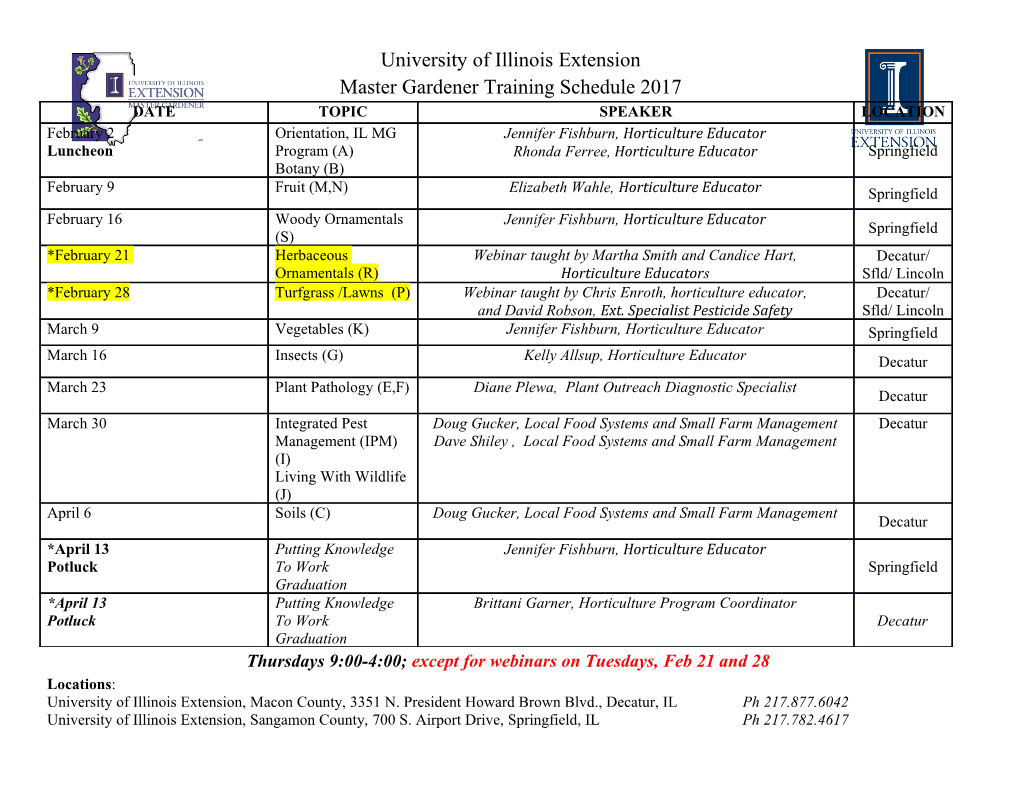
NASA CR-145032 NASA CONFIGURATION DEVELOPMENT STUDY OF THE X-24C HYPERSONIC RESEARCH AIRPLANE - PHASE I H C COMBS, el ol Lockheed Aircraft Corporation Advanced Development Projects December 1976 Prepared for NATIONAL AERONAUTICS AND SPACE ADMINISTRATION Langley Research Center Hampton, Virginia 23665 NASA CR-145032 IWVSA National Aeronautics and Space Administration CONFIGURATION DEVELOPMENT STUDY OF THE X-24C HYPERSONIC RESEARCH AIRPLANE - PHASE I H G COMBS, et al Lockheed Aircraft Corporation Advanced Development Projects December 1976 Prepared for NATIONAL AERONAUTICS AND SPACE ADMINISTRATION Langley Research Center Hampton, Virginia 23665 1 Report No. 2 Government Accession No. 3. Recipient's Catalog No NASA-CR-1U5032 4. Title and Subtitle 5 Report Date CONFIGURATION DEVELOPMENT STUDY OF THE ~x.-2kc HYPERSONIC RESEARCH AIRPLANE - PHASE I 6 Performing Organization Code 7 Author(s) 8. Performing Organization Report No SP-4^99 Henry G. Combs, et al 10 Work Unit No 0 Performing Organization Name and Address Advance Development Projects of The California 11. Contract or Grant No H Company, A Division of Lockheed Aircraft Corporation NAS-1-1^222 Burbank, CA 91520 13. Type of Report and Period Covered 12 Sponsoring Agency Name and Address Contractor Rej>ort National Aeronautics and Space Administration Nov. 1975 thru March 1976 14 Sponsoring Agency Code Washington, D.C. 205^6 15. Supplementary Notes 16 Abstract Four Hypersonic Research Airplane configurations found to be the most cost effective have been selected for further refinement in the Phase II Study. The selection was based on a systematic analysis and evaluation of realistic designs involving nine different configurations evolving from three different structural/thermal concepts coupled with existing rocket and sustainer engines. All configurations were constrained by the mission profiles, research requirements, aerodynamic envelope and maximum launch weight established by NASA. 17 Key Words (Suggested by Author(s)) (STAR category underlined) 18. Distribution Statement Thermal Protection Systems Heat-Sink Structure Unclassified - Unlimited Hypersonic Flight Rocket Engines Lockalloy Research Ablator IS Security Ctasstf (of this report) 20. Security Oassf. (of this page) 21. No of Pages 22 Price* Unclassified Unclassified 351 r The National Technical Information Service, Springfield. Virginia 22151 'Available from] i STIF/NASA Scientific end Technical Information Facility. P O Box 33. College Park. MO 20740 FOREWORD This analytical study report is submitted to the National Aeronautics and Space Administration in accordance with NASA Contract NAS 1-14222. The work reported herein was performed between November 1975 through March 1976 culminating in an oral presentation at NASA LRC on 17 March 1976. The study was performed by the Advanced Development Projects "Skunk Works" of the California Company, a Division of Lockheed Aircraft, under the supervision of Mr. H. G. Combs, Study Manager. Engineering graphics and supporting text were developed under the direction of Messrs. D. H. Campbell (Propulsion and Thermodynamics), M.D. Cassidy (Aerodynamics), C. D. Sumpter (Structures), R. C. Murphy (Flight Dynamics), E.B. Seitz (Weight), G. J. Kachel and R. P. James (Vehicle Design), J. Walters and consulting services of J. Love (Maintenance), and R. T. Passon (Cost). The Program Monitor for NASA was Mr. J. D. Watts. This study was a co-operative effort between the contractor and NASA in which data and frequent consultation, as well as program direction were pro- vided by NASA. iii/iv SUMMARY Phase I analytical study was performed to determine the vehicle configura- tion most cost effective for refinement in Phase II and III of the NASA Configura- tion Development Study of the X-24C Hypersonic Research Airplane. The results permitted selection of cost-effective configurations for further refinement in the follow-on phases of the study. Nine vehicle configurations, consisting of three different structure concepts in combination with three propulsion systems, were subjected to a systematic pro- gram involving development and evaluation of realistic design concepts coupled with propulsion and airframe integration. All configurations were constrained by predetermined mission profiles, aerodynamic shape and launch mass as specified by NASA. Trade-off assessment of the thermal protection system clearly indicates the Lockalloy to be more cost-effective than the LI-900 RSI configuration, and to a lesser degree than the Ablator TPS. Both the Ablator configuration and Lockalloy configuration are recommended as the Phase II candidates. Engine combination analysis concluded the kerosene fueled LR-105 engine with 12 LR-101 vernier engines to be the'most effective combination as the Phase II study candidates. The LR-99 engine with two LR-11 engines is also recommended for the Phase II study. Trade studies have systematically narrowed the configuration to the four most promising for the Phase II analytical study. In addition to meeting all require- ments set forth by NASA for the X-24C they are the most cost-effective and pro- vide the maximum payload mass capability for research activities. Design refinement during the Phase II study will include analytical analysis to expand the selected configurations and an assessment of the impact to boost the vehicle to higher mach numbers. v/vi TABLE OF CONTENTS Page Foreword iii/iv Summary v/vi Introduction , 1 Basis for Design 3 Candidate Vehicles 8 Technical Approach 9 Mission Profiles I 10 Realistic Designs 29 Load Analysis 31 Structural Analysis Models 36 Wing Analysis 60 Fuselage Analysis 91 Thermal Analysis 137 Landing Gear Selection 170 Propulsion System Installation 176 Propellant Tankage - Volumetric Analysis 186 Structural Arrangement 189 Functional Systems 207 Structural Dynamics Analysis 216 Mass Analysis 221 Cost Analysis • 266 Flight Support and Maintenance Analysis 293 Research Capabilities 307 Risk Assessment 309 Trade Study Results 312 Trade Study Recommendations 315 Vll TABLE OF CONTENTS (Continued) Page Review of Phase n and HI Studies 316 References 317 APPENDICES A - NASA Statement of Work 323 B - NASTRAN Output - Unit Surface Loading and Shear Flows 341 C - Cost Trade Studies - Escalation Factor 347 D - X-24C Major Equipment Items 349 Vlll LIST OF FIGURES Number Title Page A Aerodynamic Configuration 4 1 Trim Lift Characteristics 12 2 Zero Lift Drag 13 3 Drag Due to Lift 13 4 Lift/Drag Characteristics with Scramjets 14 5 LR-99 Throttled Performance 16 6 LR-105 Throttled Performance 16 7 LR-105 DT Derated Thrust Performance 17 8 LR-105 ALC Thrust 17 9 LR-11 Thrust 18 10 LR-101's Throttled Performance 18 11 Launch/Boost Control by Pitch Attitude Schedule 20 12 Typical Boost Profile 21 13 Deceleration and Descent Path for Cross-Range 24 14 Deceleration Control 24 15 Mission Profiles - Altitude/Mach vs Time 25 16 Mission Profiles - q, NZ, a vs Time 25 17 Mission Profiles - Mach vs Altitude 27 18 Mission Profiles - Altitude vs Distance 27 19 Analysis Program 30 20 Wing Spanwise Load Intensities - Pullup after B-52 Launch (Aluminum Design) 35 21 Wing Spanwise Load Intensities - Subsonic Flight Negative One G (Aluminum Design) 35 22 Wing Surface Load Intensities - Pullup after B-52 Launch (Lockalloy Design) 38 23 Wing Surface Load Intensities - Maximum Temperature 38 Gradients (Lockalloy Design) 24 Wing Surface Load Intensities - Comparison 39 IX LIST OF FIGURES (Continued) Number Title Page 25 NASTRAN Model 40 26 NASTRAN Structural Model - Wing 43/44 27 NASTRAN Frame Model, F. S. 498 42 28 NASTRAN Frame Model, F. S. 553 42 29 NASTRAN Structural Model - Fuselage 45/46 30 NASTRAN Structural Model, F. S. 496 (Lockalloy Design) 48 31 Air frame Structural Arrangement - Aluminum 50 32 Fuselage Extensional and Shear Thicknesses Input into the Aluminum Design Structural Model 51 33 Wing Surface Extensional and Shear Thicknesses - Aluminum 52 34 Wing Rear Beam Vertical Displacement 53 35 Fuselage Lower Centerline Vertical Displacement 53 36 Wing Surface Load Intensities - Pullup 54 37 Wing Surface Load Intensities - Subsonic 54 38 Fuselage Load Intensities for Pullup After Launch 55 39 Fuselage Panel Thicknesses Input - Lockalloy 56 40 Wing Surface Extensional and Shear Thicknesses - Lockalloy Design 58 41 Wing Surface Load Intensities, Pullup - Lockalloy Design 58 42 Wing Surface Load Intensities,' Maximum Maneuver - Lockalloy Design 59 43 Wing Surface Load Intensities, Maximum Temperature Gradient Condition - Lockalloy Design 59 44 Fuselage Thermal Stress 60 45 Wing Arrangement - Aluminum 64 46 Wing Arrangement - Lockalloy 64 47 Wing Point Design Regions 66 X LIST OF FIGURES (Continued) Number Title Page 48 Wing Surface Load Intensities, Pullup - Aluminum Design 66 49 Wing Surface Load Intensities, Pullup - Lockalloy Design 67 50 Wing Surface Load Intensities, Maximum Temperature Gradient Condition - Lockalloy Design 67 51 Cross Sectional Geometry of Surface Panel Concepts 70 52 Notation of Panel Dimension and Loading 70 53 Temperature History - Aluminum/LI-900 Design 79 54 Temperature History - Aluminum/LI-900 Design 79 55 Insulation Thickness - LI-900 as Function of ' Temperature 80 56 Wing Box Unit Mass - Point Design Region 2 81 57 Estimated Ablator Thicknesses 84 58 Ablator Thicknesses as Function of Panel Thickness 84 59 Wing Box Unit Mass, Point Design - Aluminum/Ablator Design 85 60 Wing Upper Surface Panel Thicknesses 86 61 Wing Lower Surface Panel Thicknesses 86 62 Detail Mass Breakdown, Point Design - Lockalloy Design 88 63 Aluminum
Details
-
File Typepdf
-
Upload Time-
-
Content LanguagesEnglish
-
Upload UserAnonymous/Not logged-in
-
File Pages366 Page
-
File Size-