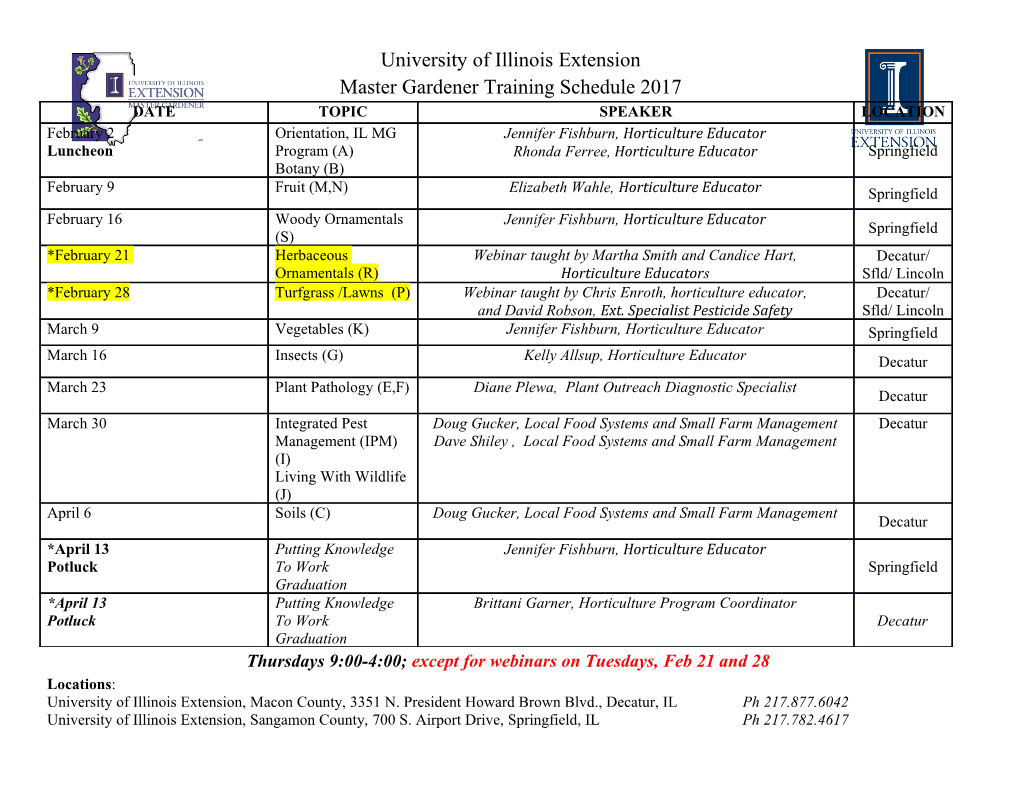
polymers Review Application of Polymer Membranes for a Purification of Fuel Oxygenated Additive. Methanol/Methyl Tert-butyl Ether (MTBE) Separation via Pervaporation: A Comprehensive Review Alexandra Pulyalina * , Valeriia Rostovtseva, Ilya Faykov and Alexander Toikka Institute of Chemistry, Saint Petersburg State University, Universitetskiy pr. 26, 198504 Saint Petersburg, Russia; [email protected] (V.R.); [email protected] (I.F.); [email protected] (A.T.) * Correspondence: [email protected]; Tel.: +7-812-428-4805 Received: 16 August 2020; Accepted: 24 September 2020; Published: 27 September 2020 Abstract: Methyl Tert-butyl Ether (MTBE) remains the most popular fuel additive to improve fuel performance and reduce the emission of hazardous components. The most common method of MTBE production is a catalytic synthesis with a great excess of methanol to improve the reaction yield. The problems of obtaining pure MTBE from the final product have determined the search for new techniques; primarily membrane methods. Pervaporation as an optimal membrane process for highly selective separation of organic mixtures is of particular interest. This review is focused on analysis of the research works on the various polymer membranes and their efficiency for the separation of the azeotropic methanol/MTBE mixture. Currently the most popular materials with optimal transport properties are poly(vinyl alcohol), cellulose acetate and polyheteroarylenes. Mixed matrix membranes (MMM) are highly effective as well as they show overall operational stability. Keywords: polymer membrane; mixed matrix membranes; pervaporation; MTBE; azeotropic mixture; fuel additive 1. Introduction The growing interest in the development of highly environmentally friendly transport fuels, and in particular, motor fuel, has led to a number of problems associated with the development of resource and energy-saving technologies used in their production. Despite the search and the proposed options for alternative fuels, the focus in coming years will be on fuel based on hydrocarbons, i.e., gasolines. It is well known that one of the most important negative factors in the use of gasoline, along with the inevitable combustion products (carbon dioxide and carbon monoxide), is environmental pollution with octane additives that improve fuel performance, but which are dangerous in terms of their impact on human health. A significant step in this regard was associated with the replacement of cheap lead additives (tetraethyl lead and its analogues) with safer compounds. It should be noted that, at present, the use of gasolines containing tetraethyl lead is prohibited in a number of countries [1]. Ethers are currently used as some of the most effective additives for the production of more environmentally friendly high-octane fuels. These include methyl tert-butyl ether (MTBE), ethyl tert-butyl ether (ETBE), tert-amyl methyl ether (TAME) and others. Other compounds such as ethanol and isooctane are also used for this purpose. Among the alternatives of non-lead additives, MTBE remains the most popular and usable one in the industry despite the well-known discussions related to its low biodegradability (in comparison with ETBE) and other negative characteristics (see, e.g., [2]). Polymers 2020, 12, 2218; doi:10.3390/polym12102218 www.mdpi.com/journal/polymers PolymersPolymers2020 2020, 12, 1,2 2218, x FOR PEER REVIEW 22 of of 22 22 Due to its chemical composition and high oxygen content, MTBE greatly affects detonation propertiesDue to and its chemicalmakes it possible composition to reduce and highgasoline oxygen consumption content, MTBEin combination greatly awithffects a detonationmodern fuel propertiessupply sy andstem makes of combustion it possible chamber. to reduce The gasoline most common consumption method in combination of MTBE producing with a modern is a catalytic fuel supplysynthesis, system which of combustion implies the chamber. use of isobutylene The most commonand methanol method as of the MTBE main producing precursors. is aIn catalytic order to synthesis,obtain the which maximum implies yield the useof the of isobutylenereaction product, and methanol an excess as of the methanol main precursors. is often used. In order A large to obtainamount the of maximum alcohol (about yield 20 of wt the.% reaction) is therefore product, present an in excess the final of methanol product, the is often release used. of which A large into amountthe atmosphere of alcohol harms (about both 20 wt.%)environment is therefore and presenthuman health. in thefinal Table product, 1 lists some the release physical of properties which into of thethe atmosphere studied liquids. harms both environment and human health. Table1 lists some physical properties of the studied liquids. Table 1. Physical properties of methanol and methyl tert-butyl ether (MTBE) [3]. Table 1. Physical properties of methanol and methyl tert-butyl ether (MTBE) [3]. Dynamic Liquid Mol. Liquid Mol. Molar Volume, Density, Tboiling, °C ViscosityDynamic, mPa∙s LiquidWeight Mol., g/mol LiquidWeight Mol., g/molMolar Volume,cm3/mol Density,g/cm3 T , C Viscosity,(20 °C) mPa s Weight, g/mol Weight, g/mol cm3/mol g/cm3 boiling ◦ · Methanol 32.04 40.5 0.792 64.7 (200.59◦C) MethanolMTBE 32.0488.15 40.5119.0 0.7920.740 64.755.2 0.590.35 MTBE 88.15 119.0 0.740 55.2 0.35 Traditional methods of this mixture separation are primarily associated with the use of reactive andTraditional azeotropic methodsdistillation of this[4–6]. mixture One of separationthe known are problems primarily is caused associated by an with azeotrope the use formation of reactive in andthe azeotropic MTBE-methanol distillation binary [4– 6system:]. One ofaccordin the knowng to problemsvarious authors, is caused it contains by an azeotrope from 80 formation to 70 mol. in % theMTBE MTBE-methanol in the temperature binary and system: pressure according range toof various298.15–324.3 authors, K and it contains 36.24–100.50 from 80kPa, to respectively 70 mol. % MTBE[7–9]. in The the temperaturevapor–liquid and equilibrium pressure range diagram of 298.15–324.3 for 293.15 K andK is 36.24–100.50 presented kPa,in Figure respectively 1. It [shows7–9]. Theequilibrium vapor–liquid vapor equilibrium–liquid compositions diagram for of 293.15the methanol K is presented-MTBE system in Figure at the1. Itgiven shows temperature equilibrium and vapor–liquidvariable pressure. compositions The intersection of the methanol-MTBE point of vapor system–liquid at equilibrium the given temperature curve and anddiagonal variable line pressure.corresponds The intersectionto the azeotropic point point of vapor–liquid of this system equilibrium at given conditions. curve and Modern diagonal methods line corresponds of distillation to themake azeotropic it possible point to of solve this systemthe problem at given of separating conditions. complex Modern mixtures. methods of However, distillation in makesome itcases, possible their toapplication solve the problem is associated of separating with additional complex problems mixtures. of energy However,- and in resource some cases,-saving their [10]. application In particular, is associatedwhen using with azeotropic additional distill problemsation, additional of energy- tasks and arise resource-saving of purifying [ 10the]. product In particular, from the when separating using azeotropicagent, and distillation, other technological additional challenges tasks arise also of occur. purifying the product from the separating agent, and other technological challenges also occur. 100 80 60 40 Methanol in vapour, wt% in vapour, Methanol 20 0 0 20 40 60 80 100 Methanol in liquid, wt% Figure 1. Vapor–liquid equilibrium curve for the MTBE-methanol system at 293.15 K [11]. Figure 1. Vapor–liquid equilibrium curve for the MTBE-methanol system at 293.15 K [11]. In the industry, methanol impurities have been recently removed by mixing the final product with waterIn the and industry, then extracting methanol MTBE.impurities The have remaining been recently aqueous removed methanol by solution mixing isthe subsequently final product distilledwith water to recover and then and recycleextracting alcohol MTBE. [12]. The However, remaining this processaqueous is methanol expensive solution and energy-consuming, is subsequently anddistilled also leads to recover to the loss and of targetrecycle components. alcohol [12]. However, this process is expensive and energy- consuming, and also leads to the loss of target components. The problems of obtaining pure MTBE from the final product have determined the search for new techniques, primarily membrane methods. Pervaporation as an optimal membrane process for Polymers 2020, 12, 2218 3 of 22 Polymers 2020, 12, x FOR PEER REVIEW 3 of 22 The problems of obtaining pure MTBE from the final product have determined the search for newhighly techniques, selective primarilyseparation membrane of organic methods. mixtures Pervaporation is of particular as an interest. optimal The membrane scheme process of the forpervaporation highly selective separation separation mechanism of organic is shown mixtures in Figure is of 2. particular The solution interest.–diffusion The model scheme is ofwidely the pervaporationused to describe separation mass transfer mechanism in the case is shown of dense in polyme Figure2r. membranes The solution–di for pervaporation.ffusion model According is widely usedto this to mechanism, describe mass the transfer pervaporation in the case process of dense includes polymer three membranes successive
Details
-
File Typepdf
-
Upload Time-
-
Content LanguagesEnglish
-
Upload UserAnonymous/Not logged-in
-
File Pages22 Page
-
File Size-