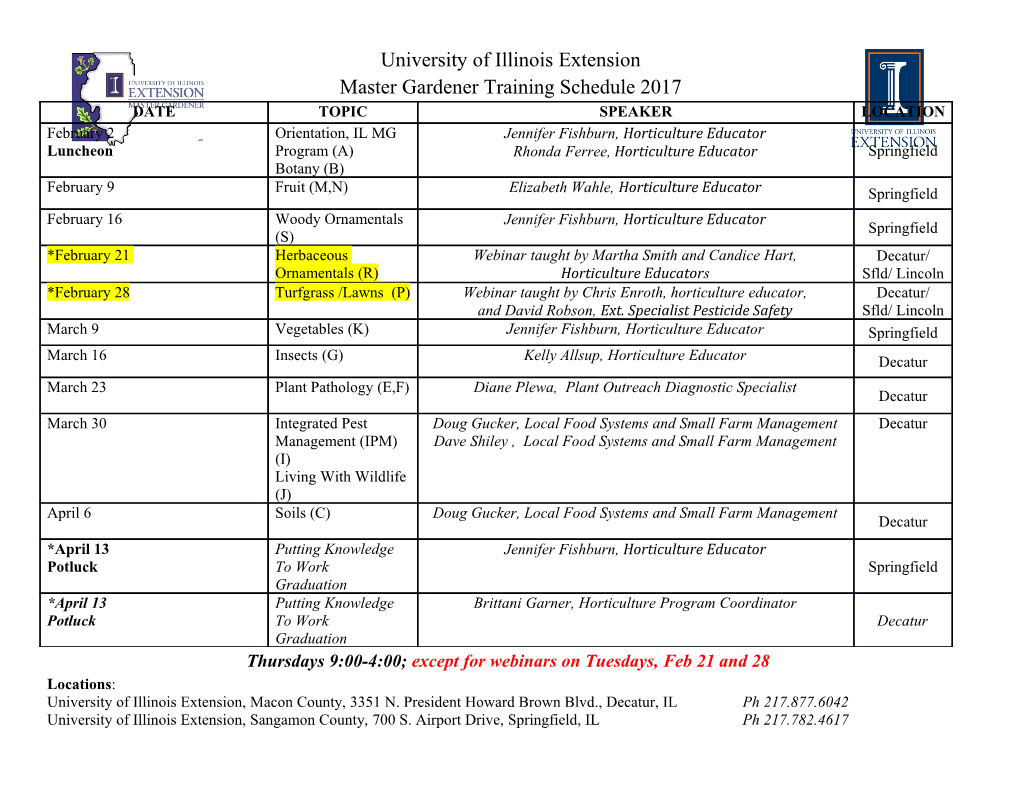
Heat Treating Metallurgical ‘Fine Points’ of Induction Hardening Valery Rudnev, Inductoheat Group, Madison Heights, Mich. Certain metallurgical phenomena and principles of heat treatment fre- quently are incorrectly assumed or improperly used in the application of induction hardening. ardening of steels and cast distribution in induction surface hardening for surface hardening. After 4.1 seconds of irons represents the most is controlled by selection of frequency, time, heating, the surface layer reaches a final popular application of induc- power and workpiece/coil geometry [1]. temperature of approximately 1050˚C tion heat treatment (Fig. 1). Hardening of steels and cast iron compo- (1920˚F). The core temperature does not Induction hardening is a complex combina- nents may be done for the purpose of rise significantly due to several factors, such tion of electromagnetic, heat transfer, and obtaining certain properties including, but as an electromagnetic skin effect and rela- metallurgical phenomena [1]. Due to the not limited to, strength, fatigue and wear tively short heating time. Because of these physics of electromagnetic induction, heat- resistance. The traditional description of factors, the heat soak from the surface ing can be localized to areas where metal- the steel hardening procedure involves toward the core is not sufficient to equalize lurgical changes are desired. The three most heating the entire component, or a part of temperature along the radius. common forms of induction hardening are the component that needs to be hardened, After the heating stage is completed, the surface hardening, through hardening, and to the austenitizing temperature, holding it quenching stage begins. The high tempera- selective hardening. Depending on the spe- if necessary for a period long enough to ture of the workpiece surface layer begins to cific application, selective hardening is achieve complete transformation to austen- decrease in the first stage of quenching. sometimes considered a part of surface hard- ite, and then rapidly cooling it below the Figure 2 shows that after 2 seconds of ening or through hardening. martensite start (Ms) temperature, where quenching, the surface temperature is The first step in designing an induction- martensite transformation begins. reduced by as much as 450˚C (810˚F), hardening machine is to specify the required For example, Fig. 2 shows the dynamics resulting in a workpiece surface temperature hardness pattern including surface hardness, of the induction heating of a carbon steel of 600˚C (1110˚F). At this point, the maxi- case depth and transition zone. Temperature cylinder and its cooling during quenching mum temperature is located at a distance of 3 mm (0.120 in.) below the surface. After 5 seconds of quenching, the surface tempera- ture decreases almost to the temperature of Core Surface 1200 4.1 Sec. 1000 3.2 Sec. 800 1 Sec. 1.8 Sec. 600 1.5 Sec. 400 Quenching Temperature, ˚C Temperature, 2 Sec. 200 0 6 Sec. 0246810 Radius, mm Fig. 2. Dynamics of induction heating of a car- bon steel cylinder (20 mm OD) and its cool- ing during quenching (F = 40 kHz) [1]; red is Fig. 1. Dual shaft induction scanner heating and blue is cooling. IndustrialHeating.com – March 2005 1 Heat Treating 1200 2192˚F 1100 E Austenite 910˚C Annealed steel 1100 ( -Fe) 2012˚F γ 1670˚F Austenite 1050 ( -Fe) A''3 γ Normalied steel 1000 Acm 1832˚F 1000 G v''>v'>v' Quenched and tempered 900 1652˚F A'cm Austenite (γ-Fe) 950 + Cementite (Fe C) 800 Austenite 3 1472˚F Ferrite A 723˚C (1333˚F) ˚C Temperature, 900 1 1292˚F 700 P S Eutectoid Temperature, ˚C Temperature, 850 Ferrite 600 Ferrite (α-Fe) Cementite (Fe3C) 1112˚F + Perlite + Perlite (α-Fe) Perlite 500 932˚F 800 0 0.2 0.4 0.6 0.8 1.0 1.2 1.4 1.6 1.8 2.0 100 1000 Carbon content, weight % Rate of heating, ˚C/sec Fig. 3. Lower left portion of the iron-iron carbide equilibrium phase trans- Fig. 4. Effect of initial microstructure and heating rate on A3 crit- formation diagram ical temperature for AISI type 1042 steel [3,4] the quenchant, while the core still remains the effect of heating the metal to elevated composition and the heating/cooling rate. quite warm at a temperature above 400˚C temperatures or metal cooling that causes a The greater the rate of heating/cooling, the (750˚F). transformation in its crystalline structure. It greater will be the difference between the Ac In some cases, heat treaters do not cool is also used to determine the range of tem- and Ar temperatures. the part completely, and after unloading the peratures in which certain types of heat Induction hardening is a very fast part from the induction coil, it is kept for treatment of the steel may be carried out. process. Heat intensity often exceeds a mag- some time on the shop floor. During that Often, heat treat practitioners use this dia- nitude of 100˚C/sec (180˚F/sec), and in time, the heat of the warm core travels gram to determine hardening temperatures. some cases reaches 900˚C/sec (1620˚F/sec) toward the surface, eventually resulting in a However, it is important to be aware that and even higher. Therefore, the process of uniform temperature distribution within the this diagram might be misleading in majori- phase transformation cannot be considered part. In this case, the remaining heat is used ty of induction hardening applications as equilibrium, and the phenomenon of for a slight temper back (self-tempering), because it is valid only for the equilibrium thermal hysteresis is always pronounced. which imparts some ductility to the part. condition of plain carbon steel at a pressure Fast heating drastically affects the kinet- At first glance, this operation is very of one atmosphere. The existence of non- ics of the austenite formation, shifting it straightforward. However, in many cases, equilibrium conditions, appreciable toward higher temperatures to create suffi- certain metallurgical phenomena and prin- amounts of alloying elements, pressure cient conditions for the required diffusion- ciples of heat treatment frequently are other than atmospheric and certain prior based processes [2]. Figure 4 shows the effect incorrectly assumed or improperly used in treatment can significantly shift the critical of the heating rate on the Ac3 critical tem- induction hardening. It is important to look temperatures. peratures of steel [3, 4]. The inability of the closer at the “fine points” of metallurgical One of the major requirements of an classical Fe-Fe3C diagram to take into con- theory to ensure optimal results. Following equilibrium condition is sufficiently slow sideration heating intensity noticeably lim- are some examples that illustrate this. heating. Ideally, for sufficiently slow heat- its its use to predict required temperatures in ing/cooling, transformation temperatures induction hardening applications. Can you directly apply the iron-iron should be approximately the same in heat- The microstructure of steel prior to heat carbide (Fe-Fe3C) equilibrium phase- ing as well as in cooling resulting in no treatment (sometimes referred to as initial transformation diagram to induction appreciable difference between the Ac and structure, structure of the parent material, hardening of steel? Ar critical temperatures. However, from a and structure of the “green” part) also has a When iron is alloyed with a different per- practical standpoint, the equilibrium condi- pronounced effect on the results of the heat cent of carbon, the critical temperatures tion simply does not exist in induction treatment and required process parameters. often are determined based on the Fe-Fe3C hardening. This includes, but is not limited to, the diagram. Figure 3 shows the lower left-hand The Ac temperatures are always higher austenitizing temperature and the time part of this diagram representing the heat than Ar temperatures. The difference required to hold at that temperature. treatment of steels. This widely used dia- between Ac and Ar temperatures represents As can be seen from Fig. 4, even for gram represents a graph of temperature ver- a thermal hysteresis, which is a function of induction hardening of AISI 1042 plain car- sus carbon content of the steel and shows several factors including the metal chemical bon steel, depending on the heat intensity 2 March 2005 – IndustrialHeating.com 0mm 0.5mm 1mm 1.5mm 2mm 2.5mm 800 70 Eutectoid temperature γ––> Pearlite 700 60 Quenched and Coarse pearlite tempered Transformation 600 50 ends Fine pearlite + Fe C Normalized 500 α 3 40 Upper bainite 400 γ––> Bainite 30 Transformation –– Hardness < Hardness, HRC Low bainite 300 begins 20 Annealed ˚C Temperature, 50% Ms 10 200 100 0 γ––> Martensite 0 0.02 0.04 0.06 0.08 0.1 M90% M50% Distance below surface, in. 0 Surface 1 10 100 10000 10000 Time, sec. Fig. 5. Effect of initial microstructure in AISI type 1070 steel bars on response to surface hardening using 450-kHz induction generator Fig. 6.Time-temperature isothermal transformation diagram for AISI operated at a power density of 2.5 kW/cm2 (16 kW/in.2) [5] type 1020 plain carbon steel, austenitized at 900˚C; grain size: 6 [3,7] and structure prior to induction hardening, the ferrite. The ferrite clusters or bands can Can time-temperature-transformation the required hardening temperatures range function as one large ferrite grain and often (TTT) and continuous-cooling-trans- from 1620 to 2000˚F (880 to 1095˚C) for will be retained in the austenite upon fast formation (CCT) diagrams be directly annealed prior microstructures, 1550 to heat up [1]. After quenching, a complex fer- applied in induction hardening? 1830˚F (840 to 1000˚C) for normalized ritic-martensitic microstructure can be TTT and CCT diagrams are widely used in prior microstructures and 1510 to 1710˚F formed.
Details
-
File Typepdf
-
Upload Time-
-
Content LanguagesEnglish
-
Upload UserAnonymous/Not logged-in
-
File Pages5 Page
-
File Size-