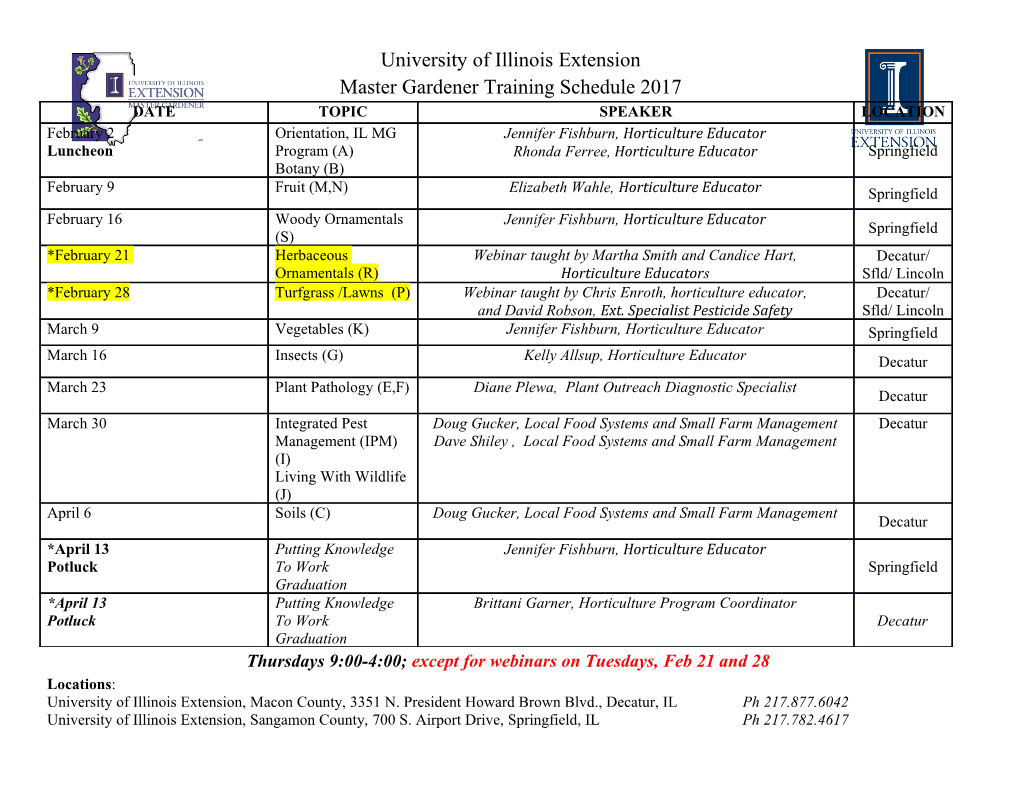
DESIGN OF JIGS & FIXTURES Introduction The successful running of any mass production depends upon the interchangeability to facilitate easy assembly and reduction of unit cost. Mass production methods demand a fast and easy method of positioning work for accurate operations on it. Jigs and fixtures are production tools used to accurately manufacture duplicate and interchangeable parts. Jigs and fixtures are specially designed so that large numbers of components can be machined or assembled identically, and to ensure interchangeability of components. JIGS It is a work holding device that holds, supports and locates the work piece and guides the cutting tool for a specific operation. Jigs are usually fitted with hardened steel bushings for guiding or other cutting tools. a jig is a type of tool used to control the location and/or motion of another tool. A jig's primary purpose is to provide repeatability, accuracy, and interchangeability in the manufacturing of products. A device that does both functions (holding the work and guiding a tool) is called a jig. An example of a jig is when a key is duplicated, the original is used as a jig so the new key can have the same path as the old one. BORING JIG FIXTURES It is a work holding device that holds, supports and locates the work piece for a specific operation but does not guide the cutting tool. It provides only a reference surface or a device. What makes a fixture unique is that each one is built to fit a particular part or shape. The main purpose of a fixture is to locate and in some cases hold a work piece during either a machining operation or some other industrial process. A jig differs from a fixture in that a it guides the tool to its correct position in addition to locating and supporting the work piece. Examples: Vises, chucks A VISE-JAW FIXTURE The basic purposes of developing and using suitable jigs and fixtures for batch production in machine shops are : to eliminate marking, punching, positioning, alignments etc. easy, quick and consistently accurate locating, supporting and clamping the blank in alignment of the cutting tool guidance to the cutting tool like drill, reamer etc. increase in productivity and maintain product quality consistently to reduce operator’s labor and skill – requirement to reduce measurement and its cost enhancing technological capacity of the machine tools reduction of overall machining cost and also increase in interchangeability. Role of Jigs and Fixtures on machining cost How do jigs and fixtures differ Advantages of Jigs and Fixtures PRODUCTIVITY: Jigs and fixtures increases the productivity by eliminating the individual marking, positioning and frequent checking. The operation time is also reduced due to increase in speed, feed and depth of cut because of high clamping rigidity. INTERCHANGEABILITY AND QUALITY: Jigs and fixtures facilitate the production of articles in large quantities with high degree of accuracy, uniform quality and interchangeability at a competitive cost . Advantages of Jigs and Fixtures SKILL REDUCTION: There is no need for skillful setting of work on tool. Jigs and fixtures makes possible to employ unskilled or semi skilled machine operator to make savings in labor cost. COST REDUCTION: Higher production, reduction in scrap, easy assembly and savings in labor cost results in ultimate reduction in unit cost. Fundamental principles of Jigs and Fixtures design LOCATING POINTS: Good facilities should be provided for locating the work. The article to be machined must be easily inserted and quickly taken out from the jig so that no time is wasted in placing the work piece in position to perform operations. The position of work piece should be accurate with respect to tool guiding in the jig or setting elements in fixture. FOOL PROOF: The design of jigs and fixtures should be such that it would not permit the work piece or the tool to inserted in any position other than the correct one. Fundamental principles of Jigs and Fixtures design REDUCTION OF IDLE TIME: Design of Jigs and Fixtures should be such that the process, loading, clamping and unloading time of the Work piece takes minimum as far as possible. WEIGHT OF JIGS AND FIXTURES: It should be easy to handle, smaller in size and low cost in regard to amount of material used without sacrificing rigidity and stiffness. JIGS PROVIDED WITH FEET: Jigs sometimes are provided with feet so that it can be placed on the table of the machine. Fundamental principles of Jigs and Fixtures design MATERIALS FOR JIGS AND FIXTURES: Usually made of hardened materials to avoid frequent damage and to resist wear. Example- MS, Cast iron, Die steel, CS, HSS. CLAMPING DEVICE: It should be as simple as possible without sacrificing effectiveness. The strength of clamp should be such that not only to hold the work piece firmly in place but also to take the strain of the cutting tool without springing when designing the jigs and fixtures. Principles And Methods Of Locating, Supporting And Clamping Blanks And Tool Guidance In Jigs And Fixtures It is already emphasized that the main functions of the jigs and fixtures are : (a) easily, quickly, firmly and consistently accurately • locating • supporting and • clamping the blank (in the jig or fixture) in respect to the cutting tool(s) (b) providing guidance to the slender cutting tools using proper bushes There are and can be several methods of locating, supporting and clamping depending upon the size, shape and material of the job, cutting tool and the machining work required. But some basic principles or rules are usually followed while designing for locating, supporting and clamping of blank in fixtures. Principles or rules of locating in jigs and fixtures For accurate machining, the work piece is to be placed and held in correct position and orientation in the fixture (or jig) which is again appropriately located and fixed with respect to the cutting tool and the machine tool. It has to be assured that the blank, once fixed or clamped, does not move at all. Any solid body may have maximum twelve degrees of freedom as indicated in Fig Principles or rules of locating in jigs and fixtures By properly locating, supporting and clamping the blank its all degrees of freedom are to be arrested as typically shown in Fig Some basic principles or rules need to be followed while planning for locating blanks in fixtures, such as; One or more surfaces (preferably machined) and / or drilled / bored hole(s) are to be taken for reference The reference surfaces should be significant and important feature(s) based on which most of the dimensions are laid down Locating should be easy, quick and accurate In case of locating by pin, the pins and their mounting and contact points should be strong, rigid and hard A minimum of three point must be used to locate a horizontal flat surface Some basic principles or rules need to be followed while planning for locating blanks in fixtures, such as; The locating pins should be as far apart as feasible V-block and cones should be used for self-locating solid and hollow cylindrical jobs as typically shown in Fig Some basic principles or rules need to be followed while planning for locating blanks in fixtures, such as; Sight location is applicable to first – operation location of blank with irregular surfaces produced by casting, forging etc. as indicated in Fig when the bracket is first located on two edges to machine the bottom surface which will be used for subsequent locating. Some basic principles or rules need to be followed while planning for locating blanks in fixtures, such as; Sight location is applicable to first – operation location of blank with irregular surfaces produced by casting, forging etc. as indicated in Fig when the bracket is first located on two edges to machine the bottom surface which will be used for subsequent locating. Essential features of Jigs and Fixtures Essential features of Jigs and Fixtures Essential features of Jigs and Fixtures Essential features of Jigs and Fixtures General rules for designing General rules for designing MATERIALS USED MATERIALS USED MATERIALS USED General methods of locating Locating blanks for machining in lathes In lathes, where the job rotates, the blanks are located by ο fitting into self centering chuck ο fitting into 4 – independent jaw chuck and dead centre ο in self – centering collets ο in between live and dead centers ο by using mandrel fitted into the head stock – spindle fitting in a separate fixture which is properly clamped on a driving plate which is coaxially fitted into the lathe spindle. Locating by flat surfaces Fig. typically shows locating jobs by their flat surfaces using various types of flat ended pins and buttons. Locating by holes Locating by holes Locating on mandrel or plug Supporting – principles and methods A work piece has to be properly placed in the jig or fixture not only for desired positioning and orientation but also on strong and rigid support such that the blank does not elastically deflect or deform under the actions of the clamping forces, cutting forces and even its own weight. Basic principles or rules to be followed while designing or planning for supporting supporting should be provided at least at three points supporting elements and system have to be enough strong and rigid to prevent deformation due to clamping and cutting forces unsupported span should not be large to cause sagging as indicated in fig. Basic principles or rules to be followed while designing or planning for supporting supporting should keep the blank in stable condition under the forces as indicated in fig.
Details
-
File Typepdf
-
Upload Time-
-
Content LanguagesEnglish
-
Upload UserAnonymous/Not logged-in
-
File Pages127 Page
-
File Size-