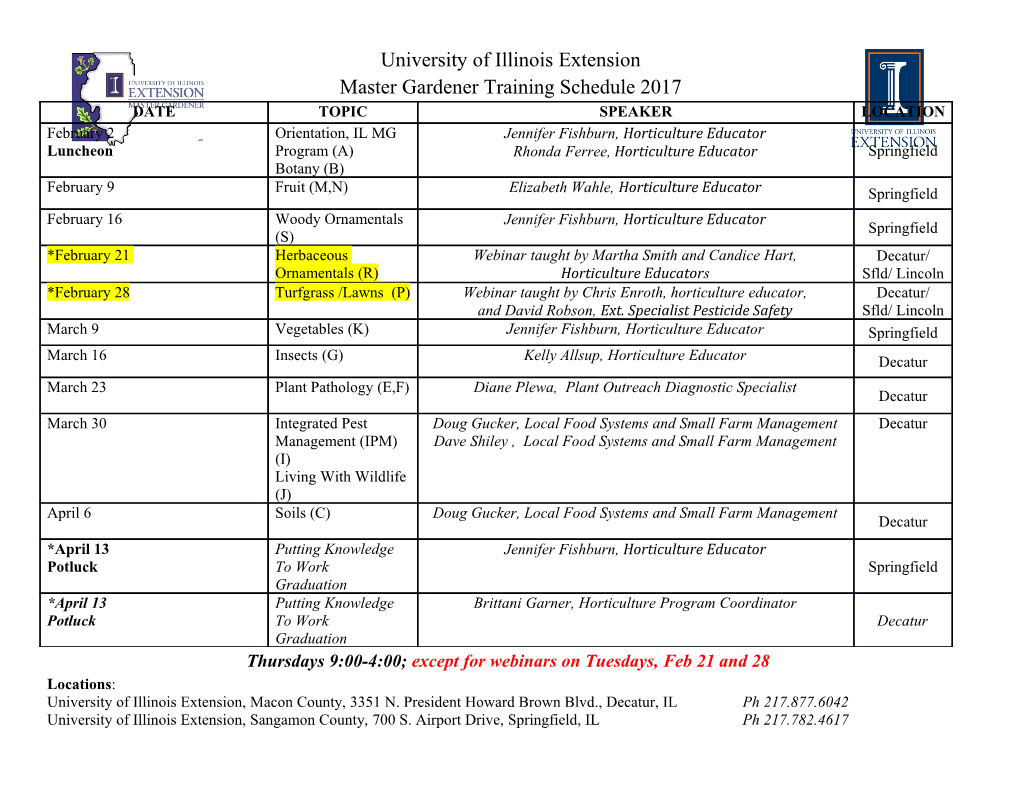
AMEC Oil Sands 2010-001 THE FUTURE OF THE CANADIAN OIL SANDS: ENGINEERING AND PROJECT MANAGEMENT ADVANCES Peter B. Madden* and Jacek D. Morawski† This paper discusses production technology and project management developments in the Canadian oil sands industry, in the context of AMEC’s experience as a consultant and EPCM service provider to lease holders, developers and operators. Mineable and in situ oil sands developments are described, along with methods for and challenges of various production types of in situ, including Cold Flow, Cyclic Steam Stimulation (CSS), Steam Assisted Gravity Drainage (SAGD), Toe to Heel Air Injection (THAI), and VAPEX. Effective project management and supporting systems are critical to achieve cost and schedule targets on large, complex projects performed by AMEC. Workfront planning is essential to achieve optimum construction execution and a best value project. Construction Work Packages (CWPs) divide the work into discrete pieces and the Construction Work Execution Plan influences scheduling of engineering and procurement deliverables. Integration of the schedules and linking to the required on site (ROS) dates of the CWP scopes minimizes workfront duration requirements, allowing progressive completion of systems. AMEC’s Engineering Data Warehouse (EDW) works with centrally-hosted, intelligent engineering design tools to assist in achieving tight cost and schedule targets. The EDW ensures all information related to a given piece of equipment is consistent across all systems, supporting quality assurance of engineering data between AMEC, its sub-contractors and supervised contractors. Once verified and consolidated, the information becomes part of a Master Tag Register (MTR), improving AMEC’s ability to meet contractual turnover requirements for data quality, completeness and accuracy. Health, safety, security and environmental (HSSE) systems are proactively developed and AMEC’s progressive improvement in safety performance over the years is demonstrated. The improvement is due in part to the company’s Beyond Zero program, designed to achieve sustainable, world-class HSSE performance. INTRODUCTION This paper addresses developments in the Canadian oil sands industry including production technology and project management advances, in the context of AMEC’s experience as a consultant and EPCM service provider to lease holders, developers and * President Oil Sands, AMEC, 900 AMEC Place 801-6th Avenue SW, Calgary, AB, Canada, T2P 3W3. † Engineering Director, AMEC, 900 AMEC Place 801-6th Avenue SW, Calgary, AB, Canada, T2P 3W3. operators of the oil sands. Additionally, the paper addresses the specific areas where AMEC is working with the clients on Oil Sands mega-projects to provide solutions to technological, environmental and commercial challenges. Enhanced project management initiatives and systems that support data management are also addressed. The implementation of these initiatives and systems is accomplished through an integrated completions and commissioning plan with improved accessibility for operations. OIL SANDS BACKGROUND AND FACTS The oil sands accounts for more than 170 billion barrels of the 175 billion barrels of proven oil reserves in Canada that are recoverable with today’s technology. Canada is second only to Saudi Arabia in terms of total volume.1 The reserves are contained in three major areas of northeastern Alberta beneath about 140,000 square kilometers. As of March 2009, approximately 600 square kilometers of land were disturbed by oil sands surface mining activity.2 Approximately 80 per cent of recoverable oil sands can be recovered through in situ production, which has significantly less land disturbance, with the remainder recoverable by mining. In 2008, Alberta produced 213 million barrels (33.9 million cubic meters) from the in situ area and 264 million barrels (42.0 million cubic meters) from the mineable area, totaling 75.9 million cubic meters (477 million barrels), for a total of 1.31 million barrels (207.4 thousand cubic meters) per day. While the bitumen produced from mining was upgraded, bitumen crude produced from in situ operations was mainly marketed as non-upgraded crude bitumen.3 One in 13 jobs in Alberta is directly related to energy and every dollar invested in the oil sands creates about $9 worth of economic activity, with one-third of that economic value generated outside Alberta – in Canada, the U.S. and around the world. Oil sands make up about five per cent of Canada’s overall greenhouse gas emissions and less than one-tenth of one per cent of the world’s emissions.4 The Canadian Association of Petroleum Producers (CAPP) conducted a survey of oil sands producers in early 2010 to determine their plans for production of both bitumen and upgraded crude oil from 2010-2025.5 Figure 1 – Growth Case – Western Canada Oil Sands & Conventional Production The Growth Case illustrated in Figure 1 is based on the assumption that oil sands projects will be developed and brought into service gradually.6 Typically, oil sands leases are in undeveloped locations near the Athabasca River which, along with underground aquifers, provides a source of water. The remote locations and limited labour capacity from the Fort McMurray area have necessitated large camps to be built at the mine site as well as airstrips to transport labour from all over Canada without increasing local labour demand. MINEABLE OIL SANDS The depth of the reserves determines whether mining or an in situ process will be used for recovery. Overburden removal is economically practical up to a depth of 75 meters for mining; beyond that depth, in situ techniques are preferred.7 Table 1 – Evolution of Oil Sands Mining Technology Function Old Current Next Cutter Wheel At Face & Oil Sands Extraction Conveyor Shovel & Trucks Conveyor with Dragline Hydrotransport Power Power from the Grid Cogeneration Nuclear Generation CT (composite tailings) Tailings Ponds Ponds & Thickeners MFT (mature fine tailings) Management Polymers Prior to excavation, muskeg and overburden are removed to expose the oil sands and stockpiled for use in reclamation. The evolution of oil sands technology is listed in Table 1 and, since the first oil sands plant started production in 1967, innovation has been at the forefront of the industry.8 Initially, draglines excavated the face of the formation and bucketwheels along with long conveyor belts moved the raw bitumen to on-site processing facilities that used hot water and tumblers to separate the oil and the sand.9 By the 1980s, trucks and power shovels began to replace the bucketwheels and draglines and, today, all bitumen mining employs the truck and shovel method.10 Power shovels dig out the oil sands and load it into trucks which transport the oil sands to crushers that break up lumps and remove rocks. In a process called hydrotransport, the oil sand is mixed with water at either 35°C or 50°C, depending upon the mine, and is piped to the processing plant. During hydrotransport, the bitumen begins to separate from the sand, water and minerals. The introduction of the hydrotransport system greatly increased both yields and reliability.11 Separation continues at the plant where the bitumen forms a thick froth at the top of the separation vessel and the sand settles out to the bottom. Material, including water, from the middle part of the vessel is further processed to remove more bitumen, the water is recycled and the sand is used in mine site reclamation.12 The next step is froth treatment, in which froth from the top of the separation vessel is treated to eliminate aqueous and solid contaminants to produce a clean bitumen product. The froth is first diluted with a hydrocarbon solvent to reduce the viscosity and density of the oil, which accelerates the settling of the impurities.13 Conventional froth treatment uses inclined plate settlers or centrifuges to remove water and solids.14 Figure 2 – Mineable Bitumen Extraction Plant Flowchart A typical mining oil sands facility today, as illustrated in Figure 2, consists of: Open pit mine Shovel and truck (100 tonnes and 400 tonnes payload) Double roll crushers Conveyors (8,000 tonnes/hr) Slurry plant (mix box) Pumping and hydrotransport pipeline Primary separation vessel (PSV) Secondary separation (flotation) Tailings, pipeline and pond Froth treatment (solvent recovery, removal of fines and addition of diluent) Diluted bitumen tank The future of oil sands mining includes mobile “at face” crushing and slurification to reduce both cost and environmental impact. As the name implies, the principles of “at face” crushing involve a mobile crusher, located next to the power shovel at the mine face, so that the ore can be dumped in directly, crushed, and fed to a connected slurry pipeline. With this system, trucks would still be needed to carry overburden and to reach less accessible parts of the mines, but trucking requirements and related air emissions would be greatly reduced.15 Technical Challenges In a mineable bitumen extraction facility, the froth treatment area has seen many technological improvements. Most notable is the move away from the naphthenic process to a paraffinic process. The naphthenic process is mechanical, requiring centrifuges and inclined plate separators. The paraffinic process is chemical and utilizes gravity separation, with the resulting product having lower levels of contaminants such as water and mineral solids.16 Environmental Challenges Tailings Management. It requires two tonnes of oil sand to produce one barrel of synthetic crude oil. As a by-product of the production, oil sands tailings are produced and contained in large earthen tailings ponds. Tailings are a mixture of clay, sand, water, silt, residual bitumen and other hydrocarbons, salts and trace metals. Over time, the particulates settle out and much of the water is treated and reused.17 New techniques are being implemented to: promote the settling of fine solids in tailings ponds, reducing the volume of water required for process cooling improve consolidated tailings, thus reducing tailings ponds create dry tailings, reducing the use of water, eliminating ponds and aiding the reclamation process.18 Water Use.
Details
-
File Typepdf
-
Upload Time-
-
Content LanguagesEnglish
-
Upload UserAnonymous/Not logged-in
-
File Pages19 Page
-
File Size-