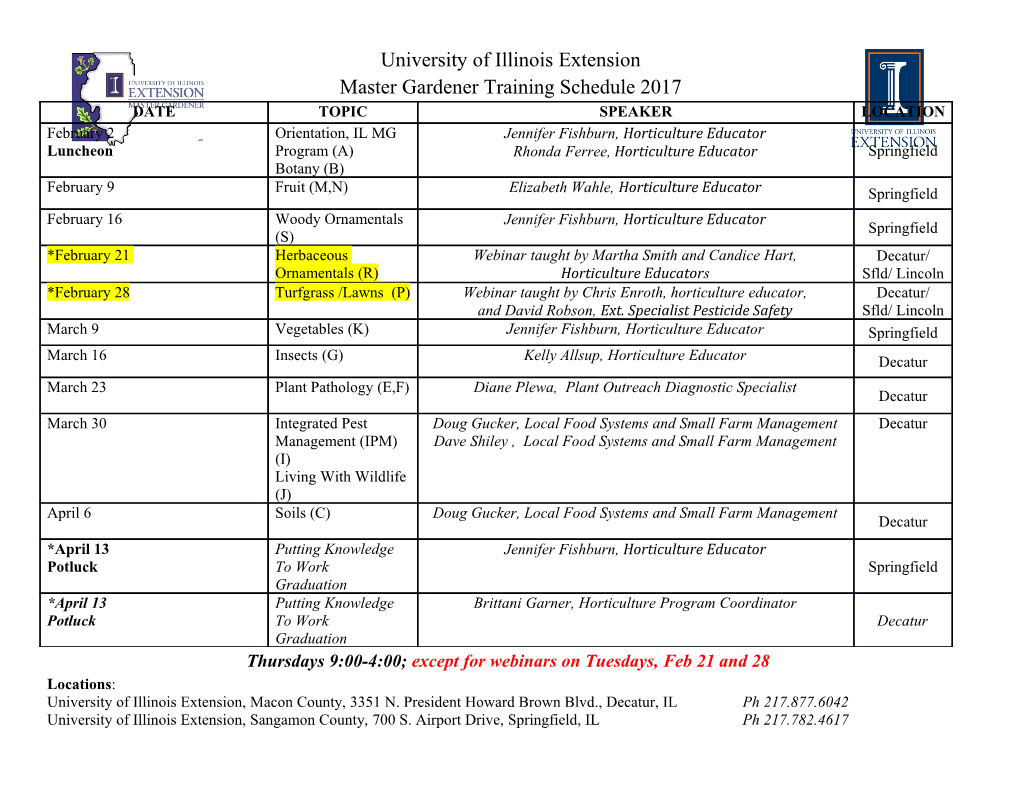
TRACK GEOMETRY MAINTENANCE MANAGEMENT SYSTEM Willem Ebersohn, Professor in Railway Engineering, Department of Civil Engineering University of Pretoria, South Africa Michael J. Trosino, Technical Director Clearances, Inspections & Tests, Amtrak 30th Street Station – Box 24, Philadelphia, U.S.A. Abstract Railroads face severe challenges as a result of demands for better service under continuously more constrained budgets. Better management systems are urgently needed to support more effective decision making. This paper will discuss the need for railroad infrastructure maintenance management systems and will describe the composition of these systems. Examples concentrating on maintaining track geometry by utilizing production maintenance work will be given. It is our intent to show how implementing a Maintenance Management System will optimize maintenance resources. Key Words: Maintenance Management Assets, Condition, Geometry. 1. COST OF MAINTENANCE Railroads are showing a substantial revival throughout the world. In the United States, railroads are showing a sustained growth in business, with an increased need for more transport capacity. Traditionally the easiest way to solve the capacity problem was to build new lines. It is also known that the full potential of the existing railroad capacity is not being utilized. A major bottleneck in providing this increased capacity is the competition for track time between train operations and track maintenance. This is exacerbated by ineffective and disruptive maintenance practices. Therefore the industry must first consider better utilization of available capacity by improving the management of existing infrastructure assets. The right of way infrastructure is by far the largest investment made by the railroad. Maintenance of these assets typically accounts for between one quarter and one third of a railroads operating cost. (E.g. infrastructure expenditures on Spoornet and on Amtrak's NEC account for 23% and 31% of operating costs respectively.) Thus by better management of the maintenance activities, the railroad's maintenance managers and engineers can play an important role in improving the efficiency of the railroads operation. This in turn will improve the overall profit margin of the railroad without the need for increased capital. Experience shows that the use of a management system which integrates the location of track assets with its successive geometrical condition measurements and production maintenance input can conservatively save up to 15% of the existing maintenance costs. This can be achieved by spending less than 2% of the maintenance cost on the development and implementation of the management system. In today's environment, with the ease of measurement and considering the size/speed of computers, it is feasible to have a proper maintenance management system in place to assist all levels of maintenance managers and engineers in their decision-making processes. In essence, such a system will equip the user with the knowledge and understanding of infrastructure's configuration and condition to target maintenance resources only to those areas needing work. A comprehensive infrastructure management system, integrated with the other business units of a railroad will result in even more savings. It is anticipated that implementation of a comprehensive management system will result in indirect savings attributable to increased capacity with improved reliability. This will in turn allow for increased revenues due to increased business. 2. MAINTENANCE MANAGEMENT CYCLE There are four major stages in the life of a railroad. We designate them as planning, design, construction, and operational use with maintenance. Each of these stages has important but changing impacts in terms of the influence that they have during the life of the railroad. Expenditures during the first three stages represent a relatively small portion of the total cost of establishing and operating the railroad infrastructure. Most of the cost to provide a safe and reliable railroad infrastructure is incurred while maintaining the railroad over its lifecycle. Figure 1 shows a typical maintenance cycle consisting of the following steps and considerations. A short description of each step follows: Step 1: Identify the need for maintenance which will consist of the following actions: • Define the current operating requirements. • Conduct condition measurements. • Identify reoccurring problem sites. • Perform cause investigation of reoccurring problem sites. • Design alternative solutions to correct problems. • Predict performance of alternatives. • Conduct a needs analysis for maintenance work (i.e. surfacing, ditching and undercutting). Step 2: Determine which maintenance alternative is economically justifiable. Step 3: Plan maintenance projects to ensure the availability of the required resources. Step 4: Schedule people, equipment, and material to complete the projects Step 5: Assign tasks. Step 6: Execute the planned work Step 7: Obtain feedback to determine. • Quality of work. • Success of work input. • Update of maintenance records. Step 1 is primarily technical in nature and is defined as Maintenance Engineering. The remaining steps involve the control of work activities and are defined as Maintenance Management 3. TRACK GEOMETRY MAINTENANCE MANAGEMENT CYCLE Maintaining track geometry and rail profile are common track maintenance activities. This paper will focus on maintaining track geometry. A typical tack geometry deterioration trend is shown in Figure 2. The graphs illustrate the effects of various categories of maintenance inputs with respect to track roughness. For purposes of discussing Figure 2, track roughness is defined as an index calculated using the geometric deviation measurement and determined by the sum of squares with a summation length as expressed in the formula: Where: n = number of measurements in the summation length. di = deviation measurement. In the examples used in this paper the summation length is 200 ft. The deviation measurements are 62-foot mid-chord offset measurements for profile and alignment or deviation measurements for cross-level and gage. All are measured in inches. The first section of Figure 2 shows the effect from initiation of service to an accumulation of 60 MGT of traffic. The solid line shows the change in back roughness when there is no maintenance input and the dashed line shows the change in track roughness with managed production surfacing input. The service life of the track is substantially reduced if the track is allowed to deteriorate without any maintenance input. As traffic accumulates over the track without any effort to reduce the geometry deterioration rate, failure of the weaker components will determine the life of the track. Further, the full potential of the stronger components will not be utilized, as most of these components will now deteriorate at an accelerated rate due to the poor performance of the weaker components. As the geometric condition of the track reaches the operational limit, renewal or upgrading work will have to occur at a premature stage. Conversely, the service life of the track can be extended by allowing the track to deteriorate to a predefined maintenance limit and then rehabilitating it through managed surfacing input to its best possible geometrical condition. In this way the full potential of the stronger components can be utilized, as the failure of the weaker components does not occur until much later in the life cycle of the track The second cycle begins at 60 MGT following the track renewal work and extends to 120 MGT. The geometry deterioration characteristics will be the same as the first cycle if no components were improved. Should the maintenance manager find that the rates of deterioration and the corresponding levels of maintenance are unacceptable, the track can be redesigned and upgraded with premium components. The third cycle begins at 120 MGT and extends to 180 MGT. It illustrates the results of the upgrade work. The rate of track geometry deterioration is slower and the level of maintenance input required to keep the track in serviceable condition is reduced. 4. MAINTENANCE MANAGEMENT SYSTEM Completing the steps in the maintenance management cycle described above requires a comprehensive knowledge of complex railroad component interactions. These include the relationship between the condition of the track and its structural performance; the effects on track performance of rehabilitation, renewal and upgrading; and the dynamic effects of vehicle speed and weight on the track response. The cycle of conducting condition measurements, performing evaluations and analyses, and drawing up consistent work plans for numerous track sections several times a year involves the processing of a massive amount of data. This data consists of condition measures, traffic records, cost information, asset inventory data, and maintenance history. To simply handle and store these masses of data becomes a daunting task. Taking the next step to actually use this information to effectively manage the maintenance of the railroad's infrastructure then requires the design of a system to manage maintenance information. In its most basic form a maintenance management system collects, correlates, and displays maintenance data. In this way, it acts as an analysis tool for the maintenance engineer. A well-designed railroad maintenance management system will accomplish the following: • Link the management of maintenance work
Details
-
File Typepdf
-
Upload Time-
-
Content LanguagesEnglish
-
Upload UserAnonymous/Not logged-in
-
File Pages16 Page
-
File Size-