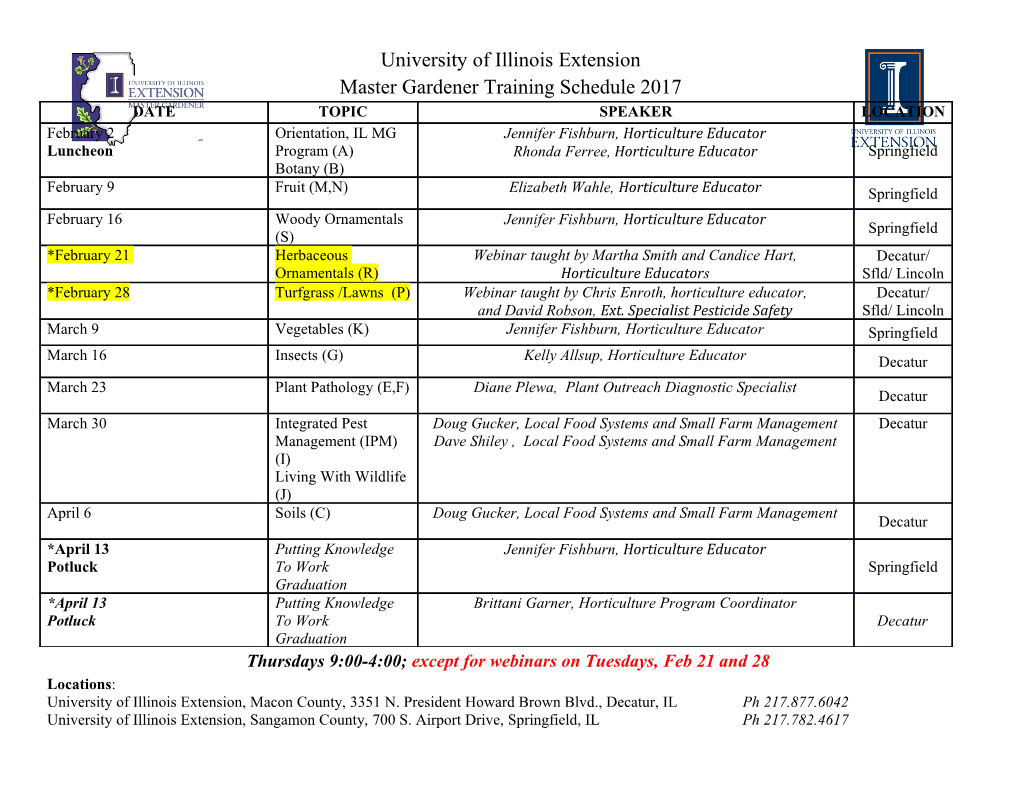
Copyright Surface Design Journal®. Not to be reprinted. All rights reserved. Technology&Design A Creative Alliance in Arashi Shibori by Anne Selby From the moment of discovering silk painting in the 1990s, I have been passionate about color on silk—particularly the intensity and shading that happens when colors interact. When I was given the book Shibori: Creating Color and Texture on Silk (Watson-Guptil, 2002) by Karren Brito, I was hooked and fascinated. Busy with a private psychotherapy practice, teenage children, and elderly parents, I did no more than regularly look at it and dream of one day being able to concentrate on textiles. Joining a master’s program in Textile Design at Bath Spa University in England began my journey into Arashi shibori. My textile focus at that time was screen-printing on devoré fabrics. However, shibori pleating quickly became my chosen research topic, beginning a thrilling and challenging journey into the world of engi- neering, textile manufacturing, and international travel that still continues. Arashi shibori involves placing fabric on a pipe, over-binding it firmly with string at regular intervals, and then compressing the bound fabric. The fabric pushes up to form pleats between each revolution of string. These pleats can be discharged and dyed to introduce contrasting colors along their peaks. Originating in Japan in the 19th Century as an efficient method for creating patterns for kimonos, western shibori artists further developed the technique on silk, retaining the pleats through steam-fixing. Arashi practitioners are resourceful in finding ways to facilitate the arduous process of wrapping and compressing. To make pleated pieces commercially viable, I needed to access some mechanization of the turning/wrapping process to avoid repetitive strain and increase efficien- cy. So began the development of the Compleat™ Arashi Shibori Wrapping Machine, which I developed over a two-year process with the aid of a gen- erous innovation award from Bath Spa University. To find a local engineer with the right skills, I searched through the national professional body of engineering firms. Eventually, Amag in nearby Bristol built two Compleat prototypes over the course of 15 months. My science background in chemistry needed a dusting-off in order to communicate with them during the design process. Imagine try- ing to quantify the strength used in the wrapping process. Defining the torque required to turn the pipe would, in turn, clarify the specification for the motor needed for the wrapping process. We resorted to pulling on fishing scales to find the answer, and I recall the engineers’ expressions when I tried to describe the function of an Arashi wrapping machine—“It does what?!” Clearly, I was working at the interface between two very dif- ferent worlds. Unfortunately, Amag went into receivership in 2009. I was left with a half-finished project, powder-coated and looking smart, but still RIGHT: ANNE SELBY Peacock Fibonacci Wrap Silk, 2013. Detail LEFT. Photos: Patrick Anderson. All works are made with Anne Selby’s Compleat™ Arashi Shibori Wrapping Machine. 20 Surface Design Journal Spring2013 21 22 Surface Design Journal ABOVE: ANNE SELBY (center) reviewing the quality of scarves with the team in the Sri Lanka studio, 2011. RIGHT: Fine wrapping of a classic Arashi scarf on Anne Selby’s Compleat machine, 2011. LEFT INSET: ANNE SELBY Concertina Scarf 8 layers of silk and silk organza, 2010. Photo: Nadine Elhage. LEFT BACKGROUND: ANNE SELBY Concertina Collar Detail, 10 layers of silk and silk organza, 2010. with significant unresolved technical difficulties the peaks. Once achieved, the effects are extraor- around the steaming process. Searching for a dinary and the scarves stand out for their fine manufacturer, I took this third prototype to a pleating. major textile equipment show in Germany— In automating any craft activity, there is where it won first prize for innovation. While a need to balance the contribution of the mecha- there, I met a textile engineering company that nized process with the hand of the maker. If the was keen to collaborate with me. product is too regular, the handmade feel of the Amag had been an engineering firm that piece can be lost. Certainly, these Arashi scarves built simple metal structures with some electrical are more regular in their pleating than any I have function. The new engineers worked only with seen. But I believe that Compleat, in the hands of textiles, where incorporating a steam function a highly skilled practitioner, has contributed to was quite normal and innovation was highly val- the creation of beautiful scarves that are simply ued. They wanted to use their factory in Sri Lanka not possible otherwise. to set up a production studio using Compleat to The scope of my own Arashi shibori make pleated wedding saris and headscarves for practice is extended by Compleat in several ways. the Muslim market and, ultimately, permanently My hands are free to concentrate on the spacing pleated silk for the lingerie market! I trained of my wrapping and the tightness of the thread. I seven staff in the key processes, beginning with a can let go of the thread without losing its consid- simple classic Arashi scarf, which has become a erable tension because it is held tight in a cleat. regular best-seller at the British Museum in To compress the pleats, I place a gripper on the London. wrapped work that completely surrounds the The studio in Sri Lanka posed many chal- pipe in a way that my hands cannot. This method lenges. The design requires wrapping on the ensures an even pressure and sharp results. diagonal; with high humidity, the silk was distort- Nevertheless, the compression of the fabric ing and twisting unless the spaces between each remains a very physical process in which the final wrap of string were reduced to almost .5 cm. This results depend entirely on operator skill. adaptation created tiny shallow pleats, but Arashi shibori usually involves folding increased the challenge of changing the color on the material to be pleated into several layers to fit Spring2013 23 24 the chosen pipe. Using Compleat, I am able to take the folding a step further to produce accessories that become three-dimensional. In my Fibonacci range of boas, for example, I am sometimes pleating 24 layers of silk. When the piece is finished and opened up, it transforms, gaining body and sculptural form as the layers separate. Recent work includes a Concertina Ruffle that uses three layers of different organ- za folded over and pleated as six layers on the pipe. This is the stiffest combination of silks that I have used so far and the strongest in retaining its pleats and form upon wearing. Additionally, wiring the edges gives a sensual and floral finish to the multiple layers, and the ruffle’s movement makes it sensational to wear. Many shibori artists have experiment- ed with pleating leather with fascinating results—as seen in the exhibition Animal Fibres: Art informs Shibori at the 8th International Shibori Symposium in Hong Kong in 2011. In collaboration with Northampton University’s European Centre of Excellence for Leather in the UK, I am researching the various character- istics of each type of skin. Tiny variations can ABOVE: ANNE SELBY Fibonacci Stole 2010. BELOW: ANNE SELBY result in significantly different outcomes in the Fibonacci Boa 4 layers of silk, 2010. Photo: Nadine Elhage. pleating process. Tanning method, thickness of skin, even the diet of the animal before skinning LEFT INSET: ANNE SELBY Concertina Ruffle (Magenta/Green) are all factors that have to be controlled if a reli- 6 layers of silk and metallic organza, wired edges, 2012. able pleated leather product is to be developed. Photo: Patrick Anderson. LEFT BACKGROUND: ANNE SELBY Concertina Ruffle (Black/Red) Detail, 6 layers of silk and metallic Having pleated cow hide and a finished organza, wired edges, 2012. scarf in pig-split suede, I found that the most challenging project has been the double pleating of Arashi shibori just wanting to push the bound- of goat skin. This was pleated first one way, then aries of the technique for myself and create new again at 90 degrees to the original pleats. The and beautiful objects. Somehow, en route, I have lightweight and supple skin transformed into a found myself running a business exporting rigid three-dimensional piece that was well shibori pleating equipment and silk accessories received at a recent international leather show in worldwide. But when I get to the studio and turn Hong Kong. on Compleat, its quiet hum settles me. Using its Textile design and fashion students with strength, I can quickly get back to the excitement access to Compleat have experimented with I always feel as I begin to wrap and pleat. many other materials, including burlap. A product range of multi- Anne Selby will be a featured speaker during layered pleated paper lamp- in•ter•face, the 17th International Surface Design shades was exhibited in a recent Association Conference in San Antonio, TX (June graduate degree show at Bath 6–9, 2013). To read the brochure and register online, Spa University, and leather pleat- visit surfacedesign.org/2013conference. ing is being explored in the Fashion Department of —Anne Selby is an award-winning shibori artist (and Northampton University. These SDA member) who specializes in pleating multi-lay- are just a few examples where the ered silk. Based in the UK with a studio in Sri Lanka, she use of the technology of has developed a range of equipment for Arashi work, Compleat has opened up creative which includes the DVD Arashi Shibori: Pleating on possibilities and new directions. Silk and the Compleat™ Arashi Shibori Wrapping I began my exploration Machine.
Details
-
File Typepdf
-
Upload Time-
-
Content LanguagesEnglish
-
Upload UserAnonymous/Not logged-in
-
File Pages6 Page
-
File Size-