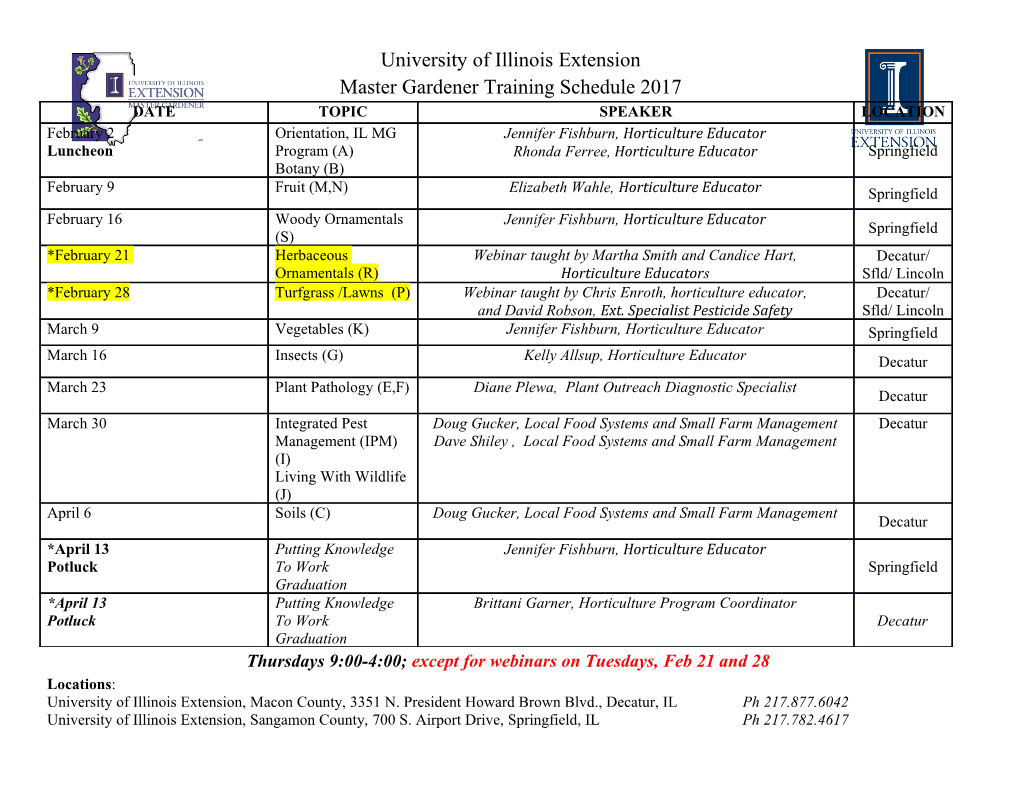
JOURNAL OF SPACECRAFT AND ROCKETS Engineering Notes Parametric Analysis of Single-Stage combination was already injected in LEO [3–6]. Nevertheless, previous studies considered on-orbit refueling of the upper stages of Earth-Departure-Stage the launch vehicle stack, including refueling of the EDS, as a In-Orbit Refueling technology of interest to enhance payload capacity [7]. On-orbit refueling options have also been considered as means to allow the use of smaller launch vehicles (LVs) with respect to heavy-lift and super- Alessandro A. Golkar∗ and Edward F. Crawley† heavy-lift LVs that are typically required in all-up architectures of Skolkovo Institute of Science and Technology, 143025, human space exploration missions beyond LEO [7]. Previous studies have also considered reference designs of high-specific-impulse Skolkovo, Russia electrical tugs for refueling chemical orbital transfer vehicles for DOI: 10.2514/1.A32718 geostationary transfers [8] and on-orbit refueling of satellites in orbit [9,10]. However, there has been little systematic effort in the literature in characterizing fundamental tradeoffs associated with on-orbit Nomenclature refueling from a systems architecture perspective. A = total mass stage gear ratio The goal of this Note is to fill this gap in the literature and explore possibilities associated with different on-orbit refueling strategies A1 = propellant mass stage gear ratio while evaluating associated performance benefits. This goal is Isp = stage specific impulse, s achieved through a first-order parametric analysis of on-orbit mEDS = total Earth-departure-stage stage mass (reference case is overlined), kg refueling of single-stage Earth departure stages. The analysis derives m = stage inert mass (reference case is overlined), kg nondimensional parameters for payload growth rates and packaging d ratios, which make the framework suitable to be used to any reference mp = Earth-departure-stage propellant mass (reference case is overlined), kg payload mass size of interest and allow consideration of a variety of classes of launch vehicles. mpl = cargo launch-vehicle payload mass (reference case is overlined), kg mp0 = Earth-departure-stage payload mass (reference case is overlined), kg II. Parametric Approach m tank = tanker launch vehicle propellant payload mass p This section describes the parametric approach that has been (reference case is overlined), kg developed for the analysis, documenting assumptions, and sizing mtot = cargo launch-vehicle total mass (reference case is processes followed for two different on-orbit refueling strategies overlined), kg considered in the study. The Note considers in-orbit refueling α = propellant fill ratio coefficient scenarios where a single-stage EDS is carried by a cargo LV to LEO β = payload growth rate and is later refueled by a tanker LV. The goal of the analysis is to Γ = packaging efficiency quantify the performance benefits associated with on-orbit refueling ΔV0 = design delta V (reference case is overlined), m∕s operations, as measured by payload capability growth for an EDS λ = tare overhead fraction operating from LEO, and the packaging efficiency associated, as μ = stage inert mass fraction measured by the ability of enabling refueling using a tanker LV of similar class of the cargo LV. The analysis is performed through a parametric model that compares a reference case to other scenarios where two different on-orbit refueling strategies are considered. I. Introduction N EARTH departure stage (EDS) is one of the required A. Reference Case A developments toward the establishment of a future launch The reference case consists of a fully fueled single-stage EDS infrastructure for human space exploration beyond low Earth orbit of mass m EDS delivered in LEO by a cargo LV. It is assumed that Downloaded by MASSACHUSETTS INST OF TECH on February 21, 2014 | http://arc.aiaa.org DOI: 10.2514/1.A32718 (LEO). Because orbital maneuvers required in human spaceflight the EDS and its payload mp0 have a nominal total mass equal to mpl, missions to the Moon and Mars imply demanding delta V budgets that is, compared to LEO missions, an in-orbit propulsion stage will likely be required to efficiently meet overall mission requirements in conjunc- mpl mEDS mp0 (1) tion with a new generation of man-rated transportation infrastructure ’ [1] such as NASA s Space Launch System [2]. Traditionally, concep- Once in LEO, the EDS accelerates the nominal payload m 0 for a “ ” p tual studies considered all-up launch architectures, where the EDS change in orbital velocity ΔV0. Using the rocket equation [11], the was launched fully fueled and ignited once the EDS and payload reference EDS mass can be calculated as Received 21 May 2013; revision received 18 August 2013; accepted for m EDS m 0 m m m 0 p p d p publication 1 September 2013; published online 20 February 2014. Copyright μ © 2013 by Alessandro Golkar and Edward Crawley. Published by the 1 A1 1 m 0 A · m 0 (2) American Institute of Aeronautics and Astronautics, Inc., with permission. 1 − μ p p Copies of this paper may be made for personal or internal use, on condition that the copier pay the $10.00 per-copy fee to the Copyright Clearance Center, Inc., 222 Rosewood Drive, Danvers, MA 01923; include the code 1533-6794/ 1 − μ 1 − R (3) 14 and $10.00 in correspondence with the CCC. A1 μ − 1 *Assistant Professor, Skolkovo Tech, 100 Novaya Ulitsa, Skolkovo, R Moscow Region 143025, Russian Federation. † President, Skolkovo Tech, 100 Novaya Ulitsa, Skolkovo, Moscow Region where R is the EDS gear ratio defined as a function of ΔV0 and stage 143025, Russian Federation. specific impulse Isp: AIAA Early Edition / 1 2 AIAA Early Edition / ENGINEERING NOTES Table 1 Survey of existing and proposed U.S. cryogenic upper The goal is to estimate the increased payload capacity on the cargo LV stages (public-domain data) achieved by means of on-orbit refueling, as measured by payload growth rate β: Name Gross mass, t Dry mass, t Dry mass fraction Isp,s Centaur B–X 19.1 2.4 0.11 470 m 0 m 0 1 β (7) Centaur C 15.6 2.0 0.11 425 p p Centaur C–X 19.1 2.4 0.11 450 Centaur D/E 16.3 2.6 0.14 444 Payload growth rate achieved is a function of the chosen refueling Centaur I 15.6 1.7 0.10 444 strategy. In both refueling strategies considered, a constraint is set so Centaur-2A 19.1 2.3 0.11 449 that all EDS configurations are such that the total mass of the EDS Centaur-3A 18.7 1.9 0.09 451 stage plus carried payload equals the total EDS mass plus payload Centaur-V1 22.8 2.0 0.08 451 mass of the reference case: Centaur-V2 23 2.2 0.09 451 Delta 4-2 24.2 2.8 0.10 462 mtot mEDS mp0 Delta 4H-2 30.7 3.5 0.10 462 —— —— Average 0.10 451 mtot mEDS mp0 mtot mtot → mEDS mp0 mEDS mp0 (8) The isomass constraint shown in Eq. (8) enables comparison of ΔV0 payload growth rates between different refueling strategies. The R exp (4) gIsp following sections describe those strategies and derive associated closed form expressions of payload growth rates. μ is the dry mass fraction of the EDS stage, which relates the stage dry C. Refueling Strategy 1: Transfer Some Fuel, No Payload mass m d and propellant mass m p as follows: The first refueling strategy being considered, named “transfer μ some fuel, no payload”, is illustrated in Fig. 1. This strategy involves μ (5) md md mp1 − μ mp launching a partially fueled EDS carrying the nominal reference case payload mp0. The EDS is then refueled in orbit by one or more tanker LVs. In this strategy, the limit case α 1 reproduces the EDS of the The reference case considered in this Note assumes Isp 451 s and reference case. As α is reduced, both the payload and the EDS grow in μ 0.10 as performance values for the analysis. These assumptions size as space is made available by propellant instead being delivered represent average performance values of cryogenic upper stages, as by tanker LVs. As a result, the limit case of α 0 is the case in which derived by a survey on public domain data of existing and proposed both the EDS and EDS payload are maximum. cryogenic upper stages (that are close analogs to Earth departure Payload growth rate is derived by applying the constraint described stages). The survey is shown in Table 1. in Eq. (8): 1 β − 1 − α (9) B. Refueling Scenarios Modeling Approach mtot Ampl mp In the refueling scenarios considered, the EDS initially carries Substituting terms using the parameterization shown in Table 1 leads α · m propellant, where m is propellant mass at full load, and α is p p to the following expression for β: the fill ratio coefficient (varying from 0 to 1). Therefore, tanker LVs carry a propellant mass of 1 − αmp as their payload. A tare λ β A − 1 (10) overhead fraction is added to account for refueling equipment − 1 − α (worst-case reference value considered λ 0.30), making the total A A1 payload propellant for tanker LVs equal to Packaging efficiency Γ is defined as the ratio between propellant mass to be delivered by the tanker LV (including tare overhead) and 1 − α 1 λ (6) mptank mp cargo LV payload mass: Downloaded by MASSACHUSETTS INST OF TECH on February 21, 2014 | http://arc.aiaa.org DOI: 10.2514/1.A32718 Fig. 1 Refueling strategy 1: transfer some fuel, no payload. AIAA Early Edition / ENGINEERING NOTES 3 mptank A Γ (11) B − 1 (13) mp0 A − 1 − 1 − αA1 Packaging efficiency Γ is measured as the ratio between propellant Section III will compare payload growth rate and packaging mass to be delivered by the tanker LV (including tare overhead) plus efficiency shown in Eqs.
Details
-
File Typepdf
-
Upload Time-
-
Content LanguagesEnglish
-
Upload UserAnonymous/Not logged-in
-
File Pages5 Page
-
File Size-