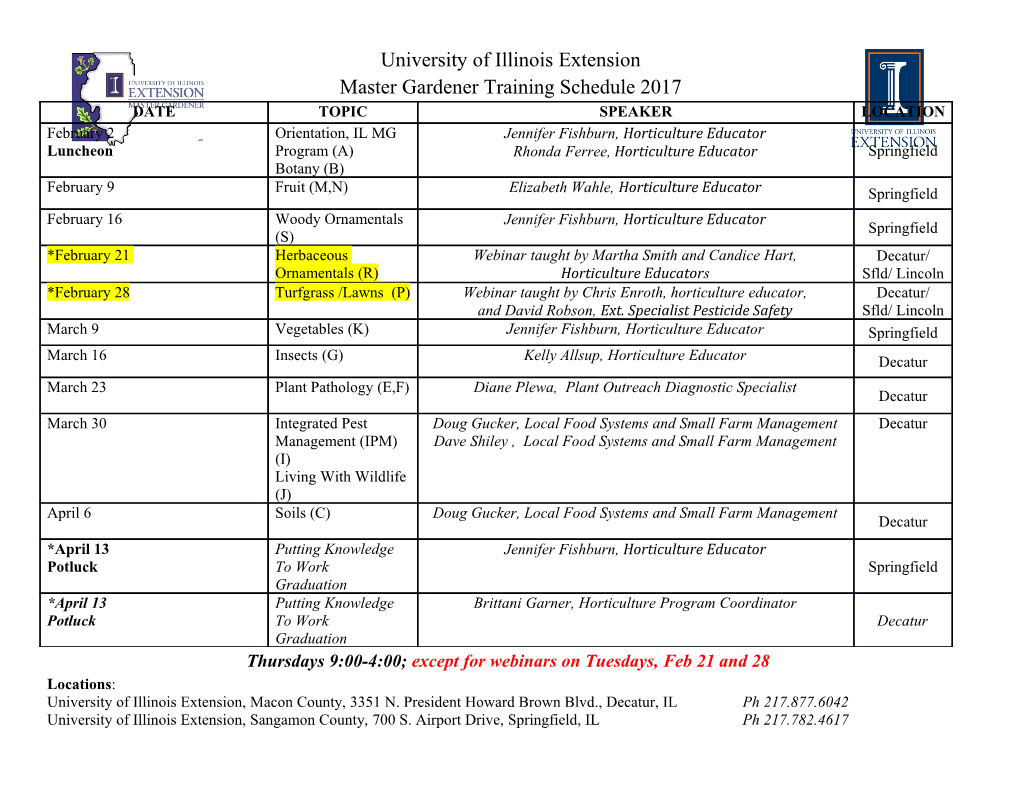
Project of the Rear Wing of a LMP3 Race Car Gonçalo Gaspar Bentes Pimenta Thesis to obtain the Master of Science Degree in Mechanical Engineering Supervisor: Prof. João Manuel Pereira Dias Examination Committee Chairperson: Prof. João Orlando Marques Gameiro Folgado Supervisor: Prof. João Manuel Pereira Dias Member of the Committee: Prof. Luís Alberto Gonçalves de Sousa November 2018 ii To my family, who was always there for me during the hardest times. To my friends, who walked with me through the toughest challenges. iii iv Acknowledgments First of all, I would like to thank my supervisor Professor Joao˜ Dias with whom I have worked closely since 2013 when PSEM was revived. His belief on my skills and the freedom he gave me while devel- oping this thesis was essential for its successful completion. Secondly, my family. My mother, father, sister and grandmother who always supported me and be- lieved on my decisions and my ability to overcome whichever setback I was faced with without never doubting me. I would like to thank Stephane´ Chosse, ADESS CEO, for the opportunity he gave me to work on an area I’ve loved since I was a little kid. Regarding ADESS, the team is amazing and we spent a great time working on some amazing projects. Maduro, Jose,´ Sergio,´ Andre,´ Hugo, Carlos, Marcio,´ Torsten, Jose´ Loureiro, Rui and Filipe, thank you for what you guys taught me and for the team spirit. I could not forget about the PSEM team where I spent most of my time in Tecnico.´ Most of what I know today I learned with you, working through endless days and sleepless nights. Mario,´ Frederico, Nuno, Guilherme, Andre,´ Gerardo, Catarina, Rita, Henrique, Hugo, Alves, Dias, Pedro, Joao˜ Oliveira, Rui, Chico, Ribeira, Ines,ˆ Gonc¸alo, Ch´ıcharo and Mendes, this here is for you. I would like to give a special thank you to Prakash from Altair who, despite not knowing me, helped me a lot through the Altair Forums, e-mails and Skype calls so I could finish my work in time. Last but not least, I want to thank all my friends from Tecnico´ who walked this path with me, Pedro, Catarina, Beatriz, Duarte, Jose,´ Renato, Hugo, Carolina and Ricardo. A special word to Ana for her encouragement and for always being by my side to support me face my challenges and help however she could. v vi Resumo Esta tese acompanha todo o trabalho de actualizac¸ao˜ e optimizac¸ao˜ da nova asa traseira do Prototipo´ LMP3 ADESS-03. O trabalho desenvolvido esta´ inclu´ıdo no processo de actualizac¸ao˜ do carroc¸aria do mesmo prototipo´ para os novos regulamentos de 2019. Para comec¸ar, o modelo CAD da asa foi alterado devido a defeitos estruturais existentes no modelo anterior. De seguida, foi definido um layup standard e avaliado a sua rigidez estrutural recorrendo a estudos de elementos finitos. Com base nos resultados desses estudos, foram definidos objectivos para optimizac¸ao˜ da estrutura da asa de maneira a obter a maior rigidez poss´ıvel para a menor massa poss´ıvel. Recorrendo ao solver Optistruct e a um novo algoritmo desenvolvido para simplificar a forma do resultado da optimizac¸ao,˜ foi atingido um layup ideal que apresentava uma rigidez 73% superior apesar de ser 12% mais pesado. Com base no resultado optimizado foi analisado todo o processo de fabrico, desenhados os moldes e por ultimo,´ realizado um estudo para prever o custo relativo da pec¸a comparativamente ao layup original. Os resultados deste estudo colocaram o layup optimizado fora do plano de fabrico devido ao custo total ser 479% superior ao layup standard. Com base no layup optimizado, foi testado um novo layup simplificado que nao˜ so´ teria melhor comportamento mecanicoˆ que o layup standard mas seria tambem´ significativamente mais barato que o layup optimizado. No final, a asa optimizada pesa 20% menos que o layup standard, e´ 54% mais r´ıgida para um aumento de custo de produc¸ao˜ de 163%. Palavras-chave: Prototipo´ LMP3, Optimizac¸ao˜ Estrutural, Materiais Compositos,´ Analise´ de Custo. vii viii Abstract This thesis follows all the design and optimization work of the new rear wing for the ADESS-03 LMP3 prototype. The work developed is included on the process of updating the bodywork of the prototype to comply with the new 2019 regulations. To start, the CAD model was updated due to structural defects existing on the previous model. After, a standard layup was defined and its structural integrity evaluated using FEA studies. Based on the results from those studies, objectives were defined for the wing opti- mization to obtain the stiffest structure possible for the least possible mass. Using Optistruct and a new algorithm developed to simplify the shape of the optimization process, an ideal layup was obtained that allowed for 73% less displacement to an increase in mass of 12%. Based on the optimized result, the whole manufacture process was analysed, the moulds were designed and finally, a study was performed to try to estimate the relative cost of the optimized layup compared to the standard layup. The results of this study placed the optimized layup outside of the manufacturing plan due to the total cost being 479% higher than the standard layup. Based on the optimized layup, a new simpler layup was tested that should have a better mechanical behaviour than the standard layup while being significantly cheaper than the optimized layup. In the end, the optimized wing weights 20% less than the standard layup, is 54% stiffer while being 163% more expensive to manufacture. Keywords: LMP3 Prototype, Structural Optimization, Composite Materials, Cost Analysis. ix x Contents Acknowledgments . v Resumo . vii Abstract . ix List of Tables . xv List of Figures . xix Nomenclature . xxiii 1 Introduction 1 1.1 A Brief History of Modern Prototype Racing . 1 1.1.1 The LMP3 Class Introduction . 3 1.2 Thesis Motivation . 5 1.3 Regarding Composites Manufacture and Optimization . 7 1.4 Objective of this Thesis . 7 1.5 Structure of this Thesis . 8 2 Performance Background and Work Methodology 9 2.1 A Brief Introduction to the Concepts of Aerodynamics . 9 2.1.1 Mastering the Concepts and the New Standards . 10 2.1.2 Aero Package of a LMP Prototype . 12 2.2 The Old ADESS-03 Wing . 13 2.3 Planning for Design, Development and Manufacture . 15 3 The New ADESS-03 Wing 17 3.1 Modeling the New Wing . 17 3.2 FEA Analysis of the Standard Layup Wing . 21 3.2.1 Building the FEA Model – Before Meshing . 23 3.2.2 Meshing and Analysis . 23 3.2.3 Convergence Study . 29 3.3 Standard Layup Analysis Results . 31 4 Optimization Process 33 4.1 Optistruct Optimization . 33 xi 4.1.1 Free Size Optimization . 34 4.1.2 Size Optimization . 35 4.1.3 Shuffle Optimization . 35 4.2 Wing Optimization . 36 4.2.1 Free Size Optimization . 36 4.2.2 Ply Shape Edit . 40 4.2.3 MATLAB Bespoke Cleanup . 42 4.2.4 Cleaned Plies vs Free Size Plies . 46 4.2.5 Size Optimization . 47 4.2.6 Shuffle Optimization . 48 4.2.7 Manual Laminate Edit . 51 4.3 Analysis of the Optimization Results . 52 5 Manufacturing Planning and Analysis 55 5.1 The Wing Assembly Process . 56 5.2 Mould Design . 57 5.2.1 Top Skin Mould . 57 5.2.2 Lower Skin Mould . 59 5.2.3 Rib Mould . 60 5.3 Special Considerations and Manufacturing Procedure . 60 5.4 Costs of Manufacture . 62 5.5 Devising a Simplified Layup . 65 5.5.1 Simplified Layup Study and Optimization . 68 5.5.2 Simplified Layup Cost Study . 72 6 Conclusions 75 6.1 Achievements . 75 6.2 Future Work . 76 Bibliography 77 A Optimized Layup - Optimization Evolution 83 A.1 Plies Created After Free Size Optimization . 83 A.2 MATLAB Cleaned Plies Comparison - HyperMesh . 86 A.2.1 Ply 101200 . 86 A.2.2 Ply 213200 . 87 A.2.3 Ply 311300 . 88 A.3 MATLAB Cleaned Plies Comparison - MATLAB . 89 A.3.1 Ply 101200 . 89 A.3.2 Ply 213200 . 91 A.3.3 Ply 311300 . 93 xii A.4 Comparison - Cleaned Plies vs Free Size Plies . 95 A.5 Plies Created After Size Optimization . 98 A.6 Plies Created After Shuffle Optimization . 101 A.7 Laminates After Manual Editing . 104 B Material Cost for Optimized Layup 107 C Simplified Layup - Optimization Evolution 110 C.1 Plies Created After Free Size Optimization . 110 C.2 Plies Created After Size Optimization . 112 C.3 Plies Created After Shuffle Optimization . 114 C.4 Laminates After Manual Editing . 116 D Material Cost for Simplified Layup 118 xiii xiv List of Tables 3.1 Wing parameters for downforce calculation. 23 3.2 Mechanical properties of Standard Modulus Plain Weave carbon fibre fabric. ..
Details
-
File Typepdf
-
Upload Time-
-
Content LanguagesEnglish
-
Upload UserAnonymous/Not logged-in
-
File Pages146 Page
-
File Size-