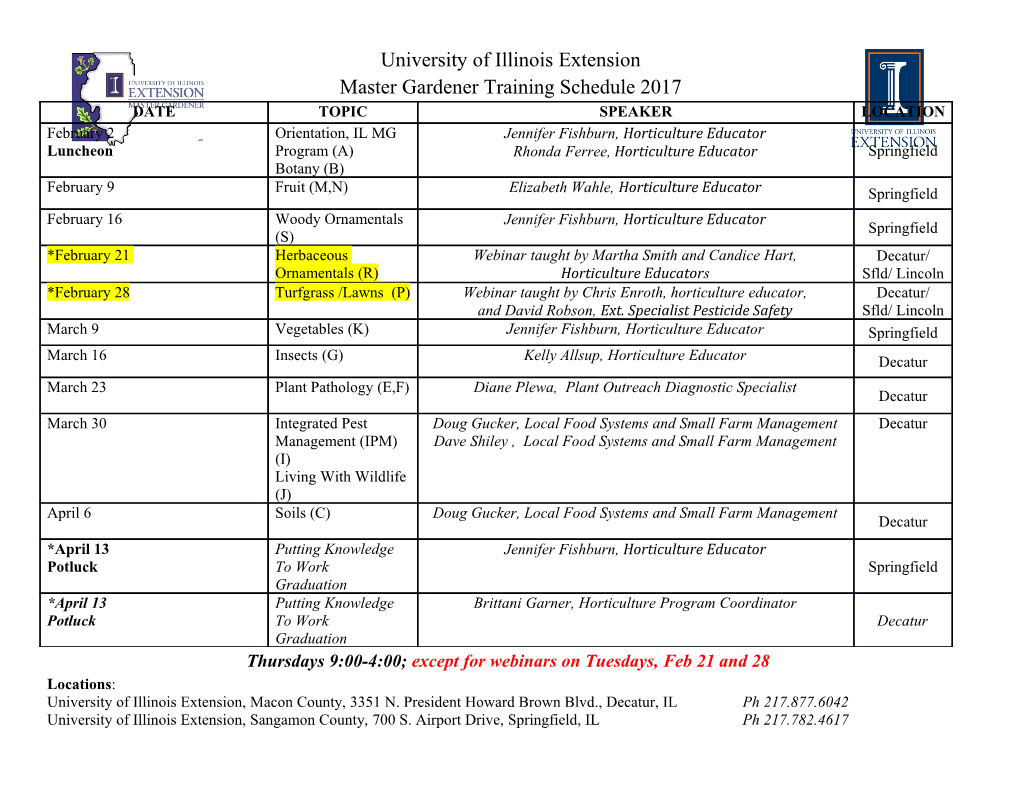
View metadata, citation and similar papers at core.ac.uk brought to you by CORE provided by Institute Of Mechanics,Chinese Academy of Sciences Cryogenics 50 (2010) 743–749 Contents lists available at ScienceDirect Cryogenics journal homepage: www.elsevier.com/locate/cryogenics CFD analysis of thermodynamic cycles in a pulse tube refrigerator ⇑ Ling Chen a, Yu Zhang a, , Ercang Luo b, Teng Li a, Xiaolin Wei a a Key Laboratory of Environmental Mechanics, The Institute of Mechanics, Chinese Academy of Sciences, Beijing 100190, China b Key Laboratory of Cryogenics, The Technical Institute of Physics and Chemistry, Chinese Academy of Sciences, Beijing 100190, China article info abstract Article history: The objectives of this paper are to study the thermodynamic cycles in an inertance tube pulse tube refrig- Received 7 June 2010 erator (ITPTR) by means of CFD method. The simulation results show that gas parcels working in different Received in revised form 18 August 2010 parts of ITPTR undergo different thermodynamic cycles. The net effects of those thermodynamic cycles Accepted 26 August 2010 are pumping heat from the low temperature part to the high temperature part of the system. The simu- lation results also show that under different frequencies of piston movement, the gas parcels working in the same part of the system will undergo the same type of thermodynamic cycles. The simulated thermal Keywords: cycles are compared with those thermodynamic analysis results from a reference. Comparisons show that Pulse tube refrigerator both CFD simulations and theoretical analysis predict the same type of thermal cycles at the same loca- CFD Thermodynamic cycles tion. However, only CFD simulation can give the quantitative results, while the thermodynamic analysis is still remaining in quality. Ó 2010 Elsevier Ltd. All rights reserved. 1. Introduction effect to illustrate the refrigeration in PTRs. This theory points out that when gas flows through a tube half filled with porous mate- Pulse tube refrigerator (PTR) has many advantages over conven- rial, it will experience strong non-symmetric heat exchange and tional refrigerators, such as no moving part, low cost, high reliabil- consequently generate refrigeration. Besides those discussions, ity and less mechanical vibration. Therefore, the PTR is recognized thermo-acoustic effect is also introduced to explain the mecha- as one of the most promising refrigerators in the future. Since the nism of PTRs. However, all of these theories have their own limita- invention of the basic pulse tube refrigerator (BPTR) in the early tions and cannot explain the mechanism of the PTRs adequately. 1960s [1], pulse tube refrigerator has experienced several signifi- The theories mentioned above fail to give detail information of cant structural improvements including the orifice pulse tube thermodynamic processes of the working gas in a cycle, which refrigerator (OPTR) [2], the double inlet pulse tube refrigerator must be important for understanding the mechanism of PTRs. (DIPTR) [3], the multi-stage pulse tube refrigerator [4] and most re- The thermodynamic processes of the working gas in PTR are very cently the inertance tube pulse tube refrigerator (ITPTR) [5]. All of different from those described in classical thermodynamic cycles these improvements have led to the technical progress of the PTR, such as an ideal Stirling cycle, in which every portion of the gas and so far the lowest temperature attained by the pulse tube is assumed to undergo the exact same thermodynamic cycle. In refrigerator has already reached about 1.3 K [6]. PTR each small portion of the working gas, viz. a gas parcel, oscil- However, till now, the mechanism of PTR has still not yet been lates only in a small part, and the thermal cycles at different parts fully understood. Several theories have been developed to explain should be also different [10]. In 1997, Liang [10] proposed a sinu- the refrigeration mechanism of PTRs since their invention. Gifford soidal model to analyze the thermodynamic processes of gas par- and Longsworth first explained the refrigeration effect in BPTR by a cels oscillating in a regenerator. In his analysis, results show that process named surface heat pumping [7], which is determined by each gas parcel in the regenerator works as either a heat engine both the thermal interactions between the wall of the BPTR and or a refrigerator. But Liang did not attain the transient temperature the properties of the working gas; however, this theory is only suit- of the gas parcel and the obtained function of the regenerator is able for PTRs operating under low frequencies. Peter and Radeb- questionable. In 2004, a further theoretical study was conducted augh [8] assumed that phase shift between pressure and the by Luo [11] to investigate the thermodynamic cycles in the regen- mass flow rate is the major mechanism for heat transfer in PTRs. erator. That theory is named as meso-scope thermodynamic the- In 1990s, Liang et al. [9] proposed thermodynamic non-symmetry ory. With some assumptions and thorough mathematical computation, the thermodynamic cycles of these characteristic ⇑ Corresponding author. Tel.: +86 10 82544231; fax: +86 10 62561284. gas parcels were attained. However, in Luo’s analysis some E-mail address: [email protected] (Y. Zhang). assumptions such as the working gas has no viscosity, the phase 0011-2275/$ - see front matter Ó 2010 Elsevier Ltd. All rights reserved. doi:10.1016/j.cryogenics.2010.08.004 744 L. Chen et al. / Cryogenics 50 (2010) 743–749 Nomenclature X piston displacement (m) Greek letters Xa piston displacement amplitude (m) x angular frequency f operating frequency (Hz) c porosity t time (s) q density (kg/m3) m intrinsic velocity (m/s) a permeability E energy (J/kg) l viscosity (kg/m s) p pressure (bar) ~s~ stress tensors (N/m2) t specific volume (m3/kg) T temperature (K) Subscripts s specific entropy (J/kg K) f fluid k thermal conductivity (W/m K) r radial coordinate h enthalpy (J/kg) s solid À1 C2 initial resistance factor (m ) x axial coordinate Cp specific heat (J/kg K) ref reference R gas constant (J/kg K) shift between fluctuated pressures and flow rates is keeping uni- Table 1 form everywhere, are not reasonable. Furthermore, those analyses Dimensions of the ITPTR. are still qualitative, but have no quantitative meanings. In this paper, two-dimensional axi-symmetric CFD simulations Components Diameter (mm) Length (mm) are conducted to analyze the thermodynamic processes in ITPTR. Compressor 19.08 7.5 Instead of assumptions, CFD method directly calculates the gas Transfer line 3.1 101 WHX1 8 20 velocity, the gas temperature, the gas pressure and the phase shift Regenerator 8 58 of different variables at different locations. After CFD calculations, CHX 6 5.7 summarizing the obtained results in Lagrangian’s view, the quanti- Pulse tube 5 60 tative results of thermodynamic cycles will come out. WHX2 8 10 Inertance tube 0.85 684 Reservoir 26 130 2. Simulation model hi @ ~ ðq EÞþr ð~vðq E þ pÞÞ ¼ r Á kf rT þ ~s Á ~v ð4Þ A two-dimensional, axi-symmetric schematic of the ITPTR @t f f system is shown in Fig. 1. The sizes of all parts of the system are where listed in Table 1. The details of the simulated system can be found p v2 in the publication of Cha et al. [12]. E ¼ h À þ ð5Þ A commercial CFD code Fluent [14] is applied in this simulation. q 2 The amount of computational cells reaches 4600. The piston move- The mass, momentum and energy equations for the porous media ment is described as are as follows: X ¼ Xa sinðxtÞð1Þ @ 1 @ @ ðcqf Þþ ðcrqf vrÞþ ðcqf vxÞ¼0 ð6Þ where Xa = 4.511 mm is the amplitude, x =2pf is the angular veloc- @t r @r @x ity and f is the operating frequency. A User Define Function (UDF) is written to track and guide the movement of the piston. @ ~ ðcqf~vÞþr ðcqf~v~vÞ¼crp þ r Á c~s The mass, momentum, and energy equations solved by Fluent @t for the working gas are [12,14] l 1 À ~v þ C2 q j~vj~v ð7Þ a 2 f @qf 1 @ @ þ ðrqf vrÞþ ðqf vxÞ¼0 ð2Þ @t r @r @x @ ½þcq Ef þ ðÞ1 À c q Es r Á ½~vðÞq Ef þ p @t f s f @ ~ hi ðqf ~vÞþr ðqf~v~vÞ¼rp þ r ð~sÞð3Þ ~ @t ¼ r Á ðÞckf þð1 À cÞks rT þ c~s Á ~v ð8Þ 9 1 34 7 5 2 6 8 Fig. 1. Schematic of the physical model of ITPTR: (1) compressor, (2) transfer line, (3) after cooler (WHX1), (4) regenerator, (5) cold end heat exchanger (CHX), (6) pulse tube, (7) hot end heat exchanger (WHX2), (8) inertance tube, and (9) reservoir. L. Chen et al. / Cryogenics 50 (2010) 743–749 745 where c is porosity of the porous media, a is the permeability and C2 gas parcels are: gas parcel oscillating in after cooler (WHX1) and is the inertial resistance factor. In simulation, c = 0.69, a = 1.06 Â regenerator; gas parcel oscillating entirely in regenerator; and À10 2 4 À1 10 m , and C2 = 7.609 Â 10 m . gas parcel oscillating in regenerator and CHX. The gas parcels cho- In this simulation, the working gas is helium, which is modeled sen are located on the axis where the radial velocities of the gas as a compressible ideal gas. Its viscosity is set to be temperature- parcels are far smaller than the axial velocities, so that the influ- dependent. The walls of WHX1 and WHX2 are maintained at ences of the radial velocities of the gas parcels can be neglected. 300 K while all the other system walls are assumed to be adiabatic.
Details
-
File Typepdf
-
Upload Time-
-
Content LanguagesEnglish
-
Upload UserAnonymous/Not logged-in
-
File Pages7 Page
-
File Size-