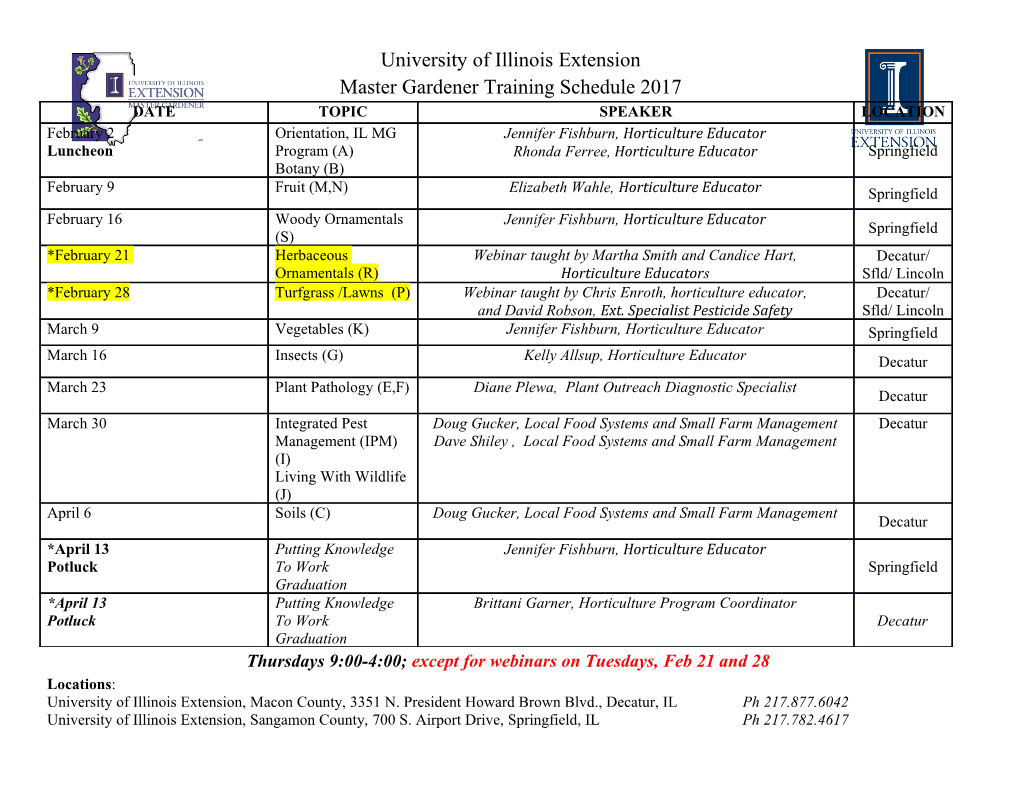
Copper Alloys for Marine Environments Copper Alloys for Marine Environments Carol Powell and Peter Webster, Copper Development Association CDA Publication No 206 May 2011 Revised December 2012 Copper Development Association is a non-trading organisation that promotes and supports the use of copper based on its superior technical performance and its contribution to a higher quality of life. Its services, which include the provision of technical advice and information, are available to those interested in the utilisation of copper and copper alloys in all their aspects. The Association also provides a link between research and the user industries and is part of an international network of trade associations, the Copper Alliance™. Disclaimer: Whilst this document has been prepared with care, we can give no warranty regarding the contents and shall not be liable for any direct, incidental or consequential damage arising out of its use. For complete information on any material, the appropriate standard should be consulted. Cover page picture acknowledgement: Copper-nickel splash zone sheathing on a platform in the Morecambe Field (Courtesy Centrica Energy Upstream, East Irish Sea) Contents Tables and Figures 2 1.0 Introduction 3 2.0 Copper Alloy Groups: Properties and Applications 4 2.1 Coppers 6 2.2 Copper-nickel Alloys 7 2.2.1 90-10 and 70-30 Copper-nickel Alloys 7 2.2.2 High Strength Copper-nickel Alloys 10 2.3 Bronzes 11 2.3.1 Phosphor Bronze 11 2.3.2 Gunmetals 11 2.3.3 Aluminium Bronzes 11 2.3.4 Silicon Bronzes 14 2.4 Brasses 14 2.5 Copper-beryllium 17 3.0 Corrosion Behaviour of Copper Alloys in Seawater 18 3.1 Selective Phase Corrosion 18 3.2 Stress Corrosion Cracking 18 3.3 Erosion Corrosion 18 3.4 Crevice Corrosion 20 3.5 Polluted Conditions 20 3.6 Splash Zone Protection 21 4.0 Galvanic Behaviour 22 5.0 Marine Biofouling 24 6.0 Summary of Good Practices 25 7.0 Recyclability 26 8.0 References and Further Information 27 8.1 References 27 8.2 Other Useful Documents 28 8.3 Information Sources 28 COppER ALLOYS FOR MARINE ENVIRONMENTS | 1 Tables and Figures Tables Table 1 Alloy Groups Table 21 Typical Mechanical Properties of Figure 13 90-10 copper-nickel splash zone Table 2 Selection of European Standards Copper-beryllium protection on a platform in the for Product Forms in Copper and Table 22 Flow Rate Guidelines and the Morecambe Field, UK Copper Alloys Influence of Solid Matter Figure 14 Galvanic series in seawater Table 3 Examples of Temper Designation Table 23 Typical Guidelines to avoid Figure 15 Comparison of a cathodically for Copper Alloys (ASTM B601 Sulphide Corrosion during protected and freely exposed – Standard Classification for Commissioning, Shutdown and 90-10 copper-nickel panel after Temper Designations for Copper Standby Conditions 12 month exposure at Langstone and Copper Alloys – Wrought Table 24 Typical Considerations for Good Harbour, UK and Cast) Practices Figure 16 Van Diemen Aquaculture in Table 4 Letter Symbols for Property Tasmania has successfully used Designations (EN 1173) Figures Mitsubishi-Shindoh’s UR30™ Table 5 Typical Physical and Mechanical brass alloy in salmon cages Properties Figure 1 Underwater photo of royal crest supplied by the Ashimori still plainly visible on a bronze Industry Company Table 6 Typical Mechanical Properties of cannon on a warship wrecked Engineering Copper Figure 17 Dismantling Oscar1 class in 1744 submarine Table 7 Typical Applications for Figure 2 Copper-nickel pipework aboard Engineering Copper ship Table 8 Typical Applications for Figure 3 Fourteen year corrosion rate Copper-nickel Alloys data at LaQue Center for Table 9 Nominal Compositions of Corrosion Technology, North Copper-nickel Alloys (weight %) Carolina, for 90-10 and 70-30 Table 10 Typical Mechanical Properties of copper-nickels Copper-nickel Alloys Figure 4 Nickel aluminium bronze ship Table 11 Typical Guidelines for Flow propeller Velocities for 90-10 and 70-30 Figure 5 Silicon bronze rigging toggle for Copper-nickel Alloys in Seawater mast support Systems, m/s Figure 6 Manganese bronze dee shackle Table 12 Standards and Typical All-Weld- Figure 7 Tungum® brass tubing on Metal Compositions of Filler decompression chamber housing Metals living and sleeping sections for Table 13 Typical Applications for Bronzes divers Table 14 Nominal Compositions of Typical Figure 8 Copper-beryllium repeater Bronzes (weight %) housing assembly Table 15 Typical Mechanical Properties Figure 9 Dezincification of a 60-40 brass of Bronzes valve stem Table 16 Typical Applications for Brasses Figure 10 Erosion corrosion in a 90-10 Table 17 Nominal Compositions of Typical copper-nickel tube due to Brasses (weight %) excessively high flow velocities Table 18 Typical Mechanical Properties Figure 11 Relative breakdown velocities of Brasses for copper alloys in seawater Table 19 Typical Applications for Figure 12 Between 150-200 tons of 90-10 Copper-beryllium copper-nickel have been Table 20 Nominal Composition of installed on individual drill ships Copper-beryllium (weight %) for the fire fighting system 2 | COppER ALLOYS FOR MARINE ENVIRONMENTS 1.0 Introduction The aim of this publication is to provide to meet today’s exacting engineering good standard of tolerance and surface engineers with an appreciation of copper challenges, copper alloys continue to offer finish. Some copper alloys have excellent alloys commonly used in marine solutions to a range of industries requiring machinability as a primary attribute - applications. It will provide an overview reliability in seawater. specifically leaded brasses, which set the of the range of alloys and their standard by which all other metals are properties, and give references and The metal copper is very versatile, having judged. Other copper alloys are made with sources for further information. good resistance to corrosion in marine a variety of combinations of properties atmospheres and in seawater with such as strength, wear resistance, Copper is a metal that is extracted from moderate flow velocities. Its properties, anti-galling and cold formability. These the earth, is essential to the development both in terms of corrosion resistance and may be less easily machined, but are still of all forms of life and has been vital in the mechanical strength, can be further easier to machine than many other types progress of civilisation. Alongside gold, it improved by alloying. There are many of material. is the oldest metal used by man and its copper alloys suitable for marine service history of use dates back more than 10,000 and the main groups are: For seawater systems, copper-nickel and years. aluminium bronze are often preferred, Coppers although other copper alloys are used in Since antiquity, both wrought and cast Copper-nickels marine service and have their specific forms of copper alloys have shown high Bronzes advantages. Copper alloys differ from resistance to the ravages of the marine Brasses other metals in that they have an inherent environment, like the bronze cannon in Copper-beryllium high resistance to biofouling, particularly Figure 1. Seawater is corrosive to most macrofouling, which can eliminate the construction materials and, with properties All copper alloys can be machined need for antifouling coatings or water which have been developed and modified accurately and cost-effectively and to a treatment. Figure 1 - Underwater photo of royal crest still plainly visible on a bronze cannon on a warship wrecked in 1744 (Courtesy Odyssey Marine Exploration) COppER ALLOYS FOR MARINE ENVIRONMENTS | 3 2 2.0 Copper Alloy Groups: Properties and Applications There are many copper alloys which fall Table 1 - Alloy Groups within each group and a selection are examined here. Copper Development Alloy Group Alloy Types Association publication 120 Copper and Coppers Cu Copper Alloys(1) gives a more comprehensive breakdown of standards, Copper-nickels 90-10 Cu-Ni compositions and properties. Typical 70-30 Cu-Ni applications for marine environments Cu-Ni-Cr include heat exchangers and condensers, Cu-Ni-Sn seawater piping, hydraulic tubing, pump Cu-Ni-Al and valve components, bearings, fasteners, marine fittings, propellers, shafts, offshore Bronzes Cu-Sn-P (phosphor bronze) sheathing and aquaculture cages. Cu-Sn-Zn (gunmetal) Cu-Al (aluminium bronze/nickel aluminium bronze) The alloy groups, and alloys within each Cu-Si (silicon bronze) group, are described in Table 1. Brasses Cu-Zn Copper and copper alloys are produced to Copper-beryllium Cu-Be conform with a wide variety of national and international specifications prepared to suit different conditions and bronzes may be made which would either hardened alloys which are heat treated to requirements. They are ductile and may be not be covered in the wrought strengthen the metal matrix by forming manufactured by extrusion, forging, rolling, specifications or be of non-standard sizes. precipitates in the structure. Copper alloys drawing, hot stamping and cold forming. do not undergo a ductile-brittle transition, They can also be cast by all of the Minimum mechanical properties will as mild steel does, and are ductile down to traditional casting methods such as sand depend on the product form, specification cryogenic temperatures. The highest and die, and by continuous and centrifugal used, dimensions and material condition. strength of any copper alloy is given by the methods. Mechanical properties of copper alloys can copper-beryllium alloys, which may be range from ‘moderate’ in the case of the hardened by a combination of cold working Table 2 gives a selection of EN standards coppers to ‘extremely high’ for the and age hardening to values comparable to for copper and copper alloy product forms. Cu-Ni-Sn, Cu-Ni-Al and Cu-Be alloys. that of high strength steel. It is clear that, by selection of the Annealed values can be increased by cold appropriate wrought or cast route, almost work for copper and alloys such as brasses, Table 3 shows the range of conditions any shape can be obtained.
Details
-
File Typepdf
-
Upload Time-
-
Content LanguagesEnglish
-
Upload UserAnonymous/Not logged-in
-
File Pages32 Page
-
File Size-