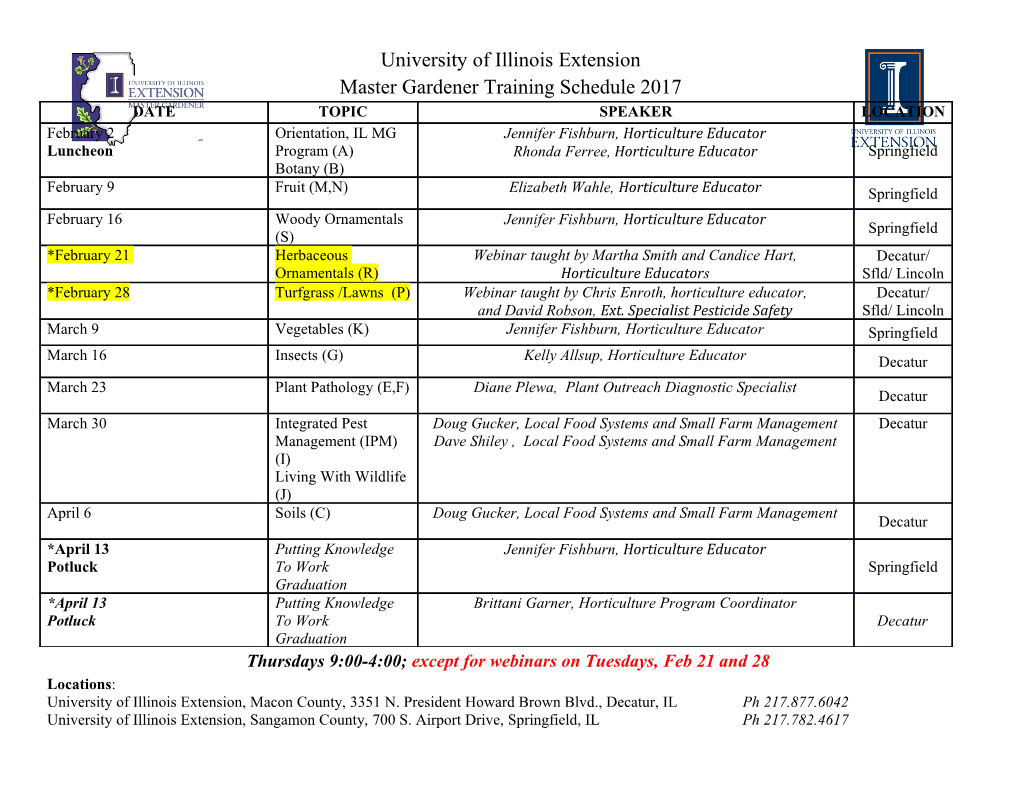
Iowa State University Capstones, Theses and Retrospective Theses and Dissertations Dissertations 1991 Modification of axial-flow compressor stall margin by variation of stationary blade setting angles John Paul Rukavina Iowa State University Follow this and additional works at: https://lib.dr.iastate.edu/rtd Part of the Mechanical Engineering Commons Recommended Citation Rukavina, John Paul, "Modification of axial-flow compressor stall margin by variation of stationary blade setting angles " (1991). Retrospective Theses and Dissertations. 9575. https://lib.dr.iastate.edu/rtd/9575 This Dissertation is brought to you for free and open access by the Iowa State University Capstones, Theses and Dissertations at Iowa State University Digital Repository. It has been accepted for inclusion in Retrospective Theses and Dissertations by an authorized administrator of Iowa State University Digital Repository. For more information, please contact [email protected]. INFORMATION TO USERS This manuscript has been reproduced from the microfilm master. UMI fihns the text directly from the original or copy submitted. Thus, some thesis and dissertation copies are in typewriter face, while others may be from aiiy type of computer printer. The quality of this reproduction is dependent upon the quality of the copy submitted. Broken or indistinct print, colored or poor quality illustrations and photographs, print bleedthrough, substandard margins, and improper alignment can adversely affect reproduction. In the unlikely event that the author did not send UMI a complete manuscript and there are missing pages, these will be noted. Also, if unauthorized copyright material bad to be removed, a note will indicate the deletion. Oversize materials (e.g., maps, drawings, charts) are reproduced by sectioning the original, beginning at the upper left-hand corner and continuing from left to right in equal sections with small overlaps. Each original is also photographed in one exposure and is included in reduced form at the back of the book. Photographs included in the original manuscript have been reproduced xerographically in this copy. Higher quality 6" x 9" black and white photographic prints are available for any photographs or illustrations appearing in this copy for an additional charge. Contact UMI directly to order. University Microfilms International A Bell & Howell Information Company 300 North! Zeeb Road. Ann Arbor, Ml 48106-1346 USA 313/761-4700 800/521-0600 Order Number 0126243 Modification of axial-flow compressor stall margin by variation of stationary blade setting angles Rukavina, John Paul, Ph.D. Iowa State University, 1991 UMI 300N.ZcebRd. Ann Aibor, MI 48106 NOTE TO USERS THE ORIGINAL DOCUMENT RECEIVED BY U.M.I. CONTAINED PAGES WITH POOR PRINT. PAGES WERE FILMED AS RECEIVED. THIS REPRODUCTION IS THE BEST AVAILABLE COPY. Modification of axiai-flow compressor stall margin by variation of stationary blade setting angles by John Paul Rukavina A Dissertation Submitted to the Graduate Faculty in Partial Fulfillment of the Requirements for the Degree of DOCTOR OF PHILOSOPHY Major: Mechanical Engineering Signature was redacted for privacy. I ' "'nk Signature was redacted for privacy. For the Major Department Signature was redacted for privacy. For the Graduate College Iowa State University Ames, Iowa 1991 ii TABLE OF CONTENTS NOMENCLATURE xiv ABSTRACT xviii 1. INTRODUCTION . 1 1.1 Stall 4 1.2 Surge 7 1.3 Avoiding Stall 8 2. RELATED ISOLATED AIRFOIL DYNAMIC STALL RESEARCH 12 3. PROOF OF CONCEPT IN LOW-SPEED COMPRESSORS . 24 3.1 Stationary Blade Setting Angle Variations 25 3.2 Two-Stage Axial-Flow Fan 29 3.2.1 Two-stage fan performance tests 31 3.2.2 Axial-flow fan results . 33 3.3 Three-Stage Axial-Flow Compressor 39 3.3.1 Three-stage compressor performance tests 43 3.3.2 Three-stage compressor results 45 3.4 Detailed Flow Measurements for Three-Stage Compressor 57 3.4.1 Velocity diagram calculations using detailed measurements . 67 iii 3.5 Low-Speed Compressor Conclusions 74 . 4. PRATT & WHITNEY COMPRESSOR 78 4.1 Pratt & Whitney Axial-Flow Compressor 78 4.1.1 D.C. drive motor and gearbox 83 4.1.2 Throttle 83 4.1.3 Surge detection and relief system 84 4.2 Pratt & Whitney Compressor Data Acquisition System 88 4.2.1 Pressure system 88 4.2.2 Temperature system 106 4.3 Pratt k Whitney Three-Stage Compressor Performance Tests .... 108 4.3.1 Inlet corrected mass flow 108 4.3.2 Compressor pressure rise ratio 113 4.3.3 Inlet corrected rotational speed 114 4.3.4 Detection of stall in the Pratt & Whitney compressor 114 5. ESTIMATION OF REDUCED FREQUENCY AND ROTOR INLET FLOW ANGLE VARIATION FOR PRATT & WHIT­ NEY COMPRESSOR 116 .5.1 Calculation of Reduced Frequency at Stall, K,taii, for the Pratt & Whitney Compressor 118 5.2 Rotor Inlet Flow Angle Analysis for Pratt & Whitney Three-Stage Compressor 126 6. PRATT & WHITNEY RESULTS AND DISCUSSIONS 135 6.1 Pratt and Whitney Baseline and Modified Compressor Performance . 135 6.1.1 Pratt & Whitney detailed flow measurements 138 iv 7. CONCLUSIONS 155 8. BIBLIOGRAPHY 160 9. ACKNOWLEDGEMENTS 162 10. APPENDIX A: DETAILED FLOW MEASUREMENTS FOR THREE-STAGE COMPRESSOR 163 11. APPENDIX B: VELOCITY DIAGRAM CALCULATIONS FROM DETAILED MEASUREMENT DATA 171 V LIST OF TABLES Table 3.1: Summary of two-stage fan builds and results 34 Table 3.2: Absolute flow angle ( °), baseline, $ = 0.353 63 Table 3.3: .Absolute flow angle ( °), baseline, $ = 0.420 63 Table 3.4: Absolute flow angle ( °) variation from baseline, +6° 2/rev, 0 = 0.353 65 Table 3.5: .Absolute flow angle ( °) variation from baseline, +6° 2/rev, = 0.420 65 Table 3.6: Absolute flow angle ( °) variation from baseline, -6° 2/rev, ^ = 0.353 66 Table 3.7: Absolute flow angle ( °) variation from baseline, —16° 2/rev, 0 = 0.353 66 Table 3.8: Detailed flow measurement data, baseline, ^ = 0.353 ..... 72 Table 3.9: Detailed flow measurement data, +6° 2/rev, $ = 0.353 ... 72 Table 3.10: Detailed flow measurement data, —6° 2/rev, ^ = 0.353 ... 73 Table 3.11: Detailed flow measurement data, —16° 2/rev, ^ = 0.353 ... 73 Table 4.1: Pratt & Whitney compressor design specifications 81 Table 4.2: Pratt k Whitney compressor blading specifications 82 Table 4.3: D.C. drive motor specifications 84 vi Table 4.4: Scanivalve pressure system power supplies 95 Table 4.5: Control pressure logic 95 Table 4.6: Calibration constants for the Z0C14 pressure sensor 105 Table 5.1: Stalling mass flowrates and axial velocity at stall for the base­ line compressor configuration 119 Table 5.2: Velocity diagram calculations for the baseline stalling condition 121 Table 5.3: Reduced frequency at stall, Kstalls for the Pratt & Whitney three-stage axial-flow compressor 122 Table 5.4: Amplitude of blade setting angle variation, and corre­ sponding rotor inlet flow angle variation for the low-speed, three-stage compressor 129 Table 5.5: Amplitude of blade setting angle variation, and corre­ sponding rotor inlet flow angle variation the Pratt & Whitney, three-stage compressor 133 Table 10.1: .Absolute flow angle ( °), baseline, = 0.353 164 Table 10.2: Absolute flow angle ( °), baseline, ^ = 0.420 164 Table 10.3: Absolute flow angle ( °), +6° 2/rev, $ = 0.353 165 Table 10.4: Absolute flow angle ( °) variation from baseline, -t-6° 2/rev, $ = 0.353 ; 165 Table 10.5: Absolute flow angle ( °), -f-6° 2/rev, $ = 0.420 166 Table 10.6: Absolute flow angle ( °) variation from baseline, +6° 2/rev, $ = 0.420 166 Table 10.7: Absolute flow angle ( °), -6° 2/rev, $ = 0.353 167 vii Table 10.8: Absolute flow angle ( °) variation from baseline, —6° 2/rev, <5 = 0.353 167 Table 10.9: Absolute flow angle ( °), -6° 2/rev, $ = 0.420 168 Table 10.10: Absolute flow angle ( °) variation from baseline, —6° 2/rev, $ = 0.420 168 Table 10.11: Absolute flow angle ( °), —16° 2/rev, $ = 0.420 169 Table 10.12: Absolute flow angle ( °) variation from baseline, —16° 2/rev, = 0.420 169 Table 10.13: Absolute flow angle ( °), —16° 2/rev, $ = 0.353 170 Table 10.14: .Absolute flow angle ( °) variation from baseline, —16° 2/rev, <i = 0.353 170 Table 11.1: Detailed flow measurement data, baseline, $ = 0.353 172 Table 11.2: Detailed flow measurement data, baseline, = 0.420 172 Table 11.3: Detailed flow measurement data, +6° 2/rev, $ = 0.353 . 173 Table 11.4: Detailed flow measurement data, +6° 2/rev, = 0.420 . 173 Table 11.5: Detailed flow measurement data, -6° 2/rev, 0 = 0.353 . 174 Table 11.6: Detailed flow measurement data, —6° 2/rev, $ = 0.420 . 174 Table 11.7: Detailed flov/ measurement data, -16° 2/rev, = 0.353 . 175 Table 11.8: Detailed flow measurement data, —16° 2/rev, = 0.420 . 175 viii LIST OF FIGURES Figure 1.1: Stall/surge boundary for a multistage compressor, Copen- haver [1] 2 Figure 1.2; Propagation of stall in a cascade [2] 5 Figure 1.3: Fully developed rotating stall cell [3] 6 Figure 2.1: Typical airfoil pitching about a midchord axis 15 Figure 2.2: Airfoil geometry and important angular quantities, McCroskey [5] 17 Figure 2.3: Experimental stall boundary according to McCroskey [5] . 18 Figure 2.4: Dynamic stall angle increase as a function of A', Halfman et al. [6] 20 Figure 3.1: Blade setting angle variations, (a) Sinusoidal, (b) Rectified Sine-wave, and (c) Asymmetric 26 Figure 3.2: Two-stage axial-flow fan apparatus 30 Figure 3.3: Blade-to-blade view of two-stage, axial-flow fan blade rows . 32 Figure 3.4: One-stage axial-flow fan results, A(/> = 5°, n = 3 cycles/rev, rotor speed = 2000 rpm 36 Figure 3.5: Two-stage axial-flow fan results, = 5°, n = 3 cycles/rev, rotor speed = 1600 rpm 37 ix Figure 3.6: Three-stage axial-flow
Details
-
File Typepdf
-
Upload Time-
-
Content LanguagesEnglish
-
Upload UserAnonymous/Not logged-in
-
File Pages200 Page
-
File Size-