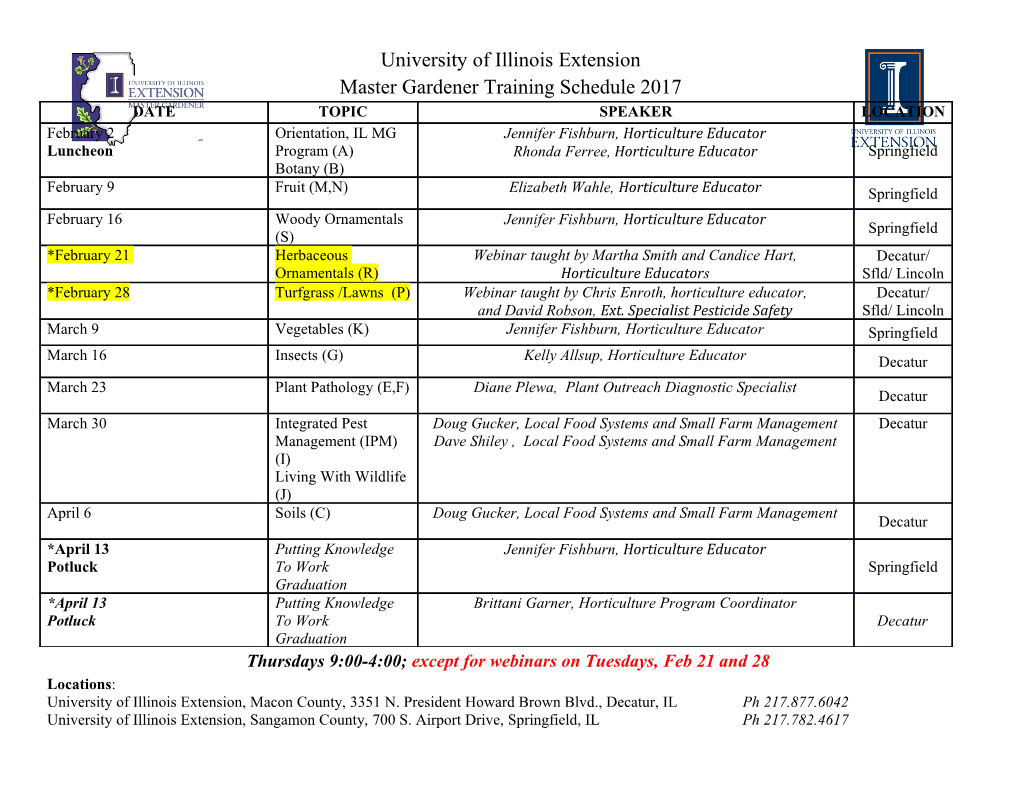
SHUTTLE LIQUID FLY BACK BOOSTER CONFIGURATION OPTIONS* T. J. Healy, Jr. Boeing Reusable Space Systems Downey, California ABSTRACT This paper surveys the basic configuration options available to a Liquid Fly Back Booster (LFBB), integrated with the Space Shuttle system. The background of the development of the LFBB concept is given. The influence of the main booster engine (BME)installations and the fly back engine (FBE) installation on the aerodynamic configurations are also discussed. Limits on the LFBB configuration design space imposed by the existing Shuttle flight and ground elements are also described. The objective of the paper is to put the constrains and design space for an LFBB in perspective. The object of the work is to define LFBB configurations that significantly improve safety, operability, reliability and performance of the Shuttle system and dramatically lower operations costs. INTRODUCTION The Liquid Fly Back Booster (LFBB) is a proposed upgrade to the Space Shuttle System which replaces the existing water recoverable, refurbished solid rocket boosters with one or two new fully reusable liquid rocket boosters (Figure 1). The goal of the LFBB program is to increase safety, reliability, performance, and operability, I Present _ Reduced . ! while significantly decreasing operations costs. These Solid Rocket Boos_rs _ Operatmg costs LFBB's launch vertically with the Shuttle, but fly back to the launch site, land on a runway and are returned to Future Future Liquid Flyback Booster Liquid Flyback Booster flight, very similar to a large aircraft (Figure 2). (Deal Option) (Catamarg. n Option) BACKGROUND OF THE LFBB CONCEPT Increased _l _ ,_ Safety " "qllJl__._ The concept of a recoverable liquid rocket booster Reliability _ _ has been around for many years, predating the Space Shuttle program. Wernher von Braun caught the public's imagination with his concept for a three stage Figure 1. A possible Shuttle upgrade - Liquid Fly fully reusable launch system I which was popularized in Back Boosters Colliers Magazine in 1952. In this concept, the first two stages were recovered on parachutes, and the third was a manned winged orbital space plane. All the early Space Shuttle concepts in the late 1960's through the summer of 1971 were fully reusable with fly back liquid rocket boosters 2, 3 which were piloted. These fully reusable boosters and the two stage fully reusable Space Shuttle concepts were eliminated from the program primarily due to development cost reasons, and a two stage partially reusable system adopted. 4 The current Shuttle uses two Redesigned Solid Rocket Motors (RSRM), which are recovered by parachute and retrieved by ship. They are completely refurbished for subsequent reuse. The Shuttle also uses an expendable external tank (ET) for second stage propellant for the Orbiter. The Orbiter itself is the only truly reusable element in the system. However, for safety, performance and operational cost reasons, there has been a continued interest in replacing the Shuttle's solid rocket boosters with liquid rocket boosters, usually reusable concepts. The Shuttle Growth Distribution Statement: Approved for public release; distribution is unlimited. * This unclassified work was performed under NASA Contract NAS8-97272 as part of NASA's Shuttle Upgrades Feasibility Investigation of Liquid Fly Back Boosters (LFBB). Presented at July, 1998 JANNAF JPM. Dual Confiauration I BALLISTIC 1"] __ _/t = 5.55 mi-n Booster Separation: To Or _ / h = 125,000 ft t=2.17min - / _ / M=48o h = 149,508 ft t = 3.84 min _ / ot - 40 deg h = 254,999 ft _ / - M = i: V= 5,442 fps / range = 95.4 nm _'_N t = 7 62 min M=5.0 M=5.13 N,,%N h = 37,353 ft range=30.2nm _/. I ENTRY- ]_.,,_ range = 218.2 nm It'YPERSONIC f=80dog Aerodynamic Turn: "_ Omax: t = 7.69 min t = 7.81 min h = 32,988 ft t = 51.6 sec h = 31,000 ft range = 217.0 nm range = 216.1 nm M = 0.984 rha:g2eO'__31.%ftnm M°° 5osf --8.0deg II M = 1.0 IIs s°' 'ccRU EI N,c,I t = 0 seej h = 15,000 ft nominal t = 55.47 rain M = 0.48 (Throttle adjusted to give 10 min separation at landing) v = 190 kts Figure 2. The LFBB sees five different flight regimes Study, sponsored by Marshall Space Flight Center (MSFC) and conducted by Rockwell in the mid-1970's was typical. _ This study examined a wide range of water recoverable and fly back land recoverable, reusable boosters, finally electing a parachute/water recoverable liquid booster, in order to limit the estimated development costs, at the expense of operations. After the Challenger disaster, interest was rekindled in liquid rocket boosters to replace the solids. A major effort was conducted by MSFC with contracts to Martin Marietta (NAS8-37136) and General Dynamics (NAS8- 37137), supported by the Kennedy Space Center with a contract to Lockheed (NASI0-11475). The effort was concentrated in the 1987-1989 time period, with some tasks on-going to 1991. The focus was on liquid rocket boosters that could easily replace the solid boosters; and while recovery was studied, the selected baselines were expendable. 6.7 Meanwhile, interest in fully reusable liquid boosters continued to build as part of a thrust for continued Shuttle evolution and improvement)' 9 NASA conducted an extensive in-house Access-To-Space Review in 1993, out of which have grown several important thrusts, including the Shuttle Upgrade program and the Reusable Launch Vehicle program. The Access-To-Space team, studying Shuttle evolution, recommended a liquid fly back booster as a key Shuttle improvement. _° This recommendation resulted in NASA embarking on a major in-house study, the Liquid Fly Back Booster Pre-Phase A Assessment, completed in September 1994. The Liquid Fly Back Booster Pre-Phase A Assessment '_' n concluded that a liquid fly back booster (LFBB) is the only cost effective replacement for the solid rocket boosters from a life cycle cost standpoint. The primary benefits from the proposed LFBB are enhanced safety, operability, reliability and performance, and a significant reduction of operational costs. This renewed interest in LFBB's and a number of concepts were investigated in parallel with or subsequent to the NASA efforts (Figure 3). NASA placed the LFBB into the Shuttle Upgrades program as a Phase IV improvement, but follow-up effort was postponed. Perceived high development cost was an issue. In 1996, Rockwell (now Boeing) conceived a catamaran configuration that promised affordable development costs. This sparked renewed interest in getting detailed LFBB feasibility data to support Shuttle service life decisions and resulted in NASA establishing a study effort in February 1997 to conduct feasibility studies of the LFBB. This LFBB effort is under the direction of Johnson Space Center (JSC) who controls the system integration effort. Supporting JSC FOLDING is MSFC who leads the " ' Rockwell Cetamoran LFBB vehicle development and has Fonverd Scissoring Wlng Preferred Configuration awarded study contracts NASA TM 104801 1994 LFBBS to Boeing and Lockheed-Martin. KSC LFB84 _ MSFC 1996 I BoeingFeb. Catamaran1997 J support the effort • _ MSFC 1996 I focusing on operations and launch facilities. Figure 3, Many LFBB concepts have been studied As of the spring of 1998, the results of this effort are: (1) LFBB concept is viable--three configuration options identified; (2) no technology breakthroughs are required; and (3) three affordable main engine candidates are available. 13 LFBB GOALS AND REQUIREMENTS The LFBB responds to the overall objectives of Goals & Requirements Drives Confi_luration Element BME Reliability the Shuttle Upgrade program which are to fly safely, Safety "'_ BMEout _Number &SizeofBME's ensure mission supportability, meet the manifest, and reduce cost. Applied to the LFBB, these become the goal areas, shown in Figure 4. These requirements Perform__ affect all aspects of the LFBB design, but several are .,o. ....... , key in driving the LFBB aerodynamic and propulsion _Jdfotaab,e D_eloomen, YJ_ P!anf°rm & L°ca!! On system configurations. Many of these Cost_,_Mm. ET & Orbiter _ - interrelationships drive to conflicting optimums, thus "__ Impacts _ Fully Reusable System opening the way for tradeoffs and design compromise. "q_ow Ops Costs _ , Operability & "_ Reliable. Ma_tslnable Mission Effectiveness "1 Subsys. Design & Installation CONFIGURATION TRADES Figure 4. LFBB goals & requirements shape The configuration trades are performed within a configuration options framework of geometry, system and configuration constraints that limit the trade space. Major constraints are that the LFBB: • Is fully reusable, land recoverable at the launch site--previous studies show this is required to meet operations cost goals. • Uses catamaran (twin fuselage) or dual boosters, using ET/SRB attach locations--single and triple or greater boosters create major ET redesign and other integration issues (Figure 5). * Uses liquid oxygen/RP-1 (or kerosene) propellants--use of liquid hydrogen makes the LFBB too large to integrate with the Orbiter or KSC. • Meets KSC facilities constraints - Vehicle Assembly Building (VAB) door width (Figure 6) dla Max. For zero wing •18 in. MIn loadincmue Clearance _ax to Clu Max Span VAB Doors for Tower Clearance on Pad Catamaran Wlnl 112.3 ft Figure 5. Facilities constraints & air loads limit body diameter & location 144.0 ft Figure 6. Min. clearance of VAB doors - Use a Mobile Launch Pad (MLP that can be modified from the existing MLP ET GOIvent Arm Structure (FSS) Use existing Tail Service Masts (TSM) Rotating Servlca_ ET Intertank s_re (ass) 0AA) - Clear the launch pad service tower and use a Tall Selvi(_ ET Gl-ll Vent Arm existing flame trench (Figure 7) can be modlfkKl - Maintain Orbiter and ET position in relation Mobllo IJun©h SOft. mlx, half to MLP as it presently exists.
Details
-
File Typepdf
-
Upload Time-
-
Content LanguagesEnglish
-
Upload UserAnonymous/Not logged-in
-
File Pages14 Page
-
File Size-