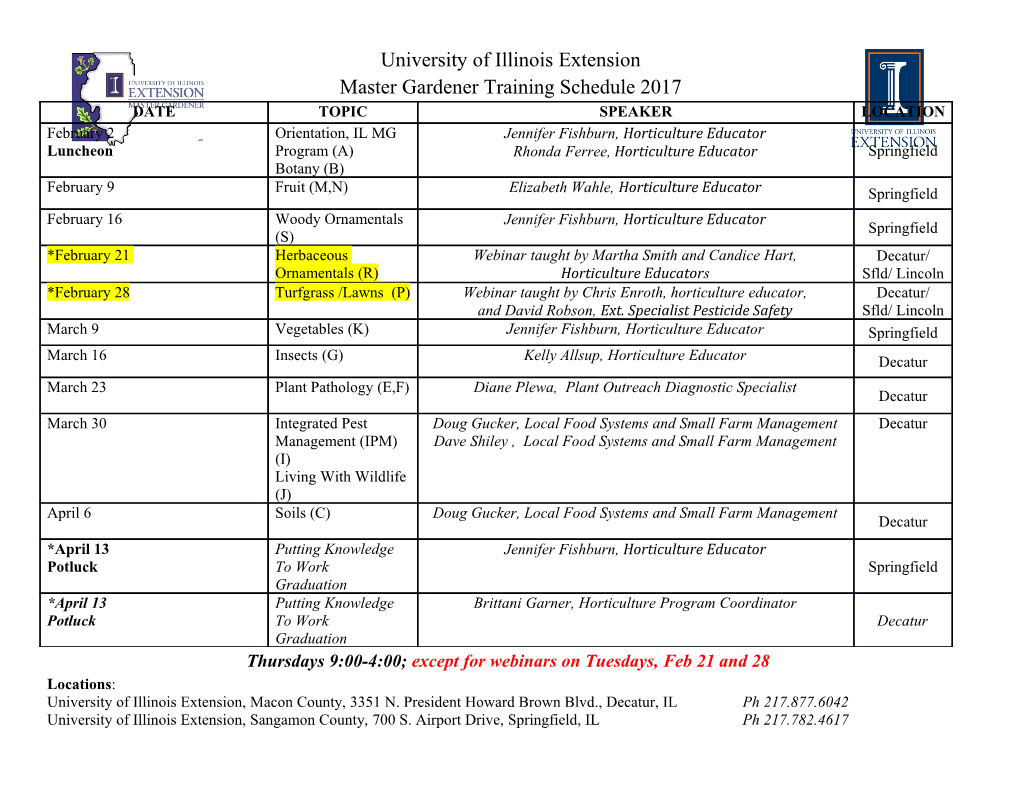
HYDRATION MECHANISMS OF MAGNESIA-BASED REFRACTORY BRICKS by SHUXIN ZHOU B. Sc., Tianjin University, China 1986 M. Sc., Shanghai Institute of Ceramics, China 1989 A THESIS SUBMITTED IN PARTIAL FULFILMENT OF THE REQUIREMENTS FOR THE DEGREE OF MASTER OF APPLIED SCIENCE m THE FACULTY OF GRADUATE STUDIES (Metals & Materials Engineering) THE UNIVERSITY OF BRITISH COLUMBIA December 2004 Shuxin Zhou, 2004 ABSTRACT Hydration of magnesia-based refractory bricks could occur during storage, during drying after installation, or in service, and the hydration would cause damage to refractory bricks and furnace linings. In order to understand the hydration mechanisms of magnesia-based refractories, three types of bricks were chosen: magnesia, magnesia-spinel and magnesia- chrome bricks, and hydration tests were performed at 60 to 130°C in 98% relative humidity, water, and steam. The variation of the modulus of elasticity (MOE), determined by the impulse excitation technique (IET), as well as apparent porosity, air permeability, pore size and pore size distribution were correlated with the hydration data. The phase compositions and microstructure modifications were also studied on selected specimens by XRD and SEM/EDS. Based on the experimental results, a hydration model of "cylindrical pore model" was established and a hydration mechanism was suggested. The hydration takes place in three stages. In the first stage, which is controlled by chemical reaction, a film of brucite forms and MOE quickly increases. During the second stage, which is controlled by diffusion, the MOE gradually reaches a maximum value followed by a slow, decrease due to the formation of cracks on the film and weakening of grain boundaries until the MOE reaches the initial value. At this point, the third stage, corresponding to "dusting", starts to take place until the brick disintegrates. The results also indicate that the hydration rate increases with rising temperature and the CaO/Si02 ratio. The variations in permeability and porosity are opposite to that in MOE. A nondestructive method - IET to assess the hydration degree of magnesia-based refractory bricks was proposed. ii TABLE OF CONTENTS ABSTRACT .' ii TABLE OF CONTENTS iii LIST OF TABLES v LIST OF FIGURES vi LIST OF ABBREVIATIONS AND SYMBOLS ix ACKNOWLEDGMENTS xiv 1. INTRODUCTION 1 2. LITERATURE REVIEW 4 2.1. Hydration of Magnesia-Based Refractories 6 2.2. Hydration of Polycrystalline Magnesia 7 2.3. Hydration of Pure Magnesia in Liquid Water 9 2.4. Hydration of Magnesia in Water Vapor 10 2.5. Kinetics of Hydration 12 2.6. Hydration of Refractory Grade Magnesia 17 2.6.1. Effect of the Physical Properties of Magnesia 17 2.6.2. Effect of Impurities 18 2.6.2.1. CaO 18 2.6.2.2. Si02 19 2.6.2.3. CaO/Si02 Ratio 20 2.6.2.4. A1203 20 2.6.2.5. Iron Oxides 20 2.6.2.6. B2O3 22 2.6.2.7. Cr203 22 2.6.2.8. Other Oxides 22 3. OBJECTIVES 23 4. EXPERIMENT PROCEDURES AND METHODOLOGY 25 4.1. Experimental Materials 25 4.2. Samples Preparation Procedures 27 iii 4.3. Experimental Methods ..28 4.4. Hydration Studies 29 4.4.1. Hydration Test Conditions 29 4.4.2. Hydration Equipment and Procedures 29 4.4.3. Calculations 30 4.5. Modulus of Elasticity 33 4.6. Permeability 36 4.7. Pore Size and Pore Size Distribution 38 4.8. Mineralogy Studies 40 4.9. Microstructure Studies 41 5. RESULTS AND DISCUSSION 42 5.1. Degree of Hydration under Different Testing Conditions 42 5.1.1. Hydration of Magnesia-Based Bricks 42 5.1.2. Magnesia-Chrome Bricks 54 5.2. Modulus of Elasticity (MOE) versus Hydration Degree 61 5.3. Influence of Brucite on MOE Variation 68 5.4. Influence of Hydration on Pore Size Distribution 76 5.5. Influence of Hydration on Permeability 78 5.6. A Simplified Kinetic Analysis 80 5.7. The Mechanism of Hydration of Magnesia-Based Refractory Bricks 90 6. CONCLUSIONS 92 7. FUTURE WORK 95 8. REFERENCES 96 iv LIST OF TABLES Table 4-1. Properties of the experimental magnesia and magnesia- spinel bricks 26 Table 4-2. The characteristics of experimental magnesia-chrome bricks 26 Table 4-3. A summary of hydration tests 31 Table 4-4. Relations between porosity P and Young's modulus E [41] 35 Table 5-1-1. The compositions of binding phases for sample MS2, Ml, and M2 from EDS analysis •. 51 Table 5-1-2. EDS results of the binding phase in the MCI and MC2 samples, wt% 58 Table 5-3-1. The compositions of different grains in MC3 shown in Fig. 5-3-2 70 Table 5-3-2. Apparent porosity of MC3 after hydration in steam at 109°C 76 Table 5-6-1. The reaction rate constants, K, of the Ml samples 87 Table 5-6-2. The reaction rate constants, K*\0, of samples MSI, MS2 and M2 in steam and humidity at different temperatures 88 Table 5-6-3. The rate constants, K*\0, for the magnesia-chrome bricks in steam 88 Table 5-6-4. Activation energies, E (kJ/mol), for the hydration of all the experimental bricks in steam and humidity 90 Table 5-6-5. Activation energy for the hydration of magnesia 90 v LIST OF FIGURES Figurel-l. Hydrated magnesia brick 2 Figure 2-1. Crystal structure of periclase 5 Figure 2-2. Crystal structure of brucite 6 Figure 2-3. Hydration curves for the magnesia single crystals, where a is the hydration degree of magnesia 8 Figure 2-4. Hydration model for polycrystalline magnesia 8 Figure 2-5. Brucite participated at 60°C in (a) fast nucleation process at pH > 13 and (b) slow nucleation process at pH ~ 10 10 Figure 2-6. Phase diagram of system CaO-MgO 19 Figure 2-7. Phase diagram of system FeO-MgO 21 Figure 4-1. Schematic representation of the specimen preparation from a brick, a) for bars used in hydration studies and MOE measurement and (b) for cylinders for permeability and pore size and pore size distribution 26 Figure 4-2. The impulse excitation technique apparatus 34 Figure 4-3. The VacuPerm Decay Permeameter (a) schematic diagram and (b) instrument 37 Figure 4-4. The operation principle for measuring pore diameters 40 Figure 5-1-1. Weight increases versus time for hydration in steam at 121°C 44 Figure 5-1-2. Weight increases versus time for hydration in steam at 109°C 44 Figure 5-1-3. Weight increases versus time for hydration in steam at 100°C 45 Figure 5-1-4. Weight increases versus time for hydration in 98% humidity at 80°C 45 Figure 5-1-5. Weight increases versus time for hydration in 98% humidity at 60°C 46 Figure 5-1-6. Weight increases versus time for hydration in water at 100°C 46 Figure 5-1-7. Weight increases versus time for hydration in water at 80°C 47 vi Figure 5-1-8. Weight increases versus time for hydration in water at 60°C 47 Figure 5-1-9. Backscatter electron micrograph of the MSI sample 48 Figure 5-1-10. EDS results of the bonding phase in the MSI matrix 49 Figure 5-1-1.1. The XRD diffractograms for the unused MSI and MS2 samples (P = pericalse and S = spinel) 50 Figure 5-1-12. Backscatter electron micrograph of the MS2 sample 51 Figure 5-1-13. Backscatter electron micrograph of brick Ml, binding phase (light gray) and periclase (dark gray) 52 Figure 5-1-14. The XRD diffractograms for the unused Ml and M2 (P = pericalse) 53 Figure 5-1-15. Backscatter electron micrograph of the M2 brick structure 53 Figure 5-1-16. Weight increases versus time for hydration in steam at 109°C. (a) for brick MC2, MC3 and MC5 and (b) for MCI, MC4 and MC6 55 Figure 5-1-17. Weight increases versus time for hydration in steam at 121°C. (a) for brick MC2, MC3 and MC5 and (b) for MCI, MC4 and MC6 56 Figure 5-1-18. Weight increases versus time for hydration in steam at 130°C 57 Figure 5-1-19. XRD diffractogra for MCI- the unused sample. P = pericalse (MgO) and C = complex spinel (Mg, Fe)(Cr, Al, Fe)204 58 Figure 5-1-20. Hydrated MgO versus CaO/Si02 ratio for the hydration of the magnesia- spinel and magnesia bricks in water at 60°C 60 Figure 5-1-21. Hydrated MgO versus CaO/Si02 ratio for the hydration of the magnesia- chrome bricks in steam at 109°C 60 Figure 5-2-1. MOE variation versus time for hydration in steam at 121°C for magnesia- spinel and magnesia bricks 61 Figure 5-2-2. MOE variation versus time for hydration in steam at 109°C for magnesia- spinel and magnesia bricks 62 Figure 5-2-3. MOE variation versus time for hydration in steam at 100°C for magnesia- spinel and magnesia bricks 63 Figure 5-2-4. MOE variation versus time for hydration in 98% humidity at 80°C for magnesia-spinel and magnesia bricks 64 Figure 5-2-5. MOE variation versus time for hydration in 98% humidity at 60°C for magnesia-spinel and magnesia bricks 64 Figure 5-2-6. MOE variation versus time for hydration in steam at 109°C. (a) for brick MC2, MC3 and MC5 and (b) for MCI, MC4 and MC6 65 Figure 5-2-7. MOE variation versus time for hydration in steam at 121°C. (a) for brick MC2, MC3 and MC5 and (b) for MCI, MC4 and MC6 66 Figure 5-2-8.
Details
-
File Typepdf
-
Upload Time-
-
Content LanguagesEnglish
-
Upload UserAnonymous/Not logged-in
-
File Pages115 Page
-
File Size-