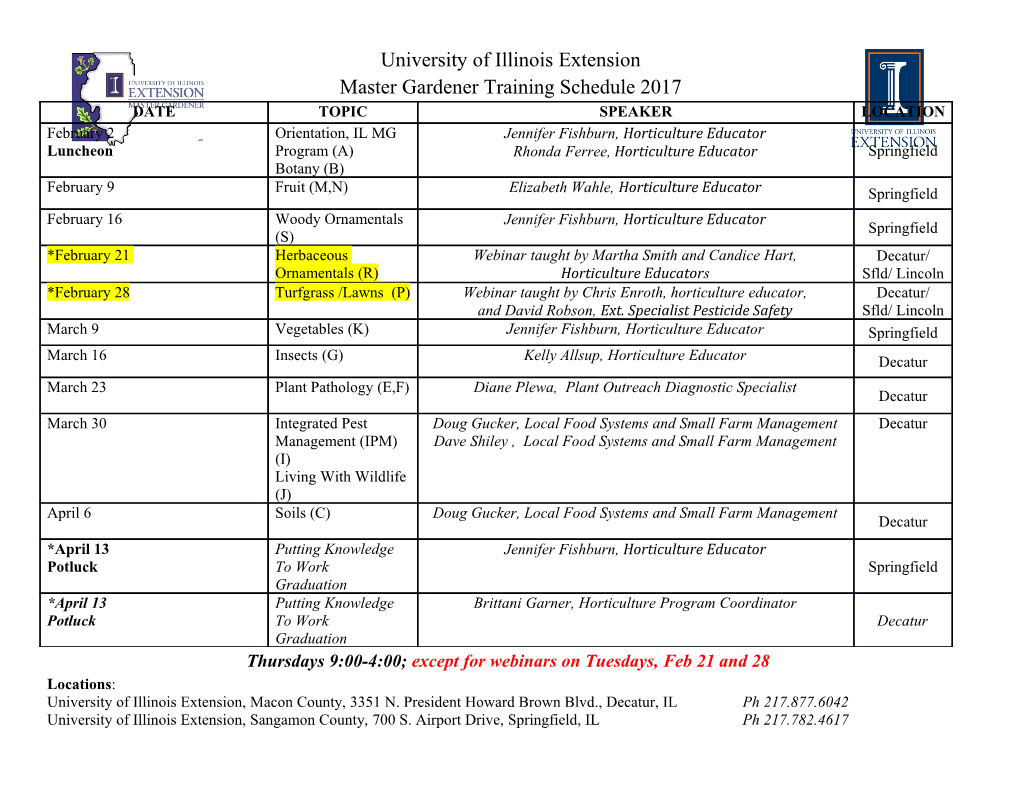
DOI: 10.13009/EUCASS2019-421 8TH EUROPEAN CONFERENCE FOR AERONAUTICS AND AEROSPACE SCIENCES (EUCASS) DOI: ADD DOINUMBER HERE Reusable stage concepts design tool Lars Pepermans?, Barry Zandbergeny ?Delft University of Technology Kluyverweg 1, 2629 HS Delft [email protected] yDelft University of Technology Kluyverweg 1, 2629 HS Delft Abstract Reusable launch vehicles hold the promise of substantially reducing the cost of access to space. Many different approaches towards realising a reusable rocket exist or are being proposed. This work focuses on the use of an optimisation method for conceptual design of non-winged reusable upper stages, thereby allowing it to take into account landing on land, sea or mid-air retrieval as well as landing the full stage or the engine only. As the optimisation criterion, the ratio of the specific launch cost of the reusable to the expendable version is used. The tool also provides for a Monte Carlo analysis, which allows for investigating the ruggedness of the design solution(s) found. The article will describe the methods implemented in the Conceptual Reusability Design Tool (CRDT) together with the modifications made to ParSim v3, a simulation tool by Delft Aerospace Rocket Engi- neering. Furthermore, it will present the steps taken to verify and validate CRDT. Finally, several example cases are presented based on the Atlas V-Centaur launch vehicle. The cases demonstrate the tools capa- bility of finding optimum and the sensitivity of the found optimum. However, it also shows the optimum when the user disables some Entry Descent and Landing (EDL) options. 1. Introduction To make space more accessible, one can reduce the cost of an orbital launch. Of the total cost per launch, the manufac- turing cost of the rocket makes up 60% and 70%.10 To reduce the manufacturing costs, one can consider designing a reusable rocket stage. This will reduce the hardware costs but at the expense of higher development cost. Both SpaceX and United Launch Alliance have added reusability to their launcher’s first stage to decrease the cost per launch. Be- sides that, several other companies are investigating reusing the first stage. Most research focuses on the first stage and very little research is done on the upper stage. The upper stage of the Atlas V Centaur launcher is about 25% of the mass and 30% of the hardware cost of the entire launcher.23 This means that a significant portion of the cost is not considered for reuse at the moment. Upper stage reusability has been proposed for the Blue Origin New Glenn rocket3 and the Kistler K1 rocket.6 However, neither have proven this in flight. The USA Space Shuttle is the only example of an operational reusable upper stage. From literature, two classes of entry vehicles can be identified: ballistic or lift generating vehicles.31 Most research done on the upper stages focuses on the winged entry vehicles following a glide entry, such as the USA space shuttle, SpaceX BFR, and CNES/ESA Hermes.15 This means that the stage has to be developed from scratch. The development of an entirely new stage, however, is a time and cost-intensive process. Therefore the focus of this research is on making an existing upper stage reusable by applying commercially available entry descent and landing (EDL) hardware. For this research, it is assumed that the stage performs a ballistic entry and that no form of a winged entry vehicle is possible. It furthermore assumes that the initial condition for the stage is a stable orbit, this orbit is the target orbit for the satellite. When adding reusability to a stage, one adds hardware to bring it back the stage safely to the ground. This added hardware comes at a price in terms of payload reduction and hardware cost increase. Besides that, reliability might decrease when a stage is reused often. To determine whether the reusable upper stage is cheaper than an expendable upper stage, the Reuse Index as proposed by United Launch Alliance (ULA), is used.23 An overview of the investigated hardware and the Reuse Index can be found in section 2. As the Reuse Index requires the cost and mass for each Copyright © 2019 by L. Pepermans and B.T.C Zandbergen. Published by the EUCASS association with permission. DOI: 10.13009/EUCASS2019-421 REUSABLE STAGE CONCEPTS DESIGN TOOL recovery element of hardware required. These modifications to the stage are represented in an ID. Together with the various mass and cost models, this is shown in section 4. To determine whether a solution exists that can reduce an upper stage cost’s by adding reusability, an optimisation tool has been developed. The optimisation tool is based upon a genetic algorithm and is described in section 3. This method has been chosen due to the non-linear and non-continuous nature of the problem. When an optimum has been found, the tool performs a Monte Carlo analysis to determine the sensitivity of the found solution. The individual mass and cost models have all been verified using existing information. The trajectory verification, together with the verification of the optimisation algorithm, is done in section 5. Finally, in section 6, a case study is done using the Centaur upper stage. This case demonstrates the feasibility of upper stage reusability and shows the capabilities of the tool. The conclusions can be found in section 7. 2. Background From literature, it was found that the flight of an upper stage consists of five main phases, see Figure 1. Each phase requires the addition of hardware elements, these are presented in in Table 1. Figure 1 is preceded by the ascent flight of the upper stage and is followed by the retrieval and refurbishment of the upper stage. Figure 1: Flight phases of a reusable upper stage Table 1: Overview of identification phases in the reusable flight Phase Design options 1) De-orbit Two burn de-orbit 2) Atmospheric entry Conventional heat shield Inflatable heat shield 3) Descent Ballute Supersonic parachute Subsonic parachute Drag plate Engine burns Rotor landing 4) Landing None Airbag Retrorocket Water landing Mid air recovery 5) Retrieval and Refurbishment The de-orbit phase is done using a Hohmann transfer orbit with two engine burns, one at the apogee of the initial orbit, and one at the user-defined entry point (periapsis), see Figure 2. The entry point is defined by its altitude [m], velocity [m/s] and entry angle [deg] 1. The goal of the first burn is to attain the desired entry altitude while the second determines the entry angle and entry velocity. 1Downward from local horizon is negative 2 DOI: 10.13009/EUCASS2019-421 REUSABLE STAGE CONCEPTS DESIGN TOOL Figure 2: De-orbit manoeuvres When re-entering the atmosphere, the stage experiences heat transfer due to aerothermal heating. This resulting heat flow can require the use of thermal protection system is. Literature suggests two options for thermal protection: solid heat shields and inflatable heat shields. The solid heat shield is however a more conventional solution the inflatable heat shield has the advantage that it can combine the functions of thermal protection, parachute, and airbag landing system.8, 14 It has however a lower technology readiness level compared to the conventional heat shields. To ensure a safe landing, one or more decelerators are required. Four main decelerator options have been identified from literature: parachutes, drag plates, engine burns, and rotor landing. Even though the rotor landing nicely combines the decelerator and landing options, the technology readiness level is not sufficient for current applications and thus not considered.22 The parachutes identified to be of use for this research are ballistic, non-steerable parachutes. The parachutes con- sidered for this research come in three categories: ballute, ribbon parachutes, and Ringsails parachutes. The ballute’s primary function is stabilisation of the stage and is used when the upper stage is unstable during the flight. The rib- bon parachutes are assumed to be supersonic, drogue parachutes where the Ringsail parachutes are mainly used for subsonic, main parachutes.12 The choice of parachutes is based upon the deployment altitude: • 100000 m - 60000 m - Ballute • 60000 m - 7500 m - Ribbon parachute • 7500 m - 0 m - Ringsail The drag plates are deployable, solid drag enhancement surfaces. These surfaces increase the drag of the body to decrease the terminal velocity. Drag plates can also provide aerodynamic control, although this is not considered in this research. Engine burns are an air-independent method of deceleration. This means it can decrease the maximum dynamic pressure and heat flux on the stage during the atmospheric entry flight. When a concept separates the engines and propellant tanks, engine burns are not a feasible decelerator. The landing hardware assumes that the stage always performs a safe landing as long as the terminal velocity of the stage is within the allowable range. Four landing options have been identified from literature: retrorockets, airbags, water landing and mid-air retrieval.12 Both the retrorockets and airbags are used for a dry landing; this can either be on land or a ship. The retrorocket solution equips the stage with small solid rocket engines that are fired just before the stage hits the ground. The advantage of this system is that the maximum allowable terminal velocity is assumed to be 100 m/s. The airbag system has a lower maximum acceptable landing velocity of 10 m/s.12 However, it has a lower cost than the retrorocket system for landing velocities below 12 m/s. During a land landing, the stage is retrieved by a truck with a crane. This is comparable to the Soyuz landings. When the stage lands in the water, it is assumed that any landing is safe when the landing velocity is below 20 m/s.
Details
-
File Typepdf
-
Upload Time-
-
Content LanguagesEnglish
-
Upload UserAnonymous/Not logged-in
-
File Pages14 Page
-
File Size-