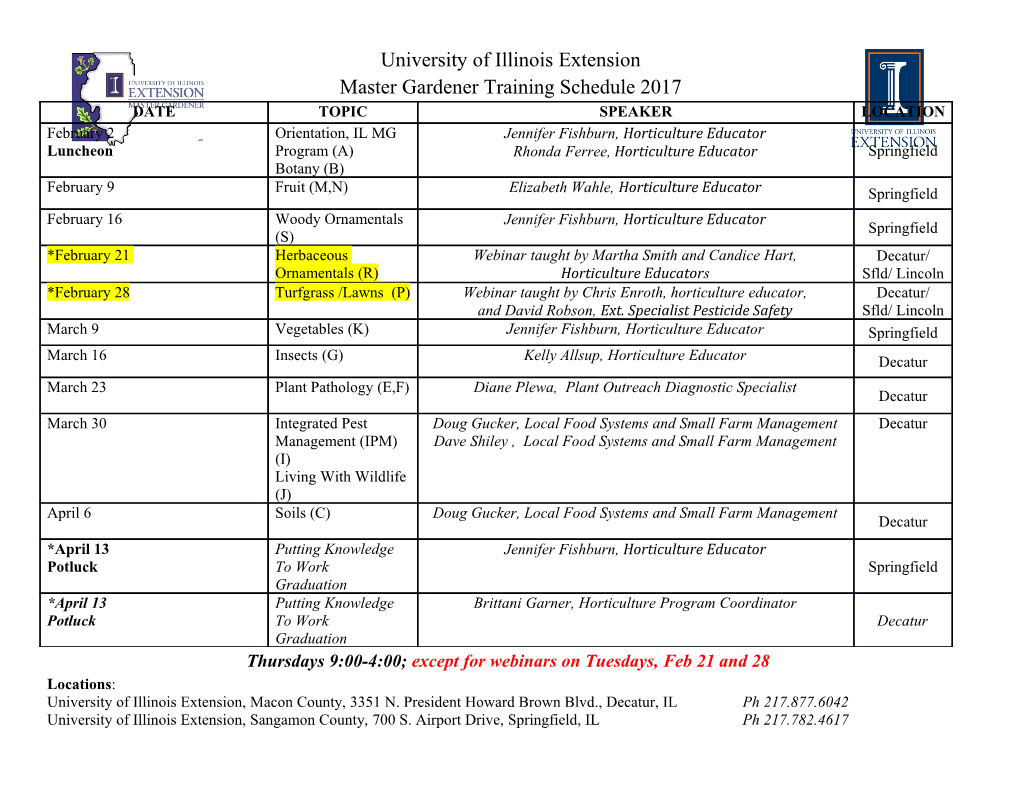
INGENIERÍA MECÁNICA TECNOLOGÍA Y DESARROLLO Fecha de recepción: 02-12-10 Vol. 3 No. 4 (2010) 123 - 134 Fecha de aceptación: 22-01-10 Dynamic Analysis of Pneumatically Actuated Mechanisms Arturo Lara-López, Joaquín Pérez-Meneses, José Colín-Venegas*, Eduardo Aguilera-Gómez and Jesús Cervantes-Sánchez Mechanical Engineering Department, University of Guanajuato at Salamanca Palo Blanco, Salamanca, Gto., México Phone: +52 (464) 647-9940, Fax: +52 (464) 647-9940 ext. 2311 *Corresponding author email: [email protected] Resumen En este artículo se analiza el comportamiento dinámico de sistemas impulsados neumáticamente. Primeramente se analiza un modelo básico que consiste de un eslabón montado sobre un eje impulsado neumáticamente contra una fuerza externa. El modelo matemático que resulta es el fundamento básico para formular modelos de mecanismos más complejos. Luego, el análisis se extiende a un meca- nismo de cuatro barras donde el eslabón de entrada se impulsa por un cilindro neumático y la fuerza externa es aplicada contra el eslabón de salida. Los modelos para ambos sistemas se obtuvieron de la aplicación directa de principios dinámicos y termodinámicos y de relaciones de la cinemática, incorporando características físicas de los mecanismos y el efecto de condiciones del aire, tamaño del tanque y amortiguamiento del pistón. Tales parámetros pueden manipularse con propósitos de diseño. Se construyeron prototipos experimentales de ambos modelos (un eslabón montado sobre un eje y un mecanismo de cuatro barras) para medir su respuesta dinámica. Los datos experimentales se compararon con la solución teórica mostrando buena similitud. Abstract The dynamic behavior of pneumatically driven systems is analyzed in this paper. First a basic model consisting of a single pivoted link pneumatically actuated against an external force is discussed. Resulting mathematical model is the basic foundation to formu- late models for more complex mechanisms. Then, the analysis is extended to a four bar mechanism, where the input link is driven by a pneumatic cylinder and the external force is applied against the output link. Models for both systems were obtained from direct application of dynamic and thermodynamic principles and kinematics relations, incorporating physical characteristics of the mechanisms and the effect of air conditions, tank size and piston cushion. Such parameters can be manipulated for design purposes. Experimental apparatus were constructed to measure the dynamic response of both models (the single pivoted link and the four bar mechanism). Experimental data where compared with the theoretical response showing good agreement. Palabras clave: Key words: Mecanismos impulsados neumáticamente, dinámica de me- Pneumatically actuated mechanisms, dynamics of canismos mechanisms Introduction It is a well recognized fact that increasing productivity in the The models presented in this article include important high technology systems demanded by today’s industry largely machine dynamic properties, such as those related to the relies upon the ability of machines in service to run at higher compressed air in a tank, a pneumatic actuator with an speeds while still maintaining the desired dynamic behavior and exhaust valve that permits to regulate the start and end precision. Many of these machines include pneumatically driven cushion periods and the kinematics and dynamics properties pivoted links or mechanism. Then the knowledge of the transient of the impulse link or mechanism, that could be under the response of high speed linkages may be of great interest for action of external forces including dry and viscous friction industry to meet the compromise between speed of process and and the useful force. It is expected that the contribution of avoidance of damage to products, especially when excessive this article would be centered in a new model that integrates acceleration may damage products being handled. This natu- as completely as possible the performance of the whole rally poses a challenge to machine design engineers for reliable system, this means the pneumatic circuit with the kinematics and precise prediction of consequences resulting from an incre- and dynamics of the mechanism and the analysis of the ment of the operation speed. In addition, one more difficulty is influence of their parameters. In addition the resulting due to the inability of commercial computer-based design tools model is simpler than those related to similar problems to include realistic properties in models of the dynamic behavior previously published with no additional simplifying hypothesis. of pneumatic systems. Practical modeling techniques also need to Moreover, the theoretical response of the whole system be computationally efficient and should be experimentally veri- was experimentally verified. fied, hence the motivation to write this paper. Ingeniería Mecánica 123 INGENIERÍA MECÁNICA TECNOLOGÍA Y DESARROLLO Vol.3 No.4 (2010) 123 - 134 A number of important contributions oriented to understand and where L ≡ OA and p ≡ AC. predict the dynamic performance of this type of pneumatically . .. Then, given the input motion r, r and r a closed-form solution driven devices are in the literature. A summary is presented. for the remaining joint variables and their time derivatives Bobrow and Jabbari (1991) modeled this type of mechanism con- may be obtained, namely: (Shigley & Uicker, 1995) sidering the rigid body equation of motion for pivoted link in addi- tion to the energy equation for the air in the cylinder. Pressure in the 2rL + A inlet of the cylinder was assumed as constant. Authors emphasize φ =±2arctan (2) the nonlinear characteristic of the system. J. Tang and G. Walker 2rL − A (1995) proposed a model to simulate the movement of a pneu- matic actuator based on the equation of motion of a translating mass under friction force which includes dry and viscous components. 2Lp+ B θ =±2arctan (3) That paper presents the control analysis of the system. M. Skreiner 2 2Lp− B and P. Barkan (1971) proposed a model for a four bar linkage driven by a pneumatic actuator. This model was analyzed as a rL(cosφ − r ) control system based on two equations. The first one is a kinematic φ = (4) equation and the second one is the control equation. Kiczkowiak φ Lrsin (1995) proposed a model to simulate the dynamic performan- ce of a cylinder driving links of a manufacturing machine tool. rrsincφφ+ osφ θ = (5) Kawakami et al (1988) proposed a model for pneumatic cylinder 2 θ considering the dynamics of the piston and thermodynamics of the pcos 2 air. Such model shows that the heat transfer from the cylinder has rL(cosφφ−−rr)(rL+−2 sin)φφLr 2 cosφ little effect on movement of the piston. Authors emphasized the φ = (6) nonlinear characteristic of the cylinder. Aguilera and Lara (1999) Lrsinφ proposed a model to predict the dynamic performance of a cylin- der actuating on a translating mass under resistive forces taking −−()rrφφ2 cos(++2rrφφ)csinφθ− 2 p osθ θ = 2 2 (7) into consideration the dimensions of the system, and basing its 2 psinφ formulation on dynamic and thermodynamic considerations. Start and end cushion periods are considered in the modeling. Where the involved geometric parameters (see Fig. 1) are The Basic Model: a Pivoted Link. defined as follows: ≡ 2 2 2 ≡ 2 2 2 As mentioned before, the basic model includes a pivoted link A p - r - L , B p +L - r . driven by a pneumatic system, as shown schematically in Fig. Dynamic Analysis 1. In the following subsections the analysis involved in the de- Forces acting on the piston and rod are shown in Fig. 2a. velopment of the whole theoretical model, is presented. It is assumed that the weight and the moment of inertia Joint kinematics corresponding to the piston and rod are small, causing ne- gligible normal forces N and N . The main reason for this Figure 1 shows the schematic configuration of the actuated linka- P 0 ge, which can be completely described by means of the vector assumption comes from the idea that the useful axial force T on the rod F should be much greater than the weight of of joint variables q≡(r,φ, θ2) . These selected joint variables are related by a set of constraint equations that come from the vec- the cylinder. tor loop-closure that .is .detected. for the linkage. Similarly the Applying Newton’s Second Law to the pivoted link (Fig. 2b joint velocity vector q≡(r,φ,θ )T and the joint acceleration vector and Fig. 2c), in order to find an expression for the piston force .. .... .. 2 T q≡(r,φ,θ2) are defined as function of the time derivatives of the F, the resulting equations are: joint variables. Thus, the vector-loop closure gives: Ax + Fx = mbax (8) jjφ jθ2 0 (1) re−−= pe Le 0 A + F −W = m a (9) y y b b y MM−=I θ (10) FWA 2 where Ax, Ay are the components of the reaction force acting on the pivoted link at point A, Fx, Fy are the components of the reaction force between piston and link, mb is the mass of Figure 1. Basic Model, (a) Schematic diagram, including a pivoted link (3) the link, ax, ay are the components of the acceleration of the driven by a pneumatic actuator (2) with exhaust control valve (4) and tank center of gravity of the link, M and M are the moments due to (1), (b) Kinematic layout of the actuated pivoted link. F W the useful force, F, and weight of link, Wb, about A respectively, Marzo 2010, Vol.3 124 Dynamic Analysis of Pneumatically Actuated Mechanisms INGENIERÍA MECÁNICA TECNOLOGÍA Y DESARROLLO Vol.3 No.4 (2010) 123 - 134 Figure 2. a) Free body diagram of Piston and rod, b) Free body diagram of the Pivoted link, and c) Modified free body diagram with forces translated to the pivoted axle and resulting moments. ≡ φ θ ≡ θ and are given by MF Fpsin( + 2), MWb r21Wbcos 2, and IA where Q is the heat transfer between the control volume and is the moment of inertia of the link about point A which is its boundary occurring during the process from an initial state I ≡ 1 m d 22 defined as IAA 3 mbbd for a rectangular bar (as in the experi- (1) and any other state (2), Wair is the work done on the air mental apparatus), with a length d.
Details
-
File Typepdf
-
Upload Time-
-
Content LanguagesEnglish
-
Upload UserAnonymous/Not logged-in
-
File Pages12 Page
-
File Size-