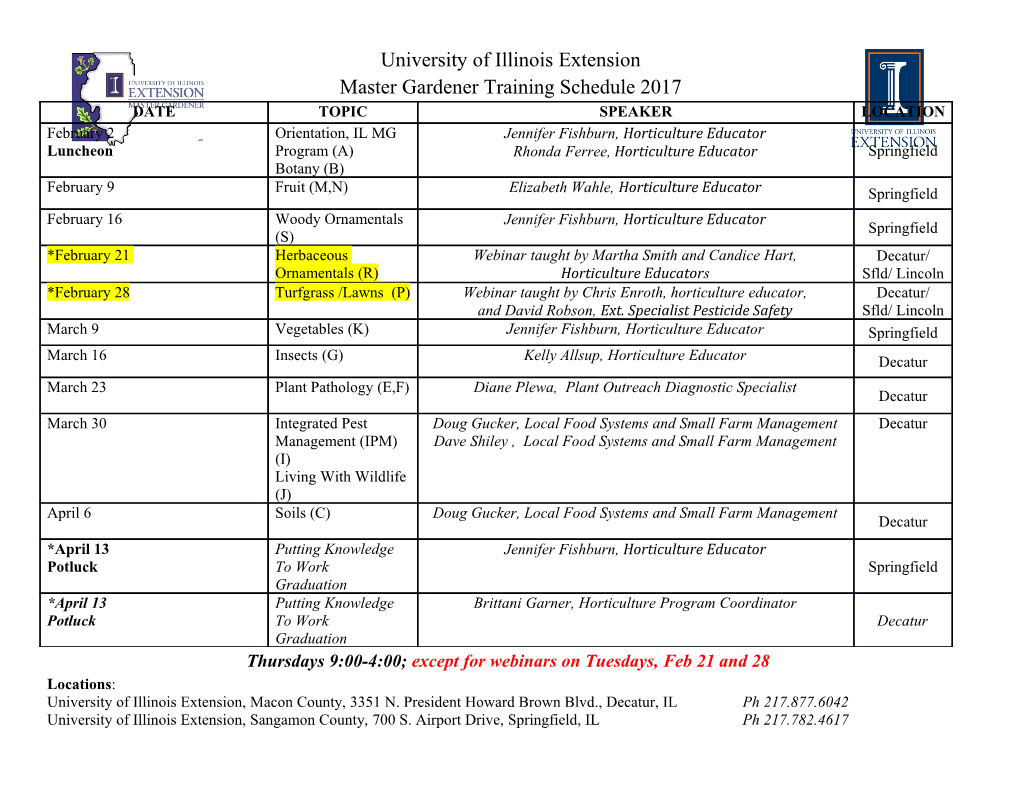
SSC99-VII-4 Design of Simple Low-Cost Mars Microlander Tomas Svitek Stellar Innovations, Inc. 1436 Clover Creek Dr, Longmont CO 80503 303-651-7580, [email protected] Abstract. This paper describes the development of a simple low-cost Mars microlander that is matched to the capabilities of the recently-approved Mars Micromission program. This particular microlander design is in- tended to fill a capability gap between two existing landing systems: the large sophisticated soft landers like Mars Polar Lander and the miniaturized DS-2-class penetrators. This microlander would be able to deliver (in a con- trolled manner) a small but sophisticated science payload to multiple, exciting but risky landing sites (as an ex- ample for our point design, we have used the delivery of the 60% scale Sojourner-class minirover). The unique attribute of this design is the maximum exploitation of existing technology that is integrated in a un- precedented-simple lander system configuration. This inherent simplicity results in the system that is simultane- ously low-cost and robust (and thus reliable). Two key technologies are employed in the microlander design: · small solid rocket propulsion (commercially available) with adequate performance, and · integrated FM-CW radar sensor (also commercially available) that is used as the only guidance sensor. .The lander design is intended to be field tested soon in order to maximize the probability of mission success. Introduction surmountable obstacle for many sophisticated sci- ence payloads, particularly involving mobility. This microlander was conceived in response to the capabilities of the recently-announced Mars Micromis- To fill this performance gap, several alternative de- sion program. This program aims at developing and signs were proposed in the past, based on various deploying a new class of affordable Mars exploration schemes for the parachute deceleration and impact missions. The microlander would be carried to Mars attenuation by crushable materials or air bags. The in an entry aeroshell by the micromission probe carrier parachute/air-bag deceleration approach was proven by spacecraft that is launched by Ariane 5 as the piggy- the Mars Pathfinder mission and by the multiple earlier back payload. The introduction of the Mars Micromis- Russian Mars and Lunar lander missions. It will be sion concept generated many exciting diverse ideas for used by two upcoming European missions to Mars future Mars exploration that were highlighted in sev- (Beagle-2 and NetLander), as well. eral Mars Micromission science workshops and during the latest Discovery proposal cycle. The difficulty with this approach is scaling down to- wards the smaller physical size, essential for compati- This particular microlander design is intended to fill a bility with the Mars Micromissions. Additionally, in capability gap between two existing landing systems: these landing schemes, the landers impacts the surface 1) A large sophisticated lander like Mars Polar in an arbitrary orientation and thus requires some me- Lander is capable of the precision landing with chanical means for positioning itself the right side up. multiple instruments, and serving as the long-term That further degrades the payload mass allocation for a scientific platform on the surface. But its high re- small micromission lander. Incompatibility of the air- curring cost (over $100M, including a dedicated bag landing scheme with the Mars Micromission con- launch) prevents its proliferation and deployment straints has been verified by an earlier JPL/CNES to high-risk scientifically interesting sites. study. 2) Highly miniaturized DS-2-type penetrators offer low-cost payload surface delivery, particularly Our microlander design would enable the low-cost de- suited for experiments requiring subsurface access. ployment of relatively sophisticated science payload to The DS-2 design nicely matches the Mars Mi- multiple sites. These landing sites can be more risky cromission concept but its ruggedization require- (and thus potentially scientifically more interesting) ment due to its 10-30K g’s impact shock is an in- than would be acceptable for a conventional single 1 Tomas Svitek 13th Annual AIAA/USU Conference on Small Satellites lander. The payload options includes payloads with Technical Description mobility or mechanical components (small rovers, ma- nipulator arm), shock-sensitive instruments (e.g., long- This microlander is designed to satisfy these specific period seismometer), tethered microballoons, etc. requirements for Mars Micromission compatibility: a) total entry mass of less than 40 kg (when deployed The microlander design is carefully matched to the from the probe carrier spacecraft), Mars Micromission ASAP probe carrier requirements b) maximum aeroshell diameter of 75 cm, and results in the net 30% payload mass fraction. This c) recurring microlander EDL cost of few $M, and payload capability corresponds to about the 60%-scale d) flight readiness for the 2005 launch opportunity. Sojourner-type rover (13 kg mass, 50 cm length) -- as The landing system consists of these key components: an example. propulsion hardware, guidance sensor(s), control elec- tronics, and aeroshell and structure. Additionally, an even smaller version of the micro- lander is being investigated. This smaller microlander Propulsion: The key enabling technology for this de- would fit within the DS-2-sized aeroshell (35-cm di- sign is the recent commercial availability of small solid ameter) and carry about 1 kg payload -- for example, rocket motors with reasonable performance, resulting the Martian version of the Muses-CN nanorover. from growth of the model rocketry hobby (so called Three or four of these entry probes can be launched on High Power Rocketry). The Isp performance of these a single Mars Micromission ASAP probe carrier and motors is respectable (210+ sec), given their small size thus 3-4 nanorovers could be deployed on the Martian and ambient-pressure nozzle design, and adequate for surface in one low-cost Mars Micromission. This the Mars landing. The propellant mass fraction is also smaller microlander version will require some technol- acceptable, although it may require some mission ogy advances, in contrast to its larger version which unique optimization. The reliability and safety record employs strictly off-the-shelf technology. of this propulsion technology is remarkable. Single motors with over 20 kNs total impulse are available Either lander version, the EDL (entry-descent-landing) (well beyond our mission requirements of about 7 sequence preserves DS-2 simplicity by eliminating the kNs). The space qualification of this commercial tech- requirement for a parachute and any complex deploy- nology is being addressed, with the particular focus on ment mechanisms, inertial sensors and guidance soft- the interplanetary cruise dormancy and the ignitor reli- ware. The mission profile simplification and testability ability. are essential for this low-cost microlander design. During the initial microlander concept design, both This microlander design employs the small solid pro- liquid and solid propulsion choices for the microlander pulsion (with relatively modest performance) for im- propulsion subsystem were investigated. The liquid pact deceleration and thrust steering. The streamlined propulsion would have moderately better payload mass guidance scheme requires only minimalistic electronics fraction and it would allow the significantly more pre- and sensor suite. The control algorithm can be imple- cise landing and result in the lower impact shock. mented in hardware for the maximum robustness. The lander would land a modest science payload at less Ultimately, the deciding factor for the solid propulsion than 15 m/sec vertical velocity, with the negligible was its commercial availability and possibility of low- horizontal velocity and less than the 500-g impact cost testing. Solid propulsion systems on the scale shock (with the lander material attenuation). similar to the Mars microlander are routinely built and flown solid – as a hobby! The quick-and-dirty ap- Our goal is to demonstrate in a credible way that the proach to the field testing would not be possible with technology for this low-cost microlander is at the suffi- the conventional liquid propulsion. A small company cient technological readiness. The unique contribu- could never credibly contemplate the design and field- tion of this design in an integration of several existing testing of a hydrazine-powered Mars lander but we can proven low-cost technologies into a new class of sur- make such a claim for our solid-propelled microlander. face exploration vehicle. The development will result in a coherent microlander point design to the particular Besides the low-cost testing option, the solid- set of realistic requirements. propulsion microlander has an additional advantage of minimizing the launch site operations because no fu- eling is required. This is potentially a great cost driver in the piggyback launch mode, because of the planetary 2 Tomas Svitek 13th Annual AIAA/USU Conference on Small Satellites quarantine requirements of any Mars surface mission. fies the system design, lowers its cost and enables This lander design can be shipped via a commercial higher-fidelity end-to-end lander testing. However, it carrier to the launch site with its solid rocket motors creates the challenge of separating the front heat shield installed, including ignitors, and in its aeroshell, as (addressed
Details
-
File Typepdf
-
Upload Time-
-
Content LanguagesEnglish
-
Upload UserAnonymous/Not logged-in
-
File Pages9 Page
-
File Size-