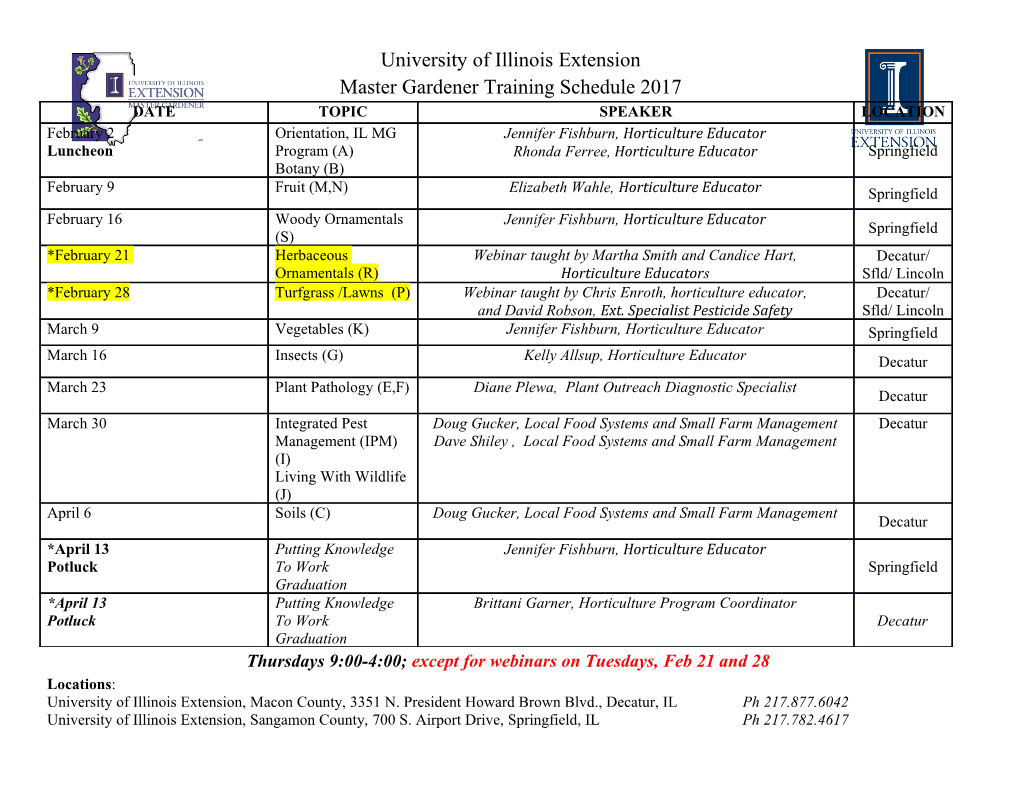
Comparative LCA on Plastic Packaging 1N1800 25 May 2005 Group nr 2: Britta Lehmann Francisco Vilaplana Emma Strömberg Widad Suliman Laura Rodriguez Cerrato 1 List of content 1. Goal and Scope.................................................................................................. 3 1.1 Goal of the study.......................................................................................... 3 1.2 Functional unit ............................................................................................. 4 1.3 System boundaries ....................................................................................... 5 1.4 Assumptions and limitations........................................................................ 5 1.5 Impact categories and impact assessment method ...................................... 6 1.6 Normalisation and weighting....................................................................... 6 2. Life cycle inventory analysis............................................................................. 7 2.1 Process flowchart......................................................................................... 7 2.2 Data .............................................................................................................. 9 3. Life cycle interpretation .................................................................................. 18 3.1 Results........................................................................................................ 18 3.2 Conclusions and recommendations ........................................................... 21 4. References ....................................................................................................... 22 Appendix ............................................................................................................ 23 2 1. Goal and Scope 1.1 Goal of the study Background The aim of this study is to compare the environmental effects during the whole life cycle (from manufacture to waste management) of the usage of two different plastic materials, PET and HDPE, for bottling applications. It is of great interest to have this comparison, since the HDPE resin is cheaper and could be beneficial to the bottling company. But the environmental effect of the material must be established in order to follow the guidelines issued by the legislation on packaging and packaging waste. Apart from the academic intention of this study, the results of a similar analysis carried out at a higher scale could be employed at the industrial level in order to select the most “environmentally-friendly” plastic material intended for bottling. The design of a product must nowadays take into account, apart from the economical aspects, other factors such as the legislation pressures on environmental issues and the publicity of having an ecological product. The intended audience for this LCA are mainly all the parties involved in the plastic industry, manufacturers, packaging processors, environmental consultants, legislators, etc. A summary of this LCA could also be made in a clear language so that the main public could understand the environmental effects of employing different plastics in bottle packaging. Since the main objective of the analysis is to compare and evaluate the environmental impacts of the employment of two different plastic materials for bottling applications, the LCA can be defined as accounting. Polyethylene terephtalate, PET Poly(ethylene terephthalate), PET, containers form part of everyone's daily life. PET is a strong but lightweight form of clear polyester. It is used to make containers for soft drinks, juices, alcoholic drinks, water, edible oils, household cleaners, and other food and non-food applications. It is the strength of the material that contributes to make PET the success it is. The carbonated soft drinks can generate pressure inside the bottle reaching up to 6 bar. Such high pressure however, thanks to the alignment of macromolecules (crystallisation), is not capable of deforming the bottle nor can it make the bottle explode. PET’s molecules consist of long chains of repeating units only containing carbon, oxygen and hydrogen, the repeating unit is shown in Figure 1.1. O O OC C O CH CH 2 2 n Figure 1.1: Repeating unit of PET Ethylene glycol, EG, and terephthalic acid, PTA, are the building blocks of the commercial PET. The substances react to form a resin, which is melted and injected into a mould to make a preform. The preform, a sort of test tube shorter than what the bottle will be but with thicker walls, is then stretch blow moulded. Blow moulding is the primary method to form hollow plastic objects such as soda bottles. The process includes clamping the ends of a softened tube of polymers which can be either extruded or reheated, inflating the polymer against the mould 3 walls with a blow pin, and cooling the product by conduction or evaporation of volatile fluids in the container. Stretching blow moulding is also called biaxial orientation blow moulding. During the blow moulding phase, high-pressure air is blown into the preform allowing it to take the exact shape of the mould it is set into. The final product is a transparent, strong and lightweight bottle. High Density Polyethylene, HDPE Polyethylene is probably the most common polymer in daily life. HDPE plastics offer a wide range of desirable properties and characteristics for packaging applications such as toughness, low cost and good barrier properties. This is the polymer that makes grocery bags, beverage bottles, children's toys, and even bullet proof vests. For such a versatile material, it has a very simple structure, the simplest of all commercial polymers. A molecule of polyethylene is a long chain of carbon atoms, with two hydrogen atoms attached to each carbon atom, the repeating unit of polyethylene is demonstrated in Figure 1.2. CH2 CH2 n Figure 1.2: Repeating unit of polyethylene High density poly(ethylene) is a linear polymer, it has very little branching along the hydrocarbon chains - the crystallinity is 95% or better, and has the density of 0,95-0,97 g/cm3. It is manufactured by a Ziegler-Natta polymerisation at low pressures and at temperatures of 50-75°C. A Ziegler-Natta catalyst is a catalyst used in the production of unbranched, stereoregular polyalkene polymers. Ziegler-Natta catalysts are typically based on titanium tetrachloride and the organometallic compound triethylaluminium. The polymer forms as a powder or granules which are insoluble in the reaction mixture. When the polymerization is completed, the catalyst is destroyed by adding water or alcohol to the reaction mixture. The polymer is then filtered or centrifuged off, washed and dried. Injection blow moulding process is used for production of bottles from HDPE. Injection blow moulding gives better definition of details (e.g. screw thread), and a better control of the distribution of the thickness of the material. 1.2 Functional unit Definition of function The system function was beverage bottles made of HDPE or PET during their whole life-time. In the model we didn’t consider the two different types of PET for bottling applications (one- way and reusable bottles), which obviously would have changed the model building and the waste scenarios. If so, we should have had realistic data about if the weight and thickness of the different bottles made from PET possess really such different values. We think that the difference between the PET grade used in one-use and refill PET bottles is not in the thickness and weight of the bottles, but in their crystallinity and additives. Functional unit, which quantifies this function The functional unit for this study was 1 kg of polymeric material used for bottle application. The unit was chosen to 1 kg instead of 1 litre since it was the one specified by SimaPro. The average weight of the HDPE bottle is 32-54 g and of the PET bottle 53 g, so the weight was considered the same. 4 1.3 System boundaries Boundaries in relation to nature In this LCA we are taking into account the entire life-cycle of the bottles, from the raw material (oil) to the moment they loose totally their value (landfilling). Recycling and energy recovery of the bottles are therefore included in the study, since these operations revalue the product. The material production phase includes the extraction of the raw materials as well as the materials manufacture, which is the processing of the raw materials into intermediate materials. This phase also includes transportation of raw materials to the location where they are processed into intermediate materials. The transportation of the collected and recycled materials is included in the waste management phase. Geographical boundaries Sweden is the geographical limit in this LCA. Time horizon This study has a retrospective view, because it is accounting the environmental impact of two different materials. The purpose of this is therefore not to make future predictions. Cut-off criteria One of the cut-offs performed in the study is the omission of the “usage” part of the bottles, since it is considered that the performance in use of both materials (PET and HDPE) during their life as bottles would be the same. Another cut-off is the transport of the bottles to the distribution market, since the weight, distance and transportation means are assumed equal. Another criterion is used in the implementation of the inventory, considering the negligible values of the impacts and their significance. Allocation procedures
Details
-
File Typepdf
-
Upload Time-
-
Content LanguagesEnglish
-
Upload UserAnonymous/Not logged-in
-
File Pages55 Page
-
File Size-