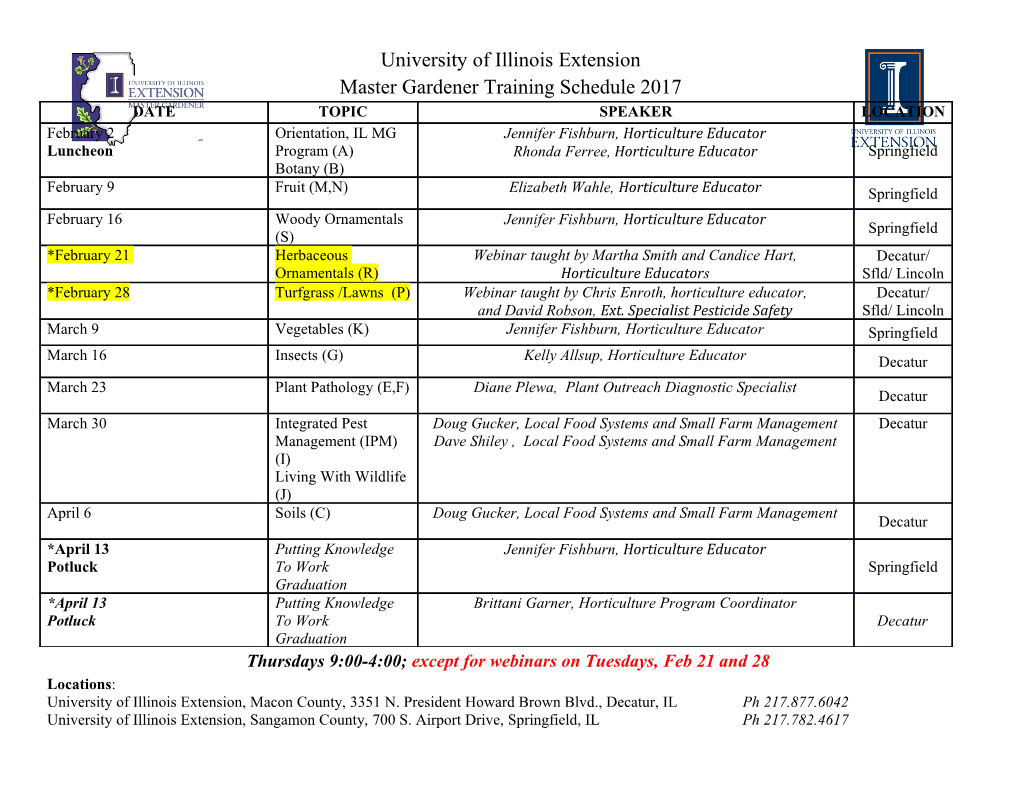
PAPER Dynamic Analysis of Stresses and Evaluation of Service Life of Jointed Rails Hiroo KATAOKA Yuya OIKAWA Osamu WAKATSUKI Senior Researcher, Researcher, Senior Researcher, Track Structures & Components G., Track Technology Div. Noritsugi ABE Nihonkido Kogyo Co., LTD Jointed rails are replaced periodically in Japan. Their service life is governed mainly by the fracture at the joints. To evaluate the fatigue life of jointed rails, it is necessary to verify the stress distribution around fish-bolt holes and an S-N curve of jointed rails. Therefore, we carried out static loading tests in a laboratory and field tests to measure the stresses around the fish-bolt holes, and further dynamic stress analysis of jointed rails and bending fatigue tests of rails used in the field. The dynamic stress analysis model is composed of a beam model to calculate dynamic wheel/rail contact forces and a solid model to calculate stress distribution resulting from those contact forces. These models were validated using field test data. Based on the study results, we established a method to evaluate the fatigue life of jointed rails. In this method, we calculated the stresses under several combined conditions of jointed rail, vehicle type and vehicle speeds. The fatigue life was calculated by applying the stresses to the S-N curve. As a result, the rail replacement period have a potential to be extended except in cases of heavy wear between a fishplate and rail. KeywordsKeywords: jointed rail, stress, fish bolt hole, fatigue, service life 1. Introduction 2. Jointed rail stress To ensure operational safety, ultrasonic detection of Stress measurement positions are shown in Fig. 2. rails is carried out during maintenance, replacements The stresses were measured at 5 mm and 0 mm posi- made periodically to prevent rail fractures. The service tions away from the edge of fish-bolt holes in the 45- life of jointed rails is governed mainly by the fatigue frac- degree direction to the rail's longitudinal axis using ture at joints. There are several types of fracture, with uniaxial strain gauges. The reason for measuring at po- cracks tending to emanate from the paticularly prone sitions 5mm away is that the gauges at the 0 mm posi- fish-bolt holes, as shown in Fig. 1. As vehicles have be- tion might come in contact with the bolt holes and ren- come lighter, the number of fractured jointed rails has der the readings useless. The averages of measured val- decreased in recent years, so it is likely that rail replace- ues at 5 mm away from positions inside and outside track ment periods can be extended. gauge are called F1 (the average of F11 and F12) and F2 In order to verify the stress distribution around fish- (the average of F21 and F22) respectively, as shown in bolt holes, we had performed static loading tests and field Fig. 2. The measured values at 0 mm points are called tests as well as static stress analysis. Bending fatigue H1 and H2, as shown in Fig. 2. tests of new jointed rails had been also carried out. Running direction In this study, several tests, dynamic stress analysis and fatigue tests of used rails were carried out to evalu- ate service life accurately. Inside: F11 Outside: F12 45-degree H1 5mm H2 Inside: F21 Outside: F22 Inside: inside track gauge Fig. 1 Rail fracture at a joint Outside: outside track gauge Fig. 2 Stress measurement positions 250 QR of RTRI, Vol. 46, No. 4, Nov. 2005 Table 1 Technical details of test track structure 40 H2max. Item Specifications Rail type 50kgN rail H1max. ) 20 Type for jointed rail 2 Joint Fastening (50kgN) type H1min. Other Type 5(for 50kgN) Railpad stiffness 110 MN/m (N/mm -40 Sleeper Joint Wooden tie for joint Stress amplitude type Other PC sleeper type 6 H2min. Sleeper spacing 39 sleepers / 25 m -80 01020304050 Fishbolt fastening 500 Nm torque Velocity (km/h) Fig. 4 Stress amplitudes under stepped joint and elastic 2.1 50kgN rail joint field test (1) support conditions Running tests of a track vehicle on a tangent test increases. The negative peak value of H2 and the posi- track of a meter-gauge line were carried out to confirm tive peak value of H1 are caused by the impact wheel the basic characteristics of bolt hole stresses under clear load on the joint, so that the impact load increases un- substructure conditions. The technical details of test der stepped joint conditions. track structure are shown in Table 1. The rail was sawn into two parts, holes were drilled and rail joints as- 2.2 50kgN rail joint field test (2) sembled, so there were no irregularities on the top sur- faces of the jointed rails. To create another rail joint with In order to verify the relationship between impact a 1 mm step at the joint, shims were inserted between wheel load on the joint and stress variations, field tests the fishplates and the rail. Five sleepers around the joints were carried out with a test vehicle on which the wheel were wooden and the others were PC sleepers. load and lateral force were measured. Concrete supports were cast under the five wooden The test section was composed of ballasted track with sleepers and two supporting conditions were set, one by 50kgN rails on a 500 m radius curved section of meter- the insertion of rubber mats of 70 MN/m stiffness be- gauge line. The cant was 55 mm. The measurement was tween the concrete supports and wooden sleepers and performed at a low rail joint. The test vehicle was a Type- the other without rubber mats inserted (rigid support). 103 EMU used on local lines, set up for empty or loaded The stress variations around bolt holes at 5 km/h conditions. The velocity was set at between 10 km/h and under rigid support and no irregularity conditions are 70 km/h at 10 km/h intervals. shown in Fig. 3. The stress was set at 0 when the joint The ratio of lateral force to the wheel load was 0.02- bolts were fastened. The stresses of F11 and F12 decrease 0.12, which is small; therefore the stress variations were rapidly when the vehicle passed the joint gap. The analyzed relating to the wheel load. The wheel load was stresses of F11 and F12 as well as F21 and F22 have filtered out with a low-pass 100 Hz filter. Fig. 5 shows negative and positive smooth peak values behind the the relationship between the impact wheel load and the joints. These characteristics were consistent with past stress variations. F1min denotes the average of the mini- static test and analysis results. mum F11 and the minimum F12, and F2max and F2min Fig. 4 shows the maximum and minimum stress mean respectively the average of the maximum value of variations under stepped joint and elastic support F21 and F22 and the minimum value of F21 and F22. condintions. The stress amplitudes increase as velocity Each solid line in the figure shows a regression line. F2min correlates with the wheel load, however, F1min 20 and F2max don't correlate with the wheel load because Gap ) 10 2 40 0 F12 ) 30 2 (N/mm -10 F11 − 7.54 Stress variation 20 F2max = 0.10 P -20 2 10 R = 0.26 -500 0 500 1000 0 20 F2min = − 0.21 P − 2.05 F21 -10 R2 = 0.66 ) 10 2 F1min = − 0.25 P − 7.93 -20 0 2 F22 R = 0.36 Stress amplitude (N/mm (N/mm -10 -30 Stress variation -40 -20 0 20406080100120 -500 0 500 1000 Impact wheel load (kN) Distance (mm) Fig. 5 Relationship between impact wheel load and stress Fig. 3 Stress variations around bolt holes amplitude QR of RTRI, Vol. 46, No. 4, Nov. 2005 251 the impact wheel load caused the former and the latter comotives passed. The ratio of stresses at the edge of the occurred at the point distant from the joint gap, as shown hole against those at a position 5 mm away at an angle in Fig. 3. of 45 degrees was less than 3.0. The results validate the previously calculated estimation that the ratio is less 2.3 60kg rail joint field test than 3.0. The bending stresses of the trailing rail measured 60kg rail joint field tests were carried out on a tan- at positions 280 mm away from the rail end are called gent section of ballasted track on a meter-gauge line. S1 (inside track) and S2 (outside track). They become We set three conditions on jointed rails, which were nor- greater in local train, limited express and locomotive mal state, with a loose sleeper and with a worn fish- order as shown in Fig. 6(b). The maximum value was 51 plate. The tests were carried out for limited express, N/mm2 under the worn fishplate condition when loco- local and freight trains. Inserting steel plates between motives passed. the rail and the sleepers adjacent to joints set the condi- tion of a loose sleeper with a 3 mm gap between the 2.4 Static lateral loading tests sleeper and ballast. The worn fishplates were made ar- tificially by inserting 1 mm cuts into their bottom end Static loading tests, performed on a rail with nine and top centers. sleepers, were carried out to clarify the effect of a lat- We clarified the effect of the vehicle speed, wheel eral load on the stresses. The sleepers were set on a rigid load and lateral force on the measured stress amplitudes bed, pressed down by anchor bolts and ballast mats be- under each condition by multiple regression analysis, tween the sleepers and the rigid bed with a stiffness of substituted the parameters averaged under each condi- 30 MN/m.
Details
-
File Typepdf
-
Upload Time-
-
Content LanguagesEnglish
-
Upload UserAnonymous/Not logged-in
-
File Pages6 Page
-
File Size-