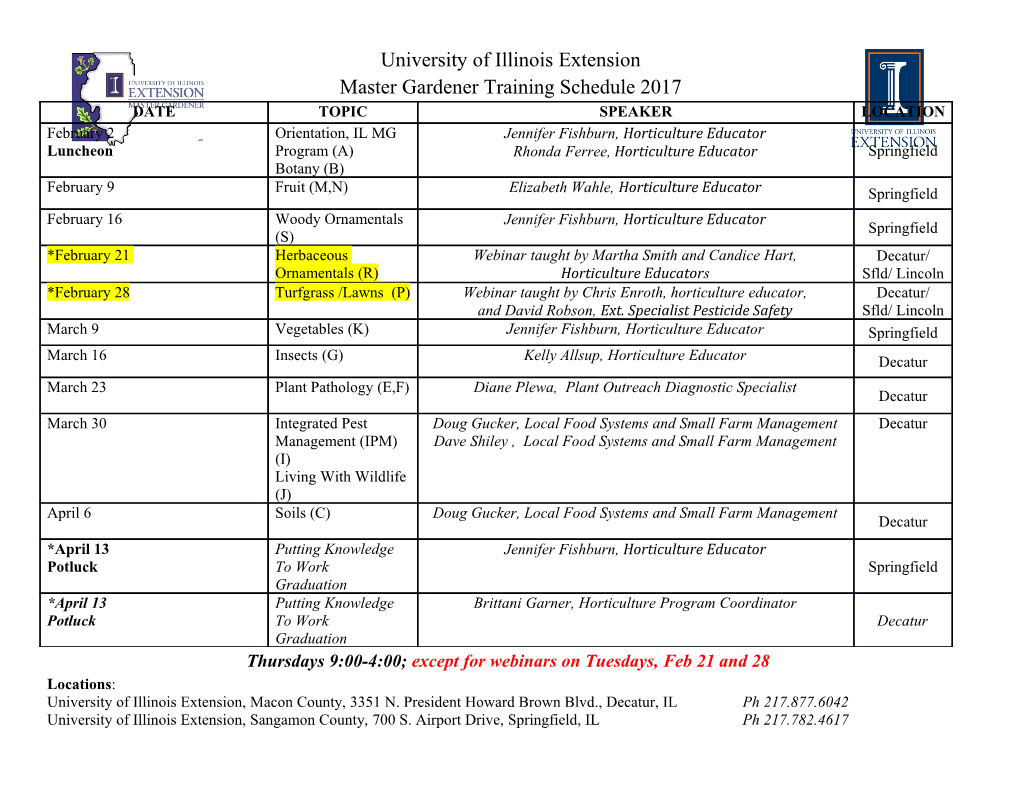
Imppgroving off-road vehicle handling using an active anti-roll bar PH Cronjé Supervisor: Prof PS Els 1 Table of contents • Statistics • Problem statement • Theory • Proposed solutions • Simulations • Design, manufacturing and testing • Results • Conclusion 2 Rollover accident statistics • Number of rollover fatalities per million registered vehicles, averaged from 1985 to 1990 in the United States 3 Rollover accident statistics • Passenger vehicles involved in fatal accidents, by vehicle body type in the United States 4 Problem statement • SUVs are growing in popularity • Poor handling due to off-road capabilities • Problem statement: Can the handling of an off-road vehicl e b e i mproved with out th e sacrifi ce of rid e comf ort? 5 Theory: Steady state cornering 6 Theory: Vertical load distribution 7 Theory: Static stability factor t SSF = 2hCG • Determines if the vehicle will slide before it will roll • To improve the safety of the vehicle, the following relationship must hold: t μ < 2hCG 8 Theory: Conclusion • If th e latera l acce lerat ion is use d as t he opt im iz ing variable, the vehicle will roll • Previous work showed that body roll angle is a desired variable to optimized when improving handling for a predefined road and manoeuvre •To imppgrove handling: o Lower the CG point o Increase suspension stiffness and/or damping o Add additional system which increases the roll stiffness 9 Solutions proposed in literature • Passive suspension • Semi-active suspension • Active anti-roll bar • Active suspension • Tilting vehicles Each of these solutions will now be discussed 10 Passive suspension • No energy is put into the system and no adjustments are made during operation 11 Semi-active suspension • Only a small amount of energy is put into the system with which adjustments are made to the system according to external inputs 12 Active anti-roll bar • Anti-roll bar actuated by an actuator which is actively controlled according to external inputs 13 Active suspension • A great amount of energy is put into the system and controlled by external inputs 14 Tilting vehicles • Vehicle leans into the turn • Works only on narrow vehicles 15 Selected solution Question 1 2 3 4 5 6 Solution Weighting 0.2 0.1 0.2 0.2 0.1 0.2 Total Position 1. Passive suspension 10 9 4 2 10 7 6.5 4 2. Semi‐active damping 10954887.1 3 3. Active anti‐roll bar 1097.55697.8 1 4. Active suspension 10 8 8 7 3 8 777.7 2 • The solutions was weighted according to the selection criteria • Selected solution: Active anti-roll bar 16 Active anti-roll bar (AARB) 17 Simulations • Full non-linear vehicle model in ADAMS 2005 • Simulation uses Simulink and Matlab • Adjustments to obtain correlation: – Spring and damper characteristics – Tyre characteristics – CG height – Chassis torsional stiffness 18 Correlation of baseline model 6 Measured Simulated 4 2 g) ee 0 Body roll angle (D -2 -4 -6 3 4 5 6 7 8 9 10 11 Time (s) 19 Model proposed solution • Proposed solution was modelled in ADAMS • Simulations was used to obtain specific design variables and predict results • Proposed solution predicts 80% improvement in bodyyg roll angle 20 Simulate proposed solution Body roll angle: Base vehicle vs AARB vehicle on flat road 6 Base vehicle AARB vehicle 4 2 (Deg) ee 0 age body roll angl rr -2 Ave -4 -6 0 1 2 3 4 5 6 7 8 9 10 Time (s) 21 Design, manufacturing and testing 22 Vehicle implementation 23 Tests • Tests was performed as Gerotek Test Facilities, West of Pretoria • The tests consisted of: o Steady state handling test: Constant radius test o Dynamic handling test: DLC manoeuvre o Ride comfort test: Drive over the Belgian paving at constant speed Each of these test will now be discussed 24 Constant radius test • Accelerate slowlyyg from standstill while following a constant radius around a point until the vehicle is unable to maintain a constant radius 25 Double-lane-change-manoeuvre • Enter fffirst lane at a predefined speed • Swerve to offset lane • Return to original lane 26 Ride comfort test • Dr ive over the Be lg ian pav ing in a s tra ig ht line w ith a constant speed 27 Results: Constant radius test 7 6 5 4 e (Deg) 3 rage bodyrage roll angl 2 Ave 1 0 Soft suspension, ARB disconnected Soft suspension, ARB connected Soft suspension, AARB -1 -1 0 1 2 3 4 5 6 7 8 Lateral acceleration (m/s2) 28 Results: DLC manoeuvre 6 Without ARB 5 With ARB With AARB 4 3 )) 2 1 Roll angle (Deg 0 -1 -2 -3 -4 5 6 7 8 9 10 11 12 13 Time (s) 29 Results: Ride comfort test • Vertical acceleration weighted according to the BS 6841 : 1987 standard for vertical vibration on a seated person • RMS was calculated from weighted vertical acceleration TtTest run SiSuspension ARB setti ng: WihtdWeighted no.: setting: RMS: 1 Soft Disconnected 143m/s1.43 m/s2 2 Soft Connected 1.41 m/s2 3 Soft Active 1.44 m/s2 30 Conclusion • The AARB system shows a 74% improvement in maximum body roll angle during a DLC manoeuvre with the soft suspension over the base line vehicle • The AARB system showed no detrimental effect on the ride comfort of the vehicle • AARB system can dramatically improve the handling of an off-road vehicle without the sacrifice of ride comfort. • Thank you for your time and safe driving! 31.
Details
-
File Typepdf
-
Upload Time-
-
Content LanguagesEnglish
-
Upload UserAnonymous/Not logged-in
-
File Pages31 Page
-
File Size-