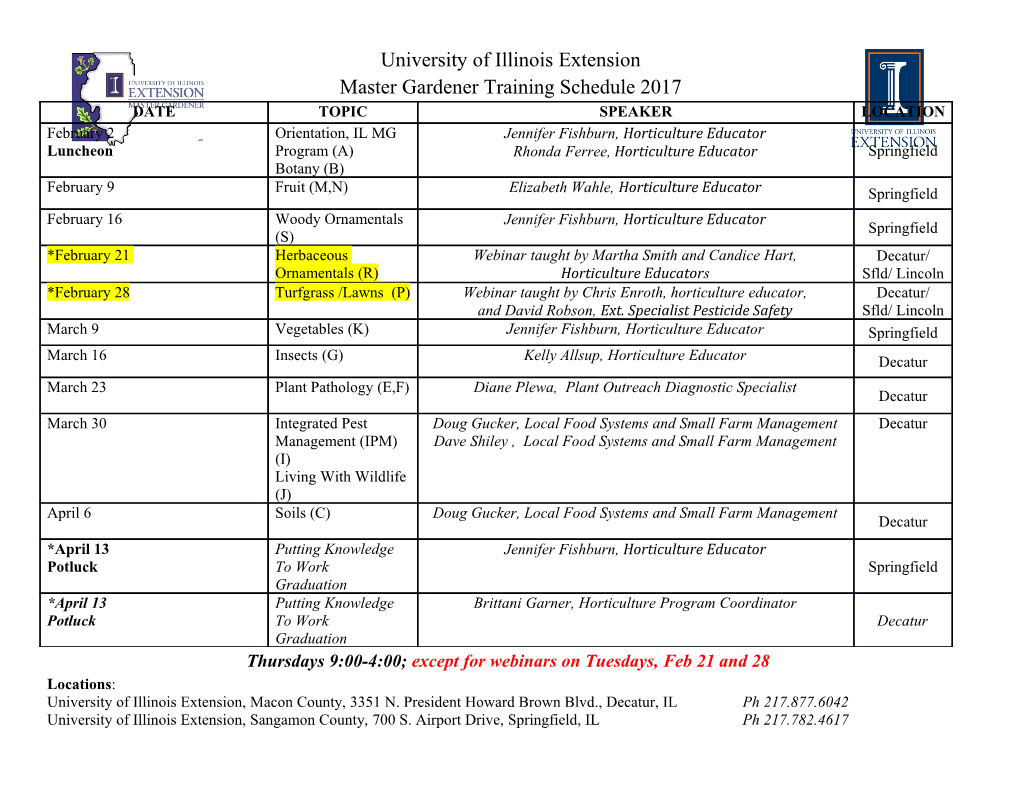
THE AMERICAN SOCIETY OF MECHANICAL ENGINEERS 345 E. 47th St., New York, N.Y. 10017 97-GT-171 The Society shall not be responsible for statements or opinions advanced in papers or discussion at meetings of the Society or of its Divisions or Sections, or printed in its publications. Discussion is printed only if the paper is published in an ASME Journal. Authorization to photocopy material for Internal or personal use under circumstance not falling within the fair use provisionsof the Copyright Act is granted by ASME to libraries and other users registered with the Copyright Clearanoa Center (CCC) Transactional Reporting Service provided that the base lee of $0.30 per page is paid directly to the CCC, 27 Congress Street Salem MA 01970. Requests for special permission or bulk reproduction should be addressed to the ASME Technical Rdaishing Department Copyright CD 1997 by ASME All Rights Reserved . Printed in U.S.A Downloaded from http://asmedigitalcollection.asme.org/GT/proceedings-pdf/GT1997/78682/V001T02A003/2408503/v001t02a003-97-gt-171.pdf by guest on 02 October 2021 Research into the Drive Transition of 1111111111111111111111111 Combined Diesel or Gas Turbine Plant BREAK ZANG SHUSHENG MENG HONGTAO LI SHUYING SUN HAIOU Dept of Power Eng. Harbin Engineering University, Harbin 150001, P. R. C. C. ng = rotational speed of output shaft of gas turbine [rpm) T = time needed for changing diesel engine fuel control lever [s] ABSTRACT Ta = elan:magnet time constant of servomotor used for fuel A small test installation of Combined Diesel or Gas control [s] turbine(C0000) was made, its primary aimed at investigating the Tm = machine time constant of servomotor used for fuel control [a] changes of various operational parameters of the two engines in the Go = voltage of signal with set diesel speed [mV] change-over process. Firt the computer sinmation of this process is 6(s) = trattsfonnation function of speed governor cared out it the papa. Variations of torque turd rotational speed on gp = coefficient the transmission shafts wider different rates of fuel supply and the Kind = coefficient affect of hydraulic coupling on the change -over process are investigated. Then, the comparison i/3 made of variation of speed and 86 = real angle of engine fuel control lever [degree] torque by?! governing with that by PID governing. The rack shows 04 = ogle of tel control lever [degree] that the rate of increase or decrease of diesel engine Awl supply has singnificant effect on the variation of torque, and the change of = caltnroPI governor Sin* angle [degree] parametas in governing system has markable effect on the speed and torque in change-over process, especially on the peake value of diesel engine torque. INTRODUCTION At present CODOG plants have become a main type of NOMENCLATURE propulsion plant for major surface warship' s. The altinnative Md = torque of diesel engine (Mn) operation of diesel engine and gas turbine leads them to bring their My = torque of input shaft of hydraulic coupling (Mn] tam into full play, thus the Vasa= of propulsion plant is Jd ornament of inertia of shafting of diesel engine [kg.m.e 2] kept efficient The change-over between two engines is a special process of CODOG pin In this process, in order to reduce the = total moment of inertia of output shaft of hydraulic coupling mechanical impact between gears and within the coupling, it is and input shaft of SSS check [kg,m22 1 required to make the speed difference in power trammtinion between the two engines as minimum as possible. Therefore, how to control Jg a total mane= of inertia of output shaft of gas turbine and the principal parameter% such as the fuel supply, the rate of inmate input shaft of $SS clutch [kg.m.s2] or decrease of engine fuel supply, and the corresponding change of a a total moment of output shaft of SSS clutch and shaft of engine load, is essential for meeting the above-mentioned requitement_ Consequently, the study of this problem becomes hydraulic dynamometer [k&nial] indispensable to the application of CODOG plant ad a rotational speed of diesel engine [rpm] Based on a small test imitation of CODOG plant, which is to be rotational speed of input shaft of hydraulic coupling [rpm] used for experiment, we calculated variations of torque and MIUMaran BY nf rotational speed of shalt of hydraulic dynamometer [rpm] speed on the output shafts and hydraulic coupling shafts of the two Presented at the International Gas Turbine & Aeroengine Congress & Exhibition Orlando, Florida — June 2-June 5,1997 engines. The calculation shows that the rate of increase or decrease of engine fuel supply in the change -over process deserves extra attention in the design and use of a CODOG plant_ Mt -Mr =(Js -Jf ) titdi ) 3x4 ( TEST INSTALLATION nt = nf The diagram of test installation of the CODOG plant is shown in Fig. 1. It consists of a single-shaft constant-speed gas turbine, a diesel engine, hydraulic coupling two Synchronons-Self-Shifting (SSS) In case the load is taken by diesel engine only, the SSS cluth on rletrbps, gas rmbine side is disengaged, the output shaft of gas turbine is a gearbox ad a hydraulic dynamometer. The principal/ Downloaded from http://asmedigitalcollection.asme.org/GT/proceedings-pdf/GT1997/78682/V001T02A003/2408503/v001t02a003-97-gt-171.pdf by guest on 02 October 2021 parameters of the two engines are as follows: cormected with the input end of SSS clutch only. Gas turbine: rated pow Z34 kw In addition to Eq.(1), there are other equations as below. rated rpm 1500 For gas turbine shaft and input shaft of SSS clutch no-load rpm 1560 Diesel engine: rated power 35 kw M = J dnz (5) MS rpm 2000 g gdt For output shaft of hydraulic coupling and hydraulic dynamometer shaft I gas turbine I—I S.S.S gear box mdYn eteer el dialf H dt (8) diesel rrcoi ing E fly = of In case the diesel engine, gas turbine and dynamometer work in common, the output shaft of hydraulic coupling, gaa turbine shaft and Fig.] Diagram of CODOG test Installation dynamometer shaft maintain the same speed. In addition to Eq.(1), there are other equations as blow EQUATION OF CHANGE -OVER PROCESS M +M -M =(J +J +J ) dnY The mathematical desaeption of the change-over process of a y syr dt (7) CODOG plant thin mode is mainly given by equations of motion of n = n =111 engine rotors, chat equations of speed governing hydrolic 7 coupling and load- In addition, the composition of equations may Besichs, the ton carves betw-een the Epee& torque and angle vary slightly in light of the regime of change-over process. of fuel control lever 8d, that expresses the governing characteristic of In case the load is taken by the gas turbine only, the SSS clutch dismal engine, are given in this paper by way of experimental on the diesel engine side is disengaged, the output shaft of the measurement It is expressed in the form below hydraulic coupling works together with one end of the SSS clutch ht, = (8) only. The equations are as follows. Kaaet, The motion equation of diesel engine and input shaft of the in which, Odd is the real angle of engine fuel control lever, mid lrychudic coupling Eldf 3d-Om In fact, the change rate of this parameter reflects the rate of fuel °Piny, On is the centrifugal governor adjusting angle. There M 4 -M y = Ja d&ind (1) is where, Md is an output torque of diesel engine, M y is tm input torque 8, = Kat% of the hydraulic coupling. Jd is the moment of inertia of both the So that, according to Eq.(1) shafts of diesel engine and the input end of hydraulic coupling. This equation will not vary in both cases below. The Jy is the moment of inertia of both output shaft of hydyalic ea --My = Old +1.4 —dad ) ( 9 ) coupling and input shaft of the SSS clutch, and the motion equation 1C4,4 dt of them is 1 2rad where 1.4 = du, M = J K K d 60 7 7 dt (2) M _ The gas turbine used in our ten installalion operates in constant The motion equation of gaa turbine and dynainomeier shaft is speed mode. Btu the speed vanes slightly raider different conditions of load. According to experimental data, we have the following relation between torque ad speed: 2 1750 1750 1700 1700 1850 1850 1603 ietx) 1 1550 1 1550 1500 15C0 Downloaded from http://asmedigitalcollection.asme.org/GT/proceedings-pdf/GT1997/78682/V001T02A003/2408503/v001t02a003-97-gt-171.pdf by guest on 02 October 2021 case! 1450 +-03upliig 1450 geStufbil 1400 444ynemometer 1400 1350 135° 0 50 100 150 200 250 300 350 400 0 50 100 150 200 250 300 350 400 ane(s) 11mM 203 odesd 150 -scOlitUng 150 -rgesturbin -*dynamometer kat 100 S 50 -50 -100 -100 50 100 150 ED 250 TO 360 400 0 SO 100 150 200 250 300 350 400 time tane(s) Ftgl Variation of speed and torque with T-10 seconds F1g.3 Vartadon of speed and torque with T-60 seconds i K y (n p -or) ago > nr (10) thar M I = 10 n s nr Ky K 7 (12) where, ago is the gas Outline speed with no load and a y is thin with 1 22 T = K— (J. +Jy +Jr ) load. y 60 • The torque toomitted by hydraulic coupling is a inaction of The load of this test instant/on is provided by a hydraulic difference between the pump wheel speed rrp and the mrbine wheel dynamometer.
Details
-
File Typepdf
-
Upload Time-
-
Content LanguagesEnglish
-
Upload UserAnonymous/Not logged-in
-
File Pages6 Page
-
File Size-