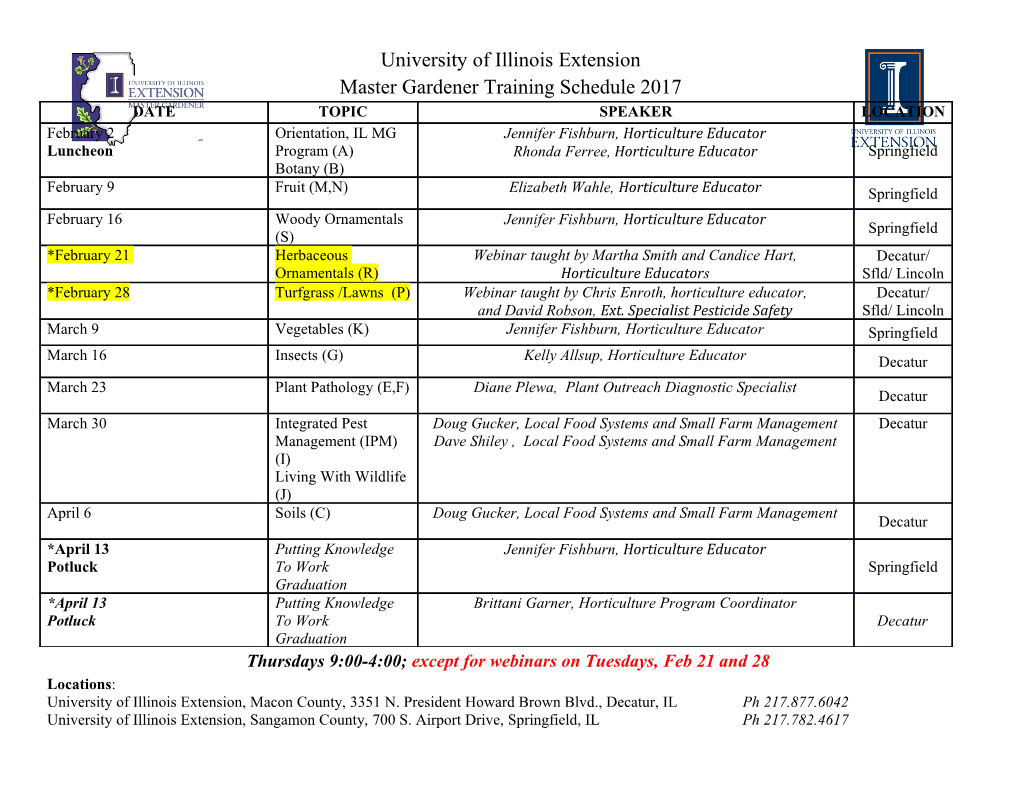
DRILLING OFFICIAL MAGAZINE OF THE INTERNATIONAL ASSOCIATION OF DRILLING CONTRACTORS Drilling CONTRACTOR MARCH/APRIL 2012 WWW.DRILLINGCONTRACTOR.ORG CONTRACTOR ShaleFracturing With each lesson learned, industry evolving practices, WWW.DRILLINGCONTRACTOR.ORG technologies to enhance efficiency, reduce impact MARCH/APRIL ALL DRILLING • ALL COMPLETIONS • ALL THE TIME 2012 INNOVATING WHILE Dual-gradient drilling set to help IADC’S NEW PRESIDENT Stephen Colville undertakes industry navigate deepwater’s strategic review to map out DRILLING precarious pressure zones IADC’s key goals for the future DC Mar12 COVER indd 3 3/2/2012 12:55:30 PM Completions: Shale Fracturing REPRINTED FROM THE MARCH/APRIL 2012 EDITION OF DRILLING CONTRACTOR MAGAZINE Completions: Shale Fracturing What the shales have taught us From Barnett to Bakken, lessons learned about hydraulic fracturing have pushed unconventional production to levels once considered impossible BY KATIE MAZEROV, CONTRIBUTING EDITOR hen the industry cracked the code on shales, it changed the landscape, delivering production levels that were unlocked a wealth of unconventional resources, intro- unattainable five years ago. W duced new methods of drilling and completions, and “In the early days of post-Barnett gas shale development, made “fracturing” a household word. Technology sparked the the tendency was to say, ‘If it worked in the Haynesville or shale boom that began a decade ago in the dry gas reservoirs of the Barnett, it ought to work here,’ but that was not neces- the Barnett play, and then moved to Haynesville, Marcellus and sarily the case,” Scott Nelson, director of engineering for US others. Technology has continued to drive the current migration Land Pressure Pumping for Baker Hughes, said. “Often, the into the oil and liquids-rich Bakken and Eagle Ford plays, with technologies that were developed and refined in the Barnett new and extremely prolific basins continually being discovered. just didn’t fit other plays because they had different reservoir However, along the winding road of shale production, the properties – the rock was not as brittle or as hard, or the pore industry has learned many important lessons, not the least of structure was different. So, it’s important to assess the res- which is this: Fracturing methods that work in one play may not ervoir properties in these plays before we design a fracturing yield success in another. treatment.” While that fundamental truth may seem obvious now, it wasn’t always so. Over the years, operators and service companies have developed an extensive arsenal of tools and knowledge Left: Marathon Oil entered the Niobrara’s Denver/Julesburg they can call on when embarking on a new fracturing operation. basin in 2010. The emerging Niobrara is described as having Greater understanding of the geologic properties of reservoirs, tight, layered chalk and marlstone with some natural frac- enhanced well architecture, improvements in drilling, multi-well turing, where hydraulic fracturing methods can be applied. pads and developments in fluid and proppant technologies have Pictured is an H&P FlexRig. REPRINTED FROM THE MARCH/APRIL 2012 EDITION OF DRILLING CONTRACTOR MAGAZINE Completions: Shale Fracturing Left: Baker Hughes’ IntelliFrac service validates reservoir modeling and supports the company’s “Understand the Reservoir First” philosophy. It combines microseismic services and pumping knowledge. Right: Baker Hughes utilizes different tech- niques and technologies for fracture treatments based on reservoir properties. The company’s operations in the oil-rich reservoirs of the Eagle Ford and Bakken require more complicated fracturing fluids than needed for gas shales. That approach is the embodiment of the company’s Ultra-lightweight proppants and fluids also have been “Understand the Reservoir First” philosophy – one that first enhanced and are used in the more oily plays to achieve greater examines the geological and geomechanical characteristics of conductivity. “We must have good conductivity in fracturing the reservoir and its bounding beds. Gas shales, for example, to produce that liquid,” explained Harold Brannon, Baker are typically mudstone rocks defined by their particle size, and Hughes’ vice president of technology for Pressure Pumping. have varying percentages of clay, carbonate and silica content, “Gas is more mobile than liquid, so in the Bakken, for example, explained Randy LaFollette, director of applied reservoir we need to use higher-viscosity fluids to achieve wider frac- technology for Baker Hughes’ Pressure Pumping division. The tures, and we need a larger proppant size to deliver the higher Bakken oil play is geologically dissimilar, as it may be either a conductivity.” siltstone with high carbonate content or a crystalline carbonate Baker Hughes’ LiteProp ultra-lightweight proppants (UWLPs) rock, depending on where it is geographically in the basin. are neutrally buoyant, low-density materials that are slightly “It begins with understanding what we have in terms of heavier than fresh water but considerably less dense than matrix permeability and the degree of natural fracturing per- sand. They can be placed throughout the induced fracture to meability, combined with the character of the oil, which drives enhance production with greater conductivity. “Slick-water flu- the mobility,” Mr LaFollette said. “That determines whether we ids drop all the proppant to the bottom of the fractures. But, the need shorter, more highly conductive hydraulic fractures or ultra-lightweight proppants can be transported deeper into the much longer and less conductive fractures. Once we understand reservoir prop fractures to greater vertical height and provide a the basic reservoir properties, we have a better understanding better flow of hydrocarbons,” Mr Nelson explained. of the issues and we can bring in the appropriate technologies.” Over the years, there has also been considerable develop- ment in completion architecture technologies, such as packer A LEARNING CURVE and sleeve configurations that can allow more zones to be Many of the fracturing techniques used in the gas shales isolated and treated, Mr Brannon noted. “We used to do six or were based on slick-water technology and sand, he continued. eight intervals per well, but with enhanced packer and sleeve “But as we have moved into more oil-rich reservoirs, such as systems, we can get as high as 40 intervals with telescoping the Eagle Ford and the Bakken, we are pumping more compli- port systems, extending the stage count even farther,” he said. cated fracturing fluids to carry larger-mesh sand grains. And And the technology is still advancing. “In the oil shales, we when we begin operating in some of these newer plays, such have operators completing more discrete intervals in laterals as as the Utica in Ohio, there will be another learning curve. We long as 5,000 ft,” he added. “The more segments we can fracture will have to model the Utica to determine the fracturing tech- individually, the better the well performs.” nologies required to address the stimulation needs of those Going forward, the emphasis will be on improving the char- reservoirs.” Baker Hughes’ IntelliFrac service, which combines acterizations of the laterals themselves to increase production. microseismic services and pumping knowledge, can validate the “Very few laterals are actually logged now,” Mr LaFollette said. modeling. “But we are using logging while drilling (LWD) technology REPRINTED FROM THE MARCH/APRIL 2012 EDITION OF DRILLING CONTRACTOR MAGAZINE Completions: Shale Fracturing extensively in one gas play to characterize the natural frac- tures, as well as the offset well hydraulic fractures along the full length of the lateral. This way, the operator can design a completion to target specific rock types and fracture patterns, avoiding the offset well fractures.” He notes that this technology hasn’t transitioned to the oily plays yet but has potential there. ROOTS OF FRACTURING Fracturing and stimulation may date back to the 1940s but development of the methods used today goes back to the ini- tial shale research efforts sponsored by the US Department of Energy and the Gas Research Institute in the late 1980s and early 1990s in the Lower Huron play that underlies south- eastern Ohio, West Virginia and northern Kentucky, explained Matthew Blauch, director of product development for Superior Well Services, a subsidiary of Nabors Drilling. “At that time, the concept of fracturing was perceived as creating a single-plane fracture. The idea of creating multiple fractures, and fracture swarms and networks, went against the grain of that model,” Mr Blauch said. But through microseismic studies of the fracture systems created by Mother Nature, the industry evolved. “It wasn’t until we started doing horizontal drilling and mul- tistage fracturing that we learned we want to create more com- plex fractures because that is what gives us the surface area we need to develop these reservoirs efficiently, cost-effectively and surgically – putting the fracture networks where they need to be,” he said. That early learning in vertical wells in the Lower Huron was taken to the Barnett play, which became a “springboard” for the key technologies that enable the level of shale production being undertaken today. “The Barnett learning curve spanned a long time frame,” Mr Blauch said. While there are key differences in producing dry gas plays versus liquids-rich reservoirs – especially regarding the use of proppants
Details
-
File Typepdf
-
Upload Time-
-
Content LanguagesEnglish
-
Upload UserAnonymous/Not logged-in
-
File Pages7 Page
-
File Size-