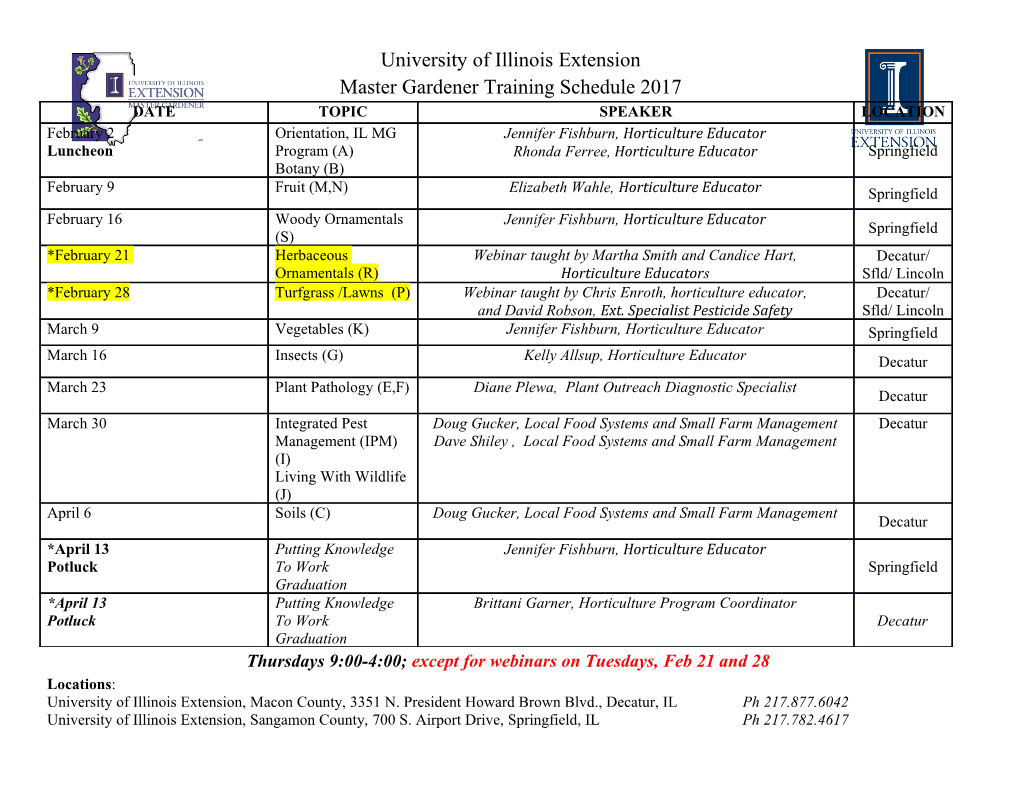
TRAINING COURSE SERIES No. 9 Non-destructive Testing: A Guidebook for Industrial Management and Quality Control Personnel 3 1-05 INTERNATIONAL ATOMIC ENERGY AGENCY, VIENNA, 1999 TRAINING COURSE SERIES No. 9 Non-destructive Testing: A Guidebook for Industrial Management and Quality Control Personnel INTERNATIONAL ATOMIC ENERGY AGENCY, VIENNA, 1999 The originating Section of this publication in the IAEA was: Industrial Applications and Chemistry Section International Atomic Energy Agency Wagramer Strasse 5 P.O. Box 100 A-1400 Vienna, Austria NON-DESTRUCTIVE TESTING: A GUIDEBOOK FOR INDUSTRIAL MANAGEMENT AND QUALITY CONTROL PERSONNEL IAEA, VIENNA, 1999 IAEA-TCS-9 ©IAEA, 1999 Printed by the IAEA in Austria January 1999 FOREWORD The introduction and application of non-destructive testing (NDT) in industry is grossly misrepresented and misunderstood. It is often said that introduction of this expensive technology does not give any tangible returns or at least does not give returns proportional to the investment made. The facts, however, are exactly opposite to this notion and thinking. In fact, NDT, when appropriately applied, gives tremendous returns by way of savings in scrap by lowering the ultimate rates of rejection, saving valuable manufacturing time, increasing the overall quality and reliability of manufactured goods, providing an extension of plant life through preventive maintenance, saving unnecessary shutdowns, particularly through in- service inspection, and enhancement of a particular industry's reputation and consequent increased sales and profits. Therefore, even from a purely commercial viewpoint, NDT is of utmost importance for an industrial concern. The additional considerations of NDT's role in safety, failure and consequent accident prevention leave no doubt at all about the value and need of NDT. It is this point that needs to be fully appreciated by the industrial managers and decision makers at all levels. Management ought to understand in quite an unambiguous way that their products can only survive in the highly competitive markets of today if they have the adequate and optimum quality. This quality can be built into the manufactured goods only if suitable measures and methods of quality control are employed and that the most suitable methods in most situations are the non-destructive testing methods. Experience shows that in many cases of industrial decision making, proper knowledge of various aspects of a particular technology plays an important role. Therefore, if positive decisions are desired to be taken in favour of introducing NDT in industry in any country, its decision makers should be properly equipped with knowledge and information about this area of technology. It was with this thinking and background that training courses were organized, first in Pakistan, with the help of IAEA assistance. Each course was of two weeks duration and covered quite comprehensively various aspects of NDT technology. The topics selected included NDT methods, their applications, capabilities and limitations; economic and administrative aspects of NDT; codes and standards; quality assurance; education, training and certification of NDT personnel and sources of information in NDT. Various manufacturing processes and the typical defects associated with them were also reviewed. The course also included demonstration practicals on all the basic five methods of NDT and, to keep the managers interested and fully occupied, a token examination was given on the last day. These courses were very well received and appreciated by all the participants, most of whom were the middle level managers in their industries. One indicator of the success and the interest it generated was the demands from these managers for training of their staff in NDT. No doubt that two weeks proved to be too long a period for which the management personnel could afford to be away from their establishments. Nevertheless, the topics covered have been found to be quite informative and of fundamental importance for impressing upon the management personnel the importance and need for NDT. A shorter version of this can be extracted from these topics and given in the form of executive management seminars. It has therefore been considered appropriate to compile the lectures delivered at these courses in the form of a book such as to make it suitable for use in the other countries of the region, as well as other regions of the world. The IAEA expert for these training courses held in Pakistan was J. Zimhelt of Canada and the contents of some of the sections are based on his lectures and are duly acknowledged. Some portions of the book have been directly adopted from the Training Course Series No. 3 entitled Industrial Radiography: Manual for the Syllabi Contained in IAEA-TECDOC-628, "Training Guidelines in Non-destructive Testing Techniques" (IAEA, 1992). The remaining sections were developed by A.A. Khan and his colleagues at the National Centre for NDT (NCNDT) of the Pakistan Atomic Energy Commission. Different sections of the book were then sent to the national co-ordinators of the NDT sub-project of RCA in the region of Asia and the Pacific for their comments and suggestions. The draft was then finalized by incorporating the recommended changes. During the process of compilation of the training notes guidance and support were provided by a large number of persons, especially from the NCNDT, the OAEP, Thailand and the RCA Co-ordinator's office at the IAEA. The IAEA wishes to express its appreciation to all those who have contributed to the production of these training course notes and to the governments and organizations whose financial and technical support made this publication possible. EDITORIAL NOTE In preparing this publication for press, staff of the IAEA have made up the pages from the original manuscripts). The views expressed do not necessarily reflect those of the IAEA, the governments of the nominating Member States or the nominating organizations. Throughout the text names of Member States are retained as they were when the text was compiled. The use of particular designations of countries or territories does not imply any judgement by the publisher, the IAEA, as to the legal status of such countries or territories, of their authorities and institutions or of the delimitation of their boundaries. The mention of names of specific companies or products (whether or not indicated as registered) does not imply any intention to infringe proprietary rights, nor should it be construed as an endorsement or recommendation on the part of the IAEA. CONTENTS 1. THE IMPORTANCE OF NON-DESTRUCTIVE TESTING 1 1.1. The scope of NDT 1 1.1.1. Need and definition of NDT 1 1.1.2. Methods of NDT 2 1.1.3. Relationship to destructive testing 3 1.2. The applications of NDT 3 1.2.1. Applications in design 3 1.2.2. Applications in manufacturing quality 7 1.2.3. Applications for in-service inspection 8 1.2.4. Applications in plant life extension 10 1.2.5. Other applications 10 1.3. The impact of NDT in disaster prevention 11 1.3.1. Loss of life 11 1.3.2. Environmental damage 11 1.3.3. Loss of product 11 1.3.4. Lost time 12 1.3.5. Repair costs 12 1.4. The historical development of NDT 12 1.4.1. Factors influencing development 12 1.4.2. Future expectations 13 2. MATERIALS, MANUFACTURING PROCESSES AND DEFECTS 13 2.1. Structure of metals and alloys 13 2.1.1. Grains (crystals) and grain boundaries 16 2.1.2. Structure of alloys 17 2.1.3. Allotropic transformation 19 2.2. Physical and mechanical properties of metallic materials 19 2.2.1. Elasticity 20 2.2.2. Strength 21 2.2.3. Hardness 22 2.2.4. Brittleness 23 2.2.5. Ductility 23 2.2.6. Malleability 23 2.2.7. Notch toughness 23 2.2.8. Conductivity 24 2.3. Basic metallurgical processes and defects 25 2.3.1. Welding processes 25 2.3.2. Weld defects 29 2.3.3. Casting processes 32 2.3.4. Casting defects 36 2.3.5. Forging processes 39 2.3.6. Rolling processes 40 2.3.7. Forging and rolling defects 41 2.3.8. Surface finishing 43 2.4. Materials in service 50 2.4.1. Behaviour of materials in service 50 2.4.2. Conditions leading to defects and failures 50 2.5. Non-metallic materials 58 2.5.1. Ceramics 58 2.5.2. Cermets 59 2.5.3. Composites 61 2.5.4. Concrete 63 3. THE TECHNOLOGY OF NDT METHODS 63 3.1. Visual testing (VT) 64 3.1.1. Tools for visual inspection 64 3.1.2. Applications of visual inspection 64 3.2. Liquid penetrant testing (PT) 65 3.2.1. General procedure for liquid penetrant inspection 65 3.2.2. Penetrant processes and equipment 68 3.2.3. Areas of application of liquid penetrants 69 3.2.4. Range and limitations of liquid penetrants 69 3.3. Magnetic particle testing 70 3.3.1. Methods of magnetization 70 3.3.2. General procedure for magnetic testing 74 3.3.3. Equipment for magnetic particle inspection 76 3.3.4. Applications of the magnetic method of testing 78 3.3.5. Range and limitations of magnetic particle inspection 79 3.4. Eddy current testing 79 3.4.1. Equipment and procedure for eddy current testing 82 3.4.2. Applications of eddy current testing 85 3.4.3. Range and limitations of eddy current testing 85 3.5. Radiographic testing 86 3.5.1. Fundamental principles 86 3.5.2. General procedure for radiographic testing 91 3.5.3. Different forms of radiographic testing 92 3.5.4. Personal safety and radiation protection 95 3.5.5. Applications of radiographic testing method 98 3.5.6.
Details
-
File Typepdf
-
Upload Time-
-
Content LanguagesEnglish
-
Upload UserAnonymous/Not logged-in
-
File Pages297 Page
-
File Size-