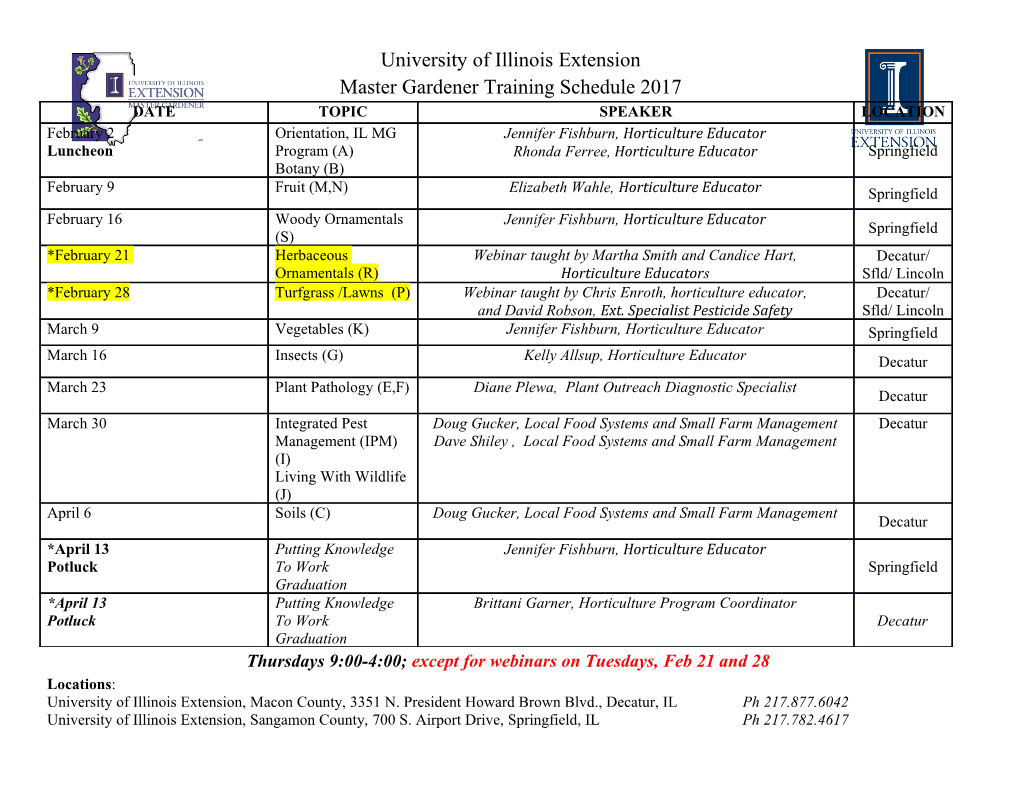
Chain shot injures operator behind cab window In 2004, the operator of a mechanical harvester was trimming the butt end of a 12-inch log. The saw bar and chain were directly in line with the front window of the operator’s cab. The saw chain had been repaired with used connecting links. While the saw chain was operating at high speed, the chain broke. The whipping action of the broken chain end then caused a drive link to separate from the chain. It penetrated the ½-inch polycarbonate windshield of the cab. This “chain shot” struck the operator, causing severe internal injuries. Although this incident occurred in 2004, chain shot is still a hazard and this older incident investigation report is being posted on the WorkSafeBC website for educational purposes. Purpose of this report The purpose of this online incident investigation report is to identify the causes and contributing factors of this incident to help prevent similar incidents and to support preventive actions by industry and WorkSafeBC. This online version is not the official WorkSafeBC report. It has been edited to remove personal identifying information and to focus on the main causes and underlying factors contributing to this incident. Notice of Incident information Number: 2004110596 Outcome: Injury Core activity: Mechanized falling/processing Region: Coastal British Columbia Date of incident: November 2004 WorkSafeBC Investigations WorkSafeBC (Workers’ Compensation Board of B.C.) Page 1 of 18 NI number: 2004110596 www.worksafebc.com Table of Contents 1 Factual Information ............................................................................................... 3 1.1 Workplace ..................................................................................................................... 3 1.2 Sequence of events ........................................................................................................ 3 1.3 Chain shot ..................................................................................................................... 5 1.4 Saw bar.......................................................................................................................... 5 1.5 Saw chain ...................................................................................................................... 6 1.6 History of chain problems at the worksite .................................................................... 9 1.7 Operator manuals ........................................................................................................ 10 1.7.1 Dangle head operator’s manual ...................................................................... 10 1.7.2 Saw chain manufacturer .................................................................................. 10 2 Analysis ................................................................................................................ 11 2.1 Saw bar orientation ..................................................................................................... 11 2.2 Windshield .................................................................................................................. 11 2.3 Saw cut drift ................................................................................................................ 11 2.4 Chain shot analysis ..................................................................................................... 12 2.4.1 Saw chain damage........................................................................................... 12 2.4.2 Effect of previous chain breakage on rivet assemblies ................................... 12 2.4.3 Saw chain repair .............................................................................................. 13 2.4.4 Side loading .................................................................................................... 13 2.4.5 Saw chain tension ........................................................................................... 13 2.4.6 Saw chain speed .............................................................................................. 13 2.5 Drive sprocket wear .................................................................................................... 14 2.6 Chain wear .................................................................................................................. 14 2.7 Saw bar........................................................................................................................ 14 2.8 The chain shot sequence ............................................................................................. 15 3 Conclusions ......................................................................................................... 15 3.1 Findings as to causes ................................................................................................... 15 3.1.1 Saw chain failure............................................................................................. 15 3.1.2 Saw bar orientation ......................................................................................... 16 3.1.3 Inadequate windshield protection ................................................................... 16 3.2 Findings as to underlying factors ................................................................................ 16 3.2.1 Saw chain repair .............................................................................................. 16 3.2.2 Saw chain speed .............................................................................................. 16 3.2.3 Saw chain tension ........................................................................................... 16 3.2.4 Excessive sprocket wear ................................................................................. 16 3.2.5 Severe side loading of chain ........................................................................... 16 3.2.6 Education and training .................................................................................... 16 4 Order Issued after the Investigation .................................................................. 17 4.1 Order to the employer ................................................................................................. 17 5 Health and Safety Action Taken ......................................................................... 17 5.1 WorkSafeBC ............................................................................................................... 17 WorkSafeBC Investigations WorkSafeBC (Workers’ Compensation Board of B.C.) Page 2 of 18 NI number: 2004110596 www.worksafebc.com 1 Factual Information 1.1 Workplace The incident occurred in November 2004 at a logging site on the west coast of mainland British Columbia. The contractor that held the stump-to-dump arrangement with the licensee had subcontracted work to two other companies. One of those companies owned the equipment involved in the incident, a forest machine with attached dangle head processor (see Figure 1). This equipment can be used for mechanical harvesting and/or processing of trees. In this incident it was being used for processing logs (delimbing and cutting to length). The windshield consisted of ½-inch thick polycarbonate. It was a replacement windshield as the previous one had been damaged. Figure 1: Forest machine with attached dangle head processor. 1.2 Sequence of events On the day of the incident, workers and equipment were working on a slope with a roadway through the cut block. The cut block had been hand-felled. A grapple yarder had placed trees in piles. A log loader operator was breaking down these piles and placing the trees on the roadway. The trees on the roadway were being processed (delimbed and bucked to length) and then laid into piles in preparation for loading onto a truck. A log loader was operating on the road below. WorkSafeBC Investigations WorkSafeBC (Workers’ Compensation Board of B.C.) Page 3 of 18 NI number: 2004110596 www.worksafebc.com At some point during the day, the dangle head’s saw chain was thrown off the saw bar. The harvester operator put the chain back on. At approximately 15:00 the harvester operator activated the saw of the dangle head in order to square the butt of a 12-inch fir log. The chainsaw bar was directly in line with the front window of the operator’s cab. Near the end of the cut the chain broke and the operator heard a crack. A drive link with side plates broke free from the chain and was propelled through the ½-inch thick polycarbonate window (see Figure 2). This “chain shot” struck the operator, inflicting serious internal injuries. He was evacuated by helicopter to hospital. Figure 2: Artist’s drawing of the path of the chain shot. The photograph shows a drive link with side tie strap similar to the chain shot that went through the window and struck the operator. The incident was witnessed by the nearby log loader operator and by the faller, who heard the crack and saw sparks coming from the bottom of the saw shroud of the dangle head. There was a mark in the bottom of the shroud indicating that the shroud was struck by the free end of the saw chain. Looking from the harvester operator’s perspective at the butt of the log involved in the incident shows that the saw cut “drifted” to the right side (see Figure 3). The “whiskers” or wood slivers at the lowest part of the cut indicate that the cut was not fully completed. The slivers indicate that the saw chain was thrown before the cut was fully
Details
-
File Typepdf
-
Upload Time-
-
Content LanguagesEnglish
-
Upload UserAnonymous/Not logged-in
-
File Pages18 Page
-
File Size-