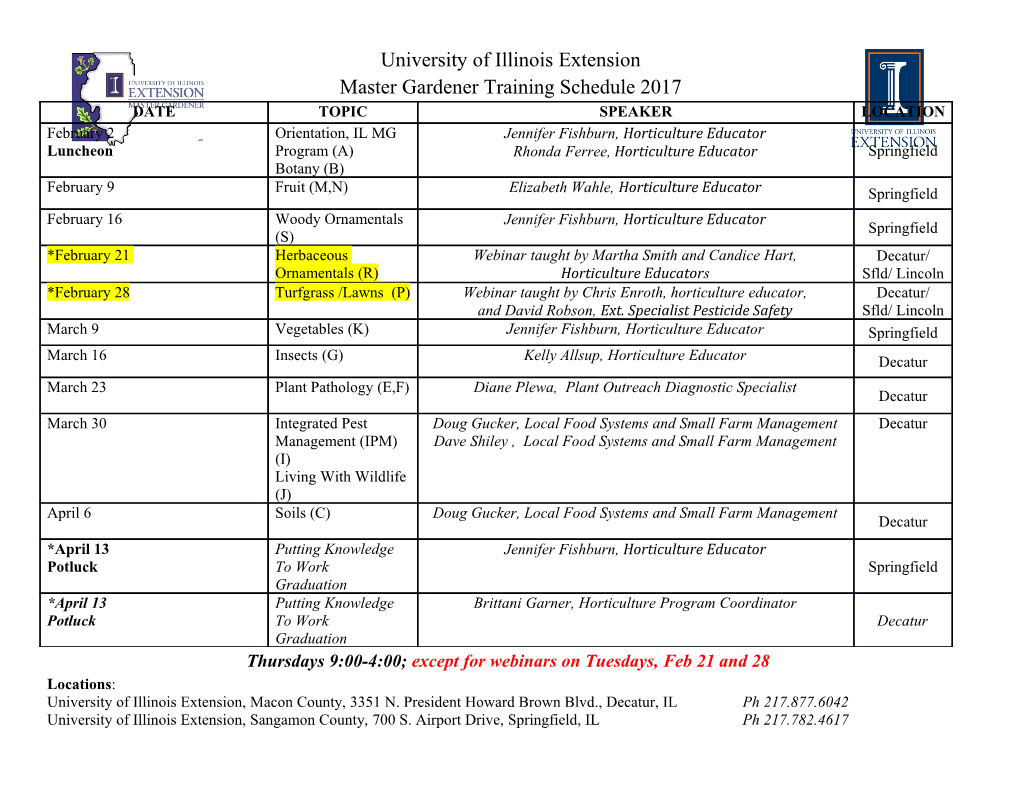
© Copyright 2011 Steven R. Mercurio Jr. All Rights Reserved EFFECT OF COPRECIPITATION OF SINTERING AIDS ON THE MICROSTRUCTURE AND GRAIN BOUNDARY DEVELOPMENT OF SINTERED SILICON CARBIDE by STEVEN R. MERCURIO JR. A dissertation submitted to the Graduate School-New Brunswick Rutgers, The State University of New Jersey In partial fulfillment of the requirements For the degree of Doctor of Philosophy Graduate Program in Materials Science and Engineering Written under the direction of Professor Richard A. Haber And approved by ________________________ ________________________ ________________________ ________________________ ________________________ New Brunswick, New Jersey October, 2011 Abstract of the Dissertation Effect of Coprecipitation on the Microstructure and Grain Boundary Development of Sintered Silicon Carbide By Steven R. Mercurio Jr. Dissertation Director: Richard Haber Coprecipitation was examined as a method of introducing sintering aids into silicon carbide (SiC) as a fine, reactive coating. The improved sinterability and mixedness of coprecipitated samples, when coupled with advanced densification methods, developed fine grained SiC with varied microstructures. Coprecipitation imparted additional process control and influenced the phase, crystallinity, and properties of the grain boundaries. A simple coprecipitation process was developed to introduce aluminum and rare earth sintering aids into SiC. Early samples yielded low densities so the process was modified to address the dispersion of the SiC particles and breakdown of agglomerates before coating. The modifications improved the densification and influenced the structure and properties. Powders were prepared with varying weight percents of sintering aids and several rare earths in order to study the grain boundary structure and properties. Samples were densified using hot pressing and spark plasma sintering to better utilize the enhanced ii sinterability of coprecipitated powders. These samples were compared to conventional ball mill processing. Scanning electron microscopy was utilized to examine the microstructure and determine the grain size and presence of defects. The degree of mixedness of the additives was investigated through fluorescence measurements. X-ray diffraction was used to determine the polytype and phase distribution. Selected mechanical properties were measured and compared between the different samples. Hardness was studied extensively, including analysis of load-hardness curves over a range of loads. The hardness data and indents were examined in order to explore the fracture behavior and defect effects. Liquid phase sintered SiC prepared using coprecipitation exhibited very different phase content and crystallinity than ball milled samples. Fluorescence measurements for coprecipitated samples showed longer decay lifetimes indicating improved mixedness. Samples with amorphous grain boundaries and triple points were developed, where XRD results displayed a lower amount of yttrium aluminum garnet than other methods. The formation of a crystalline mullite phase and absence of excess alumina were observed. These overall results indicated the possibility of different fracture behavior. iii Acknowledgments Zero score and 6 or so years ago, I began forth at Rutgers, this thesis, conceived in struggle and dedicated to the proposition that I could see this through. Now, I’m finished engaging in this great task which can long endure. I have come to dedicate these thank yous as a final resting place for those who gave their hard work, time, effort, and care so that this thesis may live. It is altogether fitting and proper that I should do this. But, in a larger sense, I cannot dedicate – I cannot consecrate – I cannot hallow – this thesis. The brave men and women who struggled here with me have consecrated it far above my poor power to add or detract with thanks. The world will little note, nor long remember what I say here, but I will never forget what all my undergraduate technicians, group members (even Stevie B), friends, family, faculty, and others did here. It is for us to be dedicated here to the excellent work which they who have helped me have thus so nobly advanced. It is rather for us to be here thanked for the great work finished – that from these hard working friends, department staff, John Yaniero, we take the increased devotion to the cause, the thesis, for which they gave their last full measure of devotion. I here highly resolve that these people shall not have worked in vain, that this thesis now has a new birth of freedom, and that it shall not perish from the earth. Thanks to Abe Lincoln for inspiring me to write some of my acknowledgments as such. I would like to give special thanks to my advisor, Dr. Haber, for your support, guidance, and entertaining moments and conversations throughout the years. I also have the deepest gratitude to Dr. Todd Jessen for providing me with support, additional funding, and especially your technical approach and wisdom. Your belief in this work during some of my less optimistic moments helped me see it through. I’d like to give a iv hearty thank you to Dr. Greenhut for your valuable conversations, both technical and non-technical. I’m also grateful to Dr. Niesz for serving on my committee. Thank you to Dr. Joseph Michael of Sandia National Laboratory for the assistance with TEM sample preparation and Dr. F. Cosandey for his guidance on the TEM imaging and analysis. The technical expertise of Dr. Bill Mayo on x-ray diffraction was invaluable in moving this work forward. Thanks to the US Army Research Laboratory, Materials Center of Excellence, and Center for Ceramics Research at Rutgers for their financial support. I’d like to thank Dr. Mihaela Jitianu for her help and expertise that added greatly to this research. Very special thanks to Dr. Steve Miller for both his contributions to this research and my overall sanity during my time at Rutgers, Doug Slusark for being my necessary “nemesis”, and to Dan Maiorano for walking much of this long and winding path with me….We will always share a bond that can only be forged in moments when hot presses are melting before your eyes and the floor is stained green with antifreeze. My deepest gratitude goes to my parents for raising me to always strive for learning and for giving me the traits that made this journey possible. Thanks to my little sister for the laughs, support, and the pleasure of watching you strive and achieve as well. To Maddie, who can’t even read this yet…Thank you for raising my spirits during the tough parts, and for appearing in that dream when I was thinking of quitting and telling me to “Finish what you started.” Becky, my wonderful wife, I can never thank you enough for helping me, supporting me, and most of all, putting up with me during this journey. I would not and could not have done this without you. v Table of Contents Abstract of Dissertation………………………………………………………………..….ii Acknowledgments…………………………………………………………………………v Table of Contents…………………………………………………………………...……vii List of Tables……………………………………………………………………………xiii List of Figures………………………………………………………………………..…..xv Chapter 1 Introduction to Silicon Carbide…………………………………………….....1 1.1 Motivation and Background……………………………………………………1 1.2 Silicon Carbide………………………………………………………………….5 1.2.1 Crystal Structure………………………………………………………..5 1.2.2 Stacking Faults………………………...………………………………10 1.3 Green Processing of SiC………………………………...…………………….13 1.3.1 Production of SiC Powders……………………………………………13 1.3.1.1 Importance of Raw SiC Powders…………………………….....15 1.3.2 Conventional SiC Processing………………………………………….16 1.3.3 Colloidal Processing……………..……………………………………18 1.3.4 Sintering…………………………………………………………….…19 1.3.4.1 Sintering Theory………………………………………………..19 1.3.4.2 Assisted Sintering Methods…………………………………….24 1.3.4.2.1 Hot Pressing……………………………………….24 1.3.4.2.2 Spark Plasma Sintering……………………………25 1.3.4.3 Solid State Sintering…………………………...……………….26 1.3.4.4 Liquid Phase Sintering………………………………………….28 1.3.5 SiC Sintering Studies…………………………………………….……31 vi 1.3.5.1 Solid State Sintering Studies……………………………………31 1.3.5.2 Liquid Phase Sintering Studies……………………...………….33 Chapter 2 Method of Attack……………………...…………………………………….35 Chapter 3 Improved Coprecipitation Processing as a Method of Removing Defects….39 3.1 Introduction…………………………………………………..………………..…39 3.2 Processing – Structure – Properties Relationship………………………………40 3.2.1 Impact of Defects on Mechanical Properties………………………..….40 3.2.2 Influence of Processing on the Population of Defects………………...41 3.3 Improved Processing Methodology………………………………………….…44 3.3.1 Coprecipitation………………………………………………………...45 3.4 Procedures……………………………………………………………………....50 3.4.1 Initial Coprecipitation Procedure…………………………………..….50 3.4.1.1 Raw Materials……………………………………………………..50 3.4.1.1.1 Silicon Carbide……………………………………..50 3.4.1.1.2 Sintering Aids………………………………..……..51 3.4.2 Composition Selection………………………………………………….52 3.4.2.1 Titration Curves……………...…………………………………52 3.4.3 Coprecipitation Procedure ……………………………………………..53 3.4.4 Processing Improvements………………………………………………56 3.4.4.1 Milling Treatment………………………………………………56 3.4.5 Comparison Samples………………………………………...…………57 3.4.6 Note on Sample Naming and Nomenclature………….………………..57 3.4.7 Sintering…………………………………...……………………………58 vii 3.4.7.1 Hot Pressing…………………………………………………….58 3.4.7.2 Spark Plasma Sintering…………………………………………60 3.5 Characterization Techniques……………………………….…………………….62 3.5.1 BET……………………………………………………………………..62 3.5.2 FTIR…………………………………………………………………….62 3.5.3 Electrokinetic
Details
-
File Typepdf
-
Upload Time-
-
Content LanguagesEnglish
-
Upload UserAnonymous/Not logged-in
-
File Pages235 Page
-
File Size-