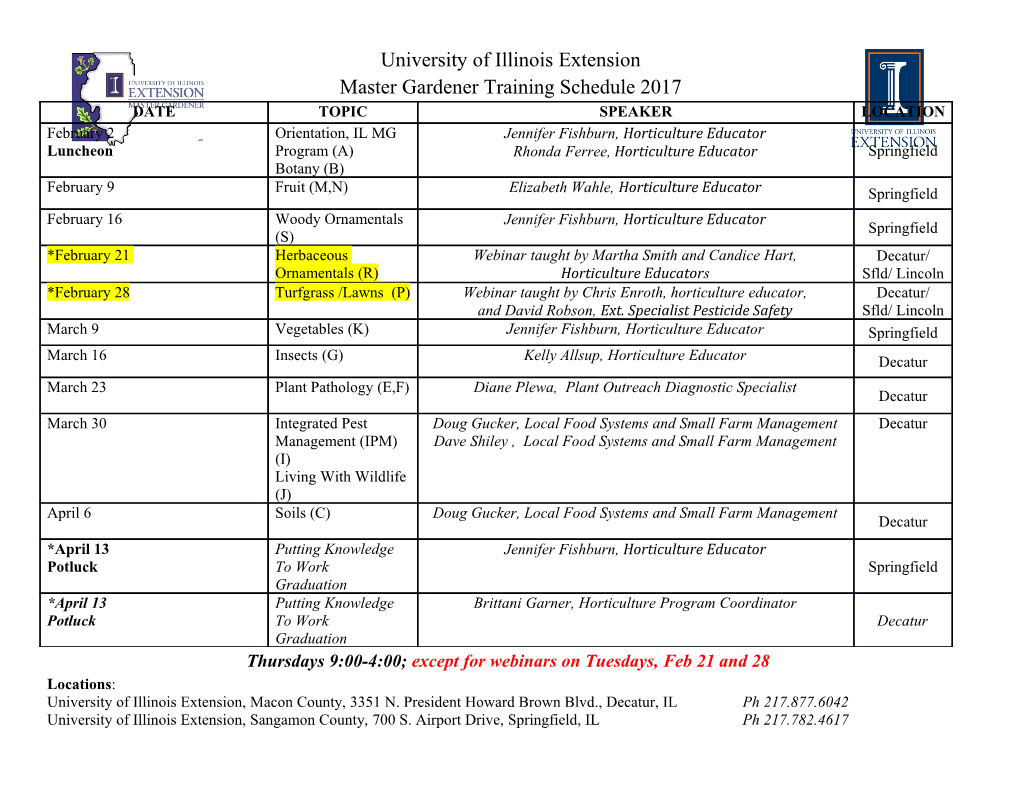
Proceedings of the 5th IASME / WSEAS International Conference on Fluid Mechanics and Aerodynamics, Athens, Greece, August 25-27, 2007 269 Hydraulic Model Test of the Bottom Outlet of Sivand Dam F. DANESHMAND, E. AZADI YAZDI and Y. BAZARGAN LARI Mechanical Engineering Department Shiraz University Namazi Square, Mollasadra Street, School of Engineering, 71345 IRAN [email protected] Abstract: - This paper presents the results of hydraulic test of bottom outlet of the Sivand Dam. The aims of the hydraulic model test are, gate discharge characteristics and gate loading. Results for different gate openings are also compared with calculated values obtained by a finite element method. Key-Words: - Hydraulic model test, Dam, Finite element method, Gate, Gate Discharge 1 Introduction provided for closing in the case of inspection or The Sivand Dam is located on the Sivand River in repair works at the downstream gate. The upstream Fars province near the Shiraz city in Iran. The dam gate will also be used for closing in case when the specifications are given in Table 1. downstream does not close. Operation of the bottom outlet system shall be possible up to a maximum head water level 1826.5 m with guaranteed Table 1- Dam Specifications 3 Type Earth fill discharge of 350 m /s. In all operating conditions, Height 57 m discharge of water downstream of the roller gate will Crest Length 600 m be free flow inside of the tunnel. Reservoir Storage 150 MCM The gates should be designed considering the influences of hydraulic conditions and cavitation and vibration in any part of the gates should be avoided. 1.1 Bottom Outlet Roller Gates So, the following aims will be included in the Two sets of fixed wheel roller gates will be provided hydraulic model test of the bottom outlet of the in the inlet of bottom outlet to facilitate evacuation Sivand Dam, of water through the bottom outlet system during • Gate discharge characteristics flood season. Some technical specifications and design data of the bottom outlet are given in Table 2. • Gate loading and dynamic response • Absence of detrimental vibrations Table 2. Technical Specifications and • The shape of water passages, which will not Design Data of Bottom Outlet include zones of low pressure having high cavitation Number of roller gates per set 2 potential (for stop log slot, if necessary) Clear height of opening 4.0 m The hydraulic model of the bottom outlet including Clear width of opening 4.0 m emergency and service gates are built to the Max water level 1826.5 m geometrical scale 1:20. Gate slot inclination (to horizontal) 60º In section II the similarity criteria and the model construction are explained. The discharge The bottom outlet system shall be normally used for characteristic results of the hydraulic test are evacuation of muddy water during flood period. presented in the third section of the paper. The next Furthermore, the system will be used in exceptional section contains the hydraulic force on the service cases in order to lower the water level in the and emergency gates evaluated in the hydraulic test. reservoir for inspection or some repair work that Results of cavitation analysis are explained in the may be required on the dam or spillway intake section IV. And finally there is conclusion in the last structure. The downstream gate shall operate as the section of the paper. service gate to evacuate water through bottom outlet system and operate at fully open position. The 2 Similarity Criteria and upstream gate shall operate as maintenance gate closing normally under no-flow condition and in Experimental Setup case of emergency under full-flow condition. It is The small-scale hydraulic model will reproduce the Proceedings of the 5th IASME / WSEAS International Conference on Fluid Mechanics and Aerodynamics, Athens, Greece, August 25-27, 2007 270 hydraulic phenomena of the prototype accurately, if The pressure of water measured in different points both geometric and dynamic similarity between the using conventional manometers, the plan of prototype and its model is obtained. manometers location is given in Fig. 2. The similarity of hydrodynamics is the similarity of The hydraulic tests are done at the openings 10%, the “dynamic loads”. Based on the governing 20%, 30%, 40%, 50%, 60%, 70%, 80%, 90% and differential equation of Navier Stockes, it is 100% of the service gate and fully open position of concluded that in order to ensure the similarity of the emergency gate at the maximum water level mean and fluctuation quantities, the Froude number 1826.5m and also at the normal water level 1813m. “Fr” and Reynolds number “Re”, and the roughness, and the boundary conditions of the model and 3 Discharge characteristics prototype should be similar [1]. A sharp-crested triangular weir and a rectangular However, it is impossible to ensure the similarity of weir, accompanying with a point gauge (for reading Froude number and Reynolds number the height of water on the weir) are used to measure simultaneously. In the engineering practice, the the model discharge. The prototype discharge for the models are usually scaled according to Froude service gate opening 10% to 100% and fully open similarity. For Froude similarity, the fine scale position of the emergency gate is shown in Fig.3. structures, which are produced by viscous dissipation, are not modeled. For high Reynolds number the energy dissipated by the fine scale of Discharge characteristics of the service gate turbulence (which is produced by viscous 400 350 dissipation) is much less than the total energy 300 production. Therefore, in high Reynolds number a 250 200 Froudian model may accurately model the 150 hydrodynamic loads, which are produced by large 100 50 Discharge (m3/sec) scale of turbulence [2],[3]. 0 In the present hydraulic test procedures, the model 0 102030405060708090100 for both emergency and service gates are constructed Se rvice Gate Ope ning (%) according to Froud similarity. Fig.3 Prototype discharge for service gate openings 2.1 Experimental Setup 10% to 100% The hydraulic model of the emergency and service The prototype discharge for the emergency gate gates are built to the geometrical scale 1:20. The opening 10% to 100% and fully open position of the Hydraulic model consists of the upstream and service gate is shown in Fig.4. downstream of the gates. The water supply is obtained from a pool with open top, and the model is directly connected to it. 4 Hydrodynamic Forces on Gates Water discharge is measured using a triangular weir Pressure of the water is measured at different and a rectangular weir at the downstream of the locations on the emergency and service gates using model. By reading the elevation of water, the flow manometers at different gate opening (Fig. 5). rate can be calculated [4]. The hydraulic model is made of plexi-glass so that it would ensure appropriate flow visualization. The hydraulic model of the test includes the entire water passage in both upstream and downstream of the gates (Fig. 1). Fig. 5 Manometers location on the service gate (downstream view) Fig. 1. Hydraulic model The hydrodynamic forces on service and emergency Proceedings of the 5th IASME / WSEAS International Conference on Fluid Mechanics and Aerodynamics, Athens, Greece, August 25-27, 2007 271 gates at different gate opening have been calculated are not located in the high velocity flow region up to with the aim of measured and the results are shown 60% gate opening, hence the cavitation index must in Figs. 6 and 7. be checked for gate openings higher than 60% (Fig. 10). 5 Cavitation A very useful index against which to correlate the occurrence, and the damage capability of cavitation, is the dimensionless parameter σo or cavitation number, namely: P P P ( i + a ) − v γ γ γ σ o = 2 (1) V i 2 g Fig. 9 Manometers locations in the Where, the pressure head at reference point, Pi the service gate slot atmospheric pressure head at reference point, Pv the vapor pressure head of water flow, Vi the average Cavitation Index velocity head at reference point. To estimate cavitation potential, the incipient 0.6 0.5 cavitation numbers σi of the critical points can be selected. Hydraulic pressures Pi were measured on 0.4 Mano. 17 0.3 the walls and velocities of the flowVi were Mano. 18 0.2 measured in the undisturbed flow at centerline of the Cavitation Index passage just downstream from the gate (all values 0.1 are refereed to the prototype). As it is known the 0 60 70 80 90 likelihood of cavitation, and the amount of damage, Gate Opening both increase as σ decreases. i The cavitation risk shall be checked for possible Fig. 10 Cavitation index for manometers 17 and 18 critical points. According to the hydraulic model in the service gate slot observations, it seems that the critical points for Although negative pressure is not appeared in the cavitation for different service gate openings may be slot of the service gate, but it can clearly be seen near the service gate slot. The prototype pressures at form the model test that some vortices are created in various gate opening for some manometers in the the service gate slot, especially in all service gate service gate slot is shown in Fig. 8. openings less than 70%. In fact, gate slots disrupt the Prototype Pressure boundary lines and create vortices and provide the separation of the flow at the slot boundaries, which causes low-pressure zones in the vicinity of the slot. 3 2.5 2 Mano. 17 6 Finite Element Analysis of 1.5 Mano. 18 1 the Problem Pressure (MWG) 0.5 During the last three decades, the finite element 0 method of analysis (FEM) has rapidly become a 0 102030405060708090 very popular technique for the solution of complex Service Gate Opening problems in engineering.
Details
-
File Typepdf
-
Upload Time-
-
Content LanguagesEnglish
-
Upload UserAnonymous/Not logged-in
-
File Pages7 Page
-
File Size-