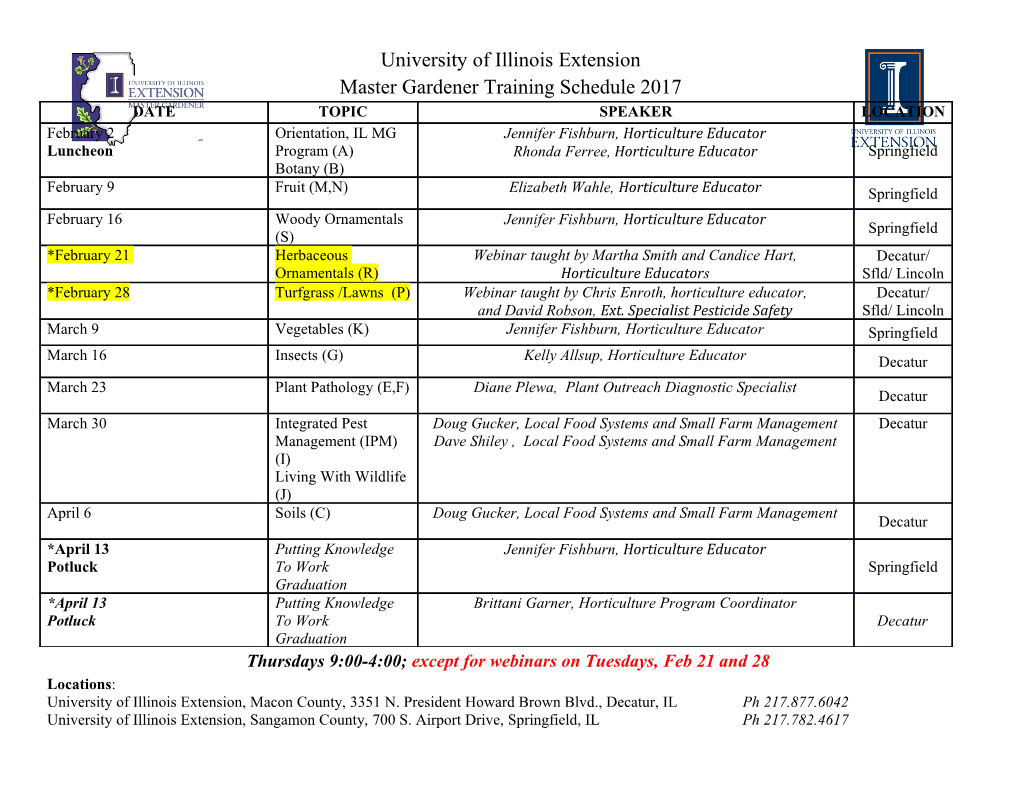
Recycling of Passenger Vehicles: A framework for upcycling and required enabling technologies by Sean Michael Kelly A Dissertation Submitted to the Faculty of the WORCESTER POLYTECHNIC INSTITUTE in partial fulfillment of the requirements for the Degree of Doctor of Philosophy in Material Science & Engineering May 2018 APPROVED: __________________________________ Professor Diran Apelian, Advisor Alcoa-Howmet Professor of Engineering Founding Director of Metal Processing Institute __________________________________ Professor Richard D. Sisson Jr. George F. Fuller Professor Materials Science and Engineering Program Director Abstract The automotive industry is expected to transition from a net-consumer to a net-producer of aluminum scrap as aluminum-intensive vehicles (AIVs, i.e., Ford’s aluminum-bodied F-150) begin to reach end-of-life (EOL). In the past, the industry has downcycled aluminum scrap to meet the consumption demands of the automotive sector. With the shift to having a large supply of this scrap in the near future, the industry needs to recover and reuse EOL Al by utilizing a circular economic model, create value via an upcycling paradigm (vs downcycling). This work establishes a platform as to how the recycling industry can be restructured to create value in our waste streams and is organized in three segments: First, an analysis of the flow of automobiles at EOL was carried out from the perspective of recovery and reuse; a recycling rate for Al has been determined, and the factors that go into the dynamics of the recycling rate have been identified. Secondly, the current state of the market was surveyed to evaluate where improvements could be made to affect material collection and recovery. The latter led to compositional characterization of aluminum auto-shred to identify the alloys in the mixture, and thereby the needed intelligent sorting systems for upcycling. Thirdly, these results were used in a dynamic material flow model to predict how the composition of auto-shred will change due to increased aluminum usage and as a function of various end-of-life processing scenarios. The outcome and impact of this work is that we have established a platform that enables the ELV recycling industry to upcycle the large amount of Al that will be available in the near future. These results will be discussed and reviewed during this presentation. ii Acknowledgments What a journey this has been. One that would not have been possible without the support from all those around me. To my family, thank you for all your love and care throughout this entire process. Meaghan, the love of my life, thank you for your patience and for being my rock. I could not have done this without you. You motivate me on a daily basis, and I look forward to sharing my life with such a beautiful, selfless person. Hank and Phil (my dogs), you were probably more of a hindrance than a help, but coming home to you guys every night made me smile even on my worst of days. WPI and local friends, you all hold a special place in my heart. I greatly appreciate all of the help you provided and look forward to developing our friendships and professional relationships further. MTE, MPI, and CR3 family: Carol, Maureen, Renee, Rita, GlorieAnne, Mike, Meagan, Professor Emmert, Professor Wang, Professor Kazantzis, Professor Mishra, Professor Trapp, and anyone else along the way that I may have missed here, thank you for your patience and guidance. We truly have a world class team! To the CR3 consortium, I hope you realize the effect that your professional guidance and support has on students like myself. You have certainly propelled me into my career. I am very grateful for all you have done for me: Mark Bauer, Dr. Uwe Habich, Dr. Georg Rombach, Jason Looman, Brandon Barnett, Dr. Nalin Kumar and team at UHV Technologies, Bob DeSaro, Anne Pichat, Karen Smith and all else! A very large thank you go to all the members from industry and other universities that helped me grow and gave me invaluable guidance along the way: Doug Richman, Jim Dickson, Chris Cooney, David Rosenblum, Larry Kraynik, Ray Peterson, Sarah Willcutts, Dr. Randy Kirchain, Professor Elsa Olivetti, Chris Dimarzio, Dr. Marshall Wang, John Weritz, and the Aluminum Association, Colin Kelly, Lee Bray, Mason Ruffing, Dr. David Spencer, Scott Robertson Jr., Laurent Chappius, and all else! Let me also express my gratitude to the team at Steinert in Kentucky and Cologne. Thank you for your hospitality, guidance, and responsiveness throughout this project: Travis Bezinger, Dr. Nico Schmalbein, Andreas Laumen, Dr. Alexander Khoury, and anyone that I missed! To the IndEcol group, you were such gracious hosts and truly enabled a successful outcome for this project through your support in Industrial Ecology, thank you, Professor Daniel Müller and team! Dr. Amund Løvik, thank you for supplying the foundational model for this work. I look forward to collaborating with you further! To my committee, I thank you for your time and effort: Dr. Hilmer Kirschner, Dr. Uwe Habich, Professor Daniel Müller, Professor Mishra, Professor Sisson, and Dr. Kevin Andersen Professor Sisson, thank you for your support and all the conversations along the way. Whether on topic or off, they were relieving, and I enjoyed them very much so. Go Hokies! And finally, last, but certainly not least, Professor Apelian. No words can express my gratitude for all that you have done for me. I would be nowhere near the person I am today if I hadn’t come to your office in my socks and sandals that spring day in 2014. You are more than my advisor you are family. I am honored to have worked with you on this project, and I am excited for what is next! Thank you for your patience and for believing in me. iii Executive Summary What is the need and the opportunity? Our generation has the unique opportunity to break the linear model for material consumption and transition to a circular system that exhausts all options to reduce waste and create value. Value creation is not defined here in the traditional sense but rather by social and environmental benefit. In a circular economic model, a distinction is made between upcycling and downcycling. Upcycling involves maximizing value creation, and downcycling follows the take-make-waste model and downgrades material resources. An example of the latter is the way aluminum is recycled from end of life vehicles (ELVs) today in the US. There are more than 30 aluminum alloys in passenger vehicles yet only two low-value secondary alloys are formed from collected automotive aluminum (Al) at end of life (EOL). Such downcycling practice is feasible today due to the relatively low weight of aluminum in the vehicles being processed currently, in addition to, fluid international trade, and an engine-dominant vehicle fleet. The latter is critical as auto-shred Al is used to produce the secondary cast alloys that form engine and transmission components. However, each of these factors is shifting away from what the ELV processing industry has become accustomed to. The curb weight of Al is expected to approach 16% by the year 2028. The cars processed today have about 8% Al by weight. Undeveloped nations will become more industrialized and will also become net exporters of Al scrap which will diminish trade opportunities. Finally, the demand for secondary cast Al will decrease as electric vehicles become increasingly accepted as a more environmentally-friendly drivetrain alternative. When supply and demand trend in opposing directions, a shift in processing paradigm is required to prevent the development of surplus. Herein, we explore and expand on viable options to reduce waste, to avoid auto-shred aluminum from downcycling, and propose technological means to create value through upcycling of ELVs. Approach Taken: Shifting the Processing Paradigm of Automotive Al at EOL The structure of this work was strategically designed to provide the auto-Al recycling industry with the tools it will need to transition from a linear to a circular economy. The strategy followed is given below: 1) A framework was designed to quantify the inefficiencies of automotive Al recycling at EOL. From dismantling to melting collected scrap, the processing flow through this recycling system has been assessed and a framework is established and presented (Manuscript 1). 2) This initial field study motivated the optimization of scrap Al processing. The compositional “DNA” of Twitch (i.e., auto-shred Al) was investigated to identify upcycling opportunities (Manuscript 2). iv 3) Sorting system criteria were designed based on this fundamental characterization and executed at the commercial scale to evaluate each sorting system’s upcycling potential. These criteria were verified using melt analysis and the resulting compositions were processed in a blending model to quantify the value of the upgraded shredded scrap (Manuscript 3). 4) The knowledge developed during the first three stages of this research enabled the redesign of a dynamic material flow analysis (dMFA) model paired with blending optimization for secondary alloy development. This sustainability model is also used to estimate the future state of the commodity trade market and the change in element concentration that can be expected due to passenger vehicle light-weighting (Manuscript 4). With this introduction of the strategy followed, we now summarize the salient points of each of these four segments. In their totality, we have established the definition of a new recycling standard: one that emphasizes upcycling and value creation in our resource streams and alleviates surplus development. (1) A Quantitative Framework for End-Of-Life (EOL) Automotive Aluminum Recycling Rate Need: Where are the inefficiencies in current recycling practice? Aluminum sheet consumption in the automotive industry is experiencing an unprecedented growth that is driven by passenger vehicle light-weighting efforts.
Details
-
File Typepdf
-
Upload Time-
-
Content LanguagesEnglish
-
Upload UserAnonymous/Not logged-in
-
File Pages166 Page
-
File Size-