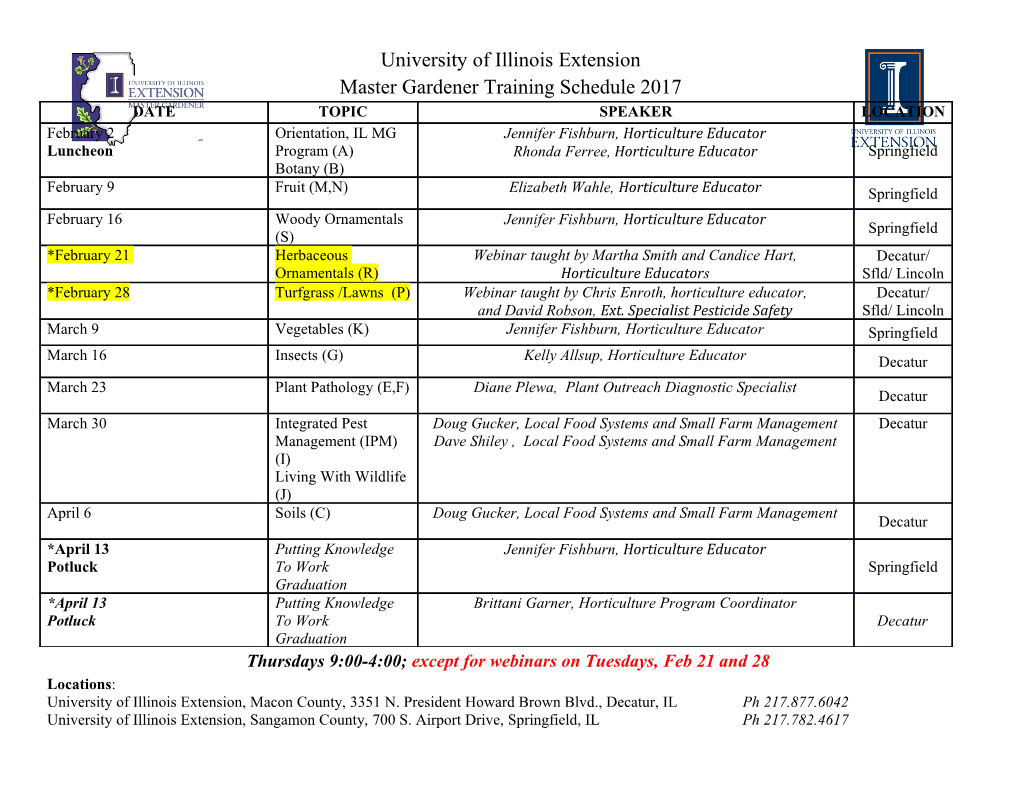
Lesson 4 Fabric Filter Material Goal To familiarize you with the construction of fabric filter material, fibers used, and problems affect- ing fabric life. Objectives At the end of this lesson, you will be able to do the following: 1. Name two ways filters are constructed 2. List at least seven natural or synthetic fibers used to make filters and identify the conditions under which they are used 3. Define five fabric treatment processes 4. Name three failure mechanisms that reduce filter life 5. Briefly describe four types of fabric tests that are used for troubleshooting bag problems Filter Construction Bag filters can be made of woven or nonwoven materials. Nonwoven materials can further be divided as felted or membrane. Most bags are either completely or partially made by weaving since nonwoven fabrics are generally attached to a woven base called a scrim. Woven filters are made of yarn with a definite repeated pattern. Felted filters are composed of randomly placed fibers compressed into a mat and attached to loosely woven backing material. A mem- brane filter is a special treatment where a thin, porous membrane (expanded polyfluorocar- bon) is bonded to the scrim, or support fabric. Woven filters are generally used with low energy cleaning methods such as shaking and reverse-air. Felted fabrics are usually used with higher energy cleaning systems such as pulse-jet cleaning. Membrane filters were developed in efforts to achieve high efficiency particle capture and to handle flue gas conditions where high moisture and resulting high pressure drop problems frequently occur. 2.0-3/95 4-1 Lesson 4 Woven Filters Woven filters have open spaces around the fibers. The weave design used will depend on the intended application of the woven filter. The simplest weave is the plain weave. The yarn is woven over and under to form a checkerboard pattern (Figure 4-1). This weave is usually the tightest, having the smallest pore openings in the fabric. Consequently, it retains particles very quickly. This weave is not frequently used, because the bags tend to have a high pressure drop (even without any dust cake). Figure 4-1. Plain weave or checkerboard Other weaves include the twill and sateen (satin). In the twill weave, yarn is woven over two and under one for a 2/1 twill and over three and under one for a 3/1 twill weave (see Figure 4-2). Figure 4-2. Twill weave patterns (2/1 and 3/1) 4-2 2.0-3/95 Fabric Filter Material The twill weave does not retain particles as well as the plain weave, but does not tend to blind as fast. Bag blinding is a condition where the particles (dust) becomes embedded in the filter over time and are not removed by the bag cleaning process. The twill weave allows good flow rates through the filter and high resistance to abrasion. In the satin weave, yarn is woven over one and under four in both directions. Satin weave does not retain particles as well as the plain twill weave, but has the best (easiest) cake release when the fabric is cleaned (Figure 4-3). Figure 4-3. Sateen weave (satin weave) Different weaving patterns increase or decrease the open spaces between the fibers. This will affect both fabric strength and permeability. Fabric permeability affects the amount of air passing through the filter at a specified pressure drop. A tight weave, for instance, has low permeability and is better for the capture of small particles at the cost of increased pressure drop. 2.0-3/95 4-3 Lesson 4 The true filtering surface for the woven filter is not the bag itself, but the dust layer or fil- ter cake. The bag simply provides the surface for capture of larger particles. Particles are collected by impaction or interception as the open areas in the weave are closed. This pro- cess is referred to as sieving (Figure 4-4). Some particles escape through the filter until the cake is formed. Once the cake builds up, effective filtering will occur until the bag becomes plugged and cleaning is required. At this point, the pressure drop will be exceed- ingly high and filtering will no longer be cost effective. The effective filtering time will vary from approximately 15 to 20 minutes to as long as a number of hours, depending on the concentration of particulate matter in the gas stream. Figure 4-4. Sieving (on a woven filter) Felted Filters Felted filters are made by needle punching fibers onto a woven backing called a scrim. The fibers are randomly placed as opposed to the definite repeated pattern of the woven filter. The felts are attached to the scrim by chemical, heat, resin, or stitch-bonding methods. To collect fine particles, the felted filters depend to a lesser degree on the initial dust deposits than do woven filters. The felted filters are generally 2 to 3 times thicker than woven filters. Each individual randomly oriented fiber acts as a target for particle capture by impaction and interception. Small particles can be collected on the outer surface of the filter (Figure 4-5). 4-4 2.0-3/95 Fabric Filter Material Figure 4-5. Felted fabric filter Felted filters are usually used in pulse-jet baghouses. A pulse-jet baghouse generally fil- ters more air per cloth area (higher air-to-cloth ratio) than a shaker or reverse-air unit. Felted bags should not be used in high humidity situations, especially if the particles are hygroscopic (these particles have an affinity to absorb moisture and thus become sticky). Clogging or blinding could result in such situations. Fibers The fibers used for fabric filters vary depending on the industrial application to be controlled. Early filters were mostly made from natural fibers such as cotton or wool. These fibers are rel- atively inexpensive but have temperature limitations (< 212°F or 100°C) and only average abrasion resistance. Cotton is readily available making it very popular for low temperature simple applications. Wool withstands moisture very well and can be made into thick felt easily. Synthetic fibers are more widely used today than natural fibers because they can operate at higher temperatures and better resist chemical attack. The synthetic fiber most often used for high temperature application is fiberglass or glass fibers. Fiberglass is the generic substance foundinFiberglas. For low temperature applications polypropylene is the most inexpensive synthetic fiber and is used in many industrial applications such as foundries, coal crushers, and food industries. Nylon is the most abrasion-resistant synthetic fiber, making it useful in appli- cations filtering abrasive dusts. Polyesters such as Dacron fibers have good overall qualities to resist acids, alkalines, and abrasion and are relatively inexpensive, making them useful for many industrial processes such as smelters, foundries, and other metal industries. Nomex fibers are widely used for fabric filter bags because of their resistance to relatively high temperatures and to abrasion. Nomex is used for filtering dusts from cement coolers, asphalt batch plants, ferroalloy furnaces, and coal dryers. Other registered trademark fibers such as Teflon, Fiberglas, Ryton, and P84, as well as carbon fibers can be used in very high temperature situations. Teflon has very good resistance to acid attack (except fluorine) and can withstand continuous temperatures up to 445°F (230°C). 2.0-3/95 4-5 Lesson 4 Fiberglas or glass is often used in baghouses that handle very high temperatures (up to 500°F or 260°C) for continuous operation. About 90% of the baghouses currently operating on coal fired utility boilers use bags made with glass fibers (McKenna and Furlong 1992). Glass fibers are usually lubricated in some fashion so they will slide over one another without breaking or cutting during the cleaning cycle. Graphite is commonly used as a lubricant and will help retain the upper service temperature limits. Glass fibers can break easily and require a very gentle cleaning cycle. Ryton is a felted filter made from polyphenylene sulfide fibers generally attached to a polyfluorocarbon scrim. Ryton can operate at high temperatures (350°F or 177°C) and shows good resistance to acids and alkalis. Fiberglas, Teflon, Nomex and Ryton have been used to remove particulate emissions generated from industrial and utility coal-fired boilers (Belba et al. 1992). Another material used to make bags is Gore-tex membrane manufactured by W. G. Gore and Associates, Inc. The Gore-tex membrane is an expanded polytetrafluoroethylene (PTFE) membrane that is laminated with a variety of fibers such as Fiberglas, polyester, and Nomex to produce felt and woven filters. Some test reports have indicated very good emission reduction (99.9+%), low pressure drops, increased bag life and higher air-to-cloth ratios using this mate- rial in metal industries, chemical industries, food industries, and coal-fired boilers. However, other fabrics have been able to obtain similar results. Finally, for very high temperature applications (> 500°C), ceramic filters are now available (McKenna and Turner 1989). These filters show promise for high temperature applications such as using the filters ahead of boiler superheater tube sections to remove particles and improve heat transfer in the boiler tubes. Table 4-1 lists a number of typical fibers used for fabric filters. The properties of the listed fibers include temperature limits, acid and alkali resistance, abrasion resistance, and relative bag costs. Table 4-1 is only a general guide since bag filters can be made of two or more layers of materials to achieve specific effects (i.e. strength, stability, filtering etc.) The cost (1992) of a fiberglass bag 14 feet long and 6 inches in diameter is approximately $35 to $40.
Details
-
File Typepdf
-
Upload Time-
-
Content LanguagesEnglish
-
Upload UserAnonymous/Not logged-in
-
File Pages16 Page
-
File Size-