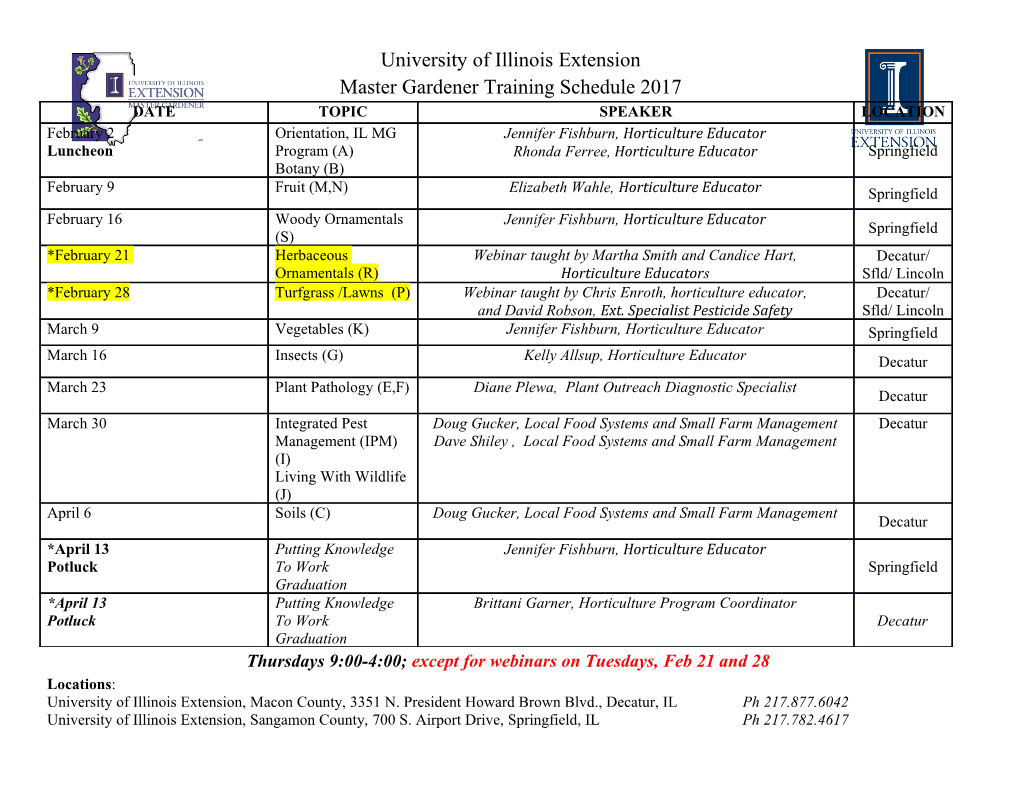
Design – Design Methodology Table of contents 1. Design methodology ............................................................................................................. 2 1.1 The design challenge: Low weight, low cost, low carbon footprint and high performance ......... 2 1.2 Introduction to the design process described in this manual ..................................................... 4 1.2.1 Overview of design process ........................................................................................... 4 1.2.2 Design Phases and Objectives ........................................................................................ 5 1.2.3 Design Tools ................................................................................................................ 9 1.2.4 ....................................................................................................................................... Version 2011 © European Aluminium Association ([email protected]) 1 1. Design methodology 1.1 The design challenge: Low weight, low cost, low carbon footprint and high performance The principal reason for introducing aluminium into automobiles, i.e. the application of aluminium alloys for vehicle components, sub-assemblies and full vehicle structures is to achieve a significant weight reduction compared to traditional car designs based mainly on steel and cast iron. At the same time, the aim must be to develop designs that are easy to manufacture and cost effective whilst meeting the required performance criteria. Today, the design and manufacture of cars must not only satisfy engineering criteria, but also fulfil environmental, social and political aims, such as minimising waste and deposition, satisfying recycling targets, respecting health and safety regulations as well as reducing emissions and saving resources. High emphasis is now given to the environmental performance of an automobile over its total life cycle. The aim is to minimise the overall environmental impact of the vehicle production stage (including materials production), service life and end-of-life phase (including recovery and recycling of the materials). A particular challenge is the treatment of end-of-life vehicles. In the future, therefore, it is envisaged that increased emphasis will be put on the disassembly of selected components for optimum recovery of the material value. This will enhance the traditional recycling route of end-of-life vehicles (shredder and subsequent metal sorting). Design for disassembly is thus an important development theme, requiring careful consideration of material combinations and manufacturing methods during early design phases in order to meet both ecological and cost targets. The finally realised weight of a system or a sub-system, however, may not be the lowest weight achievable since cost is generally an overriding issue. Nevertheless, with proper application, lightweighting with aluminium almost always delivers an improved performance of the vehicle in addition to the lower fuel consumption (which translates into lower CO2 emissions). Lightweighting with aluminium enables better acceleration, shorter braking distance, easier handling, increased car body stiffness and a lower centre of gravity at a modest cost increase, factors which also contribute in particular to an enhanced safety performance. A good example of for such a performance enhancement is body structure of the Audi TT roadster. Different aluminium product forms, but also steel are used at specific locations in the body structure with the following results: Weight reduction of 100 kilograms compared to an equivalent all steel construction Significantly reduced body-in-white mass for coupé and roadster versions (weight reduction of 100 kg leading to a total weight of 206kg) Balanced front / rear axle weight distribution Improved torsional stiffness (coupé +50%, roadster +100%). An interesting part is the lower A post, a high pressure die cast multi-functional aluminium component that links the side member, the sill, the A post and the wind-shield cross-member. The specific benefits include a very precise part geometry and the maximum use of the available space to ensure high stiffness and structural integrity in crash. For the car owner, the extensive use of aluminium translates to: Easier handling during cornering Shorter braking distance 7.5 to 12.5 grams lower CO2 emissions per kilometre Lower fuel consumption More uniform tyre wear. Version 2011 © European Aluminium Association ([email protected]) 2 Body structure of the AUDI TT roadster Source: http://www.automobilesreview.com/tag/tt/ The body structure consists of 140 kg Aluminium (68%): 63 kg of sheet, 45 kg of castings, 32 kg of extruded sections, as well as of 66 kg steel (32%). Version 2011 © European Aluminium Association ([email protected]) 3 1.2 Introduction to the design process described in this manual Automobile manufacturers have at their disposal a wealth of expertise in designing and manufacturing vehicles with a wide range of materials. The body structure and the skin panels have traditionally been manufactured from various steel grades. However, with the current focus on the reduction of fuel consumption and overall greenhouse gas emissions, other materials, and in particular aluminium, are used to achieve a significant reduction in the weight of the car body. While most of the general design principles that have been developed for steel are also valid for aluminium structures, best results are always obtained if there is enough design freedom to apply an aluminium-oriented design, rather than just to substitute aluminium for steel in existing part designs. This section will describe a design process that is later illustrated by case studies. Some vehicle manufacturers and first tier suppliers are already expert with aluminium as the example of the Audi TT structure shows. They have developed sophisticated procedures based on their accrued knowledge, in order to manage the design process with aluminium. We hope, however, that the following will be a useful introduction for both young and experienced engineers who wish to explore more fully the differences between designing with steel and aluminium. 1.2.1 Overview of design process A design process can be used for further developing existing objects or for producing completely new ones. The detailed content of each design project is likely to be different since it will depend on its specific objectives, the starting point and the available resources. Certain logical steps are often taken in order to be able to make qualified decisions selecting the best of the options available at specific points along the time-line called gates. GATE Design Brief GATE Tooling tryout GATE Tooling (Cahier de Technology manufacturing Design Freeze Simulation Charge) Selection plant Acceptance Design Pre-Prototype Design Development Industrialisation New technology scanning / Prototype Studies Detailed Design Product and Process Industrialisation Pilot SOP Concept studies Design / Validation and Trials runs ramp GATE Tooling GATE GATE Design & tryout at Implementation Prototype SOP Process tooling Readiness Selection Sign-Off manufacturer Time-line for complete Concept to Start of Production (SOP) projects Source: Roger Hall The single common element in all design projects is the design brief that describes the overall objectives of the project, such as, for example, “an electric niche vehicle with a very short wheelbase, whose target customer is young families living in the city”, etc. The design brief is then translated into specific deliverables for each department working on the project. Typical deliverables might include weight reduction, improved safety for occupants and pedestrians, cost reduction, etc. Version 2011 © European Aluminium Association ([email protected]) 4 The scope of a design project is further defined by detailed product requirements and the imposed constraints which form the specific boundary conditions of the project. Some common project boundary conditions Source: Roger Hall 1.2.2 Design Phases and Objectives In the automotive industry, “clean sheet” design projects are relatively rare because of their long duration, high cost and potentially higher risk than the development of proven designs, but also because of the possibilities ti integrate carry-over parts. Some examples of recent “clean sheet designs” are the Mercedes SLS, BMW 1 series, Fiat 500 and the GM electric vehicle. The advantages of a clean sheet design include a full freedom in the location and choice of power unit, power train and suspension. Thus they are most interesting for vehicles using new, alternative power systems. Better packaging can improve safety and access to hydrogen storage units or batteries and other rigid components that may be required by fuel cell and electric motor powered vehicles. Improved packaging of the main functional units directly influences the potential to maximise the ratio of passenger compartment volume to the vehicle length (e.g. important for the attractiveness of city cars for families). When designing with aluminium, a clean sheet approach will also deliver more efficient structures. Larger beam sections, large thin-walled castings and straight or bent extrusions may be used more effectively and also packaged to deliver stiffness and strength targets as efficiently as possible. Version 2011 © European Aluminium Association ([email protected]) 5 GATE Design Brief GATE Tooling tryout GATE Tooling (Cahier de Technology manufacturing
Details
-
File Typepdf
-
Upload Time-
-
Content LanguagesEnglish
-
Upload UserAnonymous/Not logged-in
-
File Pages20 Page
-
File Size-