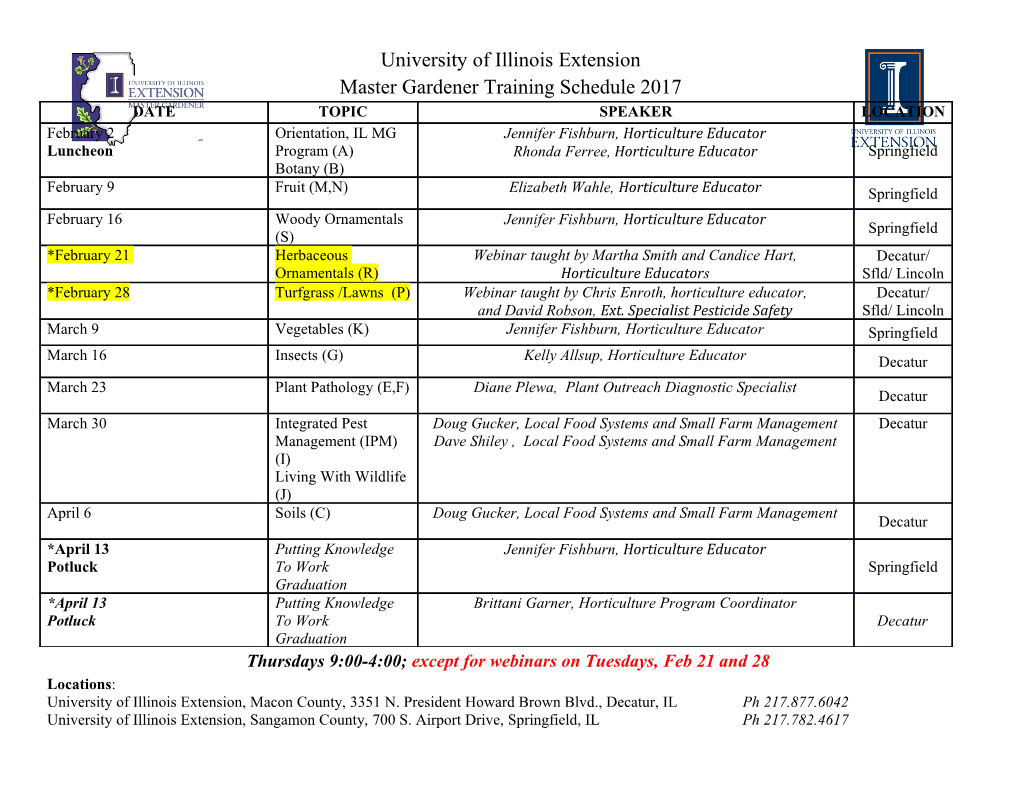
PLANT AUXILIARY SYSTEMS Designing and maintaining steam coil air preheaters for reliability and effectiveness If engineered well and drained properly, a simple finned-tube heat exchanger can help maximize a fossil-fueled power plant’s combustion efficiency, capacity, and air pollution reduction. Use the guidelines in this article ei- ther to return a disabled steam coil air preheater to service or to improve the performance of a unit that may have been wasting steam and money for years. By James R. Smith, Armstrong Heat Transfer Group team coil air preheaters (SCAPs) are sitions and the duct connection to the inlet there (Figure 4). Clogging and reduced per- found in most fossil-fueled utility and (cold end) of an RRAH. As opposed to being formance will be the undesirable outcome. Slarge industrial power plants in North bolted in place by duct flanges (Figure 2), Often (but unintentionally), the SCAP’s coils America. Their primary function is to heat units used in such a configuration are usu- serve as a convenient platform for mainte- combustion air before it enters a rotary re- ally drawer-mounted, for easier access and nance workers tasked with cleaning and in- generative air heater (POWER, April 2006, p. removal (Figure 3). specting the RRAH. 72) or a traditional tubular air heater. Wheth- Placing a SCAP ahead of the cold end Another undesirable consequence of er a rotary regenerative air heater (RRAH) (inlet side) of a RRAH, however, can invite placing a poorly constructed, specified, or or a traditional tubular heater is downstream, maintenance problems and shorten unit life. drained SCAP just upstream of the cold side the SCAP provides corrosion protection for For example, if a SCAP is placed directly of an RRAH is the development of steam the heater and maintains its cold end average below a RRAH, corrosive sediment and crud and/or condensate leaks in the air stream. exit gas temperature above a minimum. Im- dislodged during basket washdown will fall This can lead to evaporative cooling of the provements in boiler efficiency and heat rate onto coil-finned surfaces and accumulate RRAH’s surface, which “steals” valuable en- and in unit capacity from heating of combus- tion air have been documented for decades. 1. Simple in concept, complex in operation. A rough schematic of a typical Smaller industrial boilers fired by hog steam coil air preheater. For simplicity’s sake, the system shown depicts single coils in walls fuel or used for chemical recovery may use and ducts. In an actual system, the steam supply and condensate return lines typically feed 6 to 40 coils per forced-draft fan. Source: Armstrong Heat Transfer Group a SCAP as the primary preheater of com- bustion air. Increased use of alternative fuel From boiler and/or SCR system To boiler sources such as hog fuel, biomass, tire-de- rived fuels, and refuse-derived fuels have Hot end Turbine-generator made it more important to optimize the use Rotary regenerative Air heater Superheated of SCAPs. steam Condensate from Stricter emissions standards also have Cold end air preheat coils changed the utilization of SCAPs. With protection Condenser temperature plants’ increased use of selective catalytic Desuperheater and noncatalytic reduction (SNCR and SCR) To scrubber, etc. TCV Desuperheater TCV systems and other emissions-reduction equip- In-duct air ment, SCAPs now are needed year-round— preheater coils rather than just during the ozone season—to maintain heaters’ outlet gas temperature. Forced-draft fan Wall air preheater Location, location, location coils Figure 1 is a very simplified schematic of a SCAP. Most units use vertical finned-tube To condenser coils embedded in perimeter entry walls to connect to the suction side of a forced-draft Condensate Transfer (FD) fan or fan room —the source of com- receiver pump bustion air. Some SCAPs, however, are de- Condensate signed to be installed on the discharge side of Notes: SCR = selective catalytic reduction; receiver the FD fan, between the fan’s ductwork/tran- TCV = turbine control valve 2 www.powermag.com POWER | May 2006 PLANT AUXILIARY SYSTEMS ergy from the unit. All three of these SCAP- ing a unit’s heat rate and maximizing its ca- into the category of “troublesome” equip- related problems—increased maintenance pacity requires creative modifications of the ment not worth keeping in service. Accord- requirements, shortened life, and higher- entire SCAP “loop”—comprising all compo- ingly, they often receive little or no attention than-necessary energy consumption—have nents and controls from the steam source to during outage planning for design upgrade or been reported by large fossil fuel–fired pow- the condensate return. correction. er plants in the U.S. and Canada. It’s surprising that so many power plants have had so many problems with SCAPs; Where and why SCAPs go bad Problem children after all, they are fairly basic finned-tube Among the common system causes of steam Utility boilers obviously can and do remain units for exchanging heat between steam coil air preheater problems are the following. functional without the help of a SCAP. How- and air. EPRI has documented that, since the Desuperheater stations. Because they ever, the lack of a SCAP may reduce a boil- 1980s, many SCAPs had been shut down, provide pressure let-down and steam tem- er’s combustion efficiency enough to make removed, or partially blanked out of service perature control of a SCAP system, desuper- its unit only marginally profitable. Minimiz- due to maintenance, repair, and/or perfor- heater stations must be operated accurately mance-related (leakage) issues early in their and continuously. At a minimum, failing to 2. Bolted in place. A wall-mounted operating life. Often, problems appeared regulate the quality and amount of desuper- steam coil air preheater with common re- within only a few years of plant start-up and heating water and associated feedback sys- ceiver drainage. Courtesy: Armstrong Heat commissioning. tems drastically reduces SCAP performance. Transfer Group At the other extreme, SCAP coils at some At worst, failing to desuperheat steam for plants have been on the job for up to two de- optimum SCAP condensing requirements cades, but they may have been performing stresses the unit’s coil materials at key weld well below design parameters and wasting joints, with catastrophic consequences. steam for years. Often, such inefficiencies Among them is the passing of live, uncon- and losses go undetected, either due to cut- densed steam to the condensate system, backs in maintenance budgets or because overheating it. Desuperheating to a level of other maintenance items are considered a no more than 100 degrees F above saturation higher priority. temperature is a good guideline for SCAP A recent cursory inspection by the author’s design. company of just a few U.S. fossil fuel–fired Scheduled maintenance of desuperheater utility plants revealed that hundreds of SCAP station components does more than just coils had been isolated because they failed improve SCAP performance. The attention prematurely or required excessive mainte- indirectly helps improve critical pressure nance. A similar trend has been noted across differentials across the SCAP system, im- the U.S. and Canada, regardless of fuel type proving drainage. One large Midwest power or plant location. As maintenance budgets plant experienced measurable reductions in and staffs have shrunk, SCAPs have fallen wasted steam flow through targeted main- 3. Easier to replace and maintain. 4. Look out below. Because this steam coil air preheater (SCAP) was mounted di- A pre-piped, duct-mounted, drawer-type rectly below a rotary regenerative air heater, corrosive sediment and crud dislodged during steam coil air preheater with individual coil RRAH basket washdown fell onto the SCAP’s finned-coil surfaces, damaging them. Courtesy: trapping. Courtesy: Armstrong Heat Transfer Armstrong Heat Transfer Group Group May 2006 | POWER 3 PLANT AUXILIARY SYSTEMS tenance of desuperheater stations during vestment funded by the plant’s O&M budget 3. Evaluate the superheated steam sup- scheduled outages. can result in notable improvements. Justify- ply and the trapping ability of the Coil issues. A SCAP that underperforms ing modifications of a SCAP system on the pressure-reduction station. Because or fails prematurely may be a “victim of cir- basis of the plant environmental performance failed traps and blow-through cause un- cumstances.” Possibilities include airside gains they would produce is a common and necessary energy losses and operational fouling, damage during handling or removal, acceptable practice. problems, it’s a good idea to test traps reg- dirty finned tubes, changes in steam condi- ularly—at least once a year. At that time, tions, and poor positioning of the SCAP rela- Solving SCAP problems all piping insulation should be inspected tive to the air heater it serves. A total systems assessment—including sup- to ensure that it is in good condition. Condensate drainage and noncon- ply and drainage piping design and opera- densables venting issues. Poor drainage tional control details—is recommended as Options for modifying and venting practices retard efficient heat a first step. A project that is limited to coil steam supply transfer in SCAP tubes. These problems can replacement has little chance of eliminating Consider slightly increasing the steam pres- easily be remedied either by improving the most common SCAP problems. sure to the SCAP (after consulting its manu- design and specifications of materials, rees- The steam-source review portion of the facturer). Doing so may allow fin spacing to tablishing original steam conditions, or fol- systems assessment should include the fol- be widened, possibly reducing the number lowing industry best practices for venting, lowing three steps: of rows needed, airside pressure drops, and draining, and maintaining auxiliary compo- airside fouling of the finned coils.
Details
-
File Typepdf
-
Upload Time-
-
Content LanguagesEnglish
-
Upload UserAnonymous/Not logged-in
-
File Pages4 Page
-
File Size-