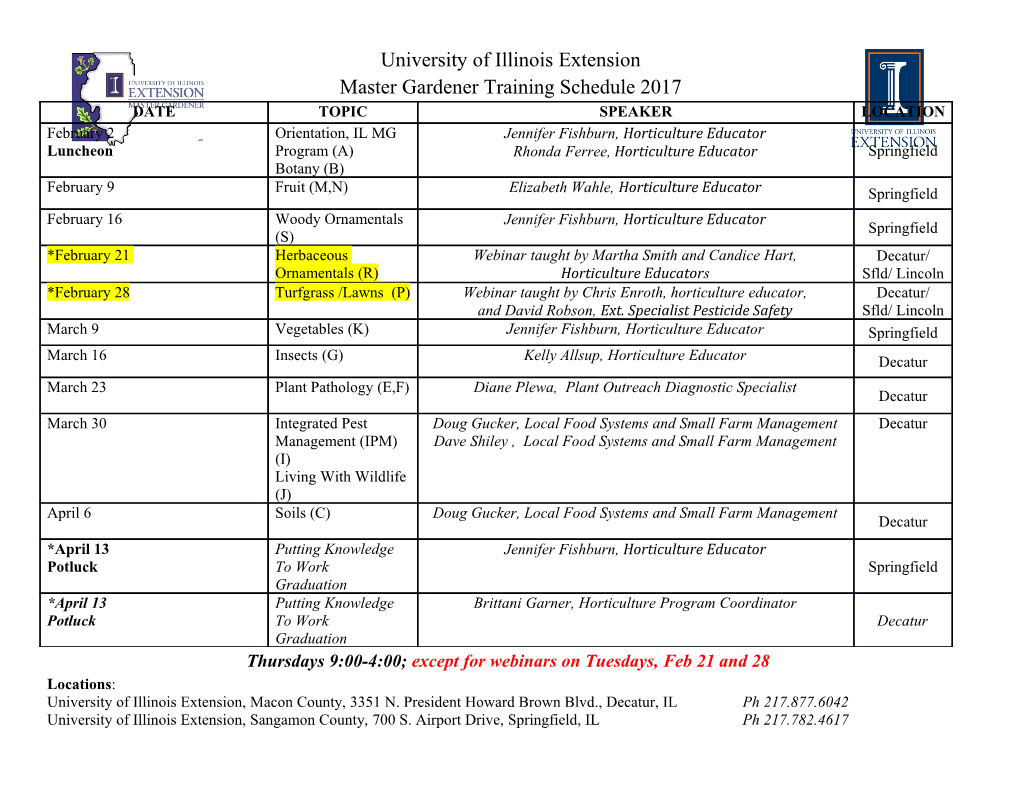
W ASM Handbook, Volume 6A, Welding Fundamentals and Processes Copyright # 2011 ASM International T. Lienert, T. Siewert, S. Babu, and V. Acoff, editors All rights reserved www.asminternational.org Mechanisms of Bonding for Solid-State Welding Processes Jerry E. Gould, Edison Welding Institute SOLID-STATE WELDING PROCESSES the diffusion bonding literature. Resulting mod- Resistance processes encompass all the methods in which metallic els show the importance of the size and distri- a. Flash butt welding bonding occurs without the presence of resolidi- bution of the residual oxide particles, as well b. Resistance butt welding fied liquid metal. These processes range from cold as the role of the thermal cycle. c. Projection welding methods (cold-pressure welding) to hot upset pro- Finally, the third underlying mechanism of d. Mash seam welding cesses (forge processes) to diffusion processes forge welding processes is the decomposition of Friction processes (diffusion bonding). Typically, these processes the interfacial structure. Following the forging a. Inertia welding take advantage of applied strain and/or heat to required to displace contaminants, the bondline b. Continuous-drive friction welding facilitate joining. Joining is largely the result of can be characterized as a highly dislocated, c. Linear friction welding intimate intermetallic contact in the absence of high-energy structure. Improvements in weld d. Friction stir welding local protective films. performance can be made by decomposing this Arc processes This article focuses on the underlying mechan- structure and reducing the residual bondline a. Percussive welding isms of bonding for these processes, with particu- strain energy. Decomposition can occur either b. Magnetically impelled arc butt welding lar emphasis on mechanisms for the forge-type by recovery or recrystallization, depending on processes, while mechanisms for both the cold the thermal cycle employed. There is evidence These processes can be thought of as having and the diffusion processes are considered in to suggest that decomposition by recrystalliza- two generally separable stages. These include a other articles. Specific mechanisms for different tion gives better bond performance. Decomposi- heating stage and an upsetting stage. As such, stages of these processes are identified and quan- tion by recrystallization can be promoted by these welding methods can be generally classi- tified using best-available theory. Further, these appropriate thermal cycles as well as appropriate fied as heat and forge processes. Distinctions mechanisms are used to understand the roles of distributions of strain following upsetting. between these processes then are largely in temperature and strain in facilitating bonding how heat and forging are applied. Inevitably, with these classes of joining technologies. however, heat is first applied. Mechanistically, There are three categories of bonding Solid-State Welding Processes this heat is used for two purposes. First, heating mechanisms for the forge welding processes to the workpieces reduces the yield strengths of be considered: Solid-state welding processes are the oldest of the base materials and permits forging to occur welding processes, with the official American with high degrees of strain at reduced upsetting Contaminant displacement/interatomic Welding Society definition of forge welding forces. Second, if heating is properly applied, bonding requiring an anvil and a hammer (Ref 1). Solid- upsetting creates high degrees of strain over a Dissociation of retained oxides state welding processes have proliferated, particu- very localized area (at the bonding surface). Decomposition of the interfacial structure larly over the last several decades, as new power Once the appropriate heating has been accom- systems have developed. General classifications plished, forging (or upsetting) commences. Modeling of contaminant displacement/inter- of these processes include cold-pressure welding, Upsetting also has two major functions. These atomic bonding is largely taken from the cold- externally heated hot-pressure processes, resis- include collapsing asperities to create intimate pressure literature and adapted to the forge tance processes, friction processes, arc-heated contact, and displacing/dispersing protective welding processes. This modeling suggests that processes, and diffusion processes. In this article, oxides and films to facilitate metal-to-metal with increasing surface strain, bond strengths mechanisms of bonding are described for those bonding. Residual heat content/heating is also can asymptotically approach that of the base processes using both mechanically applied strain- considered advantageous, to further consoli- metal. The cold-pressure models can be adapted ing and heating. Detailed examinations of bonding date/homogenize the joint. to forge welding processes by considering the mechanisms of the other processes are available in role that the developing temperature field has the literature. These include the cold-pressure on the distribution of strain. Generally, how- welding processes (Ref 2–8) and the diffusion Mechanisms of Solid-State Bonding ever, after the surface strain is applied (upset), bonding processes (Ref 9–12). Specific variants there are still residual oxide particles trapped of the other bonding processes are as follows: To attempt to define the specific mechanisms in the bondline, and thermal dissolution of these of bonding for solid-state welding processes, it particles can further improve joint performance. Externally heated hot-pressure processes is first necessary to have an understanding Thermal dissolution modeling has been a. Forge welding about the microstructural and surface condi- adapted from the carbide dissolution (in steels) b. Gas pressure welding tions of the workpieces planned for joining. literature, with stability data collected from c. Induction hot-pressure welding On a microscopic scale, the surfaces for 172 / Fundamentals of Solid-State Welding bonding have been well categorized as irregular relatively unstable and is unlikely to yield an A more general plot showing the relationship and covered with various oxide and contami- adequate joint. As a result, the last stage of between oxide/metal hardness ratio and nant films (Ref 2–12). In addition, there may the process is to relieve these local bondline required deformation for bonding is presented be microstructural/compositional irregularities, stresses, typically with some sort of thermal in Fig. 3. One method of improving the charac- which further complicate the joining process. assist. Depending on the treatment, this local teristics of surface film fracture is to locally A typical representation of the prebond surface concentration of strain energy can result in a cold work the base metal. It has been demon- condition is presented in Fig. 1. This surface is final bond structure ranging from local recovery strated that cold working the surface using generally characterized as three layers: the base to recrystallization (Ref 15). scratch brushing both minimizes the extent of material, a layer of mechanically and/or chemi- As mentioned, these mechanisms collectively contaminant films and creates a local layer of cally affected metal, and surface oxides/con- permit solid-state bonding between metallic heavily cold-worked material, which, on strain- taminant films. materials, although not all mechanisms are used ing, can fracture and carry more ductile oxide There are a number of mechanisms that can by all solid-state welding processes. Generally, films (Ref 6). proceed to form a bond between such surfaces. these mechanisms, particularly as they operate For most conventional forge welding pro- The most important of these is that asperities on within the group of forge welding processes, cesses, extension of the contacting surfaces is the surfaces must be collapsed to form intimate can be classified in three general areas. These done with a combination of heat and force. contact between materials. In forge welding include surface deformation mechanisms, con- For this stage of the process, local strain is the processes, creation of this intimate contact is taminant dissolution mechanisms, and interfa- most important factor. However, how that strain done mechanically; that is, local yield stresses cial structure homogenization mechanisms. is distributed is a strong function of how the are exceeded on the contacting surfaces, and These are described in detail, including their thermal field is applied. Figure 4 shows some surface deformation is used to create the con- direct relationship to the forge welding pro- results from numerical simulations of the tact. For diffusion bonding processes (not cov- cesses, in subsequent sections. flash-butt welding process (Ref 16). This plot ered extensively in this article), such surface Contaminant Displacement/Interatomic shows how contact surface strain is affected collapse is done under relatively low forces Bonding. As briefly described previously, sur- both by the amount of upset used and the level and relies on creep and surface diffusional face deformation mechanisms have two func- of flashing acceleration employed. Flashing mechanisms to consolidate the surfaces. tions: to collapse surface asperities and to acceleration directly controls the heat distribu- Once the surfaces have come under intimate displace surface contaminants. It is of interest tion in the workpiece, with higher flashing contact, bonding still cannot initiate
Details
-
File Typepdf
-
Upload Time-
-
Content LanguagesEnglish
-
Upload UserAnonymous/Not logged-in
-
File Pages25 Page
-
File Size-