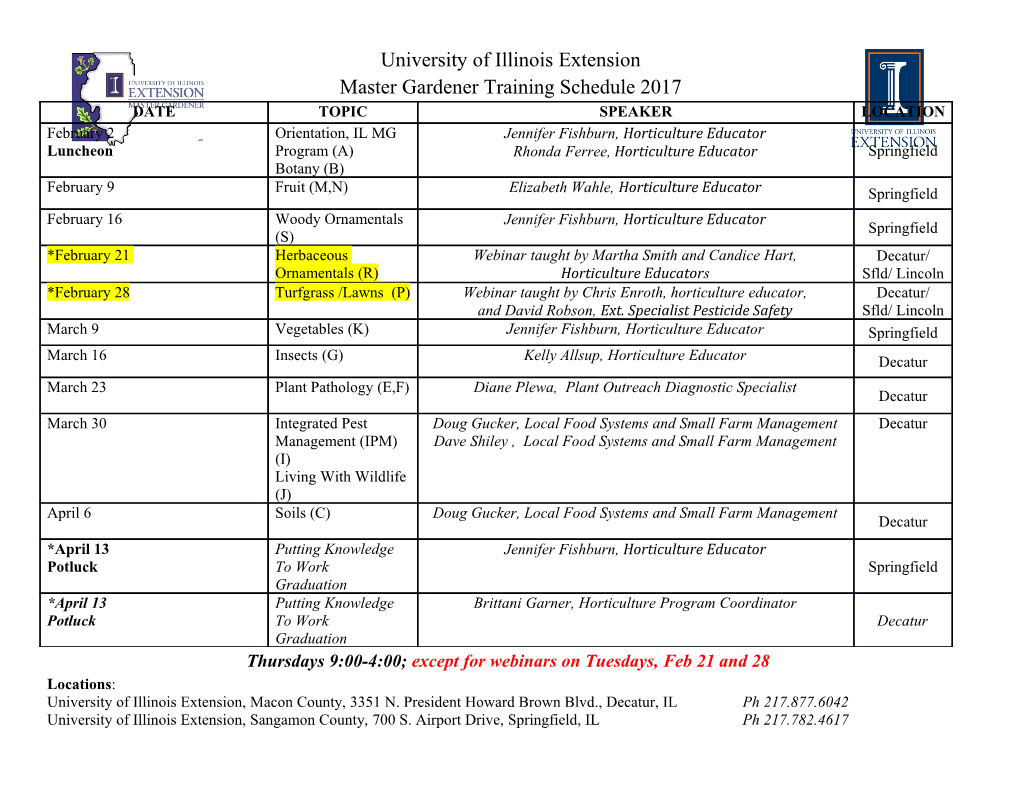
CONVERSION OF SINGLE-SHAFT TURBOPROPA ENGINE TO TWO-SHAFT INDUSTRIAL TURBil\"E A by Gas Turbine.J. D.Marketing_ Horth Manager Ingersoll-Rand Co. Phillipsburg, N.J. compared to th e more common practice of relating re­ fohn Harth r_;raduated from Car­ duced te mperatures measured further along in the ex­ negie Tech with a B.S. in pansion cycle. There are thirty-two thermocouple J/echanical Engineering.in 1943 Fallow in g elements arranged in groups of two 132) the output of service in the Corp of Enr_;ineers in which is avera!!ed to the engine (2),tu rbine inlet � � tem- II, he has spent more than twen­ perature ITIT)� !rive ty-fiveWW years in the design, ap­ plication( 25) and m arketing of Turbo­ The four turbine stages of the aircraft engine machinery. During this time, he was are a single assem( ..J.)bly, the power from which is transmit­ instrumental in the introduction of led forward. That not used for compressor section the T-56 aircraft engine to i dustrial is available for mechanical work atthe the front end through service, and its later conv ersnion to a the torque tube system. The assemblY of the turbine two-shaft model-the subject of this paper is cur· section is held together by through-bolts but torque is ently Turbine Marketing Manager for. HeIngersoll­ transmitted through curvic coupling interfaces. Randr Company.Gas This engine was one of the first to employ internally cooled blades. Both the first stage nozzle and the first The GT-40 two-shaft industrial turbine is a direct rotating stage have this feature. The construction of off-spring of the T-56 Turbo Prop single shaft engine. these elements are shown in Figs. 2 and 3. This widely used aircraft power plant is illustrated in Fig. l. In the aircraft engine, roller bearings a;e provided As an aircraft power system, the T-56 consists of to support the turbine elemen t on each end. the turbine itself, a torque meter, gearbox and impeller. At the inlet end of the compressor section, four ( 4) This assembly has a takeoff rating at 60°F and sea level, pads are provided for shaft driven auxiliaries. These are of 5150 mechanical horsepower plus 800 pounds of jet gear driven from the shaft through the struts in the inlet thrust. As an aircraft engine, it is, of course, designed housing. for \vide versatility in terms of ambient pressure and temperature extremes from Arctic to Desert climates. The T-56 has a 14-stage compressor desigend for 32 lbs/sec of air at sea level and 60°F inlet and with a pressure ratio of 8.5:1. To maintain compressor stability at startup, bleeds are provided at the 5th and lOth stages. These are to be noted since they are significant for the conversion to an industrial turbine, as will be discussed later. Six ( 6) cannular combustion chambers are provided and these are designed for operating turbine inlet tern· COOLING peratures up to l970°F during take-off. AIR OUT An interesting feature of this engine is the use of direct reading thermocouples at the combustor outlet, as Figure 1. Model T56-A-15 Tu bo prop Engine Appli­ a ion r . Figure 2. Vane Cooling Schematic. c t C-130. 20 CO:\YERSIO:\ OF A. :3!:\GLE-.SIL\FT TCRBOPROP E:\GI:\E craft auxiliarv ,·omponents. addition uf i ustri l :c:o\·ernor .mel den:'lopment of a :.:as iuel '"·steanm tond replacea the aircrartliqui d fuel �\ :'tenL ln these applications. the c· n!.>:ine ,- ,·rtlinued lo dri\·e throu:.:it the t o rque meter. pro· \ · idin g ito power to industrial machiner�· instead of the p ropelle r . Ingersoll-Rand. as a manufac turer of compressors and pumps. has been emploving aircraft derivati\·e tur­ bines to drive their products in industrial service for a number of years. In thev sought a ISO v horsepo11·er industrial prillJme/0. move-r. and made 4000a compr e­ hensive review of the aircraft engines available that might be emploved. The T-56 had established the outstanding record of operating in industrial service in excess of :)0.000 hours without overhaul. and thereby appeared to highlv qualified for the purpose intended. It suffered befro m one handicap however-the fact that it was a single shaft engine. This limited its usefulness in two (2) ways : l. Speed \ ariation was onh· 12/L 2. .-\s a sinde shaft engine. it could not be used for a p plicati ons ;uch as liq�id pumps that require a high starting torque capabilitY. �lanv of the potential uses for a ri ver in this size range are in liquid pump· ing, such asd oil pipelines. A detailed study of the T-56 revealed that bv fortunate coin cidence the thermody­ Figure 3. Turbin e namics of the r;ower secion of the turbine split almo.s t Air-Cooled Blade. perfecth· between the 2nd and ::lrd turbine stages. In other 11·ords, the power of the first two stages was ade­ quate for driving the compressor section and the power The T-56 engine completed initial tests and went in to of the 3rd and 4th stages was available as mechanical production in 1956. Since then, more than units shaft output. D DAD was, therefore, approached for a have been built by Detroit Diesel Allison, 10Div.000ision of program of modifying the engine, and agreement was General Motors (DDADl . These power such craft as the reached between the two companies in June of 1970 to Lockeed Electra, Hercules and PB-3 shown in Fig. 4-. proceed with a joint development. The resultant engine By 1963, this engine had demonstrated high reli­ is shown in Fig. 5. As will be noted, it appears remark­ abilitv as an aircraft propulsion unit and the manufac­ ably like the original T-56. The same compressor, com­ turer decided to offer it for industrial service. It was. bustors and turbine rotor elements are used in both. therefore, introduced into gas pipeline and electric gen � In fact. in the critical aero-dmamic cascade the only erator applications in the original single shaft version . changes are: (a.) A two-degree alteration of the 3rd stage Changes at that time were limited to removal of the air- vane angle ; and (b.) An increase in the stage spacing between the 2nd and 3rd turbine stages of less than lJ:! ". The power turbine takes the 3rd and 4th turbine wheels from the T-56 and moun ts them in an overhung configuration from a separate shaft. The wheels ar� joined by through-bolts as before. and torque is carried through curvic connections. This required the addition of a cun·ic element on the back of the last turbine wheel and removal of the same element from the 2nd and 3rd stage interface. The wheel assemblies and the stator elements continue to be made by DDAD to minimize : I hardware change and to take advantage of quantity pro­ - _ ·I '- , duction. i ' The power turbine rotor is mounted on two (2) tilting shoe radial bearings in a conventional manner, and a Kingsbury thrust is provided. Outboard of the thrust bearing, a gear system is built in for driving auxiliaries. These consist of lube oil, compressor seal oil and hydraulic service gear pumps. The gas generator now referred to as the 501-K16 is bolted by external flanges to the power turbine. Trun- · nions on the power turbine casing provide the main sup­ port for the turbine through a mounting pedestal as illustrated in Fig. 6. Further support is provided above Figure 4. T-56 Applications. the gas generator center of gravitv by a flexible hanger, PROCEEDI:l'<GS OF THE SECO::\D T"CRBO:\IACHI::\ERY SY:\IPOSI"C:\I POWER TURBINE EXHAUST TWO·STAGE POWU TURBINE Con Be Rotated for flel.bility . Pro�n Design-Centerline Support) Of COUPliNG CONTIHUOUSLV lUBRICATED ACCESSORY GEAR BOX FUEL METERING VAlVE ACCESSORY DRIVE GEAiOOX CURVK COUI'tiiiG CCM!IfcnON FOI LUll SEAl PUMPS BETWHH DISCS & SHAFT & HYDUULK ( 5. Figure GT--f.O Gas Turbine. its purpose being to carry weight only and allow com­ ports are manifolded to a single modulating valve for plete freedom of movement. Within the power tu rbine. each of the two ( 21 stages at which bleed takes place. the bearing assembly at the hot end is supported from The modulating valves are scheduled as a function of the casing by a system of struts attached tangentially to RPM and compressor inlet temperature. The range of the bearing casing. The rear bearing is essentially sup­ full op�n to full close is approximately 900 RPM as ported by a flexible plate mounted under the avxiliary illustrated in Fig. 8. The full gas generator operating �ear casin !r. The turbin e diffuser an d exhaust collector speed range is from 10,000 to l-1-,500 RPM correspond­ �re suppo;ted by struts from the inter-bearin� housing ing to a 1000 to 1-J.,SOO RPM range for the power in the se�tion surroundin g the th rust bearin g. turbine. Because the output drive is now taken from the left The gas generator lube system, combustors and end of the turbine rather than from the front. the me­ thermocouples remain unchanged from the T-56. The ;_.. ·.. · ch anical ou tput th rough the gas generator nose has been gas generator turbine blading is unaltered from the T-56 removed. This simply meant leaving off the torque tube and the only significant change in this area is in the and adding a small nose cone to cover the openin�.
Details
-
File Typepdf
-
Upload Time-
-
Content LanguagesEnglish
-
Upload UserAnonymous/Not logged-in
-
File Pages9 Page
-
File Size-