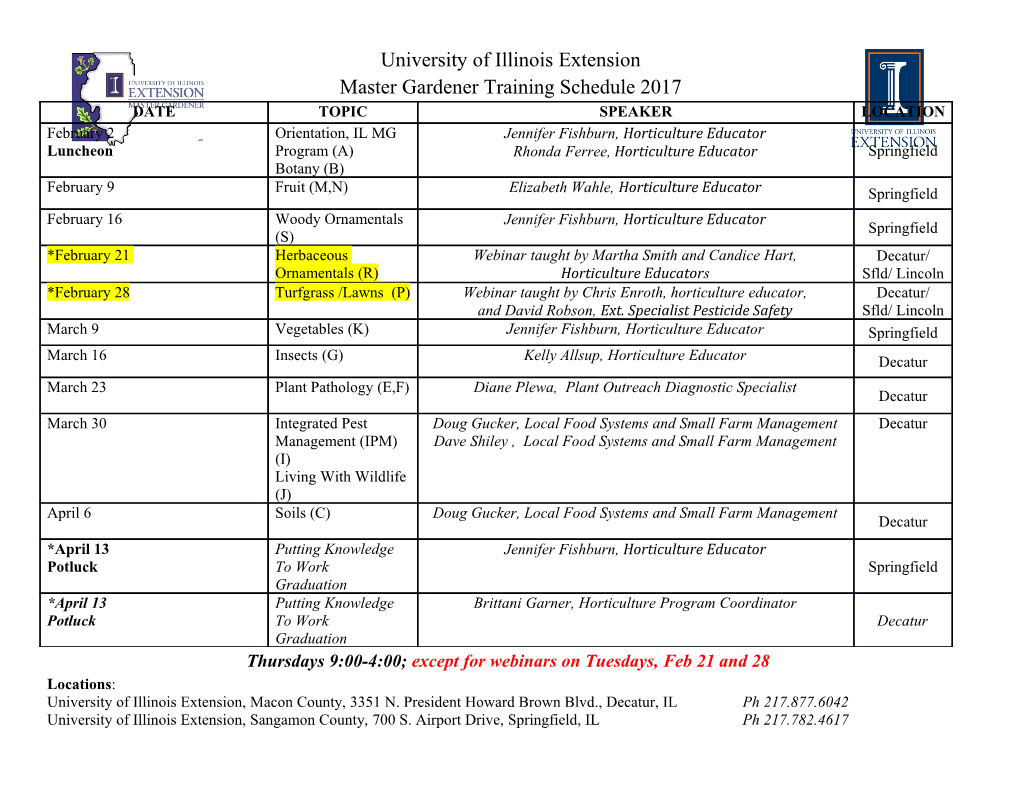
FRACTURE TOUGHNESS OF RAILWAY TRACK MATERIAL USING FINITE ELEMENT ANALYSIS MOHD NURUL AKMAL BIN MOHD YUSOF Thesis submitted in fulfilment of the requirements for the award of the degree of Bachelor of Mechanical Engineering Faculty of Mechanical Engineering UNIVERSITI MALAYSIA PAHANG DECEMBER 2010 i AWARD FOR DEGREE Bachelor Final Year Project Report Report submitted in partial fulfilment of the requirements for the award of the degree of Bachelor of Mechanical Engineering. ii SUPERVISOR’S DECLARATION I hereby declare that I have checked this project and in my opinion, this project is adequate in terms of scope and quality for the award of the degree of Bachelor of Mechanical Engineering. Signature : .................................... Name of Supervisor : MADAM NORHAIDA BINTI ABD. RAZAK Position : LECTURER OF MECHANICAL ENGINEERING Date : 06 DECEMBER 2010 iii STUDENT’S DECLARATION I hereby declare that the work in this project is my own except for quotations and summaries which have been duly acknowledged. The project has not been accepted for any degree and is not concurrently submitted for award of other degree. Signature : .................................. Name : MOHD NURUL AKMAL BIN MOHD YUSOF ID Number : MA08008 Date : 06 DECEMBER 2010 v ACKNOWLEDGEMENTS I am grateful and would like to express my sincere gratitude to my supervisor Madam Norhaida Binti Abd Razak for her germinal ideas, invaluable guidance, continuous encouragement and constant support in making this research possible. She has always impressed me with her outstanding professional conduct, her strong conviction for science, and her belief that a Degree program is only a start of a life-long learning experience. I appreciate her consistent support from the first day I applied to graduate program to these concluding moments. My sincere thanks go to all my lab mates and members of the staff of the Mechanical Engineering Department, UMP, who helped me in many ways and made my stay at UMP pleasant and unforgettable. Many special thanks go to member engine research group for their excellent co-operation, inspirations and supports during this study. I acknowledge my sincere indebtedness and gratitude to my parents for their love, dream and sacrifice throughout my life. I cannot find the appropriate words that could properly describe my appreciation for their devotion, support and faith in my ability to attain my goals. Special thanks should be given to my committee members. I would like to acknowledge their comments and suggestions, which was crucial for the successful completion of this study. vi ABSTRACT Railway track are used as way for carrying cargo or passengers from one place to another place. Nowadays, Malaysia still using the old railway line and accidents can happen at any time due to several factors, namely high density load of railroad rails, cracks due to vibration and friction wheel. Therefore, in this project the analysis is to prevent and predict the occurrence of harm or injury to passengers, and goods. The objective of this project is to determine the value of fracture toughness of railway track material using analytical solution. Finite element analysis is used to find the value of stress that has been used in analytical equation. The design of the model specimen drawn by Solidworks software and then imported into the Patran software to key in data such as load, material, element, and properties. Then, Nastran software is used as a solver and decision analysis model will be produced when the specimen is successful simulated. Comparisons are made between the simulation using finite element analysis and previous research. The result shows that the fracture toughness decreasing when the thickness is increasing. The average value of fracture toughness found was 39.02 MPa.√m. It is said to be plane strain fracture toughness. vii ABSTRAK Landasan rel keretapi digunakan sebagai laluan untuk membawa muatan atau penumpang dari suatu tempat ke tempat yang lain melalui laluan tertentu. Saat ini, Malaysia masih menggunakan laluan kereta api lama dan kemalangan boleh terjadi pada bila-bila masa saja disebabkan oleh beberapa faktor, iaitu beban yang tinggi pada rel kereta api, retak kerana getaran dan geseran pada roda. Oleh kerana itu, analisa ini adalah untuk mengelakkan berlakunya kerosakan atau kecederaan pada penumpang, dan barang-barang. Tujuan dari projek ini adalah untuk menentukan nilai ketangguhan retak menggunakan penyelesaian analitis. Analisis unsur terhingga digunakan untuk mencari nilai tekanan yang telah digunakan dalam persamaan analitis. Spesimen reka bentuk model dilukis dengan menggunakan perisisan Solidworks dan selepas itu dimasukan ke dalam perisian Patran untuk memasukkan data seperti beban, bahan, unsur, dan sifat. Kemudian, dengan menggunakan perisian Nastran untuk analisis dan model analisis keputusan akan dihasilkan ketika spesimen berjaya disimulasikan.Perbandingan dilakukan antara simulasi dengan menggunakan penyuluh dan penelitian terlebih dahulu. Keputusan kajian menunjukkan pada ketangguhan retak berkurang dengan ketebalan meningkat. Nilai rata-rata Ketangguhan retak ditemui adalah 39.02 MPa.√m. Hal ini dikatakan regangan bidang ketangguhan retak. viii TABLE OF CONTENTS Page AWARD FOR DEGREE i SUPERVISOR’S DECLARATION ii STUDENT’S DECLARATION iii ACKNOWLEDGEMENTS v ABSTRACT vi ABSTRAK vii TABLE OF CONTENTS viii LIST OF TABLES xi LIST OF FIGURES xii LIST OF SYMBOLS xiii LIST OF ABBREVIATIONS xiv CHAPTER 1 INTRODUCTION 1.1 Introduction 1 1.2 Background of Study Problem 4 1.3 Project Objectives 5 1.4 Problem Statement 5 1.5 Scopes of Projects 6 CHAPTER 2 LITERATURE REVIEW 2.1 Introduction 7 2.2 Fracture Ductility 7 2.3 Fracture Toughness 9 2.3.1 Role of Material Thickness 10 2.3.2 Plane Strain and Stress 10 2.3.3 Plane-strain Fracture toughness Testing 12 2.3.4 Uses of Plane-Strain Fracture Toughness 13 2.4 Typical Rail Defects 15 2.5 Finite Element Analysis 17 ix CHAPTER 3 METHODOLOGY 3.1 Introduction 19 3.2 Project Planning 19 3.3 Software Requirement 22 3.4 Model Design 22 3.5 Model Analysis 24 3.6.1 Patran and Nastran Software 25 3.6 Analytical Calculation 26 3.7 Finite Element Analysis Calculation 26 3.8 Result Verification 28 CHAPTER 4 RESULTS ANALYSIS AND DISCUSSION 4.1 Introduction 29 4.2 Finite element analysis using Patran and Nastran 29 4.2.1 The result of simulation for thickness 3.50mm 4.2.1 The result of simulation for thickness 5.00mm 4.2.1 The result of simulation for thickness 20.00mm 4.2.1 The result of simulation for thickness 50.00mm 4.3 Results for fracture toughness of railway track material 34 4.4 Plane strain fracture toughness 36 4.4.1 Fracture toughness evaluation for simulation 36 4.5 Theory calculation for previous research 38 4.5.1 Fracture toughness evaluation 38 4.5.2 Result verication 38 4.6 Problems and Errors 39 CHAPTER 5 CONCLUSIONS & RECOMMENDATION 5.1 Conclusion 40 5.2 Recommendation 41 REFERENCES 42 x APPENDIX 44 A Solidworks, Patran and Nastran Software 44 B Result from the Patran and Nastran Software 46 C Gantt Chart 50 D Run the simulation 51 xi LIST OF TABLES Table No. Page 1.1 Number of accidents on the Swedish railways, including suicide or attempted suicide, from 1997 to 2003 2 3.1 Sample dimension of beam 23 3.2 Properties of Mild Steel 24 4.1 Result for fracture toughness 33 4.2 Result for fracture toughness 38 xii LIST OF FIGURES Figure No. Page 2.1 Schematic diagram of load versus load point displacement showing difference in fracture ductility of mild steel 8 2.2 Type mode of fracture 9 2.3 Schematic representation showing the effect of the plate thickness on the fracture toughness 11 2.4 Common specimen configuration for fracture toughness test CT specimen (left) and SENB specimen (right) 13 2.5 Typical rail defects 15 2.6 Process of Finite element analysis 18 3.1 Project’s Flow 20 3.2 Flow chart shows the overall flow of the process of this Project 21 3.3 The dimension of beam 23 4.1 Single Edge Notch Bend (SENB) model geometry 28 4.2 After Simulation using Patran and Nastran 29 4.3 Thickness 3.5mm 30 4.4 Thickness 5.0mm 30 4.5 Thickness 15.0mm 31 4.6 Thickness 50.0mm 32 4.7 Maximum stress versus thickness 32 4.8 Effect of thickness on Kc behaviour for mild steel 34 xiii LIST OF SYMBOLS KI is the fracture toughness in MPa.√m σ is the applied stress in MPa a is the crack length in meters or inches Y geometry factor load, kN P΅ S span length B specimen thickness, mm W specimen width f geometrical factor ʠ2ʡ xiv LIST OF ABBREVIATIONS ASTM American Standard Testing Method SENB Single Edge Notch Bend CT Compact Tension FEM Finite Element Method FEA Finite Element Analysis 1 CHAPTER 1 INTRODUCTION 1.1 INTRODUCTION Rail track network forms an essential part of the transportation system of a country and plays a vital role in its economy. It is responsible for transporting freight and bulk commodities between major cities, ports and industries, and carrying passengers, especially in urban areas. Hundreds of millions of dollars are spent each year for the construction and maintenance of rail tracks in large countries like the USA, Canada and Australia. The efficient and optimum use of these funds is a challenging task which demands innovative and cutting edge technologies in railway engineering. The efficiency and safety of a railway track, including passenger comfort, depends on the complex interaction of various system components in response to the cyclic wheel loading of various magnitudes and frequencies (Indraratna B. and Salim W.,2005). Nevertheless, the annual frequency of accidents with people kills or seriously injured is strikingly high, and more than half of these accidents happen under circumstances that suggest suicide or attempted suicide.
Details
-
File Typepdf
-
Upload Time-
-
Content LanguagesEnglish
-
Upload UserAnonymous/Not logged-in
-
File Pages24 Page
-
File Size-