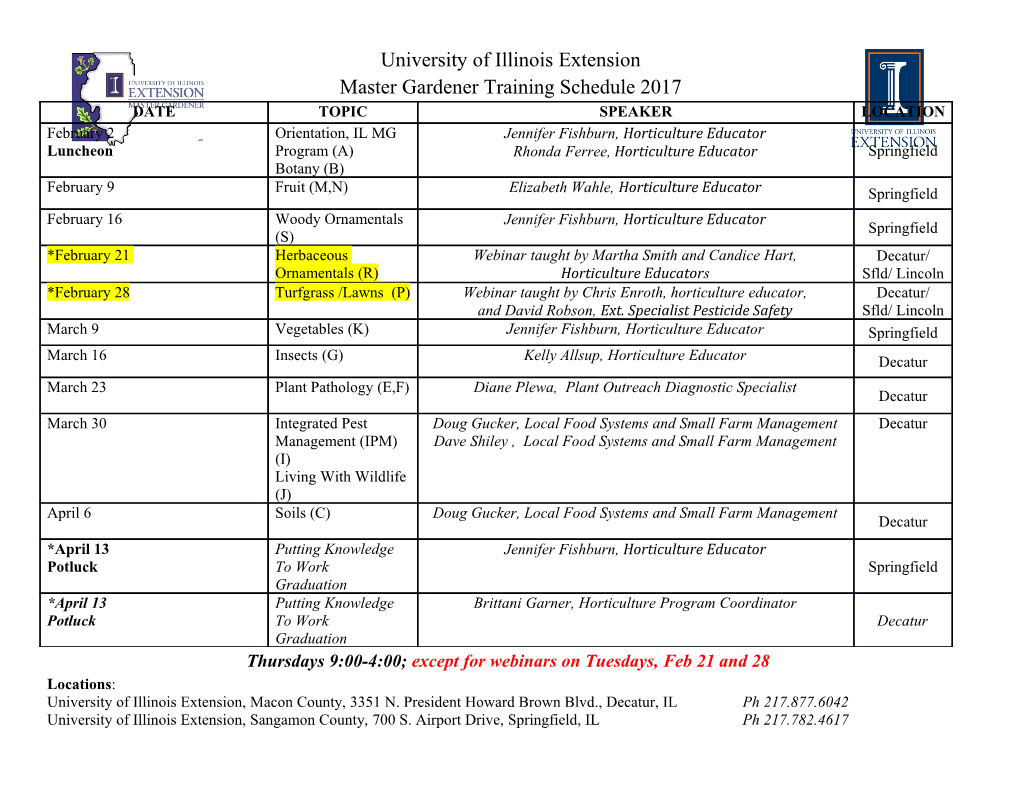
energies Article Core Structure and Electromagnetic Field Evaluation in WPT Systems for Charging Electric Vehicles Kamal Eldin Idris Elnail 1, Xueliang Huang 1,*, Chen Xiao 2, Linlin Tan 1 and Xu Haozhe 1 1 School of Electrical Engineering, Southeast University, No. 2 Sipailou, Nanjing 210096, China; [email protected] (K.E.I.E.); [email protected] (L.T.); [email protected] (X.H.) 2 Shanghai Aerospace Control Technology Institute, Shanghai 2100096, China; [email protected] * Correspondence: [email protected]; Tel.: +86-25-8379-2260 Received: 1 June 2018; Accepted: 28 June 2018; Published: 2 July 2018 Abstract: The electromagnetic field (EMF) in a wireless power transfer (WPT) system needs to couple inductively between the primary and the secondary coils through a large air gap, thus giving the system a loosely coupled characteristic. Therefore, magnetically permeable material must be employed to improve the coupling and reduce leakage magnetic flux. However, adding an iron core increases the weight and introduces core loss as a new factor. In this paper, a WPT system model using a lumped circuit model is introduced. Moreover, the relationship between the relative permeability and the coupling coefficient in addition to the core amount (core thickness) and core loss are discussed. Three cores structure named: pot, slotted, and shaped bars cores are investigated using finite element method (FEM) software. Inspired by the investigation results, a new core structure using optimum shaped bars is proposed, the EMF level for reducing core loss in high-power transfer systems and in order to mitigate the EMF exposure to humans is intensively evaluated. The proposed core succeeded in reducing EMF and core loss by about 44% and 30%, respectively. The FEM software and physical prototype were used to validate the proposed optimum core structure. Results showed that 3.5 kW power transferred through a 20 cm air gap with 96% system efficiency(coil–coil). Keywords: electric vehicle (EV); wireless power transfer (WPT); electromagnetic field (EMF); core structure; core loss 1. Introduction An electric vehicle (EV), which uses an electric motor for propulsion, replaces conventional vehicles that utilize the internal combustion engine (ICE). EVs outperform traditional vehicles in terms of high efficiency, less routine maintenance, and zero tailpipe emissions. However, the lack of reliable means of recharging EV batteries infrastructure has been a major issue in delaying their practical implementation. To address this problem, wireless power transfer (WPT) charging systems have been adopted for charging EVs either on-road [1] or in parking spaces [2]. Besides EV charging, WPT has been rapidly developed for powering many electronic devices such as medical implants and portable electronic devices such as cellular telephones, laptop computers, and toothbrushes [3]. WPT charging systems have many advantages: they are cordless, need less maintenance, and are safe even in rain conditions. Moreover, it is less prone to vandalism when compared to conductive charging systems [4]. However, WPT systems have some drawbacks; for example, when the air gap or coils are laterally misaligned, the system characteristics change significantly [5]. In addition, in WPT systems, the transformer architecture is different than its counterpart. In a conductive charging system, the transformer coils have a common metal core that creates a strong time-varying electromagnetic flux (EMF) linkage between the primary and the secondary coils. Thus, it leads to increases in the voltage induced in the secondary coil and reduces system losses. In WPT systems, the two coils are Energies 2018, 11, 1734; doi:10.3390/en11071734 www.mdpi.com/journal/energies Energies 2018, 11, 1734 2 of 17 normally separated by a relatively large air gap, so the time-varying EMF generated by the primary coil needs to be coupled inductively through the large air gap with the secondary coil, giving the WPT system loosely coupled characteristics. To improve the coupling when the air gap increases, magnetically permeable material must be used [6]. The pad structure and core material have significant effects on system performance and misalignment tolerance between transmitting (Tx) and receiving (Rx) coils. The charger pads must meet many requirements, such as a low weight, a low EMF, a high efficiency, and a high durability. Recently, various studies have concentrated on coils and core geometries to increase the coupling coefficient (k) and the quality factor (Q) and to reduce the leakage magnetic flux in WPT systems regardless of core loss and core weight [7,8]. However, there are some studies describing the use of the optimal core thickness with core and coil shape to enhance system performance and misalignment tolerance [9–11]. A comparison between Litz wire and copper foil shows that copper foil provides less uniform magnetic flux inside the ferrite core, which reduces core loss, while the Litz wire has low AC resistance and the coupling coefficient is slightly higher [12]. However, the study does not take into account the power transfer amount and the number of turns (in the case of Litz wire), which are critical factors in WPT pad design. In the same context, three types of coil shapes are investigated [13], including the helix coil, the planar spiral coil, and the square helix coil in four-coil WPT systems where all coils have the same area. The result showed that the planar spiral coil has the lowest efficiency compared to helical and square helix, coils. Moreover, the helical coil was reported to have widest band width and longest air gap among the three types. However, the helical coil is not suitable for EV charging pads as it will increase pad thickness. In the same context, a cylindrical ferrite core with a helical coil are used as a transmitter in [14] to improve system efficiency. However, this type of core increases the pad thickness and weight by using a large amount of core, therefore becoming unsuitable for EV charging. In [15], the optimum stepped core for transmitting Tx and receiving Rx dipole-coils was investigated. The air gap used in their study was very large (5 m), which rendered the power transferred and system efficiency insufficient. Moreover, the proposed core structure was unsuitable for EV charging systems. In [16–18], E-type, I-type, ultra-slim S-type, U-type, and W-type core structures were introduced and tested in a rail power supply for powering an on-line EV. Comparison between ferromagnetic sheet and copper sheet with the Tx coil was made in [19], revealing that use of a ferromagnetic sheet can increase the electromagnetic flux density generated by the Tx coil, whereas the use of a conductive sheet (copper sheet) can mitigate the electromagnetic flux density. A novel H-shaped core was proposed in [20] for a 1.5 kW WPT system to improve efficiency and increase misalignment tolerance. However, the core loss and EMF level evaluation were not addressed. In this paper, a WPT system model using a lumped circuit model is introduced. The relationship between the relative permeability (m) and coupling coefficient (k) and that between the core amount and core loss are shown and discussed. Three case studies using shaped bars, a pot core, and a slotted core, for circular coils, are investigated using finite element message (FEM) software ANSYS Maxwell.16 (Commercial software). An EMF was intensively evaluated with a view to reducing core loss in high-power transfer systems and mitigating human exposure to the EMF. Motivated by the investigation results obtained from these three cases, a new optimum core structure is proposed as a trade-off between core loss and core weight. The proposed core reduced core loss by about 33% as a result of reducing EMF by about 44%, while the weight increased by only 15% compared to that of the system using shaped bars as the core. As a result, the proposed core is highly efficient and has a small and comfortable weight. The EMF evaluation methodology in this paper is general and can be applied to such research areas as high frequency transformers [21] used in wind farms, to ensure whether or not the emission from such devices is compliant with allowed exposure limits. The simulation software (ANSYS Maxwell and MATLABnSIMULINK) and hardware prototyping are used to validate the proposed optimum core structure. The design was able to transfer 3.5 kW through a 20 cm air gap with 96% coil–coil efficiency. Energies 2018, 11, 1734 3 of 17 2. The WPT System for Charging EVs The inductive coupling power transfer (ICPT) system at resonance can transfer high power over several millimeters with high efficiency, but its efficiency decreases when the distance increases. Moreover, it is very sensitive to lateral and angular misalignment [22]. For EV charging purposes, the ICPT system consists of many stages as shown in Figure1. The charging station side works as follows: AC utility power is converted to DC using a rectifier with a power factor correction, and a high-frequency (HF) inverter is then used as a source for the transmitter coil and compensation capacitor. The AC current in the Tx coil generates an alternating magnetic flux. The on-board side works as follows: The receiver coil is coupled with an alternating magnetic flux generated by the transmitter. As a result, the current is induced by induction therein, and a rectifier is then used to convert the AC-induced current to DC to charge the battery [23]. AC/DC DC to HF Primary Converter Converter Compensator Vin Secondary AC/DC Battery Compensator Converter Pack Figure 1. Structure of the inductive power transfer system for electric vehicle (EV) charging. Figure2 shows the equivalent circuit model using lumped parameter model when using a series–series (SS) compensation topology [24]. I1 R1 C1 C2 R2 I2 RS M R L1 L2 L Vin Figure 2.
Details
-
File Typepdf
-
Upload Time-
-
Content LanguagesEnglish
-
Upload UserAnonymous/Not logged-in
-
File Pages17 Page
-
File Size-