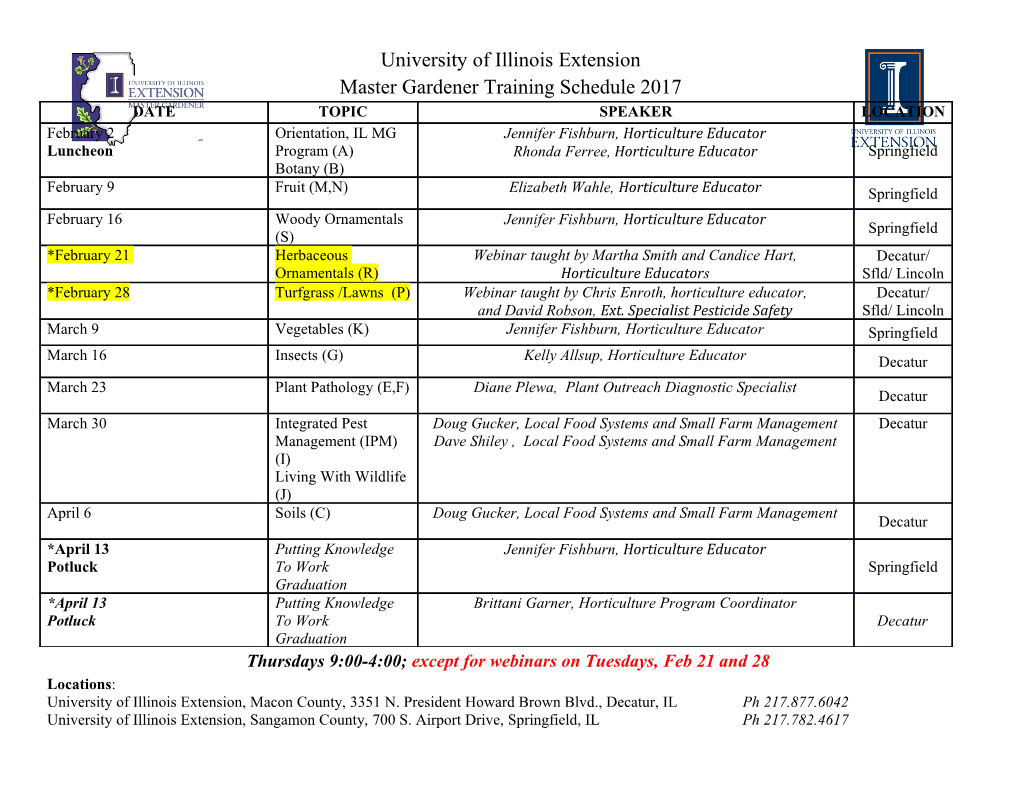
Evaluation of Multilayer Silicon Carbide Composite Cladding Under Loss of Coolant Accident Conditions By Gregory Welch Daines B.S. Mechanical Engineering (2014) The University of Maryland at College Park SUBMITTED TO THE DEPARTMENT OF NUCLEAR SCIENCE AND ENGINEERING IN PARTIAL FULFILLMENT OF THE REQUIREMENTS FOR THE DEGREE OF MASTER OF SCIENCE IN NUCLEAR SCIENCE AND ENGINEERING AT THE MASSACHUSETTS INSTITUTE OF TECHNOLOGY February 2016 © 2016 Massachusetts Institute of Technology. All rights reserved. Signature of Author: ____________________________________________________________________ Gregory Welch Daines Department of Nuclear Science and Engineering December 17, 2015 Certified by: __________________________________________________________________________ Michael P. Short, Ph.D. Assistant Professor of Nuclear Science and Engineering Thesis Supervisor Certified by: __________________________________________________________________________ Thomas J. McKrell, Ph.D. Research Scientist Thesis Reader Accepted by: __________________________________________________________________________ Ju Li, Ph.D. Battelle Energy Alliance Professor of Nuclear Science and Engineering And Professor of Materials Science and Engineering Chairman, Department Committee on Graduate Students THIS PAGE INTENTIONALLY LEFT BLANK 2 Evaluation of Multilayer Silicon Carbide Composite Cladding Under Loss of Coolant Accident Conditions by Gregory Welch Daines Submitted to the Department of Nuclear Science and Engineering on December 17, 2015 in Partial Fulfillment of the Requirements for the Degree of Master of Science Abstract Silicon carbide (SiC) has been proposed as an alternative to zirconium alloys used in current light water reactor (LWR) fuel cladding because it exhibits superior corrosion characteristics, high-temperature strength, and a 1000˚C higher melting temperature, all of which are important during a loss of coolant accident (LOCA). To improve the performance of SiC cladding, a multilayered architecture consisting of layers of monolithic SiC (mSiC) and SiC/SiC ceramic matrix composite (CMC) has been proposed. In this work, the mechanical performance of both the tubing and the endplug joint of two-layer SiC cladding is investigated under conditions associated with the LOCA. Specifically, SiC cladding mechanical performance is investigated after exposure to 1,400˚C steam and after quenching from 1,200˚C into either 100˚C or 90˚C atmospheric-pressure water. The samples consist of two-layer SiC, with an inner SiC/SiC CMC layer and an outer monolith SiC layer. The relationship between mechanical performance and sample architecture is investigated through ceramography and internal void characterization. The two-layered SiC cladding design offered an as-received failure hoop stress of about 600 MPa, with little strength reduction due to thermal shock, and the tube failure hoop stress remained above 200 MPa after 48 hour high-temperature steam oxidation. The cladding showed pseudo-ductile behavior and failed in a non-frangible manner. The designs investigated for joint strength offered as-received burst strength above 30 MPa, although the impact of thermal shock and oxidation showed possible dependence on architecture. Overall, the cladding showed promising accident-tolerant performance. Because the implementation of SiC is complicated by the need for an open gap and low plenum pressure, thorium-based mixed oxides (MOX) are a promising fuel for SiC cladding because they have higher thermal conductivity and lower fission gas release (FGR). Previous efforts at MIT have modified the FRAPCON code to include thorium MOX fuel. In this work, the fission gas release and thermal conductivity models of FRAPCON-3.4-MIT are validated against published data. The results of this validation indicate a need to update the FGR model, which was accomplished in this work. Thesis Supervisor: Michael P. Short, Ph.D. Title: Assistant Professor of Nuclear Science and Engineering Thesis Reader: Thomas J. McKrell, Ph.D. Title: Research Scientist 3 THIS PAGE INTENTIONALLY LEFT BLANK 4 Acknowledgments This work was supported under the United States Department of Energy award number DE-NE0000566 where MIT acted as a subcontractor to Westinghouse Electric. The samples investigated in this work were manufactured and provided by General Atomics. I would like to extend my gratitude to the late Professor Mujid Kazimi, who recruited me to this topic and supervised my research until his death. He provided me with valuable direction, feedback, and encouragement on my research. I also wish to express my gratitude to Professor Michael Short, who assumed the role of my thesis supervisor upon Professor Kazimi’s death, and to Professor Jacopo Buongiorno and Dr. Koroush Shirvan, who assumed leadership roles of the CANES group after Professor Kazimi’s death and provided feedback and guidance on my research. I would also like to thank Dr. Thomas McKrell, who provided invaluable guidance and support on the experimental aspects of my research. His experience in experimentation immeasurably helped my research and experimental skills, and his supervision and feedback during my frequent contact with the project clients enhanced my communication skills. Furthermore, I appreciate Professor Ron Ballinger and Peter Stahle for allowing me to use the load frame in the H. H. Uhlig corrosion laboratory. I also recognize Dr. Christian Deck, Dr. George Jacobsen, and Dr. Hesham Khalifa of General Atomics and Dr. Ed Lahoda and Dr. Peng Xu of Westinghouse Electric for providing feedback and suggestions for my research. Their input helped direct the conduct of my research, and they provided feedback on the results of my investigation. I thank Pierre Guenoun with whom I worked closely and I also thank Yongsoo Park, whose concern for lab safety went above-and-beyond expectations. Finally, I thank my family for their support and assistance while I have been at MIT. 5 Table of Contents Abstract ......................................................................................................................................................... 3 Acknowledgments ......................................................................................................................................... 5 List of Figures .............................................................................................................................................. 10 List of Tables ............................................................................................................................................... 15 Nomenclature ............................................................................................................................................. 17 1. Introduction ........................................................................................................................................ 18 1.1. Motivation ................................................................................................................................... 18 1.2. Overview of Current LWR Cladding ............................................................................................ 19 1.2.1. LWR Cladding Overview ...................................................................................................... 19 1.2.2. Limitations of Current PWR Cladding ................................................................................. 19 1.3. Accident Tolerant Fuels............................................................................................................... 20 1.3.1. Motivation and Description of Accident Tolerant Fuels ..................................................... 20 1.3.2. Silicon Carbide for Nuclear Applications ............................................................................. 21 1.4. Objectives and Scope .................................................................................................................. 22 1.5. Thesis Organization ..................................................................................................................... 23 2. Performance Modeling of Thorium-Based Fuels ................................................................................ 25 2.1. Motivation ................................................................................................................................... 25 2.2. Fission Gas Release Mechanism.................................................................................................. 25 2.3. FRAPCON Fission Gas Release Model ......................................................................................... 26 2.3.1. Forsberg-Massih Model ...................................................................................................... 26 2.4. FRAPCON Modifications .............................................................................................................. 28 2.4.1. Thermal Conductivity Models ............................................................................................. 28 2.4.2. Fission Gas Release Models ................................................................................................ 34 2.5. Discussion .................................................................................................................................... 42 2.5.1. Densification Uncertainty ................................................................................................... 42 2.5.2. Comparison to Published
Details
-
File Typepdf
-
Upload Time-
-
Content LanguagesEnglish
-
Upload UserAnonymous/Not logged-in
-
File Pages164 Page
-
File Size-