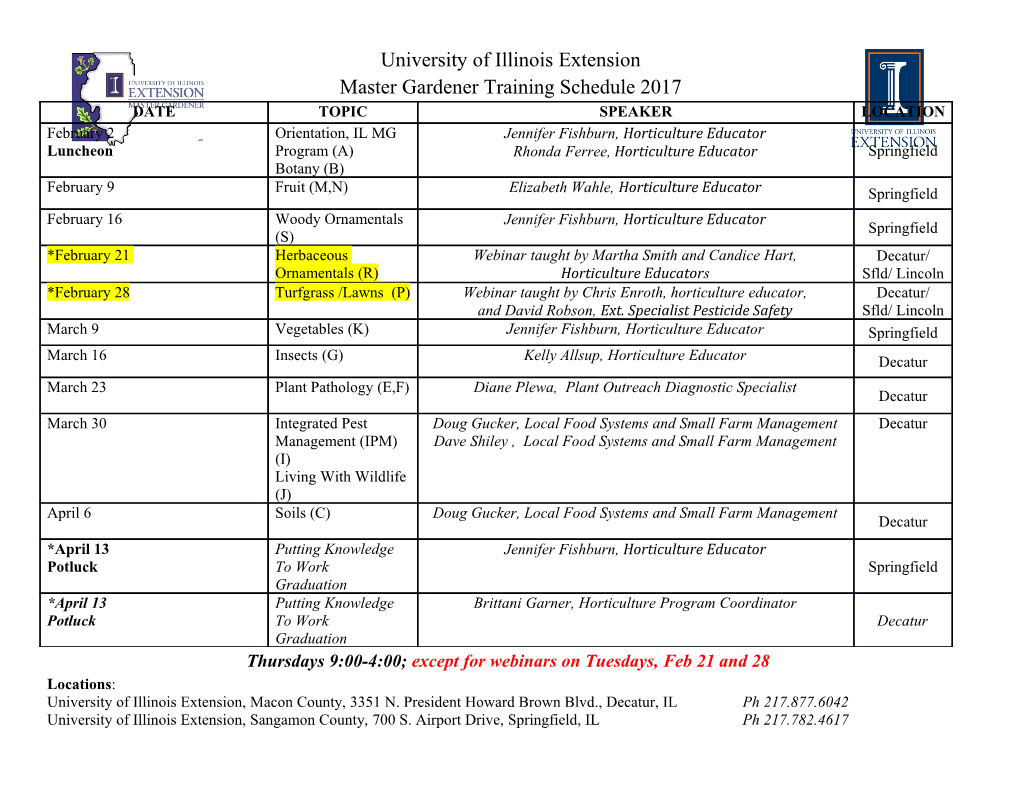
Sheet Metal Forming—Fundamentals Copyright © 2012 ASM International® T. Altan and A.E. Tekkaya, editors All rights reserved www.asminternational.org CHAPTER 7 Friction and Lubrication Hyunok Kim, Edison Welding Institute Nimet Kardes, The Ohio State University FRICTION AND lubrication in sheet selecting lubricants and producing good-quality metal forming are influenced by such parame- sheet metal parts. In sheet metal forming, the ters as material properties, surface finish, tem- magnitude and distribution of friction affect perature, sliding velocity, contact pressure, and metal flow, part defects, and quality, as well as lubricant characteristics. The parameters that tool wear and production costs. affect friction and lubrication are schematically shown in Fig. 7.1. Depending on these parame- ters, the performance of a lubricant and the co- 7.1 Lubrication Mechanisms and efficient of friction (COF) vary. Material flow in the die cavity is influenced Friction Laws by frictional conditions at the die/work piece in- terface. Therefore, a good understanding of the In metal forming, different lubrication mech- parameters that affect friction is essential for anisms may be present: Fig. 7.1 Factors that affect friction and lubrication in sheet metal forming. Ultimate tensile strength (UTS) 90 / Sheet Metal Forming—Fundamentals • Dry condition Boundary lubrication is the most widely encoun- • Boundary lubrication tered lubrication condition in metal forming. • Mixed-film lubrication Mixed-layer lubrication (Fig. 7.2) is also fre- • Hydrodynamic lubrication quently encountered in sheet metal forming. In this case, the micropeaks of the metal surface As shown in Fig. 7.2, the Stribeck curve illus- experience boundary lubrication conditions and trates schematically the onset of various types the microvalleys of the metal surface become of lubrication mechanisms as a function of lu- filled with the lubricant. Hydrodynamic lubri- bricant viscosity, η, sliding velocity, v, and nor- cation (Fig. 7.2) is experienced in a few sheet mal pressure, p (Ref 7.1). metal forming processes, such as high-speed A dry condition (Fig. 7.2) means no lubrica- sheet rolling operations, where large velocities tion is present at the mating surfaces; thus, fric- at the material-tool interface create hydrody- tion is high. This condition is often used when namic conditions. the material formability is large enough to form Coulomb, Tresca, and Modified Shear a part with simple geometry without lubricants Friction Models. Two friction models are com- or when the frictional condition does not signifi- monly used to describe the frictional condition in cantly influence the part quality, for instance, air metal forming processes: Coulomb’s friction bending, V-die bending, and U-die bending model (Eq 7.1) and the shear friction model (Eq without stretching. A dry condition is desirable 7.2). Both models quantify interface friction by in only a few selected forming operations, such lumping all of the interface phenomena, which as hot rolling of plates or slabs and nonlubri- are illustrated in Fig. 7.1 into a nondimensional cated extrusion of aluminum alloys. coefficient or factor: Boundary lubrication (Fig. 7.2) is defined as a condition where the solid surfaces are so close τµf = p (Eq 7.1) together that surface interaction between single or multimolecular films of lubricants and the where μ is the coefficient of friction (COF), p is solid asperities dominates the contact (Ref 7.2). the normal pressure, and τf is the frictional shear Fig. 7.2 Stribeck curve showing onset of various lubrication mechanisms. η, lubricant viscosity; v, sliding velocity; p, normal pres- sure; μ, coefficient of friction. Chapter 7: Friction and Lubrication / 91 stress. In many metal forming processes, the in- where f ′ is the modified friction factor, mr is the terface pressure, p, can reach a multiple of the modified shear factor (as a function of real con- yield strength of the material. Thus, the linear tact area), σ is the flow stress, and α is the real relationship between τf and p, as described by contact area ratio, Ar /Aa. In this model, the fric- Eq 7.1, may not be valid at high contact pres- tion shear stress, τf , is a function of the real con- sure levels because the shear stress, τf, cannot tact area ratio, α. exceed the shear strength, k, of the deformed Wanheim and Bay’s model did not consider work piece material. Therefore, the COF be- the effects of lubricant behavior (Ref 7.6). To comes meaningless when μp exceeds τf. Thus, take lubricant effects into account, a complex to avoid this limitation of Coulomb’s model, the model for friction was proposed for boundary shear friction model (Eq 7.2) was proposed by and mixed-film lubrication regimes at the tool/ Orowan (Ref 7.3): work piece interface by Bowden and Tabor (Ref 7.7). In this model the frictional shear stress, τf , σ is given by: τσf ==fm= mk (Eq 7.2) 3 ταfa=+τα()1− τ b (Eq 7.4) where f is the friction factor; m is the shear fac- tor, 0 ≤ m ≤ 1; k is the shear strength; and σ is the flow stress of the deforming material. In this where α is the real contact area ratio, τa is the model, as shown in Fig. 7.3, the frictional shear average shear stress at contacting asperity peaks, stress, τf , at low pressure is proportional to the and τb is the average shear stress (lower stress) normal pressure given by Coulomb’s model. at the lubricant pockets. This model explicitly However, it equals the shear strength, k, at high formulates the real contact area ratio, α, related interface pressure, p. to τa and the lubricant behavior related to τb that In Eq 7.2, m equals to zero for no friction, is influenced by viscosity, pressure, sliding and m equals to unity for a sticking friction con- speed, and film thickness. dition, which is the case where sliding at the If there is no lubricant at the tool/work piece interface is preempted by shearing of the base interface, τb will be zero and the frictional shear material (Ref 7.1). When two nominally flat stress, τf , will be a function of real contact area surfaces are placed in contact, surface rough- ratio, as expressed in Eq 7.3. To take into ac- ness causes discrete contact spots. The total area count the lubricant behavior on friction, an arti- of all these discrete contact spots constitutes the ficial lubricant film was assumed to exist at the real contact area, Ar , and in most cases this will tool/work piece interface, and the variation of be only a fraction of the apparent contact area, film thickness was calculated to characterize the Aa. The ratio of the real contact area, Ar , to the variation of friction using the Reynolds equa- apparent contact area, Aa, is known as the real tion in the fluid mechanics theory (Ref 7.6). Al- contact area ratio, α. To consider the effect of though this approach includes more detailed real contact area ratio, α, on friction, Wanheim, considerations to express the lubricant behavior, Bay, and colleagues (Ref 7.4, 7.5) proposed a the model is very difficult to apply to practical general friction model: metal forming problems. σ ταfr==fk′ m (Eq 7.3) 3 7.2 Lubricants for Sheet Metal Forming In selecting lubricants for sheet metal form- ing process, the following factors should be considered (Ref 7.8): • Methods of lubricant application • Types of additives • Corrosion control • Cleanliness and removal methods • Fig. 7.3 Relationship between contact pressure and fric- Compatibility with prelubricants and preap- tional shear stress plied oils 92 / Sheet Metal Forming—Fundamentals • Post-metal forming operations (e.g., welding trolled pressure, allowing precise control of and adhesive joining) the amount of lubricant applied • Environmental safety and recycling • Electro-Deposition: Lubricant deposited on the panel surface using electric charge; used Types of Lubricants (Ref 7.8) for high-speed applications without any • Oils: Petroleum-based oils are widely used waste of lubricant, but requires high capital as lubricants for light-duty stamping, blank- investment for small stamping shops ing, and coining operations. The use of oil • Airless Spraying: Applies precise amounts can increase the production rate. Paraffinic of lubricant to local areas, with minimal oils and naphthenic oils are examples of waste of lubricant in this method, but does these lubricants. not work with the high-viscosity lubricants • Soluble Oils: Soluble oils contain emulsifi- • Mops and Sponges: Low-cost method still ers that allow the dilution of the oils into used in a lot of small stamping shops to ap- water. These oils are referred as preformed ply lubricants on the panels, which can re- emulsions. These oils are normally mixed sult in excessive waste of lubricants, poor with water at a dilution ratio of 10 to 50%. control of the amount of lubricant, and • Semisynthetics: These lubricants are more sloppy work environment easily mixed with water than soluble oils, Types of Additives. Various types of addi- because they contain a smaller amount of tives enhance the performance of lubricants. mineral oil, usually less than 30% of the to- The extreme pressure (EP) additives are com- tal concentrate volume. • Synthetics: Synthetic fluids are categorized monly used in heavy-duty metal stamping op- by two types: water based and hydrocarbon erations (Ref 7.8). They are categorized as tem- based. The color of this lubricant normally perature activated and nontemperature activated. is hazy or milky. The temperature-activated EP additives, such as • Dry-Film Lubricants: Dry-film lubricants chlorine, phosphorus, and sulfur, react as the in- are divided into water-soluble and water- terface temperature increases and generate a free (“hot melt”) categories.
Details
-
File Typepdf
-
Upload Time-
-
Content LanguagesEnglish
-
Upload UserAnonymous/Not logged-in
-
File Pages10 Page
-
File Size-