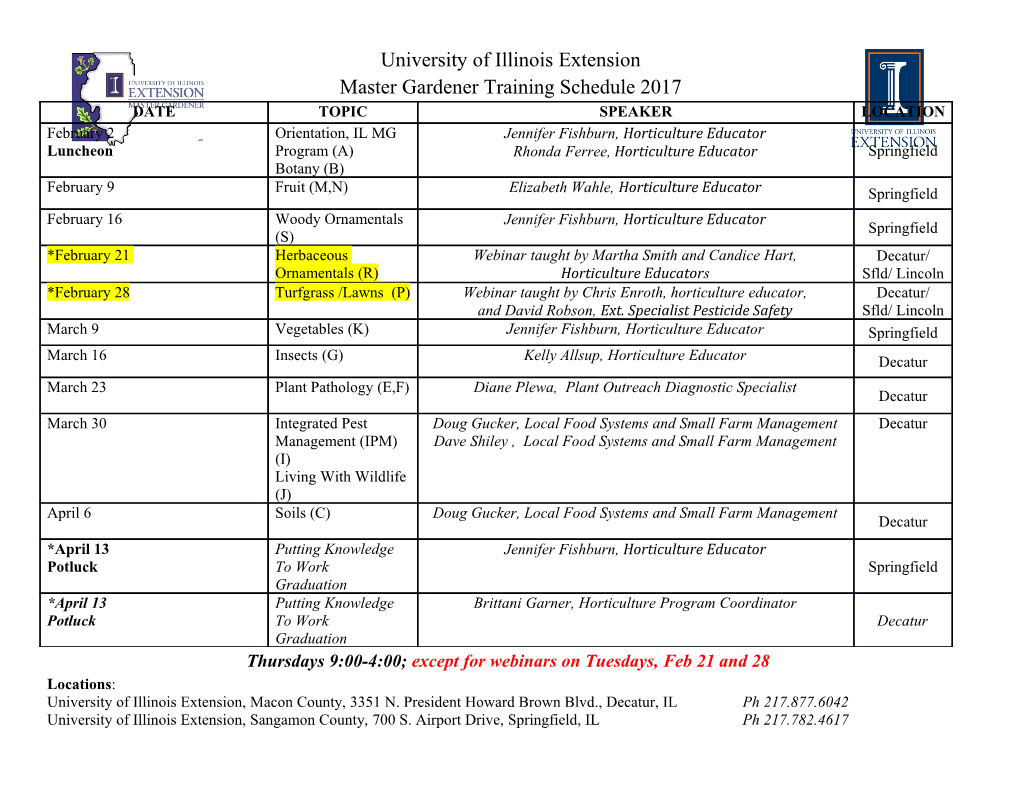
- REPORT 20 o h- a: O o_ ADVISORY GROUP FOR AERONAUTICAL RESEARCH AND DEVELOPMENT REPORT 20 DESIGN AND CONSTRUCTION OF WIND TUNNEL MODELS by JOSEPH J. MUNCEY and DAVID M. POTE FEBRUARY 1956 NORTH ATLANTIC TREATY ORGANIZATION PALAIS DE CHAILLOT, PARIS 16 REPORT 2 0 NORTH ATLANTIC TREATY ORGANIZATION ADVISORY GROUP FOR AERONAUTICAL RESEARCH AND DEVELOPMENT DESIGN AND CONSTRUCTION OF WIND TUNNEL MODELS by Joseph J. Muncey and David M. Pote This Report was presented at the Eighth Meeting of the Wind Tunnel and Model Testing Panel, held from February 20th to 25th. 1956 in Rome, Italy. SUMMARY The Cornell Aeronautical Laboratory major wind tunnel is prescheduled to operate on an around-the-clock schedule. The achievement of accurate results under pressure of such a schedule has posed many problems in the design and construction of wind tunnel models. This paper discusses some methods and techniques which have been evolved. SOMMAIRE La soufflerie principale du Cornell Aeronautical Laboratory est prevue pour un fonctionnement ininterrompu de 24 heures par jour. L'obtention de resultats precis en presence d'un programme aussi charge a pose de nombreux problemes relatifs a la conception et a la construction des maquettes pour souffleries. Quelques unes des methodes et des techniques elaborees en consequence sont ici examinees. 533.6.071.3 3b8g ii CONTENTS Page SUMMARY ii LIST OF FIGURES iv 1. INTRODUCTION 1 2. TYPES OF MODELS 2 3. MODEL DESIGN 3 4. METHODS OF CONSTRUCTION 5 5. RELATED MODEL AND WIND-TUNNEL EQUIPMENT 7 6. MACHINERY AND TOOLS 8 7. THE MODEL MAKER 8. QUALITY CONTROL 9. CONCLUSIONS FIGURES 10 DISTRIBUTION iii LIST OF FIGURES Page Typical subsonic model 10 Typical high-speed model 10 Reflection-plane model 11 Propeller nacelle assembly 11 12 Example of model making practice 12 Strain-gage hinge-moment installation 13 13 Example of model making practice 14 14 Supersonic model components 15 Internal pressure rake 15 Propeller duplicating machine 16 Propeller blade inspection 17 Molded plastic fiberglass fuselage shell 18 Method of Installing pressure tubes in thin airfoil sections 18 Fig.17 Tolerance for high-speed wind-tunnel models 19 Fig.18 Tolerance for high-speed wind-tunnel models. (Proposed) 20 iv DESIGN AND CONSTRUCTION OF WIND TUNNEL MODELS Joseph J. Muncey and David M. Pote* 1. INTRODUCTION The Wind Tunnel Department of the Cornell Aeronautical Laboratory offers a testing service to the aircraft industry and, because of heavy demand, operates its variable- density &k ft x 12 ft tunnel (2.6 m x 3.6 m. After modernization it will be 8 ft x 8 ft transonic.) on a 24 hours per day schedule. During the past year over 4000 hours of tunnel occupancy have been logged. The airplane designer is naturally anxious to obtain test data as soon as possible. This desire is reflected in a demand that wind tunnel occupancy follow design specifi­ cation by a minimum of time. As a result, a great deal of pressure is placed upon the model designers and upon the model makers to accomplish their tasks rapidly. At the same time, rather high standards of dimensional similitude between model and prototype airplane are required. In our substantially unique position of designing, building and testing models for many different airplane companies, we have developed a number of special design fea­ tures and methods of construction. We hope that the ones we can present in this paper will be of Interest to you. 2. TYPES OF MODELS The models most frequently tested in the C.A.L. tunnel include the following types:- (i) Subsonic model, usually about 60 in. span. (150 cm) (11) Transonic model of 18 to 48 in. span. (45 to 125 cm) (iii) Reflection-plane model of approximately 48 in. half span. (125 cm) (iv) Flutter models, approximately 18 in. chord x 36 in. span. (45 cm x 125 cm) (v) Propeller models of 4, 5, and 6 ft diameter. (125, 150, and 180 cm) (i) Subsonic model The subsonic type of model is a complete model (Fig.l). It is sting mounted, houses a six-component balance and all movable surfaces are equipped for hinge-moment measure­ ments. An extensive-pressure survey system and duct rakes are also installed. This model is of composite construction, reinforced wood fuselage with metal wing and tall surfaces. A few of these models are powered by high cycle variable frequency motors equipped with propellers of exact scale. These models have movable control surfaces. (ii) Transonic model The usual transonic model (Fig.2), also sting mounted, now of approximately 18 in. span will be increased to 48 in. span after tunnel modernization. It is subjected to 'Respectively Superintendent of the Model Shop and Assistant Head of the Wind Tunnel Department, Cornell Aeronautical Laboratory, Buffalo 11, New York. high loads which demand hardened steel for structural members. This type is complete in detail and fully instrumented. Within the fuselage and bolted directly to the wing it houses a balance capable of measuring three moments and three external forces. This model can be tested with or without canopy, tail, dropped leading edges or nacelles. (iii) Reflection-plane model A subsonic reflection-plane model (Pig.3) usually has a half span of approximately 48 inches. It is mounted on a balance system located beneath the tunnel floor. The plane of symmetry of this half span model is located approximately 1& in. above the floor. A non-metric marginal-sealed plateau fills the 1,4 in. gap. A grounding strip is attached to register interference. The horizontal tail is isolated on a separate balance. This is a fully instrumented model. (iv) Flutter models The airfoil flutter model is constructed of flexible materials molded, bonded and assembled in such fashion that specific bending and torsional stiffnesses can be achieved. Models are suspended from an oscillator attached to the tunnel ceiling. Subsonic, transonic and supersonic types are instrumented to measure frequency and amplitude of flutter. (v) Propeller models Cornell operates a 2000 h.p. propeller dynamometer within a removable tunnel test section. The assembled propeller models measure 4, 5, or 6 ft in diameter (See Fig.4). They are mounted on co-axial shafts projecting from a pedestal type nacelle. Thrust, torque and blade bending are measured during single rotation to 7800 r.p.m. in an air­ stream approaching Mach 0.9. The propeller hubs, both manually adjusted and control­ lable, are machined from two steel blocks joined at the blade center line. The average hub is about 10 in. diameter x 9 in. long (25 cm x 23 cm). The blade retention sockets are precisely machined and the shaft hole is broached to match the dynamometer shaft. The blades are machined and hand finished from hardened alloy steel forgings. To round out this paper, we mention here some examples of special model design. (vl) Helicopter rotor blade assemblies for whirl tests to determine blade characteris­ tics. Assemblies up to 84 in. (214 cm) in diameter are rotated by an instrumented hub. Motion and attitude records are transmitted through slip rings. (vii) Engine nacelle models are fitted over and extend forward of the propeller dynamo­ meter nacelle. Propeller effectiveness pressures and flow recovery are measured. Remotely operated valves regulate flow. (viii) The dynamic stability model Is a balanced light weight three-dimensional model of extreme rigidity. Forces, moments and oscillation data are recorded simultaneously. Maximum frequency is 15 oscillations per second. Model weight cannot exceed 15 pounds (6.8 kg). This type of model is usually suspended at the forward end of a spring-type sting which permits the model to oscillate about a point located at the airplane center of gravity or any point forward to infinity. An internal flexture type balance is located between model frame and sting for the measurement of pitching moment and normal force. 3. MODEL DESIGN We believe the theoretical ultimate in model design would be a hollow model made from one piece of steel. This configuration would offer rigidity, strength, and smoothness beyond anything obtained by joining together numerous separate parts. It is obvious that this ultimate is not practical. Need for housing the balance, and provisions for moving the control surfaces and for external configuration change prohibit such simple design. Therefore, rigid fit of mating parts is essential. Any relative movement or deflection will contribute to erroneous data. All sound models have been the accomplishment of successful co-ordination among the Aerodynamics, Design, and Shop groups. It is imperative that the design group be given detail specifications as to the requirements of the aerodynamic or engineering group before starting the detail design of a model. Specific items of information furnished either by the customer or the Cornell Aerodynamics Department are as follows: (1) All basic model dimensions or a complete set of templates reduced to model scale. (2) The required test configurations which determine the extent of complete removal components. (3) The maximum angle range of tests in pitch, yaw and roll, and the approximate maximum applied loads on the model, including normal force, pitching moment and side force. (4) Movable surfaces, if any, and desired angle settings, along with the approximate maximum hinge moment expected during the tests. (5) Which hinge moments to be measured. (6) The number of load and moment components that are to be measured, along with their approximate maximum values, will assist in the selection of the proper balance to be used or indicate the need of the design of a new balance. (7) The desired number, size and locations of all pressure orifices. (8) Any other special instrumentation that is required. Examples are provision for measuring forces on external stores, or for total vertical or horizontal tail loads.
Details
-
File Typepdf
-
Upload Time-
-
Content LanguagesEnglish
-
Upload UserAnonymous/Not logged-in
-
File Pages36 Page
-
File Size-