknowledged as a photo curable polymer. A UV laser beam then traces misnomer because the process fully melts the metal the first slice of an object on the surface of this into a solid homogeneous mass, unlike selective laser liquid, causing a very thin layer of photopolymer to sintering (SLS) and direct metal laser sintering harden. The perforated platform is then lowered very (DMLS), which are true sintering processes. A slightly and another slice is traced out and hardened similar process is electron beam melting (EBM), by the laser. Another slice is then created, and then which, as the name suggests, uses an electron beam another, until a complete object has been printed and as the energy source. can be removed from the vat of photopolymer, 4.7 Electron Beam Melting (EBM) drained of excess liquid, and cured. Electron beam melting (EBM) is a type of additive 4.2 Fused Deposition Modelling (FDM) manufacturing (AM) for metal parts, originally Fused deposition modelling (FDM) is an additive patented and developed by Arcam. ASTM classifies manufacturing technology commonly used for EBM as a powder bed fusion technique, which also modelling, prototyping, and production applications. includes selective laser melting (SLM). The main It is one of the techniques used for 3D printing. difference is that EBM uses an electron beam as its FDM works on an "additive" principle by laying power source, as opposed to a laser. EBM technology down material in layers; a plastic filament or metal manufactures parts by melting metal powder layer by wire is unwound from a coil and supplies material to layer with an electron beam in a high vacuum. In produce a part. contrast to sintering techniques, both EBM and SLM 4.3 Selective Laser Sintering (SLS) achieve full melting of the metal powder. The term Selective Laser Sintering (SLS) is an additive selective laser sintering (SLS) is mostly historical and manufacturing technique that uses a laser as the is sometimes used to describe full melting or plastic power source to sinter powdered material (typically processes. metal), aiming the laser automatically at points in 4.8 Direct Metal Laser Sintering (DMLS) space defined by a 3D model, binding the material Direct metal laser sintering (DMLS) is an additive together to create a solid structure. It is similar to manufacturing technique that uses a laser as the direct metal laser sintering (DMLS); the two are power source to sinter powdered material (typically instantiations of the same concept but differ in metal), aiming the laser automatically at points in technical details. Selective laser melting (SLM) uses space defined by a 3D model, binding the material a comparable concept, but in SLM the material is together to create a solid structure. It is similar to fully melted rather than sintered, allowing different selective laser sintering (SLS); the two are properties (crystal structure, porosity, and so on). instantiations of the same concept but differ in SLS (as well as the other mentioned AM techniques) technical details. Selective laser melting (SLM) uses is a relatively new technology that so far has mainly a comparable concept, but in SLM the material is been used for rapid prototyping and for low-volume fully melted rather than sintered, allowing different production of component parts. Production roles are properties (crystal structure, porosity, and so on). expanding as the commercialization of AM DMLS was developed by the EOS firm of Munich, technology improves. Germany. 4.4 Multi-Jet modelling (MJM) 4.9 Laminated Object Manufacturing (LOM) This again builds up objects from successive layers Selective laser melting is an additive manufacturing of powder, with an inkjet-like print head used to process that uses 3D CAD data as a digital spray on a binder solution that glues only the required information source and energy in the form of a high- granules together.
Details
-
File Typepdf
-
Upload Time-
-
Content LanguagesEnglish
-
Upload UserAnonymous/Not logged-in
-
File Pages4 Page
-
File Size-