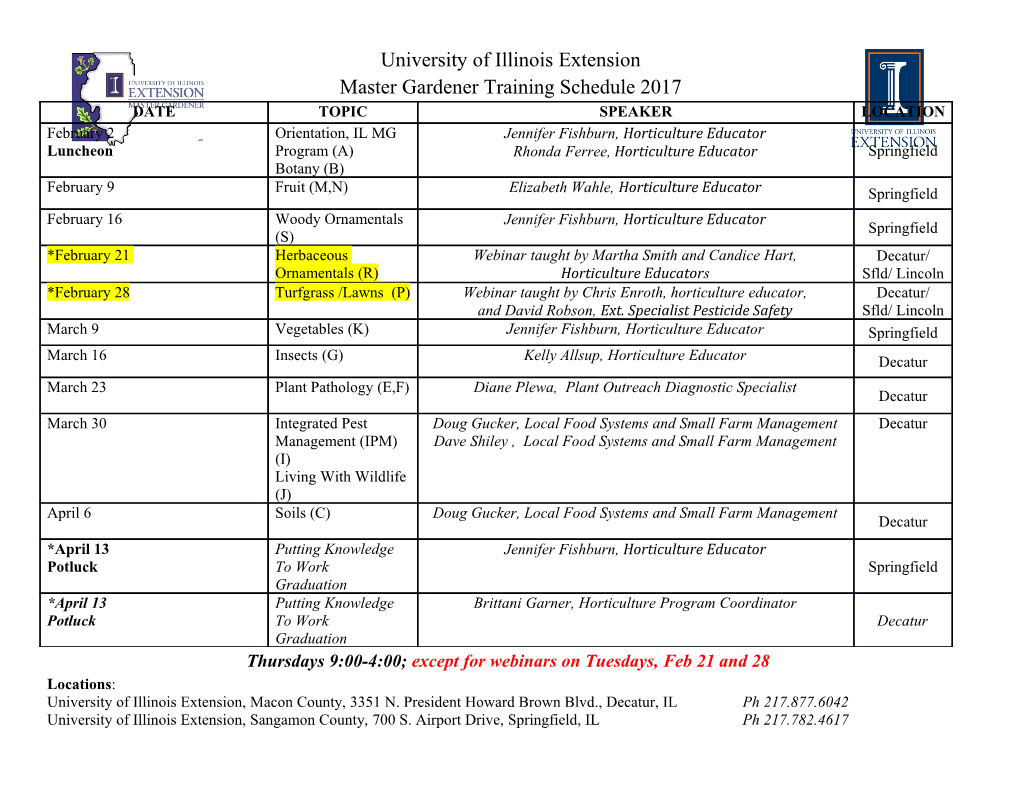
Freescale Semiconductor, Inc. White Paper Thermal Analysis of Semiconductor Systems Contents 1 Introduction ................................................................................................................................ 2 2 Definitions and Basic Principles ................................................................................................. 3 2.1 Definitions ............................................................................................................................ 3 2.2 Basic Principles ................................................................................................................... 3 2.3 Transient Thermal Response ............................................................................................... 5 2.4 Convection and Radiation ................................................................................................... 6 3 Differences between Electrical and Thermal Domains .............................................................. 8 4 Thermal Rating ........................................................................................................................... 9 4.1 Thermal Resistance Ratings ................................................................................................ 9 4.2 JEDEC Test Methods and Ratings .................................................................................... 10 4.3 Thermally Enhanced Circuit Boards .................................................................................. 12 4.4 Transient Thermal Response Ratings ................................................................................ 15 5 Ramifications of High Operating Temperature ......................................................................... 18 6 Thermal Circuits ....................................................................................................................... 20 7 Thermal Modeling Software ..................................................................................................... 24 7.1 Uses of Thermal Modeling Software ................................................................................. 24 7.2 Thermal Modeling Software Options ................................................................................. 26 8 Empirical Analysis Techniques ................................................................................................. 28 9 Optimizing the Thermal Environment ....................................................................................... 30 10 Appendices............................................................................................................................. 32 10.1 Appendix A—List of JESD51 Series Publications ........................................................... 32 10.2 Appendix B—Thermal Properties of Common Semiconductor Packaging Materials .... 33 11 References.............................................................................................................................. 34 1 Introduction Designing a cost competitive power electronics system requires careful This white paper first presents the basic principles of thermal systems consideration of the thermal domain as well as the electrical domain. and then describes some of the techniques and tools needed to Over designing the system adds unnecessary cost and weight; under complete such an analysis. Power devices and low lead count designing the system may lead to overheating and even system failure. packages are the primary focus, but the concepts herein are general Finding an optimized solution requires a good understanding of how to and can be applied to lower power components and higher lead count predict the operating temperatures of the system’s power components devices such as microcontrollers. and how the heat generated by those components affects neighboring devices, such as capacitors and microcontrollers. No single thermal analysis tool or technique works best in all situations. Good thermal assessments require a combination of analytical calculations using thermal specifications, empirical analysis and thermal modeling. The art of thermal analysis involves using all available tools to support each other and validate their conclusions. 2 Definitions and Basic Principles 2.1. Definitions H Heat flux, rate of heat flow across a unit area (J·m- A good way to begin a study of a domain is to familiarize oneself 2·s-1) with its definitions, nomenclature and notations. The terms used for R Thermal resistance between reference points “A” and thermal analysis vary somewhat throughout the industry. Some of QAB “B”, or R the most commonly used thermal definitions and notations are: THAB R Junction to moving air ambient thermal resistance T Temperature at reference point “A” QJMA A R Junction to case thermal resistance of a packaged T Junction temperature, often assumed to be QJC J component from the surface of its silicon to its constant across the die surface thermal tab, or RTHJC T or T Package temperature at the interface between the C Case R Junction to ambient thermal resistance, or R package and its heatsink; should be the hottest QJA THJA C Thermal capacitance between reference points “A” spot on the package surface and in the dominant QAB and “B”, or C thermal path THAB ºC or K Degrees Celsius or degrees Kelvin ΔTAB Temperature difference between reference points Z Transient thermal impedance between reference “A” and “B”, QAB points “A” and “B”, or Z q Heat transfer per unit time (Watts) THAB PD Power dissipation, source of heat flux (Watts) The term “Junction Temperature” The term junction temperature became commonplace in the early Most of the die’s thickness is to provide mechanical support for the days of semiconductor thermal analysis when bipolar transistors and very thin layer of active components on its surface. For most thermal rectifiers were the prominent power technologies. Presently the term is analysis purposes, the electrical components on the die reside at the reused for all power devices, including gate isolated devices like power chip’s surface. Except for pulse widths in the range of hundreds of MOSFETs and IGBTs. microseconds or less, it is safe to assume that the power is generated at the die’s surface. Using the concept “junction temperature” assumes that the die’s temperature is uniform across its top surface. This simplification ignores the fact that x-axis and y-axis thermal gradients always exist and can be large during high power conditions or when a single die has multiple heat sources. Analyzing gradients at the die level almost always requires modeling tools or very special empirical techniques. Freescale Semiconductor, Inc. Thermal Analysis of Semiconductor Systems 3 2.2. Basic Principles The across variable can be thought of as the variable that forces The basic principles of thermal analysis are similar to those in the the flow of current or heat. In each domain the forcing function is a electrical domain. Understanding one domain simplifies the task difference in potential; in one domain it’s temperature and in the other of becoming proficient in the other. This is especially clear when it’s voltage. we consider thermal conduction. The two other thermal transport Both systems have a resistance that impedes the flow of the through mechanisms are discussed later. variable. Each domain has a “through” and an “across” variable, as shown in Given the duality of the two systems, it is no surprise that the Figure 1 and Table 1. The through variable can be thought of as the fundamental equations of the domains are similar. This is illustrated parameter that flows from one reference point to another. Current is most clearly when we see that each system has an “Ohm’s Law”, as is the through variable for the electrical domain and power is the through shown in Table 1. variable in the thermal domain. Figure 1—Fundamental Relationships in the Electrical and Thermal Domains 4 Thermal Analysis of Semiconductor Systems Freescale Semiconductor, Inc. Table 1—Basic Relationships in the Electrical and Thermal Domains Electrical Domain Thermal Domain Variable Symbol Units Variable Symbol Units Through Variable Current I Amperes or Coulombs/s Power or Heat Flux PD Watts or Joules/s Across Variable Voltage V Volts Temperature T ºC or K Electrical Resistance R Ohms Thermal Resistance R ºC/W or K/W Resistance QAB Electrical Capacitance C Farads or Coulombs/V Thermal Capacitance C Joules/ºC Capacitance Q ΔT = T – T = P * R “Ohm’s Law” ΔV = V – V = I * R AB A B D QAB AB A B AB (derived from Fourier’s Law) From the relationships above, Thermal time constant is equal to the thermal R-C product, that is: ΔT = (T – T ) = P R = R C (Eq. 2) JA J A D QJA tQ Q Q we can easily derive the often used equation for estimating junction Thermal capacitance is a function of the temperature rise associated with temperature: a given quantity of applied energy. The equation for thermal capacitance T = T + (P R ) (Eq. 1) J A D QJA is: C = q t/ΔT (Eq. 3) For example, let’s assume that: Q R = 30ºC/W QJA where: P = 2.0W D q = heat transfer per second (J/s) T = 75ºC A t = time (s) Then, by substitution: ΔT = the temperature increase (ºC) T = T + (P R ) J A D QJA TJ = 75ºC + (2.0W * 30ºC/W) Thermal capacitance is also a function of mechanical properties. It is TJ = 75ºC + 60ºC the product of a material’s specific heat, density, and volume: T = 135ºC C = c d V (Eq. 4) J Q A cautionary note is in order here. The thermal conductivities of some
Details
-
File Typepdf
-
Upload Time-
-
Content LanguagesEnglish
-
Upload UserAnonymous/Not logged-in
-
File Pages24 Page
-
File Size-