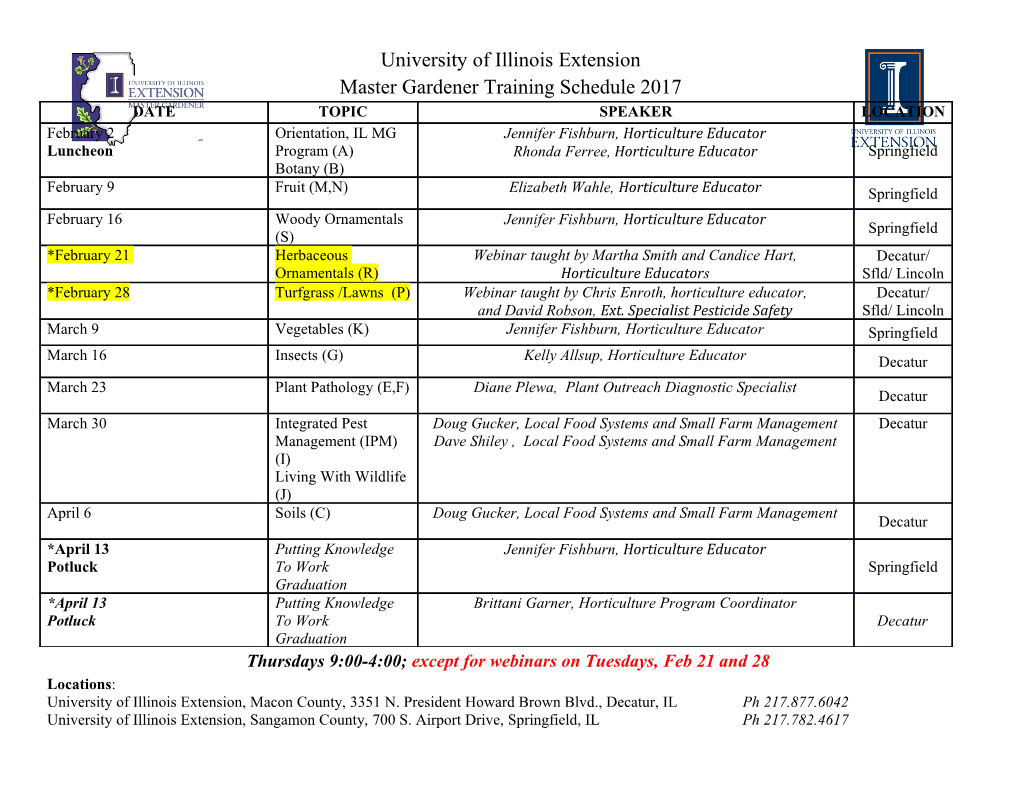
Effects of Cold Temperature and Main March 27, 2017 Compressor Intercooling on Recuperator and Recompression Cycle Performance Nathan T. Weiland, Charles W. White, Andrew C. O’Connell nd 2 European Supercritical CO2 Conference, 30-31 August, 2018 Solutions for Today | Options for Tomorrow U.S. DOE Fossil Energy sCO2 Technology Program NETL: The DOE Fossil Energy Laboratory • NETL is managing/coordinating two Fossil Energy (FE) sCO2 technology programs: • FE Base sCO2 Technology Program (indirectly & directly heated cycles for FE applications) • DOE sCO2 Crosscut Initiative (STEP – indirectly heated sCO2 Brayton cycle) • FE Base sCO2 Technology Program • Development of individual cycle components • Systems analyses • Specific interest in adv. combustion indirect cycle & IGCC direct cycle • Near term application to natural gas • DOE sCO2 Crosscut Initiative (STEP) • Collaboration between DOE Offices (Fossil, Nuclear, Renewable) • Mission: Address technical issues, reduce risks, and mature technology • Objective/goal: Design, build, and test 10 MWe pilot facility (STEP) • FE/NETL designated as lead budget focal for STEP 2 NETL Research & Innovation Center (RIC) Role in Supercritical CO2 Technology Program Goal – Develop technology toward achieving the program goal of increased efficiency using sCO2-based power cycles. Approach – Perform R&D on turbine blade cooling, oxy-combustion, and materials, along with systems studies. Aerothermal/Heat Transfer Oxy-combustion Materials Systems Analyses PI: Jim Black PI: Peter Strakey PI: Omer Dogan PIs: Weiland, Shelton, Liese Cool turbine blades to allow Improve efficiency using higher Evaluate material corrosion, Steady-state and dynamic higher turbine inlet temperature direct-fired cycle erosion, mechanical property modeling, techno-economic temperatures. with oxy-combustion. degradation in sCO2. Identify evaluations of various materials compatible in sCO2. configurations of sCO2 power cycle plants (direct- and indirect-fired cycles) Proposed Oxy-Fuel Combustor Source: NETL Source: NETL Source: NETL Source: NETL 3 Background 1 Utility-Scale Indirect sCO2 Plant Study CO2 Compression, Drying, CO2 • Objective: Establish cost and 3 Vent and Purification Unit Product CO CO2 29 2 Purification Drying 30 Ambient Air 27 performance baselines for LP CO2 1 MAC 2 Cryogenic ASU Compressor w/ Compression/ Pumping commercial-scale indirect sCO2 Intercooling Interstage O Knockout power plants with carbon capture Interstage Cooling 2 28 Knockout Water 4 and storage (CCS) 26 5 6 • Early work shows that the narrow 22 N Heater 2 21 18 temperature addition window of a 17 19 ID 20 8 24 FLUE GAS Fan FD Fan COOLER 10 Knockout recompression sCO2 Brayton Cycle Bag Water 15 House restricts boiler selection 41 16 PA Fan Fly Ash Oxy- 7 23 9 42 • Modified oxy-fired, atmospheric pressure Circulating 46 Fluidized Bed MAIN CO Coal 11 Combustor 2 CFB boilers with CCS chosen for analysis COMPRESSOR Limestone 12 31 45 HIGH LOW 40 39 TEMPERATURE 44 TEMPERATURE 34 CO • Recompression cycle with reheat and/or 2 RECUPERATOR 33 RECUPERATOR 36 TURBINE 35 main compressor intercooling 32 CO2 14 COOLER (4 combinations x 2 temperatures) Note: Block Flow Diagram is not intended to 38 represent a complete process. Only major Bottom process streams and equipment are shown. Ash Bypass CO2 Compressor Source: NETL 37 1 National Energy Technology Laboratory (NETL), "Techno-economic Evaluation of Utility-Scale Power Plants Based on the Indirect sCO2 Brayton Cycle," DOE/NETL- 2017/1836, Pittsburgh, PA, September 2017.. 4 Utility-Scale Indirect sCO2 Plant Study Summary of Overall Plant HHV Efficiencies1 • Relative to the steam Rankine cycles 42 40,8 41,2 using oxy-fired CFBs and CCS: 39,9 40 39,5 • At 620 °C, sCO2 cycles are 1.1 – 3.2 Source: NETL percentage points higher in efficiency 38 36,9 36,8 • At 760 °C, sCO2 cycles are 2.6 – 4.3 36 36,2 35,3 percentage points higher 34 34,7 33,6 • 32 The addition of reheat improves sCO2 Plant (HHVEfficiency %) 760 °C 620 °C cycle efficiency by 1.3 – 1.5 percentage 30 points Rankine Base IC Reheat Reheat+IC • The addition of main compressor Power Summary (MW) B22F Base IC Reheat Reheat+IC intercooling (IC) improves efficiency Coal Thermal Input 1,635 1,586 1,557 1,519 1,494 sCO2 Turbine Power 721 1,006 933 980 913 by 0.4 – 0.6 percentage points CO2 Main Compressor 160 154 148 142 • Main compressor intercooling reduces CO2 Bypass Compressor 124 60 117 58 Net sCO2 Cycle Power 721 711 708 704 702 compressor power requirements for both the Air Separation Unit 85 83 81 79 78 main and bypass compressors Carbon Purification Unit 60 56 55 54 53 Total Auxiliaries, MWe 171 161 158 154 152 Net Power, MWe 550 550 550 550 550 5 sCO2 Compression Power • sCO2 compression power requirements 120 100-120 are very sensitive to the proximity of the RC - Base 80-100 operating condition to the CO2 critical 100 60-80 point (Tcr = 31 °C, Pcr = 7.37 Mpa) 40-60 80 RC – with MC 20-40 • Main compressor intercooling reduces Intercooling 0-20 the bypass compressor inlet temperature 60 • Condensing sCO cycles can significantly 2 40 Pressure Ratio = 4 reduce compression power requirements ηc = 85% • Reducing compression power improves 20 MC cycle efficiency and specific power Condensing Specific Compression Power (kJ/kg) Power Compression Specific 0 Cycles 10090 80 MC RC 70 60 50 LTR HTR Heater 40 10 Cooler 30 8 9 20 6 7 105 Turb Source: NETL Source: NETL 6 Main Compressor Intercooling Effects Background 10.5 MW 11.4 MW No Intercooling 9.2 MW 8.0 MW With Intercooling 100 MW • The incorporation of main compressor 100 MW intercooling improves the specific power MC RC 1 238 C 474 C of a recompression cycle 85 C 30% 189 C 460 C 53 C 28% LTR HTR PHX • Reduces sCO2 mass flow 35 C Cooler 700 C • Reduces required cycle size and cost 35 C 700 C T 95 C 248 C 517 C 63.6 MW 108 MW • The effects of intercooling on cycle 47.6 MW 63 C 199 C 517 C 74.4 MW 58.5 MW 120 MW efficiency are complex, and require 33.7 MW 70.0 MW consideration of temperature distributions 700 along the recuperator train 600 No Intercooling 500 With Intercooling C) • A single stage of intercooling for the main ° CO2 Dome compressor offered both higher overall plant 400 efficiency (0.4 – 0.6 percentage points) and lowers 300 1 the cost of electricity by 1.8 to 2.7% 200 Temperature ( Temperature • Efficiency benefit increases (0.6 – 1.6 percentage 100 points) when the pressure ratio between 0 intercooled main compressor stages is optimized2 1 1,5 2 2,5 3 Specific Entropy (kJ/kg K) Source: NETL 1 National Energy Technology Laboratory (NETL), "Techno-economic Evaluation of Utility-Scale Power Plants Based on the Indirect sCO2 Brayton Cycle," DOE/NETL- 2017/1836, Pittsburgh, PA, September 2017. 2 Y. Ma, M. Liu, J. Yan and J. Liu, "Thermodynamic study of main compression intercooling effects on supercritical CO2 recompression Brayton cycle," 7 Energy, vol. 140, pp. 746-756, 2017. sCO2 Cooling Integration Study • Objective: Determine the extent to which increasing cooling capacity and cooling system operation conditions can improve the efficiency and cost of electricity (COE) from a utility-scale indirect sCO2 power plant. • Approach • Determine steady state plant performance as a function of cooler exit temperature and pressure, as well as the number of main compressor intercooling stages • Novel options for resolution of resulting heat exchanger temperature pinch point problems • Quantify impact on plant efficiency, specific power and other cycle parameters for condensing and non-condensing CO2 cycle operation • Develop cost and performance models of wet and dry cooling technologies • Optimize plant COE as a function of cooling technology and capacity • Expected Impacts • Cooling system optimization results are applicable to all sCO2 plant types • Published cooler cost and performance modeling tools will enable similar COE optimization by others • Enables COE optimization at any sCO2 plant site given its ambient conditions 8 sCO2 Recompression Brayton Cycle (sRBC) General Cycle Design • Cycle design features from previous work1: CFB • Circulating Fluidized Bed (CFB) coal combustor FGC HPT • Reheat turbine MC • Third recuperator stage (VTR) and an economizer that LPT supplements the HTR • Intercooled main CO2 compressor RC VTR • Flue gas cooler (FGC) in parallel with the LTR LTR HTR • Transfers additional thermal energy from the low quality Cooler combustion flue gas to the sCO2 cycle • Applicable to waste heat recovery sCO2 cycles • Present work focuses on low temperature components only • Other cycle components are only analyzed to establish a baseline plant efficiency for evaluation of parameter sensitivities • Results generally apply to other hot-side cycle configurations and heat sources Source: NETL 1 National Energy Technology Laboratory (NETL), "Techno-economic Evaluation of Utility-Scale Power Plants Based on the Indirect sCO2 Brayton Cycle," DOE/NETL- 2017/1836, Pittsburgh, PA, September 2017.. 9 sRBC Power Cycle Analysis Methodology CFB • When used, the main CO2 compressor is assumed to have a single stage of intercooling: FGC HPT • Intercooler outlet temperature is set equal to the MC LPT main CO2 cooler outlet temperature • Intercooler pressure drop is 0.014 MPa (2 psid) • Isentropic efficiencies and pressure ratios for each RC VTR compression stage are approximately equal LTR HTR • Recuperator exit temperatures are set using Cooler design specifications in the Aspen Plus model • Target a minimum temperature approach (Tapp) of Source: NETL 5.6 °C (10 °F) at one
Details
-
File Typepdf
-
Upload Time-
-
Content LanguagesEnglish
-
Upload UserAnonymous/Not logged-in
-
File Pages24 Page
-
File Size-